LEGISLATION & REGULATIONS
EPA Approves ASR Plastic Reuses
The U.S. Environmental Protection Agency (EPA) has announced an interpretation of its regulations that will allow automobile shredder operators to recycle the plastic separated from auto shredder residue (ASR). Recycling can take place under conditions described in the “Voluntary Procedures for Recycling Plastics from Shredder Residue” document, relying principally on regulatory provisions for excluding PCB (polychlorinated biphenyl) products.
The Institute of Scrap Recycling Industries Inc. (ISRI), Washington, D.C., says resolving regulatory uncertainty could lead to investments and further development of innovative methods to separate plastics from ASR that would produce broad environmental benefits and increase global competitiveness. ISRI has developed a set of voluntary procedures designed to prevent the introduction of PCBs that are regulated for disposal into recycled plastics recovered from ASR.
“Voluntary Procedures for Recycling Plastics from Shredder Residue” includes development and implementation of a documented materials management system incorporating documented source control programs aimed at preventing the introduction of PCBs regulated for disposal into shredder feedstock materials that contribute to any ASR from which plastics will be recovered for recycling and documented output control programs for facilities processing, recycling or producing plastics from shredder residue.
EPA was approached by ISRI regarding separation, recycling, use and distribution of recycled plastics from shredder residue recovered from metals recycling facilities. In a letter dated Feb. 24, 2011, ISRI writes, “written confirmation that separating plastics from ASR aggregate for use and distribution in commerce, using processes that reduce any PCBs that may be present to a level at or below which there is no unreasonable risk, is authorized” under regulations promulgated pursuant to the Toxic Substances Control Act (TSCA).
In its letter, ISRI states that “... analysis shows that the separation, recycling, distribution in commerce and reuse of plastics from shredder aggregate is consistent with existing authorizations that allow the use and distribution in commerce of products that contain low levels of PCBs, including provisions for ‘excluded PCB products’ and ‘excluded PCB manufacturing processes.’”
TSCA section 6(e) generally prohibits the manufacture, processing, distribution in commerce and use of PCBs. However, EPA has by regulation excluded certain materials, including PCB products, from the prohibitions. Excluded PCB products are defined as PCB materials that appear at concentrations less than 50 ppm (parts per million), including but not limited to:
- Non-Aroclor (while PCBs were manufactured and sold under many names, the most common was the Aroclor series) PCBs inadvertently generated as a byproduct or impurity resulting from a chemical manufacturing process;
- Products contaminated with Aroclor or other PCB materials from historic PCB uses;
- Recycled fluids or equipment contaminated during use involving the products; and
- Used oils, provided that they contain less than 50 ppm concentration PCBs were legally manufactured, processed, distributed in commerce or used before Oct. 1, 1984.
The EPA says it believes that for shredders and their suppliers following the “Voluntary Procedures for Recycling Plastics from Shredder Residue,” it is appropriate to generally treat the feedstock as consisting of excluded PCB products unless there is information specifically indicating that the feedstock does not qualify. The EPA adds that if shredders and suppliers do not follow the Voluntary Procedures for Recycling Plastics from Shredder Residue they will need to be able to otherwise demonstrate that the materials meet the exclusion.
MUNICIPAL
Coca-Cola Awards Chicago $2.59 Million Grant to Boost Recycling
Chicago Mayor Rahm Emanuel, Atlanta-based Coca-Cola and Stamford, Conn.-based Keep America Beautiful (KAB) have announced a $2.59 million grant to support the expansion of Chicago’s Blue Cart Recycling Program through the purchase of 50,000 blue carts during the next five years.
“This grant will help expand blue cart recycling to all communities by the end of 2013 and pay for damaged and replacement carts for years to come,” Emanuel says. “With the help of Coca-Cola and Keep America Beautiful, Chicago will become a greener, more sustainable city.”
The Coca-Cola Co. and its philanthropic arm, The Coca-Cola Foundation, are granting $2.59 million over the next five years to KAB to increase recycling in Chicago. The investment will bring blue cart recycling to all 50 wards in the city, according to the trio.
