![]() |
Recovering greater portions of nonferrous metals from auto shredder residue (ASR) has increased as a priority for many auto shredder operators. What’s more, processors want the metals they recover to be further separated into zorba and zurik, the specifications for which have been established by the Institute of Scrap Recycling Industries Inc. (ISRI), Washington, D.C.
To that end, equipment manufacturers have made technological improvements to help maximize the recovery and quality of nonferrous metals downstream of the auto shredder. While their objectives are the same, vendors have come up with numerous methods for achieving those goals.
In its “Scrap Specifications Circular,” ISRI defines zorba as shredded mixed nonferrous metals consisting primarily of aluminum generated by eddy-current or other segregation techniques.
Meanwhile, zurik is defined as nonferrous scrap that’s predominantly stainless steel and has been generated by computer sensing equipment, such as induction sensor sorting or X-ray techniques.
Being able to sort ASR to create these two products, at high purity levels, potentially differentiates one processor from another. The technology to do so can be costly but can result in more marketable and vualuable end products.
“Capturing only an extra few percentage points by weight of zorba and zurik can add tens of thousands of dollars per month to the bottom line and reduce landfill costs,” says Brian Vrablic, sales engineer with Eriez, based in Erie, Pa.
Total Recovery
Part of the objective is total metal recovery. Dennis Ciccotelli, scrap market manager for Steinert U.S., based in Erlanger, Ky., says ASR, which normally accounts for about one-fourth of the tonnage originally shredded, can contain from 5 to 10 percent metals. “We take this material that is 5 to 10 percent metal and we try to get 99 percent of the metal out,” Ciccotelli says.
Vrablic says shredder operators need to decide what level of separation they are trying to achieve and what that is worth to them. “The more you want to get, the more expensive it is,” he observes.
Manufacturers of downstream separation and sorting technologies tend to have similar but not identical methods for recovering these two products from ASR. Sizing the nonferrous material is often the first step in helping to create the zorba and zurik products, according to sorting equipment manufacturers.
Bill Close, sales engineer with Wendt Corp., based in Tonawanda, N.Y., says sorting ASR by size before it’s separated results in better quality. “We prefer different size cuts because it’s easier to tune the machines,” he says. This produces optimal sorting in terms of metals recovered, Close adds, in addition to improving the quality and cleanliness of that metal.
![]() |
Close describes a recent installation that sorts ASR using various screens into three fractions of different sizes. Each of those streams is then run through its own sorting processes. Each stream is first presented to a magnet to pull out ferrous dirt and fuzz, thus preparing the metal for the eddy current. “There is about 4 percent ferrous still remaining in the flow,” Close says.
Next, the eddy currents eject aluminum, brass and copper from the flow, but not stainless steel and wire, thus producing zorba, the first product stream to come off the plant.
“What’s not recovered by the eddy currents goes to the sensors,” Close says.
Wendt has partnered with Titech, which provides its Finder line of sensor-sorting equipment for recovery plants. Close says one set of Titech Finders can be used to remove the bulk of the material stream in just one pass: the nonmetallic landfill waste. With advances in sensor technology and imaging software technology, Close says, “We’re now actually in the territory of about 0.5 percent to 0.6 percent total metal content remaining in the trash stream.”
The remaining material can then be run through a second set of Finder sorters to refine the metal fraction of the stream further, producing zurik. “We are targeting and shooting the metal out of the flow and that would be taking the solids to make the zurik fraction,” he explains. Wire is deliberately missed in this process, Close says.
Finally, each stream is passed through a Titech Polyfinder to recover insulated and bare wire. The Polyfinder uses a sensor sorter to identify wire and a near-infrared optical sorter to identify the plastic insulation.
Close says those processors with lower tonnages and more time to spare also could use the Polyfinders to handle all passes of the nonferrous stream. “They can make an investment in just the Polyfinder and do multiple passes on the equipment,” he explains, selecting different parameters for each sort.
Recent Improvements
Heiner Guschall of SiCon GmbH, Hilchenbach, Germany, says until the introduction of sensor-based sorting systems some eight to 10 years ago, the loss of nonferrous metals in ASR was significant in the United States. Guschall says sensor-based systems allowed the dry separation of metals—stainless steel and wires—that might be missed by an eddy current. “These machines have been improved during the last years,” he says. Effective systems can separate wire and cable and stainless steel from other nonferrous metals.
Recent advances in nonferrous recovery technology revolve around fines and fluff processing, Vrablic says. “This technology includes high-strength magnetic separation aimed at fine ferrous, high-frequency eddy-current separators and induction sensor separation technology,” he explains.
