Few modern companies can claim a lineage that dates back more than 200 years, making La Farga Group rare among its peers. The history of this family-owned Catalonian holding company dates back to 1808 and the formation of La Farga Lacambra (LFL), which produces and sells semi-finished copper products made from recycled copper.
In 2011 La Farga Group announced a joint venture in the United States with Steel Dynamics Inc. (SDI), headquartered in Fort Wayne, Ind. The joint venture, SDI La Farga LLC, has built a secondary copper smelter in New Haven, Ind., to produce copper wire products exclusively from copper scrap. The plant is now operational and consumes copper scrap supplied by Fort Wayne-based OmniSource, a subsidiary of Steel Dynamics Inc. (SDI), as well as material purchased on the open market. (See the sidebar “Cause for Celebration” on p. 43.)
La Farga Group also has expanded recently to include La Farga Tub (LFT), which produces and sells copper pipe; La Farga Rod (LFR), which makes electrolytic copper rod from high-grade cathodes; and La Farga Intec (LFI), which in collaboration with Continuus Properzi S.p.A. develops and sells technology.
In 2004 La Farga Group established La Farga Foundation, which operates a copper museum at the group’s headquarters in Les Masies de Voltregà, Spain. That site also is home to the production plants of LFL and LFR. In addition to operating the museum, La Farga Foundation funds the university education of company employees and needy residents of Les Masies de Voltregà.
While the umbrella La Farga Group name is relatively young, having been established in 2003, its origins can be traced back to the growth of LFL.
Port of Origin
LFL traces its lineage back to 1808, when Francesc Lacambra i Pont established a small foundry in the Barceloneta port district of Barcelona. Francesc also traded used copper generated from replacing sheeting from the hulls of sailing ships, becoming one of the primary suppliers to the Barcelona Royal Mint by 1844.
La Farga Group at a Glance Executives: President Vicente Fisas Comella and CEO Oriol Guixà Location: Headquarters, La Farga Intec, La Farga Lacambra, La Farga Rod and La Farga Tub operations in Les Masies de Voltregà, Spain; La Farga Tub France, Lyon, France; and joint venture operations Ganzhou Jiangwu - La Farga in Ganzhow, Jiangwu Province, China, and SDI La Farga LLC in New Haven, Ind. No. of Employees: 350 at the company’s headquarters and manufacturing plants in Spain Services Provided: La Farga Lacambra produces and sells semi-finished copper products from recycled copper; La Farga Tub produces, sells and distributes copper pipe; La Farga Rod manufactures electrolytic copper rod from high-grade cathodes; and La Farga Intec develops and sells technology and new products in collaboration with Continuus Properzi Spa. |
In 1852 Francesc established La Farga Lacambra, a water-driven foundry along the Ter River in Les Masies de Voltregà, about an hour and a half outside of Barcelona.
The foundry began producing copper sheeting in 1853 under the direction of Francesc’s son Joan Lacambra Pujadas. The Spanish Navy was among the company’s customers, says Marc Gascón, who purchases raw material for La Farga Group. LFL even supplied the copper sheeting used on the Spanish ships that sailed to America, says Gascón.
Continuing the company’s culture of expansion, Francesc’s son Josep Lacambra Saborit led a retooling of the foundry’s machinery, enabling LFL to begin production of wire rods for electric cables in 1913. This move expanded the company’s customer base to include the critical electrical and railway industries, Gascón says.
Innovative Approach
In 1986, LFL became the first company to produce thermal rods for continuous casting using No. 2 copper scrap containing 94 percent or more copper, Gascón says. The company’s patented Cosmelt Process is a pyrometallurgical method that reduces the number of stages required to recycle copper scrap. While other methods require a total of three production phases (via an electrolytic process), LFL says it can complete the entire process in a single stage.
Gascón says the Cosmelt Process is environmentally superior to other methods as well as more efficient because it eliminates the need to first produce anodes and cathodes. Additionally, the company’s refining process uses a special furnace that can improve the purity of the copper to 99.6 percent.
“Our main strength is this technology,” Gascón says, adding that LFL can produce copper wire with a level of purity comparable with that of wire made from copper cathodes.
LFL’s Cosmelt technology has been sold to more than 28 plants in 15 countries worldwide, according to Carme Saez, corporate development director at La Farga Group. “Continuus Properzi sells the machinery, and we sell the know-how.”
LFL has the flexibility to consume No. 1 copper scrap in addition to No. 2 copper, Gascón says. The company purchases loose copper scrap from within Europe as well as baled material from the United States. LFL also sources scrap from South America.
LFL produces semi-continuous and continuous castings that are used to make semi-manufactured products, such as wire, billet, cable, cord, multi-strand wire, rigid wire and pipe. The company has branded the copper it produces from recycled metal Ecocopper. LFL says its Ecocopper products can be used to manufacture high-, medium- and low-voltage cables; data transfer, control and instrumentation cables; cables for the telecommunications industry; cables for the automotive industry; short circuit links; contacts and plates; supports for superconductive materials; wires for welding metal containers; pipes for water, gas and heating ducts; pipes for cooling and technical gases; copper wire rods; profiles and applications in galvanization.
Saez says the products produced by the various companies under La Farga Group’s umbrella are generally sold within a 900-mile radius of the manufacturing plants, given their weight. However, she continues, “We have markets around the world and are always looking to diversify our markets.” Saez adds that La Farga Group is interested in developing markets outside of its home region, noting the European debt crisis and the downtrodden Spanish economy.
