In the 21 years Steve Skurnac, president of Chicago-based Sims Recycling Solutions (SRS) America, has been involved in the electronics recycling industry, much has changed regarding how the industry processes material. He says recyclers have caught on to the fact that shredders with multiple cutting shafts produce a better particle size and help contribute to the overall efficiency of the recycling process.
SRS operates 14 electronics recycling facilities in North America in addition to more than a dozen facilities throughout Europe, Asia and Australia, giving the company a unique perspective on the global electronics recycling industry. He shares his thoughts on electronic scrap processing trends in the following Q&A with Recycling Today.
Recycling Today (RT): Is there a particular style of shredder technology that is preferred for processing electronics? Does that vary for primary shredding and secondary shredding?
Steve Skurnac (SS): There is a more preferable type of shredder technology. A lot of the industry has tried to evolve into multi-shaft shredding technology. What we mean by that is, initially, the industry used very simple twin-shaft or even single-shaft shredders, where you would draw the material into a box, if you like, that had the shredder and the teeth at the bottom of it. The material would be chopped up as it moved through the rotating cutter blades that were inside the shredder box. This type of shredder does a decent job of cutting things into smaller pieces. But what the shredder manufacturers have discovered over the years is that if you put multiple cutting shafts into the box, you can get much better particle size, much better liberation and a more efficient cutting of the electronics as they go through the shredder.
What you have now is a tri-shaft shredder with three cutting shafts in it, and even quad-shafts that have four cutting shafts in them are very popular today. It makes it easier to make all of the size reductions in one shredder rather than having to do it in multiple shredders.
In the old days, you might do one long cut that produced big, chunky pieces. Then, you would have to send that material into another shredder to make it a bit smaller and then potentially to a third shredder to make the material even smaller again. With a tri-shaft shredder, you could actually do all of that with a single piece of shredding equipment.
RT: How has the growth of small, high-capacity storage devices affected your processing? Have you had to shred to a smaller particle size?
SS: We are not seeing a lot of the new, smaller material coming through the material recycling stream just yet. The bulk of the material that comes through to us is still older, clunky material.
Having said that, the smaller particle size is more of a concern for our data-security-focused customers. When we destroy a hard drive, for example, and chop it up into pieces for commodities, there are customers who are looking for a minimum particle size. In some cases, we have had to install a dedicated shredder for hard drive shredding so we can put in a smaller screen size and get a smaller particle size when processing that kind of material.
RT: What degree of demanufacturing takes place prior to shredding?
SS: The demanufacuturing or disassembly depends on the material stream itself and what benefit we might have by doing more disassembly rather than just pitching it in the shredder.
One reason for demanufacturing is hazard removal, and by that we mean removing batteries, mercury lamps and toner prior to shredding.
The next question we would ask from a business perspective is, if we already opened up the unit to remove some sort of hazard, is it worth it to continue with the manual disassembly to remove other components. That varies by material type. For example, if we opened a desktop computer up because we were taking a battery out, the first thing we are going to look for is generic memory that could be taken out and possibly reused. Do we take the hard drive out because we are going to wipe the data before we destroy it separately?
RT: What is the optimal particle size for further sorting and separating shredded electronics?
SS: Generally speaking, the size range is from 5 to 20 millimeters in regard to particle size. The reason there is a range is that for some materials, such as some of the metals that you want to separate, you want to be on the larger end, because if it gets too small it will get too difficult to distinguish one metal from another. With some plastic-based materials, you want to go a little bit on the smaller side with the technology you are using because it gives you better separation.
RT: How has the incoming material stream changed in the last five years in electronics recycling?
SS: The most obvious change we have seen in the last five years, which might be a bit surprising to folks not in the business itself, is in fact we are seeing an influx of computer and television monitors, the tube-based monitors that we all had in our houses at one time. That is a progression, as historically most electronics recyclers would have been doing business with a corporation, so you would have been getting desktop computers, televisions, photo copiers, printers and potentially some of these giant server cabinets that would have been coming in.
Now, a lot of states brought in regulations that mandated the recycling of televisions and computer monitors along with other electronic scrap, and so there has been an influx in material that is television based along with all of this traditional computing material. That has been a bit of a surprise in terms of how much of this stuff was actually out there in the marketplace. Everyone kept their old televisions and their old computer monitors and didn’t put them in the landfills, which is great because we don’t want them in the landfills, but there has been a huge surge of this kind of material coming into recycling centers as a result of these new rules that have been put in place by states.
RT: What solutions are electronics recyclers coming up with to manage their customers’ concerns about data security?
SS: You can simply use software to erase the data that is on the hard drives, and that works fine on traditional hard drives. It allows the traditional hard drives to be completely wiped of data and reused again. Clearly there is a market for used hard drives. For average consumers and customers that just want the hard drive to be wiped of any data, we can certainly provide that service, as can other recyclers.
For customers who have higher degrees of security concerns, we do both—wipe the data then shred the drive—because they want to make sure the hard drive is destroyed. That is the highest end of service that can be provided. Most of the time, you either wipe the drives and resell them or you mechanically destroy them.
RT: How common is manual sorting to deal with low-grade material currently? Is this something that will realistically be replaced in the future?
SS: It is very common for two reasons. One reason is that virtually any recycler has to separate material prior to processing, and unfortunately for most of us we tend to get a mixed load of material coming in. You’ll get televisions and flat screens mixed in with printers and computer monitors and mice and keyboards. The collection of electronic scrap, generally, will give you a mixed load of material. You’ve got to do a lot of manual sorting when you get it, because you have to separate the glass-based products from the nonglass-based products.
Then, depending on the recycler’s business and the size of the facility, material that can be resold may be separated from material that is old and damaged or broken and needs to go into the recycling process.
I think it will evolve; right now a lot of that manual sorting happens on tabletops where material is off-loaded from trucks. I think we will see a lot more bulk handling of material, so it might be collected loose in a truck or a roll-off bin, and the roll-off bin will be unloaded onto a giant conveyor belt. Then the sorting will take place as it runs along the conveyor belt. You’ll still see manual sorting, but you’ll try to automate it as much as you can.
Steve Skurnac is president of Sims Recycling Solution (SRS) America, headquartered in Chicago. More information about SRS is available at simsrecycling.com.
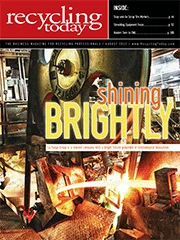
Explore the August 2012 Issue
Check out more from this issue and find your next story to read.
Latest from Recycling Today
- Toppoint Holdings expands chassis fleet
- Lego creates miniature tire recycling market
- Lux Research webinar examines chemical recycling timetables
- Plastics producer tracks pulse of wire recycling market
- Republic Services, Blue Polymers open Indianapolis recycling complex
- Altilium produces EV battery cells using recycled materials
- Brightmark enters subsidiaries of Indiana recycling facility into Chapter 11
- Freepoint Eco-Systems receives $50M loan for plastics recycling facility