Similarly, Guschall says the performance of eddy currents for the separation of zorba fines down to 1 millimeter and smaller has improved tremendously. “There are huge performance differences when we look at small particles,” he says. He points out that an eddy current shows better performance when it is fed by a defined fraction size. Guschall adds that screening to a defined size and ensuring there are few gaps in material are key. “This is often missing in older plants.”
Ciccotelli says another trend is using sorters with more than one type of sensor. “Today you can use three methods in some of these modern machines,” he says, citing shape, metallic level and color as the predominant factors. He also explains that multi-sensors have a “teach-and-learn mode” that will recognize materials approaching the sorter from numerous angles.
![]() |
During the last few years, Steinert U.S. has been employing a separating tower design for recovery plants in which ASR is lifted and then cascades through a variety of separation machines, using gravity rather than conveyors.
“If well designed it can be a very efficient operation and not take up a lot of space,” Ciccotelli explains. “The technique of using cascading machines helps to reduce material handling equipment and material spillage,” he says.
Ciccotelli says Steinert’s sensors are designed to take the nonferrous product and get it to as much as 99 percent purity, using sensors that analyze color, shape and even transmissive X-rays.
Induction sensors are used toward the end of the process to sort stainless steel, Ciccotelli says. “Stainless for us is easier to detect after all the ferrous and the nonferrous is out,” he explains. “Most of the metal that’s left in the fluff after those two major processes is stainless.”
Guschall points out that different equipment vendors have different philosophies when it comes to creating zurik. With the SiCon 100/120 system, he says, “we combine mechanical processing with the use of sensor machines and achieve metal purities of much more than 90 percent and at the same time no loss of metals in the waste.”
Eriez meanwhile uses the ProSort II, an airless paddle-driven induction sensor sorter to process the waste product off the eddy currents. Vrablic says material must generally make two passes through the sensor machines to make a quality zurik product. “The first pass gets all the metal, and the second pass cleans that metal up,” Vrablic explains.
A Uniform Flow
Close says the performance of ASR recovery and sorting technology is best enhanced by having conveying systems that deliver a uniform flow, as opposed to surges of material. Toward that end, Close also says Wendt’s nonferrous recovery and refinement plants are designed to be used offline from the the shredding plant to better manage material flows. “Shredders will always produce surges of the material,” he says. He also points out that shredding operations tend to run at a much faster pace than do nonferrous recovery operations. “What we’ve observed is that when the two plants have been joined together you basically have the two management teams in disagreement,” Close explains. “That’s why we advocate for keeping the plants segregated, so that the management teams can each pursue their goals individually.”
Similarly, Guschall says an offline installation always has advantages. “We usually offer the customer the option of inline operation as the base case and off-line in case of surges,” he says. “If a plant is running inline, then a detailed analysis of the mass flow is necessary.” He explains that if shredder surges aren’t considered in the design of nonferrous downstream plants, they could lead to a loss of metals or inefficient use of the plant. “SiCon has an in-house developed mass-balance tool which simulates the massflow at each step of the plants so that we make sure that our plants never have such design deficits,” he says.
Meanwhile Vrablic says Eriez prefers to place its nonferrous equipment inline with the auto shredder, “because that reduces your material handling costs.”
However, he says processors still should allow for the ability to inject material into the delivery system offline. “It really is a good idea if you’re building a new nonferrous downstream or you’re building a plant that you allow for the ability to inject material into the downstream offline.”
He says this could be accomplished by having a dump hopper in front of the conveyor feeding the screener. Another reason for having this dump hopper, he adds, is because the material has to be run through the sorters twice generally.
The size of the operation is an important consideration in selecting nonferrous equipment. Ciccotelli says Steinert U.S. makes nonferrous sorting equipment for shredders processing from 60 tons per hour up to 400 tons per hour.
The company’s goal is to set up systems that will pay for themselves in about a year. “In some cases where we’ve added stainless steel to an existing system, we’ve had customers tell us that in 16 weeks they had recovered the cost of the machine,” Ciccotelli says.
The author is managing editor of Recycling Today Global Edition and can be contacted at lmckenna@gie.net.
Get curated news on YOUR industry.
Enter your email to receive our newsletters.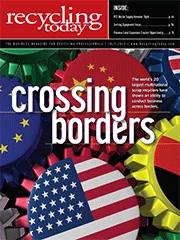
Explore the July 2012 Issue
Check out more from this issue and find your next story to read.
Latest from Recycling Today
- CP Group announces new senior vice president
- APR publishes Design Guide in French
- AmSty recorded first sales of PolyRenew Styrene in 2024
- PRE says EU’s plastic recycling industry at a breaking point
- Call2Recycle Canada, Staples Professional expand partnership
- Circular Services breaks ground on north Texas MRF
- Tariff uncertainty results in choppy nonferrous scrap flows
- CATL, Ellen MacArthur Foundation establish battery partnership