In late 2010, German-based Hammel Recyclingtechnik introduced what it described as the world’s first mobile scrap processing plant at an auto recycling show in Hohenroda, Germany.
The company says the system can process a mixed basic material into a marketable end product. Raw material, including car bodies, engine blocks and aluminum bales, is shredded with the primary shredder, the VB 950 DK, and directly fed into the metal screen, the MMS 150 DK, where it is separated using a vibratory screen, discharging the oversized material. The screened material falls onto an integrated vibration channel, which feeds the material to a drum magnet.
The drum magnet sorts ferrous from nonferrous material. The nonferrous material is transferred via a discharge belt to the eddy current system, where the aluminum and shredded light fraction are separated. The ferrous material is transported to the metal fine shredder, the HEM 1250 DK.
The shredding rotor is equipped with eccentric disc hammers and is hydrodynamic. With the special shredding rotor and its pre-stressed screen basket, Hammel says it is possible to achieve a precise end size material, adding that it was the goal to reach an E40-classification on the European steel-scrap-list.
Ralf Semler, regional manager for Hammel New York, based in Bohemia, N.Y., spoke with Recycling Today about some of the potential advantages recyclers can see from processing scrap metal with a low-speed, high-torque shredder.
Recycling Today (RT): What types of metal scrap can low-speed, high-torque shredders handle, and how do production levels differ from hammer mill shredders?
Ralf Semler (RS): The capabilities of low-speed, high-torque shredders in processing scrap metal vary a lot depending on the manufacturer and shredder model in question. Some machines utilize a cutting or shearing action; others are ripping/tearing the material apart. Not all low-speed, high-torque shredders are capable of processing scrap metal, and some should only be used for very specific and uniform materials, such as sheet metals, according to the manufacturer’s recommendations.
A Hammel low-speed, high-torque shredder works under the ripping and tearing principle, utilizing two synchronized, counter-rotating, load-sensing and auto-reversing shredding shafts that run at about 35 rpm. This design allows it to process most types of scrap metal where steel is no more than 0.25 to 0.50 inches in thickness. Miscellaneous scrap and appliances/white goods are very popular materials as are iron-y aluminum products, such as transmissions and engine blocks. The same machines are also capable of processing demolition debris, tires, wood and more with little or no changes. The larger Hammel models, like the VB 950DK Red Giant, can process an entire car or pickup truck—engine, transmission and rear-end included.
Production levels are typically between 15 to 40 tons per hour in a scrap metal environment (depending on the shredder and the application). This is less than some hammer-mill type shredders can produce, but operating and maintenance costs are also much less as well. A typical operation should incur maintenance time of about one hour per day, or about one day every other week.
RT: How can low-speed shredders be advantageous relative to such things as less noise, less dust and fewer emissions? Is the permitting process typically easier when deploying a low-speed unit?
RS: The low-speed, high-torque shredder has a big advantage when it comes to noise, dust and emissions. Noise levels emitting from the shredder in a typical operation are no louder than the material handlers and trucks operating in its vicinity. Dust levels depend on the material being shredded and can be further controlled with an optional water-spray dust suppression system. The low-speed shredding action produces a very low amount of dust in the first place compared to any high-speed shredding mill.
Hammel’s line of shredders are available with either a diesel or electric drive and range from 350 to 710 horsepower, with fuel consumption of 5 to 18 gallons per hour.
Permitting regulations vary everywhere, so anyone considering a low-speed, high-torque shredder should check with the local authorities directly just to make sure. Typically, what we have found is that our shredders, most of which are mobile, self-contained machines, do not require any additional permits to be used. The machines do not require any special foundations or concrete pads to be poured and can be moved around the yard or on the road across town and be set up and ready to be used again in less than 30 minutes. One application where this could be utilized is rotating a slow-speed, high-torque shredder from one yard to the next, processing materials in a different location every few weeks or every other month.
RT: Considering the productivity difference, what size of scrap yard or what type of scrap operation can be a good fit for a low-speed shredder? To what extent have scrap yard managers running scrap through a low-speed shredder set up nonferrous sorting equipment? In what ways does it prove to be cost-effective?
RS: A low-speed shredder in its most basic form is a volume reducer. Without any kind of downstream separating equipment, the shredder by itself can be used to efficiently densify bulky materials to maximize weight for shipping/trucking. Clean aluminum rims are a great example of this, as it is virtually impossible to get enough weight into any container when shipping unprocessed rims. Processing material on a remote feeder yard for trucking and further processing at a central location is another great example.
Another application for just the shredder by itself is as a pre-shredder for a small to medium-size hammer-mill shredder, downsizing bulky material to better feed into the hammer mill and delivering a more consistent feedstock, resulting in a more consistent operating load on the shredder.
The next step up from having no separation at all would be the addition of a magnet. Depending on the application, a cross-belt, inline or drum magnet can be used to remove ferrous material from an iron-y aluminum mix or to pick out the ferrous material from other contamination.
At this stage a small picking conveyor can be useful if either the ferrous or nonferrous stream contains materials that should be further separated. A great example of this is picking out and separating the electric motors that get picked up by the magnet along with all the other ferrous steel. These should not end up in the final steel pile and will fetch a much higher price when sold separately.
In an application where white goods are being processed, the addition of an eddy current makes a lot of sense. In Hammel’s product offering we call this our three-machine “Mobile Metal Separation Plant.” We shred the material and size it to a 6-inch-minus product using a vibrating finger screen. A drum magnet separates the ferrous material, and the nonferrous feeds into an eddy current separator to get out the aluminum. With a few hand pickers on the various output belts, this scrap yard now has the ability to take in appliances and white goods, do the processing in house and end up with sellable materials of 6-inch-minus clean steel, aluminum or zorba and the hand-picked items, like electric motors (meatballs), stainless steel, copper, insulated wires, etc.
The owners of these types of machines range from very small yards with a single small shredder all the way to the big steel companies that own multiple machines. There is no clear-cut best customer, but there does seem to be a trend for the mobile metal separation plant to find its home with the medium-size scrap companies that have between one to six locations in an area. This size business can generate enough material to keep the machines fed and can best benefit from the additional market opportunities that are opened when processing material in house.
Ralf Semler is regional manager for Hammel New York, based in Bohemia, N.Y. He can be contacted at ralf@hammelny.com.
Get curated news on YOUR industry.
Enter your email to receive our newsletters.
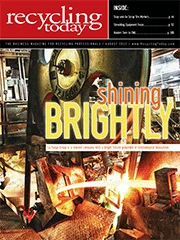
Explore the August 2012 Issue
Check out more from this issue and find your next story to read.
Latest from Recycling Today
- AF&PA report shows decrease in packaging paper shipments
- GreenMantra names new CEO
- Agilyx says Styrenyx technology reduces carbon footprint in styrene production
- SABIC’s Trucircle PE used for greenhouse roofing
- Hydro to add wire rod casthouse in Norway
- Hindalco to invest in copper, aluminum business in India
- Recycled steel price crosses $500 per ton threshold
- Smithers report looks at PCR plastic’s near-term prospects