“Our actions supporting Chicago’s sustainability reflect our belief that when we all work together, real progress happens,” says Steve Cahillane, president and CEO, Coca-Cola Americas. “By bringing business, government and community organizations like Keep Chicago Beautiful together, we can help create long-term solutions—here in Chicago and across the globe.”
Through the grant, 25,000 recycling carts will be delivered to Chicago neighborhoods. The Coca-Cola Co. will donate 25,000 more recycling carts over the next five years.
GLASS/ELECTRONICS
CEA, ISRI Seek Solutions for CRT Glass
The Consumer Electronics Association (CEA), Arlington, Va., and the Institute of Scrap Recycling Industries Inc. (ISRI), Washington, D.C., have announced a technical “CRT Challenge” to identify financially viable, environmentally conscious proposals for using recycled cathode ray tube (CRT) glass.
As CRT technology has been displaced in the market by liquid crystal display (LCD), light-emitting diode (LED) and plasma displays, the consumer electronics and recycling industries say new ways to recycle old CRT glass are becoming necessary.
In a jointly issued news release, CEA and ISRI say more than 2 billion pounds of legacy CRT TVs and monitors are expected to enter the recycling stream. And with demand for old CRT glass to make new CRT glass waning, the organizations say there is an increased need for additional environmentally sound, economically sustainable uses for this material.
In recent years, demand for CRTs has dropped drastically as newer LCD, LED and plasma technologies have become more affordable and widely available. As the making of new CRT displays had been the primary destination for recovered CRT glass, the end-use markets for CRT glass have now decreased considerably.
“The CRT challenge is a crowd-sourced technical competition to find new uses for old CRT glass,” says Walter Alcorn, vice president of environmental affairs and industry sustainability for CEA. “The consumer electronics industry is fully committed to eCycling, and this CRT challenge has the potential to uncover new, innovative electronics recycling.”
CEA and ISRI will accept submissions for the CRT Challenge until June 30, 2013, at www.innocentive.com/ar/challenge/9933317. The winning solution will be chosen based on economic and environmental benefits, with CEA awarding $10,000 to the winner.
The two groups also say they will publicize and share the solution(s) with manufacturers, retailers and recyclers and will encourage implementation.
“ISRI is very excited to be co-sponsoring the CRT Challenge with the Consumer Electronics Association,” says Robin Wiener, ISRI president. “The challenge presents a great opportunity to expand and develop new markets for recycled CRT glass and help recyclers as the industry transitions from CRTs to newer display technologies.”
“The EPA recognizes that the reduced number of facilities that accept processed CRT glass is posing challenges for recycling this material,” says Mathy Stanislaus, assistant administrator of the U.S. Environmental Protection Agency’s Office of Solid Waste and Emergency Response.
TIRES
Phoenix Industries Lands Asphalt Rubber Patent
Phoenix Industries, North Las Vegas, Nev., has been awarded a patent for its process related to the pelletizing of rubber modified asphalt (bitumen) used in the paving industry.
The patent covers the pelletization process and formula technology related to creating a premanufactured matrix of asphalt and modifiers with an outer shell coating to keep the pellets in a free-flowing form that is transported and stored at ambient temperature.
Phoenix says the process can save the energy required to keep the asphalt as a molten liquid. At the time they are used, the proportional amount of the pellets are mixed, either through a RAP (recycled asphalt pavement) collar of a continuous drum plant or directly into the mixer of a batch plant, where it is blended with the heated aggregate to produce a modified hot mix asphalt.
“This patent is a significant development that will let us move ahead with the introduction of new products,” says Serji Amirkhanian, Phoenix Industries director of research and development. “We have several materials and equipment designs in the pipeline that will expand our product line of green and sustainable innovations for the asphalt paving industry.”
METALS
OmniSource Opens Recycling Facility in Michigan
OmniSource Corp., a subsidiary of Steel Dynamics Inc., Fort Wayne, Ind., has opened its newest metals recycling facility in Coldwater Township in south central Michigan. A spokesperson for OmniSource says the new facility gives the company 10 locations in Michigan and a total of nearly 70 scrap recycling plants in North America.
Retail traffic will be the focus of the new facility, according to the company, though the site also will be able to handle scrap metal generated from industrial sources.
