Discarded waste material, especially metal suitable for reprocessing” is how TheFreeDictionary.com by Far- lex defines scrap. That is an understatement. The role of scrap metal, both ferrous and nonferrous, is changing dramatically. It is a vital raw material required for reprocessing. Yet, it is not quite treated as a raw material from a quality control (QC) standpoint. It does not come in clean, new, freshly labeled bags stating composition, country of origin and safety hazard designations. Consequently, a new unknown is added to the metal production process. Handheld X-ray fluorescence (XRF) is here to help.
Focusing on Aluminum
The attractiveness of aluminum lies within its unique properties, such as its light weight, high strength, excellent corrosion resistance, good formability, high electric and thermal conductivity, reflectivity and nontoxicity. Aluminum alloys can be divided into two major groups—wrought alloys and casting alloys—based on their method of fabrication.
Demand for aluminum is growing, propelled by strong market drivers, such as the urbanization and industrialization in China and India, growth in the transportation industry in North America and in China and the substitution of aluminum for other materials. (For instance, aluminum content in automobiles is expected to double from 8 to 16 percent from 2008 to 2025 at the cost of steel, which is expected to decline from 42 to 30 percent during that time).
Meanwhile, at a time of growing demand for this metal, we are witnessing a concurrent period where global primary aluminum production is moving into a deficit (demand is greater than production), with a modest forecast for capacity growth in the next three to five years. Additionally, a significant 29 percent of the existing primary production capacity is operating at a loss, according to Jorge Vazquez of Harbor, who spoke at the January 2012 Platts Aluminum Symposium.
With these constraints on primary production, the role of secondary aluminum production from scrap is on the rise and offers significant benefits. Aluminum production from scrap uses only 5 percent of the energy and emits just 5 percent of the greenhouse gases as compared with primary aluminum production. Further, new regulatory guidelines, such as LEED (Leadership in Energy and Environmental Design), REACH (Registration, Evaluation, Authorisation and Restriction of Chemical substances) and Walmart’s “Packaging Scorecard,” are incentivizing businesses to increase the usage of scrap. Because aluminum can be repeatedly recycled without any loss of performance, major aluminum manufacturers, such as Novelis, have set aggressive goals to incorporate additional scrap into their production. The production of secondary aluminum increased steadily from less than 1 million metric tons in 1970 to a peak of 3.7 million metric tons in 1999; between 2001 and 2006, production was around 3 million metric tons, according to “Economic Forces Shaping the Aluminum Industry,” www.secat.net/docs/resources/Economic_Forces.pdf.
It is clear that the race for aluminum scrap is on, and so is the need to add controls along the supply chain. Failure to do so will elevate the risk of introducing undesired impurities into the process, which can result in potential manufacturing interruptions and noncompliance with product specifications. This is especially true for “old,” post-consumer scrap that has been discarded, such as appliances, foil, automobile and airplane parts, sidings and used beverage cans (UBCs). However, “new,” pre-consumer scrap from aluminum fabrication operations is typically more consistent in composition.
How can handheld XRF technology help with these supply chain issues?
Optimizing the Way you Work
A handheld XRF analyzer consists of an X-ray source (i.e., an X-ray tube that generates a beam of primary X-rays). When these X-rays hit the sample, the atoms in the sample are ionized. Upon returning to a stable state, these atoms emit fluorescent X-rays back to the analyzer. These signals are used to determine chemical composition and match the results with a user-expandable built-in library.
Older handheld XRF analyzers were limited to detecting elements heavier than titanium (atomic number 22). At best, this meant that alloys could be sorted by family in light of their heavy element content (titanium, chromium, manganese, ferrous, nickel, copper, zinc, zirconium, lead and bismuth). Detecting lighter elements was made possible only with a more expensive upgrade to a helium or vacuum purge system. This changed dramatically in recent years mainly in light of the implementation of silicon drift detector (SDD) technology, but also because of the optimization of the excitation voltage to the X-ray tube and optimization of the detector-sample geometry. As a result, the detection and analysis of lighter elements (magnesium, aluminum, silicon, phosphorous and sulfur) was made possible under ambient conditions. Besides light element capabilities, overall measurement times, accuracy and sensitivity to trace and tramp elements have improved significantly.
By and large, the analyzer’s features are engineered to help benefit scrap metal recyclers. Data processing and storage are performed locally on the instrument, and the data can easily be transferred to a computer either through USB or wirelessly via Bluetooth. Further, the most advanced instruments do not require daily calibration, and measurements can be carried out on a wide variety of sample shapes and sizes. Of major benefit is the built-in alloy library, which can be expanded and tailored to individual needs. With just a short test, alloy grade and full chemical composition appear on the built-in color touch-screen display.
Removing Doubt
The rugged design, portability and ease-of-use of handheld XRF devices can make them ideal for scrap yards looking to improve their profitability, efficiency and turnover times. The ability to positively identify dozens of aluminum alloy grades and to analyze their chemical composition at material transfer points (i.e., incoming scrap and outgoing scrap) is a true value-added advantage.
