You already know that time is money. At no time or place is that more true than at a scrap yard, where unplanned equipment outages are about as unwelcome as guests without hard hats.
And during these competitive times, recyclers need to find their cost advantages where they can. Having a spare parts inventory might seem counterproductive to lowering costs. With so many model-specific parts, many of them expensive, deciding which to stock might be a challenge.
When you consider the time-savings potential of having certain spare items at your fingertips, a strategic spare parts inventory might deserve consideration. Scrap yards finding they have to wait for more than a few hours for an item their maintenance crews could easily replace themselves might quickly incur much greater costs in lost productivity than a few pre-emptively spent dollars on spare components.
Recycling Today talked to a few equipment dealers to identify common, and not-so-common, replacement items that might be worth investing in to reduce downtime and keep running without missing a beat.
Filters
The top items to stock, dealers say, are a set of the proper oil (both powertrain and hydraulic), fuel and air filters for the scrap handlers being used.
When it comes to the hydraulics system, says Gary Meister, general manager of product support for RECO Equipment Inc., based in Morristown, Ohio, most scrap handlers will require a handful of filters, along with multiple powertrain (for wheeled handlers) and fuel systems filters.
Meister says proper fuel filtration is even more critical with the newer Tier 4 compliant engines. “The tolerance for dirt and debris is so small that you have to have lots of filtrations to accommodate it,” he says. “You have a 10-micron filter all the way down to a 2-micron filter, which filters fuel down to a bacteria-sized product before it goes to the injection pump.”
Meister points out that a scrap handler’s fuel filters need to be changed regularly as specified by the manufacturer and depending on the type of fuel used. The interval can be anywhere from 250 service hours up to 1,000 service hours. And recyclers working in dustier conditions will probably need to change the filters more frequently, he adds.
Changing fuel filters only on a reactionary basis, Meister points out—such as when the engine begins to run poorly—can accelerate wear to internal components, leading to shorter service life.
Bill Dycus of Road Builders Machinery & Supply Co., Kansas City, Mo., says additional seals and parts also may be required along with the filters. For example, some hydraulic filters use O-rings on the seals that need to be replaced with each filter change and should not be reused. Some of these machines have pressurized hydraulic tanks, Dycus adds, and if an O-ring is not replaced along with the filter, the hydraulics system won’t be pressurized properly.
The same goes for the fuel filters, Dycus says. “If you don’t have a good seal, it will suck air and the next thing you know you don’t have fuel going to the engine,” he says.
While the filters are a normal preventive maintenance item, they also can occasionally be used for troubleshooting problems, says Ken Grabowski, parts manager for Gibson Machinery, based in Oakwood Village, Ohio. “Always have an extra hydraulic filter [and] engine filters on hand because you never know what’s going to happen,” Grabowski says. For example, in wintertime, if fuel line freeze-up is suspected, fuel filters can be replaced as one possible solution. Or if a catastrophic hydraulics system failure occurs, the filters could be changed in an effort to fix the problem.
Fuses
Dycus also suggests keeping fuses on hand. “A lot of machines have gone to the same types of fuses used in cars,” he says. Fuses are inexpensive—anywhere from 15 cents to 25 cents each, Dycus says, but a blown fuse can keep a machine from running.
“It’s not worth losing productive time on a hundreds-of-thousands-dollar machine for a 25-cent fuse.” Unfortunately, Dycus notes, he has run across situations where machines did not run simply because of a fuse.
Hoses and Couplings
Repeatedly, dealers also say recyclers should consider having hydraulic hoses and the appropriate fittings or adapters on hand. Any exposed hydraulic hoses on the machine are susceptible to damage. “It’s easy to get those hoses destroyed,” Dycus says. The damage can occur countless ways in a scrap yard, he says, from flying scrap to acid damage to getting them hooked on an object in the yard.
Grabowski points out that the hydraulic hoses underneath material handlers also are susceptible to damage, since scrap yards can be irregularly surfaced.
For these reasons, recyclers should consider having the various types of hoses and fittings needed for the grapple and cylinders going to the grapple. “Have two or three cylinders worth of hydraulic fittings for the grapple,” says Dycus.
When it comes to the hydraulic grapple, Dycus recommends recyclers consider keeping a spare set of couplings for between the grapple hose and the end of the stick. It’s easier and more justifiable to do this, Dycus adds, if the scrap yard has more than one of the same machine, so that one spare set will work for multiple machines. The couplings can be expensive—around $300 just for one side of the connection—and they are machine specific. “How much you want to keep on the shelf is determined by how much money you want tied up in parts that are hopefully going to sit there and how quickly can you get them from the dealer,” Dycus explains.