The new facility, on 6.5 acres of land, will accept ferrous and nonferrous scrap. Additionally, the facility will use a large portion of its acreage to handle auto parts. The property will have more than 400 vehicles on site to allow customers to salvage used parts.
Once the auto parts have been sold, the hulks will be shipped to OmniSource’s auto shredder in Jackson, Mich.
According to a local press report, the OmniSource property will feature swales that will allow the company to catch stormwater from the site.
GLASS
State Grant to Boost Rumpke’s Glass Recycling
The Ohio Environmental Protection Agency (EPA) and the Hamilton County Recycling and Solid Waste District have awarded a $250,000 recycling grant to Cincinnati-based Rumpke Recycling to finance glass recycling equipment.
The grant money will be used to install a glass recovery system at Rumpke’s new Cincinnati area material recovery facility (MRF). The new equipment is designed to screen, clean and sort glass at the company’s MRF.
After the glass is processed, it will be shipped to Rumpke’s Dayton, Ohio, facility for further processing. The processed glass will then be shipped to Owens-Illinois and Johns Manville to create glass containers and home insulation.
Johns Manville, based in Denver, manufactures insulation and roofing materials. Glass maker Owens-Illinois is headquartered in Perrysburg, Ohio.
“Today’s grant will help save landfill space and provide Ohio manufacturers with a necessary raw ingredient,” said Ohio EPA Director Scott Nally at an Earth Day Event at the Rumpke Recycling Cincinnati area MRF in St. Bernard, Ohio.
“Hamilton County has long been a leader in facilitating innovative recycling and solid waste solutions,” said County Commissioner Greg Hartmann. “This glass recycling project will provide both environmental and economic benefits to our community.”
Rumpke Consolidated Cos. Vice President Jeff Rumpke said, “This partnership ensures that when a resident recycles a glass bottle, the result is economic growth, new jobs and new products and, overall, far-reaching environmental benefits.”
According to the Ohio EPA, Ohio’s glass makers estimate they could use an additional 165,000 to 185,000 tons of cullet each year. Because 90 percent of Ohio’s postconsumer glass ends up in landfills, Nally says there is an opportunity for the state to help harvest a secondary raw material from what would have been waste.
Rumpke Recycling first invested in glass recycling in 2004 with the construction of its own glass processing facility in Dayton. With a $500,000 Ohio Department of Natural Resources grant, Rumpke completed a $4 million upgrade of that facility in 2011. Rumpke Recycling, a privately owned waste and recycling firm, provides services in Ohio, Kentucky, Indiana and West Virginia.
PLASTICS
APR Opposes Degradable Additives in Plastics
The Association of Postconsumer Plastic Recyclers (APR) has issued a statement reiterating its long-standing opposition to the use of degradable additives in plastic bottles, containers and films.
“Since mid-2009 APR has repeatedly asked those who sell and those who use Oxo-degradable or biodegradable additives to consider the sustainability implications of those additives on the recyclability of packaging,” says Steve Alexander, APR director. “We have asked for the data that support the claims of bottles containing the additives would have no impact on the recyclability of a bottle, including next use life. We have seen no credible supporting data. Without mitigating data, we must oppose the misuse of such additives in recyclable plastic.”
John Standish, APR technical director, says, “The real concern is the impact of a degradable additive once the plastic is recycled and used in second and successive applications. A great deal of recycled plastic goes into carpeting, geo-textiles, strapping, plastic lumber and pipe. All are long-lived uses. Some of these products have a 30-plus-year expected life span. What happens if the polymer molecules break down during the expected service life? Failure and potentially expensive remediation likely result.”
APR adds that it is reinforcing its support of legislation currently being considered in North Carolina and Alabama that would prohibit the use of the term “degradable and recyclable” on the label of a container and require containers with degradable additives to be labeled “do not recycle.” APR recommends environmental certifying organizations always include the impact of degradable additives on plastics recycling before permitting use of logos.
“Containers with these degradable additives can seriously impair the integrity of the plastic packaging recycling stream,” adds Alexander. “We have asked the additive providers to prove no harm done and have received no satisfactory answers. Hostile degradable additives not only mean the packaging containing them is unsuitable for recycling, but physically adjacent items are also rendered unfit.”
