The use of optical sorters for the purpose of positively sorting aseptic beverage containers and cartons is on the rise at larger material recovery facilities (MRFs).
It’s a well-known technology, yet is also one that’s been seldom used in the U.S. to sort cartons. However, that may be changing.
The practice of recycling cartons is rising thanks to an ongoing initiative driven by the Carton Council, a group that comprises four carton manufacturers—Elopak, SIG Combiblock, Evergreen Packaging and Tetra Pak—and associate member, Weyerhaeuser.
The packaging manufacturers understandably want to prevent their highly recyclable product from coming to an unpopular end that threatens to put the marketability of their products at stake: the landfill.
“Across the rest of the world the infrastructure for carton recycling is very well-established, but for a variety of reasons that infrastructure here in the U.S. didn’t develop,” observes Jim Frey president of Resource Recycling Systems, a consulting company that represents the Carton Council.
Building an infrastructure
That cartons should end up in landfills is an apparent waste of resources, recycling industry professionals say.
“The stuff itself is easy to recycle,” says Alex Wolf, sales engineer for Titech, distributed nationally by Van Dyk Recycling Solutions of Stamford, Conn. “It has valuable fiber in it that’s desirable for recycling.”
Recycled cartons serve as an ideal feedstock for the production of market pulp, which is used for a number of paper products.
To help increase recycling of cartons, the Carton Council has devised numerous interdependent strategies to ensure the product is recycled and that the demand for positively sorted cartons remains solid.
One of those strategies has been encouraging the use of optical sorters specifically tuned to sort the cartons and aseptic containers in larger MRFs. The council has done that by providing larger MRFs with equipment grants toward the purchase of optical sorting systems.
“We basically will give them an equipment grant if needed to pay for all or some of the cost,” Frey says. In effect, the Carton Council aims to remove any capital hurdle that would prevent aseptic sorting, he explains.
“As of now the Carton Council has funded over 20 optical sorters that are now actively functioning in larger MRFs across the country,” Frey says, “and we have more coming online practically every week.”
Frey says these systems are sophisticated installations where the optical sorting equipment is integrated into the MRF’s complete conveying and sorting system, and practically all are in single-stream operations.
While the Carton Council has partnered with the numerous equipment vendors on the market, it doesn’t select the equipment.
“We are neutral about suppliers,” Frey says. “We know from talking with each of these vendors that they all have the capability to tune the optical sorting equipment to identify and separate the carton.”
Frey says the largest MRFs should ideally have an optical sorter fully dedicated to sorting the polycoated cartons. The council also has funded some installations of dual-eject optical sorters that will sort for two different materials, such as cartons and 3-7 plastics.
Optical technologies
In most cases, optical sorters use near-infrared spectroscopy to identify the carton material in the container stream. It’s a technology that has been available to the field of container sorting for years, manufacturers say.
Felix Hottenstein, sales director of MSS Corp., Nashville, Tenn., explains that the NIR sensors are tuned to look for the cartons’ polyethylene layer and fibrous backing. When the levels of each are determined to be within certain ranges, he says, “the sensor knows it’s an aseptic packaging versus an HDPE (high-density polyethylene) bottle or versus a piece of cardboard,” he says.
MSS manufactures the CartonSort NIR Sensor Sorting System.
National Recovery Technologies Inc., or NRT, also uses infrared technology to sort cartons. “We are able to identify carton material and distinguish it from similar things like paper and plastic,” explains John Thomsen, engineering manager with NRT, based in Nashville.
Likewise, Wolf says Titech’s Autosort product range can be programmed to sort for PET (polyethylene terephthalate), HDPE (high-density polyethylene), mixed plastics or aseptic containers.
One newer technology that’s recently been marketed for sorting cartons is the Green Eye Optical Sorting System, from Green Machine Sales, Hampstead, N.H.
John Green, president of the company, says this patent-pending technology looks at materials three-dimensionally as well as at a molecular level.
“The technology allows us to sort not only by molecule type but also allows the system to see through certain packaging,” Green says. He explains that the system can “see” the shape and color of items in addition to the molecular structure.
“Not only are we identifying items we want to sort, but we are also singling out items we do not want to sort,” Green says.
One common example is aluminum cans, he adds. Green says the system is capable of drawing a circular target around aluminum cans in the stream and will not fire on any item that’s leaning up against the can, “so there’s no chance that we accidentally pick up that aluminum can.”
