Republic Services Inaugurates Jacksonville, Fla., MRF
Phoenix-based Republic Services has inaugurated its Jacksonville, Fla., material recovery facility (MRF). The MRF, with processing lines built by Machinex, started operating at the beginning of April.
Machinex, based in Plessisville, Quebec, Canada, says the MRF is designed to offer flexibility, with the ability to process three different streams from its tipping floor.
The company says the system can process more than 22 tons per hour while processing up to eight tons per hour of dual-stream containers simultaneously. Furthermore, the system is designed to process commercial recyclables and single-stream residential material without having to man the container line with a bypass back to the tipping floor, Machinex says.
“We believe Republic Services appointed Machinex for the project because of the design proposed, which truly took into consideration all of the market conditions for Jacksonville that were presented to the bidders,” says Nicolas Belanger, President of Machinex Technologies. “With a combination of dual-stream and the future conversion of single-stream, Machinex designed a solution to handle the needs of today with strong consideration of the growth for tomorrow. We brought them a different approach.”
According to Machinex, the system is designed with a total shift from dual-stream to single-stream collection. The company says Republic will be able to upgrade the system without prolonged downtime. It also is described as the first regional MRF in Republic Services’ history to be designed and built from the ground up.
Machinex and Republic Services partnered in 2010 on the Lakeland, Fla., MRF, and a single-stream MRF is set to be built in St. Louis this the summer.
The Jacksonville MRF features a triple-deck OCC screen, a glass-breaker screen, a dual scalping screen, a double-deck ONP screen and a 3D finishing screen. Machinex also incorporated three optical sorters, a walking floor bunker, glass cleanup system and two rejects compactors.
The CP Group Releases i-MRF Software
The CP Group, San Diego, Calif., has announced the release of its i-MRF™ software.
Key benefits of i-MRF™ are based on seamless data acquisition and control of processing equipment across the plant floor, combined with real-time reporting and integrated diagnostics, which are accessible via Internet based technologies, the company says.
In early 2012, the CP Group acquired systems integration company Advanced MRF. Richard Price, general manager of Advanced MRF, says, “We are enthusiastic about how this systems intelligence, encompassed by the term i-MRF™, is going to improve our customers’ operations by giving them the tools they need to improve their bottom line.”
Bob Davis, CEO of the CP Group says, “Our goal is to give our customers the ultimate competitive advantage, and this is achieved through the implementation of our i-MRF™.”
Behr Iron & Metal Launches $30 Million Expansion
Behr Iron & Metal, headquartered in Rockford, Ill., is expanding its presence in the Midwest at what the company says is the fastest pace in its 105-year history. To meet the demands of its customer base, Behr recently embarked on a $30 million plant expansion that will put modern scrap processing technology into its Peoria, Ill., and South Beloit, Ill., yards. The company adds that the new equipment will expand its overall capacity and help position Behr for significant growth going forward.
Mike Schwebke, Behr vice president of operations, says, “We’re just doing what Behr Iron & Metal has always done in uncertain economic times—invest big in the future.”
The expansion includes the installation of a Metso shredder a Behr’s Peoria facility. The shredder started operating in March 2012.
The 104-inch, 5,000-horsepower shredder is expected to increase the capacity of the facility from 60 tons per hour to 120 tons per hour, the company says.
Behr also has invested in the installation of an $1.1 million metal recovery system that includes a Steinert US DMS Separator to recover ferrous nuggets and ferritic dirt, according to Ridley Stone of Wendt Corp., and a Wendt Titech Finder. This is the first time the DMS and Titech Finder have been used in combination on the ferrous downstream to mine the metal from the fluff recovered by the pre-magnet air system, he says.
“This project is the first of its kind and it was completely tested, engineered and designed by Wendt using our experience, processes and technology,” Stone adds.
Behr’s South Beloit facility also is undertaking a similar expansion.
U.S. Shredder Hits the NASCAR Circuit
The No. 34 Ford race car piloted by David Ragan at the May 19 NASCAR Sprint All-Star Showdown at Charlotte Motor Speedway was be sponsored by U.S. Shredder and Castings Group, headquartered in Trussville, Ala.
The race marked U.S. Shredder’s first foray into NASCAR sponsorship, according to Front Row Motorsports, of which Ragan is a team member.
Front Row Motorsports says U.S. Shredder noticed Ragan’s strong run earlier this spring at Talladega (Alabama) and decided to come on board.
“We saw David and Front Row Motorsports running well, and we saw there was space available on David’s car, so we decided to contact Front Row Motorsports and see if we could work something out,” says Bill Tigner, president of U.S. Shredder and Castings Group.
U.S. Shredder supplies equipment and parts to the scrap industry, including shredding plants, castings, wear parts and service to scrap recyclers located throughout the world.