ELECTRONICS
ECOvanta Achieves E-Stewards Certification
ECOvanta, the recycling subsidiary of Covanta, has been certified to the e-Stewards Standard for Responsible Recycling and Reuse of Electronic Equipment®, developed by the Basel Action Network (BAN), Seattle. ECOvanta, located in Philadelphia, recycles electronic scrap. The facility serves customers throughout the Mid-Atlantic region, New York/New Jersey and New England.
E-Stewards is a global certification program designed to enable individuals and organizations to identify electronic scrap recyclers, asset recovery companies, processors and others that adhere to the e-Stewards Standard for Responsible Recycling and Reuse of Electronic Equipment. According to BAN, recyclers who have achieved e-Stewards certification pledge to process all electronic scrap in developed countries, do not use municipal solid waste facilities and do not use prison labor operations.
ECOvanta’s facility processes electronic scrap, including computers, monitors, mobile phones, printers and televisions. The company also offers secure destruction services.
In addition to e-Stewards certification, ECOvanta’s Philadelphia plant has received Responsible Recycling Practices for Electronics Recyclers (R2) certification and is ISO 14001:2004 registered.
ELECTRONICS
Canon Virginia Earns R2 Certification
Canon Virginia Inc. (CVI), a wholly owned subsidiary of Canon U.S.A. Inc., has reported that it has achieved certification to the Responsible Recycling Practices for Electronics Recyclers (R2) Standard, making it the first original equipment manufacturer to achieve certification to the standard. The certification is the result of independent audits of its Newport News, Va., facilities, which confirm the operations meet the R2 Standard, a set of best management practices governing the environmental, health, safety and security aspects of the electronics recycling industry.
CVI says that while electronic manufacturers typically employ third-party recyclers, the majority of the recycling at CVI’s facility is done on site. CVI says this practice helps reduce the environmental footprint of its products and is an example of the company’s dedication to maximizing efficiency and environmental practices.
“Achieving R2 certification is a major accomplishment and supports our commitment to the environment,” says Toru Nishizawa, president and CEO of Canon Virginia. “We work very hard to ensure the recycling side of our business complements Canon’s research and development efforts to help minimize the environmental impact of our products.”
MUNICIPAL
San José, Calif., Businesses Embrace Recycling
Businesses in San José, Calif., have boosted their recycling rate from 22 percent to almost 70 percent from July to December 2012. The city credits new collection services for the increase in its recycling rate.
The new waste collection services, begun July 1, 2012, provides a two-container wet/dry sort for businesses. Wet items include organics such as food waste, used napkins, paper plates and landscape trimmings. Dry items include glass, paper, plastics, cardboard and scrap metals. Waste collection also changed to a single-hauler system under franchise with the city. Previously, San José’s 8,000 businesses selected and negotiated their own garbage and recycling services among more than 20 city-approved haulers.
Michael Miller of San José’s Fairmont Hotel says, “The two-container, wet/dry system was quite easy to implement, and we are pleased by how committed and supportive our staff is of this most important initiative. As a result, we are realizing cost savings and proudly increasing the amount we recycle.”
Similarly, Sharon Tolaio, U.S. facilities manager for semiconductor licensing company ARM, says she is pleased with the company’s fuller participation in recycling. “At our office in San José, we recycle paper, cans and plastics, and we collect all of our wet waste for composting. This activity has significantly decreased the amount of trash we send to landfill. We are pleased to be playing our part in this environmentally friendly initiative.”
According to San José Councilman Sam Liccardo, the city is on track to achieve an 80 percent waste diversion rate by 2014. “That’s good news for everyone because this helps extend the life of our landfills and reduces associated taxpayer costs, which can be significant,” he says.
“And, with a single, streamlined collection service,” Liccardo adds, “we have reduced the number of garbage trucks driving through busy business districts. These are among the steps that help move San José towards a sustainable future.”
In its Green Vision, the San José Council has set a goal to divert 100 percent of its waste from landfills and convert waste to energy by 2022.
In 2011, the city of San José conducted a competitive bid process, bringing in Republic Services and Zero Waste Energy Development (ZWED) to collaborate on developing services and infrastructure that would escalate the business community’s rate of recycling and reduce carbon output.
