Many organizations within the recycling industry hope for zero accidents. These organizations spend significant resources on safety but often do not achieve the results they are hoping for. Many of the safety activities are well-intentioned but are not based on a real plan or strategy to reduce losses. What many of these organizations lack is a safety process.
A safety process is a strategic plan that uses a series of activities and events that are designed to reduce losses. An effective safety process will use measurements for each element to track goals, completion and results. The objective is to align safety as a process within an organization that is managed as any other process that drives the success of an organization.
Essential Elements
Developing an effective safety process does not have to be overly complex. Successful operations have developed processes that can be referenced and tracked toward a specified goal. An effective safety process follows the same basic principles. Safety activities that are not a part of a defined process are likely to be random and create inconsistent results.
An effective safety process has identifiable elements. Each element contributes to the overall success of the strategy. The six key elements include:
- A written program;
- Safety training and communication;
- Evaluation and monitoring;
- Claims management;
- Benchmarking; and
- Employee health and wellness.
(Part 1 of this article will address the first three of these six elements.)
Put it in writing
Written safety policies are similar to blueprints for constructing a building in that they provide direction and guidance toward a goal or outcome. The goal of safety is to limit losses and to comply with OSHA (Occupational Safety and Health Administration) regulations. Companies also are likely to have a few other definable goals for their safety programs. Most recycling operations have documented safety policies of some form.
Common weaknesses of safety policies are that they are too generic, overly technical or do not effectively communicate the day-to-day dos and don’ts workers need to know. Additionally, many companies with written safety policies do not put the actual policies in the hands of their workers.
Examples of some of the common safety policies that recycling companies need to ensure OSHA compliance and to manage their exposure include:
- Lockout;
- Electrical safety;
- Fall protection;
- Personal protective equipment (also known as PPE);
- Hot work;
- General safety rules;
- Disciplinary;
- Drug/alcohol;
- Accident investigation;
- Hazard communication;
- Emergency response; and
- Machine guarding.
At a minimum, each of these areas requires safety policies and, most likely, policies will be required for other more specific areas.
When policies are developed, they also must be implemented and communicated throughout the organization. Safety is a dynamic topic that changes over time. Policies should be reviewed annually to determine if they meet all of the exposures for an operation. It is likely that some safety policies will require periodic updates.
Train and communicate
Most organizations have very good intentions to train their workers about safety issues. Quite often, however, this training gets put onto the back burner and another year passes without conducting meaningful safety training for the average worker.
A good safety process includes a needs assessment regarding safety training and has an annual safety training plan. An annual safety training plan will consider which employees require training, resources for training and frequency of training.
In general, safety training topics should include the topics covered in a company’s written safety policy manual. Additional topics such as general hazard recognition should be included in the annual plan.
Some additional considerations for training include:
- All safety training activity must be documented. Documentation will include date, trainer, topic and copy of handouts used.
- Safety training must be presented in a language that each member of the workforce understands.
- To be effective, safety training should be completed periodically throughout year. A single annual safety training event is not as effective as ongoing safety training events.
- Short weekly safety training discussions, or tool-box talks, can be an effective way to keep the safety at the forefront of an operation.
Evaluate and monitor
OSHA requires that “frequent and regular” safety inspections be performed at workplaces. This is another key element of an effective safety process.
Regular safety inspections will identify hazards, effectiveness of safety policies and application of safe work practices. They also will help increase overall safety awareness at the facility.
Key areas to self-evaluate include:
- Physical conditions;
- Use of PPE;
- Fire protection;
- Equipment use;
- Safe work practices; and
- Driver operations on the tipping floor and around the facility.
A location-specific inspection form should be developed for a facility to efficiently address key safety issues. The results of a safety inspection should be addressed by the appropriate supervisors for follow up. Any unsafe conditions must receive immediate corrective action. Unsafe work practices should result in brief safety discussions or safety training with effected workers. The results of the inspection also should be shared with workers for their knowledge and to continually promote safety awareness.
Like any other safety activity, safety inspections should be documented and maintained on file. Corrective action also should be documented for any safety concerns noted in the inspection.
These three elements start the path to an effective safety process. A future issue of Recycling Today will address the remaining three key safety elements: claims management, benchmarking and employee health and wellness.
John E. Schumacher is a certified safety professional (CSP) and an insurance and risk management professional with more than 20 years of experience assisting organizations in developing strategic approaches to reducing losses and managing insurance costs. Sample safety inspection forms and other information are available from Schumacher by emailing jschumacher@assuranceagency.com or by calling 847-463-7224.
Get curated news on YOUR industry.
Enter your email to receive our newsletters.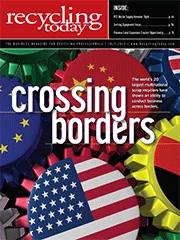
Explore the July 2012 Issue
Check out more from this issue and find your next story to read.
Latest from Recycling Today
- Altilium produces EV battery cells using recycled materials
- Brightmark enters subsidiaries of Indiana recycling facility into Chapter 11
- Freepoint Eco-Systems receives $50M loan for plastics recycling facility
- PET thermoform recycling the focus of new NAPCOR white paper
- Steel Dynamics cites favorable conditions in Q1
- Hydro starts up construction in Spain
- Green Cubes unveils forklift battery line
- Rebar association points to trade turmoil