![]() lightpro; Dreamstime.com |
Harsh economic down cycles tend to cause a shakeout in the American steel industry, as some of the least cost-efficient mills are idled either temporarily or permanently.
The downturn of 2008 and 2009 caused several casualties, and the tepid pace of the economic recovery is putting several other steelmakers in difficult financial positions.
For most of 2012 and into 2013, the steel mill capability utilization (capacity) rate calculated by the American Iron and Steel Institute (AISI), Washington, D.C., has hovered in the 75 percent range.
While this rate can go much lower—and did in 2008 and 2009—it has some analysts pondering likely targets for mill shutdowns or mergers that can lead to idled capacity.
Construction Quiet Zone
As the U.S. economy recovered from the banking and investment industry’s bailout (and the soon-to-follow auto industry bailout) in 2010 and 2011, the steel industry experienced an uneven recovery.
As vehicle sales rebounded, flat-rolled steel mills increased their output, and as infrastructure projects received allocated funding, some rebar mills benefited.
The construction industry however, has yet to approach the activity levels it enjoyed in 2005 or 2006. As a result, steel beams and plate have remained in low demand, rebar making has not fully recovered and even sheet steel could benefit if more new home buyers also were in the market purchasing washers, dryers, refrigerators and air conditioners.
In early 2013, the investment advice website Motley Fool (www.fool.com), looking at the recent financial performance of U.S.-based steel producers, commented, “Major U.S. steel companies have had nowhere to hide from the crumbling nonresidential construction market since its peak in July 2008; major domestic [steel] producers have suffered much more than the overall [stock] market.”
In late May 2013, steel industry analysts Peter Marcus of World Steel Dynamics, Englewood Cliffs, N.J., offered little short-term encouragement, predicting the steel industry will continue to travel the “rutted road” it started out on in 2008 through the rest of this year and 2014.
Marcus, speaking at the Bureau of International Recycling (BIR) World Recycling Convention in Shanghai, said steel demand in Europe looks likely to remain low in 2013 and 2014 and that even China, with its slower GDP growth, faces overcapacity. “When economies grow more slowly, steel intensity drops,” he commented.
The ruts in the road for U.S. steelmakers are clear when looking at output statistics for the first four months of 2013.
According to figures reported to the Brussels-based World Steel Association (WorldSteel), steel output in the U.S. declined 7.3 percent from the first four months of 2012, dropping from 31 million metric tons produced in 2012 to 28.8 million metric tons in early 2013.
Neighboring Canada is reporting similar conditions, with output there down 4.3 percent in the first four months of 2013.
U.S. steelmakers were already discouraged heading into 2013, particularly when looking at the critical construction sector.
In its early 2013 essay on U.S.-based steel producers, the Motley Fool notes that when asked about nonresidential construction spending in its third quarter of 2012 earnings call, Charlotte, N.C.-based Nucor Corp. then-CEO Dan DiMicco replied, “We are still seeing abysmal levels overall.”
Less Money, More Problems
Ferrous scrap dealers anticipating a boost from overseas steelmaking activity may not receive any such boost in late 2013.
In Europe, the ongoing parade of government bond and debt bailouts and austerity measures has harmed not only the construction sector but also has eroded purchases in the automotive industry—the other major pillar of steel consumption.
Whereas America’s steelmakers have witnessed 10 percent growth in output since 2010, European steel production declined sharply in 2012 and continues to sink in 2013.
WorldSteel figures showed output in the 27 EU nations at 169.4 million metric tons in 2012, down some 4.7 percent from the 177.7 million metric tons made in 2011.
Nations most severely troubled by government debt and austerity measures are responsible for a healthy portion of that decrease. Although it is not a major steel producer, production in Greece fell a staggering 35 percent compared with 2011.
The more sizable economy of Spain also is reeling. Steel production in that nation has dropped from 16.3 million metric tons in 2010 to 15.5 million metric tons in 2011 to 13.6 million metric tons in 2012. Steel production plunged nearly 17 percent from 2010 to 2012.
In Germany, the EU’s largest steelmaking nation, output has experienced ups and downs during the past two years, with 2011’s output having increased by 2.7 percent compared with 2010’s. Output in 2012 receded by 3.7 percent, however, falling from 44.3 million metric tons produced in 2011 to 42.7 million metric tons in 2012.
The growth of China’s steelmaking production has followed a rocket-like trajectory since the mid-1990s, when the nation’s economic reforms and massive infrastructure spending kicked into gear.
In 2012, the nation continued to churn out steel but not necessarily profits. In terms of output, WorldSteel figures showed China producing 716.5 million metric tons in 2012, up 3.1 percent from the 694.8 million metric tons made in 2011.
While annual Chinese steel production continues to break its own record each year, the over-heated furnaces are not necessarily producing a financial bonanza for Chinese steelmakers.
A report in the Beijing-based China Daily in late 2012 refers to Chinese steelmakers as “posting whopping losses in the first three quarters” of 2012.
China Daily reports that Liu Zhenjiang, vice president of the China Iron and Steel Association (CISA), speaking at an industry conference in November, said “most large and medium-sized steel companies have [been] suffering losses.” According to China Daily, Liu said, “The year 2012 is the most difficult year for China’s steel industry since the beginning of the 21st century.”