To process the increased volume of material from businesses, Republic expanded its San José material recovery facility to an 80,000-square-foot, multistream processing center capable of sorting 400,000 tons of mixed wet and dry materials every year. The facility stands as the largest recycling facility in the world, according to the city.
“Our facility can recover a high percentage of the incoming waste,” says Republic Bay Area Municipal Relationship Manager Gil Cheso. “And we minimize our carbon output by using compressed natural gas in all of our collection vehicles. We also have plans to use alternative energy sources at our facility. We’re committed to having the most sustainable operations possible.”
ZWED’s facility addresses the waste-to-energy component of San José’s Green Vision. ZWED is currently constructing the first commercial scale dry waste digester facility in North America in San José. It will take the organic stream generated by businesses and convert it to biogas. The facility is anticipated to be operational in early 2014.
Kerrie Romanow, the city’s environmental services director, says she is pleased with the early results of the new service. “The rapid increase in the business community’s recycling rate reflects the success of Republic’s operations and shows that our businesses are effectively participating. San José has long enjoyed one of the highest recycling rates in the nation in the residential sector. Now we can thank our business community for a similar recycling performance.”
AUTOMOTIVE
GO Auto Recycling to Open Jacksonville, Fla., Site
GO Auto Recycling, which was formed by two former employees of the David J. Joseph Co., has announced plans to open its second automotive recycling facility in Jacksonville, Fla. The new facility, to be called GO Pull-It, will target the “do-it-yourself” (DIY) sector, according to the company.
GO Auto Recycling’s first facility, also in Jacksonville, is a wholesale operation that sells parts to companies in the repair and collision businesses.
The company’s customers include professional repair facilities and DIY mechanics.
The new GO Pull-It yard, scheduled to be open by the third quarter of 2013, will use vehicle depollution and processing technology that removes all fluids and hazardous materials from the vehicles prior to recycling, the company says.
Co-owner Jason Finley says the new facility is the first phase of development for a 50-acre land parcel the company purchased in late 2012. The first phase will occupy about 20 acres.
GO Auto Recycling will use an auto crusher to prepare hulks for shipment to an auto shredder once the parts have been harvested.
Michael Mervis with Danville, Ill.-based Mervis Industries, a partner in the operation, says that rather than adding scrap processing equipment at the site, “Our No. 1 job right now is to be successful on the auto recycling side.”
INDUSTRIAL
P&G Achieves Zero Manufacturing Waste at 45 Sites Worldwide
The consumer products company Procter & Gamble (P&G), headquartered in Cincinnati, has announced that 45 of its facilities have achieved zero-waste status, marking a major step toward P&G’s long-term vision of sending no manufacturing and consumer waste to landfills.
During the past five years, P&G says its work to find worth in waste has created more than $1 billion in value for the company. Steve Owens, a member of P&G’s Sustainability and Technical Expert Advisory Panel, says, “P&G is a global leader in sustainability, and the company’s zero-manufacturing-waste initiative is setting a standard for others to follow.”
“We have a vision for the future, where plants are powered by renewable energy, products are made from recycled and renewable materials and resources are conserved, with no waste going to landfill,” says Bob McDonald, P&G president, CEO and chairman. “Changing the way we see waste as a company has brought us one step closer to this goal at 45 sites worldwide, where all of our manufacturing waste is recycled, repurposed or converted into energy.”
P&G says that since announcing its first zero-manufacturing-waste-to-landfill site in Budapest in 2007, the company has shared a long-term environmental vision, pledging to work toward zero consumer and manufacturing waste worldwide. Through its quality assurance, packaging reduction, compaction and recycling efforts, P&G says it now ensures that 99 percent of all materials entering its plants leave as finished product or is recycled, reused or converted into energy.
P&G highlights several steps the company has taken. In Mexico, the company converted paper sludge from a toilet tissue plant into low-cost roof tiles used to build homes in the local community. At a U.S. Pampers site, scrap from the wipe manufacturing process is converted to upholstery filling. And, in the United Kingdom, waste created in the production of Gillette shaving foam is composted and used to grow turf for commercial uses.