Most recycled aluminum involves a mixture of various wrought and casting grades. K. Subodh, in the June 2006 Light Metal Age article, “Designing Aluminum Alloys for a Recycle-Friendly World,” demonstrated that even when wrought scrap has been segregated, individual lots may still have widely varying compositions because of the large number of applications and industries from which the scrap originated. To illustrate, the bumper alloy 7029 contains a higher level of zinc, while the auto-body alloy 2036 contains higher copper levels. Similarly, the mixing of casting with wrought alloys can result in undesirable elevated amounts of silicon. While posing a small problem for further production of casting-grade alloys, this can be a major problem for the secondary production of wrought alloys. The automotive industry, for example, often requires separation in its use of A356, A319 and A380 cast aluminums, which differ mainly in silicon content.
Handheld XRF empowers scrap yards to perform this task through fast and efficient sorting, adding value to their services. The aerospace industry provides a good example for deploying specialty alloys with tight compositional requirements. Alloys such as 7050 and 7075 belong to the same alloy family; however, slight variations in their alloying elements are necessary to produce desired physical properties for their intended applications. Other common aerospace separation needs are 2014, 2024, 7055 and 7449, to name just a few. Handheld XRF analyzers can easily and accurately separate these alloy types, which can command a premium when sold locally rather than selling at lower “mixed” load prices to overseas markets.
Alloys 6061 and 6063 are some of the most popular aluminum alloys used in a wide variety of applications, including the construction and automotive industries. Considering the price differential of these alloys when processing several thousand pounds of mixed material, one could easily see the profit potential in properly segregating these alloys. Further, when this processed material is delivered to end users, such as a secondary aluminum smelting operations, mixed loads may not be tolerated. Repercussions, including downgrading the load, outright refusal of the load or even loss of the account completely, can negatively affect the profits and reputation of the scrap recycler supplying the material.
The major alloying elements in 6061 and 6063 are magnesium and silicon, and their maximum zinc content must be kept below 0.1 and 0.25 percent, respectively. With the help of handheld XRF, it is possible to quickly remove any zinc-containing scrap, such as alloys from the 7000 series, and thus increase the overall value of the material. In addition, a “mixed” load of 6000 series material also can include alloys such as 6262 and 6033, which are used in similar applications but contain trace amounts of lead or bismuth. Without the aid of mill stampings or markings, visual inspection alone is not a reliable method for separating these materials. Therefore, larger amounts of this material mixed in a load can be detrimental to a melt if the tramp elements introduced are above the mill’s specifications.
Another important function of handheld XRF technology is recovering the value “locked up” in scrap. Prior knowledge of the type and quantity of trace elements in scrap can be wisely built into the logistics of raw material purchasing and reduce the need to source expensive additives. For example, alloys 2014 and 2024 are similar, with varying contents of magnesium. The variation can be as low as 0.4 percent or as high as 1.6 percent, depending on individual lots. Thanks to handheld XRF technology, these two alloys can be separated. The difference in value between these two alloys, from an magnesium-sourcing perspective, can translate into a nearly $900,000 annual savings, based on a daily turnover of 200,000 pounds and an magnesium pricing of $1.5 per pound.
Straightforward Approach
The science behind handheld XRF is complex and sophisticated, yet the deployment of this technology is simple, straightforward and user friendly.
Handheld XRF offers a nondestructive and robust technology to provide rapid, on-site scrap sorting. As we continue to witness the increasing importance of scrap in the production of aluminum, there will be a growing need to install additional checkpoints along the supply chain to prevent contaminants from entering production. Achieving this early in the process, that is, before any unwanted scrap can even enter the supply chain, is advantageous in minimizing errors and protecting the reputations of the suppliers of these scrap metal materials. Handheld XRF can be an indispensable tool for achieving these critical tasks, as well as in recovering the locked up value in scrap.
Jonathan Margalit is business development manager – metals, James Stachowiak is technical sales manager – metals, Thomas Anderson is vertical marketing manager – metals and alloys and Jeffrey Walker is vertical director – recycling and metals production for Thermo Scientific Portable Analytical Instruments, Thermo Fisher Scientific Inc.
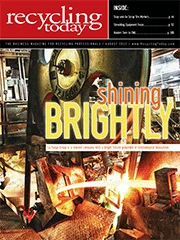
Explore the August 2012 Issue
Check out more from this issue and find your next story to read.
Latest from Recycling Today
- AF&PA report shows decrease in packaging paper shipments
- GreenMantra names new CEO
- Agilyx says Styrenyx technology reduces carbon footprint in styrene production
- SABIC’s Trucircle PE used for greenhouse roofing
- Hydro to add wire rod casthouse in Norway
- Hindalco to invest in copper, aluminum business in India
- Recycled steel price crosses $500 per ton threshold
- Smithers report looks at PCR plastic’s near-term prospects