Green says aseptic cartons are probably one of the easiest recyclable items to sort. “The molecules we’re looking for are very bold and unlike anything else on the belt,” he says.
Logistical issues
The best location in the container line for optical sorters to recover containers can vary depending on a number of factors, but many manufacturers say they are best located at the end of the container line.
Jeffrey Van Galder, executive vice president of Karl W. Schmidt & Associates, Commerce City, Colo., the U.S. distributor of RedWave optical sorters, says the sorters are best placed after the fines screens and then perhaps after a magnet and eddy current. “Aseptic containers can then more easily be detected and rejected with air nozzles,” Van Galder explains.
Wolf also says the optical sorters should probably be placed at the very end of the container line, simply because there are fewer containers in the stream at that point. “It makes it easier if most of the other items have been removed,” he says.
Hottenstein agrees the sorters can be particularly useful if placed at the end of the container line. “The residue always has some recyclables that were missed,” he says, “so if you let the cartons be sorted at the very end of the line, you could also use the same machine to recover anything missed by the upstream equipment or the sorting people.”
However Hottenstein adds that MSS normally prefers to place the optical sensors before the eddy currents on the container line, particularly considering that some containers have an aluminum layer. “If you have the eddy current first, then some of the cartons that have the aluminum layer might actually jump with the cans,” he says.
Green says the Green Eye Sorter might be placed after the PET sorter, considering that PET accounts for 50 percent of the container stream, but it certainly doesn’t need to be placed there. In fact, Green adds, the sorter could be placed anywhere on the container line.
“The less product you have on the belt, the better job it’s going to do,” Green adds.
As the percent of cartons in the container stream grows, the placement of the sorters could also change, Wolf says. “If the Carton Council is really successful and introduces more Tetra Pak packaging, then the position of the machine could change depending on the volume that is there,” he says.
A growing market
Optical sorting of cartons is apparently growing, equipment vendors say. Alain Descoins, CEO of Pellenc ST America, says so far the company has sold a few installations in recent years for the sorting of cartons in the U.S. “People are just getting started to use optical sorters for aseptic,” he says. “It’s the beginning of the process.”
Descoins says to justify the addition of an optical sorter for cartons, “it’s good to be able to sort about 1 ton an hour of the material you want to resell,” he says. Knowing the ratio of cartons in the typical residential stream, he says, that means a MRF will need more than 10 tons per hour in the container stream to justify the sorter.
One MRF that recently installed an optical sorter specifically to recover cartons is Rumpke Consolidated Cos., headquartered in Cincinnati.
The company recently upgraded its Columbus, Ohio, MRF, and, with the help of a Carton Council grant, added a fifth Pellenc optical scanner on its container line for carton recovery. The 40-ton-per-hour facility serves several thousand households.
David Schwendeman, recycling market manager for Rumpke, handles the marketing of the MRF’s truckloads. “I can tell they’ve picked up the pace,” he says of Rumpke’s carton recovery.
Schwendeman notes that with the high grade of paper in this stream and a demand for tissue, for which it serves as feedstock, “there’s no trouble moving this material to the mill system.”
But, he adds, without the grant, adding the optical scanner would have been a difficult decision. Fortunately, Rumpke’s fifth Pellenc scanner accomplishes two tasks at once. “It not only recovers the cartons but also recovers all the 3-7 plastic optically.”
He says Rumpke’s work recycling cartons looks promising and also appears to be growing. “Our subscription customers know they can recycle cartons,” he says. “We recover cartons, and we move them through a broker in the Carton Council, so it claims the whole loop, and that’s the kind of thing they want to see.”
The author is managing editor of Recycling Today Global Edition and can be contacted at lmckenna@gie.net.
Get curated news on YOUR industry.
Enter your email to receive our newsletters.
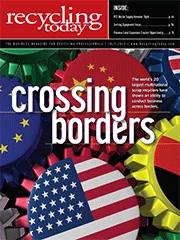
Explore the July 2012 Issue
Check out more from this issue and find your next story to read.
Latest from Recycling Today
- Plastics association quantifies US-EU trade dispute impacts
- Nucor expects slimmer profits in early 2025
- CP Group announces new senior vice president
- APR publishes Design Guide in French
- AmSty recorded first sales of PolyRenew Styrene in 2024
- PRE says EU’s plastic recycling industry at a breaking point
- Call2Recycle Canada, Staples Professional expand partnership
- Circular Services breaks ground on north Texas MRF