Grabowski points out that many customers might still need to take the hydraulic hose and adapters to their local hydraulics shop to have the hose made.
Magnetic Cables and Connections
As is the case with hydraulic hoses, electrical connections and cables for the magnetic work tools also can be vulnerable to damage. Having replacements for those is also a good idea, Dycus says. “Any kind of electrical connector for a magnet, you want a spare of.”
Similarly, the cable between the connector and the magnet is another item to stock. “Being able to replace that quickly is a good idea,” Dycus says.
Meister describes the magnetic cable as a very sophisticated extension cord going from the magnet attachment to the generator on the machine, and it is susceptible to damage just as hoses are. Any metal sticking up from the scrap pile can cut the cable or short out the magnet during the course of work, Meister explains.
“If a piece of metal splices one of those, you’re down,” he says, “which is why you should have those cables on your shelf.”
Meister says while most distributors will tend to stock these cables, having one on hand is also a good way to deal with this common problem.
Fuel Injectors and Fuel Hose
Dycus says recyclers may want one or two spare fuel injectors and some spare fuel hose. This is to quickly replace any fuel hosing that may become damaged. Any pin hole in the hose, he says, can cause a loss of fuel pressure. “They can be a pain to find,” Dycus says. “You can’t necessarily just go pick one up.” That’s because these hoses often have specially crimped ends and specific fittings. If the hose becomes pierced, the machine is out of service. Dycus says he has several customers that have opted to stock fuel hoses.
Because the fuel hoses sometimes have specific fittings and crimped ends, Dycus says they might only be supplied by the engine manufacturer, which could be a three-day wait. On the other hand, actually replacing the hose is a 30-minute job, he says.
“If it’s something that’s going to keep you down and take some time to replace, it might be a good idea to have one on the shelf, along with the seals that go with it.”
Other items to keep in stock, Dycus says, are replacement belts for the engine, generators and air conditioning system. “Any belts that can break will,” he says, noting that operators also need to pay attention to belt tension. “If an inner belt goes, it can easily take out all the rest of them,” Dycus adds.
Outriggers
Grabowski points out that some recyclers tend to have issues with outrigger cylinders or stabilizers, the feet that keep the handler stationary and prevent it from tipping over. “A lot of it depends on what you’re working in and low long the pieces are,” he says. “We have a lot of guys that damage those.”
The stabilizers also can sustain damage if the operator lifts something quite heavy or swings it improperly, leading to a safety issue. And, he says, a broken outrigger will take the machine out of service.
Deciding Factors
At the end of the day, though, scrap handler suppliers say they work to anticipate parts needs for their customers. Dycus points out that recyclers should think carefully about what they are going keep in stock and work with their dealer to come up with a plan.
“Dealers will frequently stock things specifically for customers,” he explains.
Grabowski points out that dealers often stock large inventories for their customers. “A lot of them don’t want to stock because stocking is money,” he says. “Our job is to make sure we have those items.”
Dycus says the end user needs to consider, “how much am I willing to put on the shelf dollarwise, and how much am I going to anticipate my dealer having on the shelf. Talk to the dealer, ask what they keep and how many spares.”
Ultimately, there are some things, Dycus says, there’s no point in keeping on hand. Other things, you definitely should. Knowing the difference could make all the difference.
The author is a managing editor with the Recycling Today Media Group and can be reached at lmckenna@gie.net.
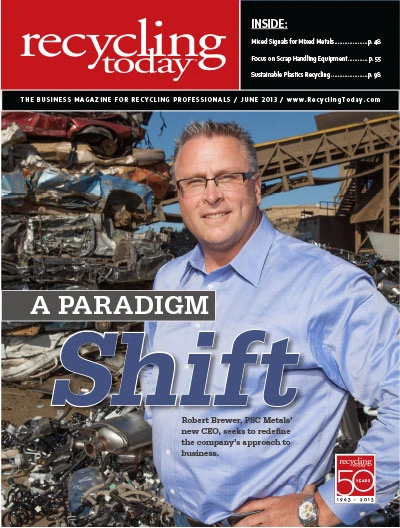
Explore the June 2013 Issue
Check out more from this issue and find your next story to read.
Latest from Recycling Today
- Aqua Metals secures $1.5M loan, reports operational strides
- AF&PA urges veto of NY bill
- Aluminum Association includes recycling among 2025 policy priorities
- AISI applauds waterways spending bill
- Lux Research questions hydrogen’s transportation role
- Sonoco selling thermoformed, flexible packaging business to Toppan for $1.8B
- ReMA offers Superfund informational reports
- Hyster-Yale commits to US production