As 2013 hits its midway point, unrest in Turkey is likely catching the attention of those in the ferrous scrap and steel industries. Turkish electric arc furnace (EAF) mills have been absorbing scrap at healthy levels for several years, as that nation’s mills provide steel for the Persian Gulf region as well as for considerable infrastructure spending within Turkey. (See “Next Boat Out” below.)
Should economic growth, infrastructure spending and foreign direct investment in Turkey hit a rough patch, its industry would almost certainly feel the effects.
Next Boat Out Among the year-end 2012 figures to be found in the publication are a list of the world’s leading ferrous scrap exporters and importers. As in 2011, the United States was the leading exporter in 2012, shipping some 21.4 million metric tons to other nations. The U.S. was followed by the European Union at 19.2 million metric tons; Japan at 8.5 million metric tons; Russia at 4.3 million metric tons; and Canada at 4.2 million metric tons. The leading destinations for this scrap also remained largely unchanged in 2012 compared with the year before. Turkey imported 22.4 million metric tons, followed by South Korea at 10.1 million metric tons and India at 8.1 million metric tons. India surpassed China for that third spot in 2012, while China finished fourth by importing 4.97 million metric tons, just barely edging out Taiwan at 4.95 million. |
Still Need To Melt
Steelmakers throughout the world in late 2013 are facing regional economic circumstances but also may face a common dilemma in terms of securing feedstock.
Several years of modest manufacturing output and a weak construction sector in both Europe and the United States have resulted in scrap generation rates that are struggling to keep up with global EAF demand for ferrous scrap.
In the U.S., a surge in natural gas production points to the increased use of direct-reduced iron (DRI) or other scrap alternatives in EAF production. Nucor Corp., despite owning the David J. Joseph Co., is investing heavily in a direct reduced iron production plant in Louisiana.
Nucor is not alone. A late December 2012 report from Bloomberg refers to operators of several existing or proposed U.S. steel mills investing to use DRI as feedstock now that natural gas has become abundant and affordable there. The Bloomberg article refers to five such projects:
- The Nucor facility in Louisiana is expected to come online yet in 2013.
- Nucor may be researching a second DRI project, likely north of Louisiana in a region with abundant natural gas.
- Voestalpine AG of Austria is considering building a $655 million steel mill in the United States in part because of affordable energy costs.
- Australian steelmaker Bluescope Steel Ltd. is considering building a DRI plant, perhaps near its Delta, Ohio, steel mill, along with a joint venture partner.
- Bank analysts in late 2012 indicated that Indian steelmaker Essar Global Ltd. is researching the possibility of building a DRI plant in Minnesota.
The pricing, supply and demand interplay between DRI and ferrous scrap has shown an established pattern in the United States. Historically, DRI production hits a price floor tied to natural gas costs that renders it competitive for relatively narrow windows of time. However, ferrous scrap prices have sustained themselves at $350 or more per short ton for several years, and seldom has natural gas been as abundant and affordable as it is set to be in 2013.
As ferrous scrap recyclers from around the world gathered in Shanghai for the BIR Convention, Marcus predicted raw material costs are on their way to heading back in favor of scrap as a feedstock.
China’s ferrous scrap reservoir has been building, said Marcus. He forecasted that by 2025 China will have a ferrous scrap surplus of 145 million tons per year, “given the same EAF steelmaking and BOF (basic oxygen furnace) scrap usage figures.”
Even if China adds EAF capacity and charges more scrap into its BOF mills, Marcus foresees “75 million tons of surplus” scrap in China annually by 2025.
“Steel’s iron age is over,” said Marcus, who predicted some Chinese steel mills would be idled as that nation’s GPD growth rate subsides. “Who’s going to build a new integrated mill in that environment?”
Unfortunately for executives at steelmaking companies, a number of strategic missteps are likely to take place as they try to determine which feedstock to use, which mills to invest in and how to deploy assets in a changing environment.
The author is editor of Recycling Today and can be reached at btaylor@gie.net.
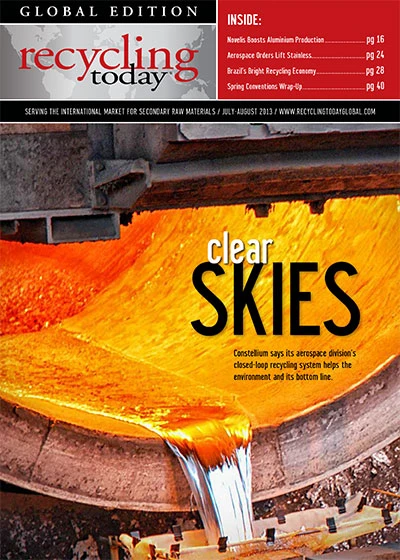
Explore the July 2013 Issue
Check out more from this issue and find your next story to read.
Latest from Recycling Today
- Magnomer joins Canada Plastics Pact
- Electra names new CFO
- WM of Pennsylvania awarded RNG vehicle funding
- Nucor receives West Virginia funding assist
- Ferrous market ends 2024 in familiar rut
- Aqua Metals secures $1.5M loan, reports operational strides
- AF&PA urges veto of NY bill
- Aluminum Association includes recycling among 2025 policy priorities