North Africa, for example, has been a growing sales region, Gascón says, helping La Farga Group to mitigate the effects of the economic downturn in parts of the European Union.
Saez says La Farga Group’s focus on research and development is the reason the company has survived for more than 200 years.
“We are continually investing in new technologies and in research and development in order to adapt ourselves to the market,” she says. Saez adds that La Farga Group also has continually sought to diversify its operations and products, often by taking cues from the needs of its clients.
Upon on a Solid Foundation
LFL accounts for the largest share of La Farga Group’s sales in terms of tonnage. LFL sold more than 100,000 metric tons throughout 2011, Saez says. During that same time, LFR, which was established in 2008 on the site of La Farga Group’s headquarters in Les Mesies de Voltregà and specializes in the production of copper wire from cathodes, sold nearly 90,000 metric tons.
LFT was formed in 2006 when La Farga Group grew its share in Tubo Técnico Europeo from 36 percent to 86 percent and the company changed its name. In September of 2011, La Farga Group formed La Farga Tub France, based in Lyon, which distributes tubes manufactured by LFT to the French market. LFT sold slightly more than 15,000 metric tons through September 2011. LFT products are used in plumbing, heating, air conditioning and refrigeration.
“Each of these companies is operated independently,” Gascón notes. “La Farga Group is a stakeholder, but they each have their own purchasing departments and management.”
In 2010 La Farga Group together with a private partner and the government of the Chinese province of Jiangxi established a joint venture in the Chinese city of Ganzhou, known as Ganzhou Jiangwu – La Farga High Speed Railway Copper Materials. The company makes a range of railway electrification products for China’s high-speed rail industry.
Sustainable Future
Saez says the family behind La Farga Group is not interested in developing the company for sale to one of its many multinational competitors. Instead, she says, the family wants to develop a long-term sustainable company.
Environmental and social responsibility also factor into the company’s decisions, according to Saez. La Farga Group’s corporate sustainability strategy requires department directors to create strategies for environmental protection, employee risk management, customer satisfaction, innovation and corporate development.
“The mission is to be a leader in copper recycling and in the development of high-performance copper materials,” Saez says.
Innovation is a key factor in maintaining the company’s leadership position, Saez says. “We have the spirit of improvement,” she says of La Farga Group. “We are always trying to improve.”
Cause for Celebration SDI La Farga LLC, the joint venture between carbon steel producer Steel Dynamics Inc. (SDI) of Fort Wayne, Ind., and copper product manufacturer La Farga Group, based in Barcelona, Spain, welcomed visitors to its New Haven, Ind., manufacturing plant July 10. The facility, which includes a 320-metric-ton furnace, produces copper wire rod from copper scrap. Roy Perala, formerly with Steel Dynamics, is general manager of SDI La Farga, while Jake Fetters is the company’s production supervisor. During a tour of the 85,000-square-foot facility, which had been in operation for roughly one month, Fetters said the plant would operate on a 24-hour cycle, with eight hours required to melt a full furnace charge, eight hours needed to prepare the molten copper for casting and eight hours required for casting. The mill’s primary line produces 8-millimeter wire. A secondary breakdown mill can produce thinner gauge wire, Fetters said. Initially, SDI La Farga expects 25 percent of its production to require additional processing through the breakdown mill, he added, though this will vary based on orders the company receives. The SDI La Farga plant is based on La Farga LaCambra’s operations in Barcelona, though the furnace is roughly 1.5 times the size of the original furnace in Spain, Fetters said. A luncheon at the grand opening featured speeches from SDI President and CEO Mark Millett, La Farga Group President Vicente Fisas Comella, Indiana Secretary of Commerce Dan Hasler, Indiana Sen. Tom Wyss, Allen County Commissioner Nelson Peters and New Haven Mayor Terry McDonald. Wyss said he expected the new facility to do “nothing but grow” in light of SDI’s involvement, while Peters said partnerships such as SDI La Farga “will help the county continue to grow and thrive.” The elderly Comella said that, despite his physical limitations, it was important for him to be at the open house and that his faith in the project made the difficulty of travel possible. Illustrating La Farga Group’s excitement about the SDI La Farga joint venture, four generations of Comella’s family were present at the grand opening, he noted. SDI’s Millett said the character of the Comella family was one of the reasons SDI partnered with La Farga Group, which also brings a great deal of technical expertise to the project. Of the new company’s location, he said, “It is not by happenstance that we are in Indiana,” adding that the state’s business climate was “tremendous.” Millett added that the goal of SDI La Farga would match SDI’s goal of being the lowest cost operator in all of its business segments. |
The author is managing editor of the Recycling Today Media Group and can be contacted at dtoto@gie.net.This article originally ran in the March/April issue of Recycling Today Global Edition, a sister publication of Recycling Today.
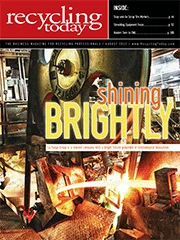
Explore the August 2012 Issue
Check out more from this issue and find your next story to read.
Latest from Recycling Today
- AF&PA report shows decrease in packaging paper shipments
- GreenMantra names new CEO
- Agilyx says Styrenyx technology reduces carbon footprint in styrene production
- SABIC’s Trucircle PE used for greenhouse roofing
- Hydro to add wire rod casthouse in Norway
- Hindalco to invest in copper, aluminum business in India
- Recycled steel price crosses $500 per ton threshold
- Smithers report looks at PCR plastic’s near-term prospects