Midwest Equipment Dealer Adds Second Location
Sargents Equipment & Repair Service, based in South Chicago Heights, Ill., has opened a new location in Gilberts, Ill.
Sargents Equipment is an authorized dealer for Harris, Steinert, Link-Belt, Genesis, Young Corp., Winkle and Flip-Screen. The company says it also performs service “on all brands of mobile and stationary processing equipment.”
According to the company’s Don Davies, the Gilberts location will help Sargents “better service the scrap and recycling industries in Northwest Illinois and Southern Wisconsin.”
BHS Lands Large Order with SITA UK
The U.K.-based waste management and recycling company SITA UK has chosen Bulk Handling Systems (BHS), based in Eugene, Ore., to design, manufacture and install four systems at SITA’s material recovery facilities (MRFs) in the U.K. The facilities are in Avonmouth, Birmingham, Darwen and South London. Combined, the MRFs will be capable of processing more than 250,000 metric tons of recyclables per year.
SITA UK says construction on the first two systems, in Avonmouth and Birmingham, is expected to start later this year.
Sponsored Content
Labor that Works
With 25 years of experience, Leadpoint delivers cost-effective workforce solutions tailored to your needs. We handle the recruiting, hiring, training, and onboarding to deliver stable, productive, and safety-focused teams. Our commitment to safety and quality ensures peace of mind with a reliable workforce that helps you achieve your goals.
“These facilities, of which two will be built before the end of this year and two the following year, will provide us with additional processing capacity in strategic areas across the U.K., allowing us to improve our service offering to our customers,” says Ben Harding, SITA UK head of infrastructure development. “The new facilities will also lead to the creation of many jobs, both in their construction and long-term operation and maintenance.”
All four MRFs are being designed to handle mixed recyclables collected from commercial sources, primarily office buildings. The materials will look much like single stream, but will be much heavier in OCC than residential collections.
While each of the MRFs will be similar in nature, each is customized to the building they will be installed in, and each has changes to maximize the efficiency of local operations. BHS adds that the MRF to be installed at SITA’s Darwen site will be slightly smaller than the other three plants.
“We are excited to be working with BHS on these projects,” Harding says. “From the outset of this procurement, they have shown a key understanding of our key objectives in developing facilities that will allow us to recycle a wide range of materials but also have the flexibility to upgrade them in the future should we wish to target different markets.”
Steve Miller, CEO of BHS, says, “SITA UK is the type of visionary company that we believe make the best customers for BHS. We are thrilled to be entrusted with helping them grow their business for the future.”
SITA UK is a subsidiary of Suez Environnement and handles more than 8 million metric tons of domestic, commercial and industrial waste.
S+S Separation and Sorting Demonstrates New Glass Sorting System at IFAT Entsorga 2012
S+S Separation and Sorting Technology GmbH of Schönberg, Germany, has launched its new K9 Flash glass sorting system at IFAT ENTSORGA 2012. A new development used in the recycling of thin-sheet, container and flat glass, K9 Flash is designed to separate unwanted color particles and CSP (ceramics, stones, porcelain) from the cullet flow with minimum loss of good material. It also will detect and remove special glass, such as Ceran, the company says.
![]() |
According to S+S Separation, the space efficient design minimizes glass breakage and features new specific-light technology, allowing for greater throughput with precise detection.
The company says the K9 Flash system scans up to nine different wavelength ranges. This allows identification of color, CSP and heat-resistant glass. Unwanted material is removed from the material flow by air-ejection nozzles operating within one millisecond, according to S+S.
Hans Eder, S+S development manager, says, “Integral to the new system design are the many years of experience of our subsidiary KRS Recycling Systems GmbH. KRS has designed and built many turnkey glass recycling plants for both container and flat glass worldwide.”
He adds, “Extending the color spectrum analysis from the three basic colors to nine and increasing pixel resolution to 0.2 millimeters sets new accuracy standards in the field of glass sorting.”
Get curated news on YOUR industry.
Enter your email to receive our newsletters.
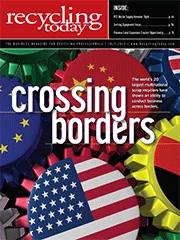
Explore the July 2012 Issue
Check out more from this issue and find your next story to read.
Latest from Recycling Today
- AF&PA report shows decrease in packaging paper shipments
- GreenMantra names new CEO
- Agilyx says Styrenyx technology reduces carbon footprint in styrene production
- SABIC’s Trucircle PE used for greenhouse roofing
- Hydro to add wire rod casthouse in Norway
- Hindalco to invest in copper, aluminum business in India
- Recycled steel price crosses $500 per ton threshold
- Smithers report looks at PCR plastic’s near-term prospects