METALS
Aircraft Fleet Recycling Association Accredits Two More Recyclers
The Aircraft Fleet Recycling Association (AFRA), a nonprofit organization based in Washington, D.C., has added two companies to its list of accredited aircraft recyclers, bringing the worldwide total to six. The accreditations are based upon the association’s third Best Management Practices Guide dealing with recycling aircraft materials, released April 2012.
The two most recently accredited companies are Aircraft Demolition, based in Burnsville, Minn., and Aircraft End-of-Life Solutions (AELS) based in the Netherlands. They join four other AFRA accredited recyclers, two based in the U.K., and one each in South Africa and the U.S.
“We had thought that our activities were already at the standards in the BMP Guide but we found out that some of our practices and procedures could in fact be improved,” says Derk Jan van Heerdan, general manager of AELS. “The accreditation process not only covered the third-party recycling of fan blades which we carry out for a client, it also covered all the recycling of airframes which we carry out, which is a key part of our business.”
Tim Zemanovic, CEO of Aircraft Demolition, says the accreditations have helped the company improve its business model. “More and more companies are requiring the accreditations in order to do business with them, and this has certainly opened new opportunities for us,” Zemanovic says.
AFRA’s mission is the sustainable management of end-of-life airplanes and engines. AFRA was founded in 2005 by 11 organizations from various sectors of the aircraft industry, including Boeing Commercial Aircraft, Europe Aviation and Rolls Royce. The association now comprises 71 members in 11 countries.
AFRA currently offers two accreditations: one for disassembly of aircraft and another for materials recycling. The organization also has published three Best Management Practice Guides offering detailed direction on the best environmental practices and technological solutions for the disassembling and recycling of aircraft, engines and aircraft materials. About 30 companies worldwide are currently AFRA-accredited disassemblers of aircraft.
ELECTRONICS
Magnum Computer Recycling Relocates
Magnum Computer Recycling, Pennsauken, N.J., has expanded its operations, allowing the company to increase the volume of electronic scrap it can process.
The R2- (Responsible Recycling Practices-) certified and ISO 14001-registered company is a subsidiary of Thanks for Being Green LLC. Previously, Magnum had been operating out of a 10,000-square-foot facility in Westville, N.J. The new facility measures 26,000 square feet and is in Pennsauken.
Magnum’s founder John Martorano Jr. observes, “The move will allow our company to better serve our clients, who will find greater convenience in our new centralized location. It also provides our team of employees with more efficient office space, which features world-class technology. It will also give us a competitive edge in meeting our clients’ rapidly changing business recycling needs.”
The company also has announced it has been chosen as the electronics recycler for the Cape May, N.J., Municipal Utility Authority.
“As a growing company that cares deeply about the environment, we are thrilled that several new counties in New Jersey have decided to work with us for their electronic recycling needs,” says Martorano.
PLASTICS
Hilex Poly Expands through Acquisition
Hilex Poly, a Hartsville, S.C.-based manufacturer and recycler of plastic bags, has acquired Fortune Plastics, Accutech Plastics and Direct Plastics Ltd., part of the North American flexible packaging division of Clondalkin Group, based in Amsterdam. Hilex Poly says the transaction will allow for continued diversification and expanded recycling work.
Stan Bikulege, Hilex chairman and CEO, says, “We are extremely pleased to welcome the employees of these companies to Hilex. They have developed a great customer base and bring a tremendous new range of product offerings to Hilex that we will continue to expand. In addition, the progressive work undertaken by Hilex in the plastic bag and wrap recycling market can now be expanded to an even wider portfolio of flexible packaging products. We also appreciate the strong support of Wind Point Partners; they understand the importance of this North American manufacturing sector.”
PLASTICS
Water Bottle Recycling Rate Nears 39 Percent
The International Bottled Water Association (IBWA), Alexandria, Va., has reported that the newest information from the National Association for PET Container Resources (NAPCOR), Sonoma, Calif., and the Beverage Marketing Corp. (BMC), New York, indicates that close to 39 percent of all plastic water bottles are now being recovered for recycling.
IBWA says the amount of PET (polyethylene terephthalate) plastic used to make bottled water containers continues to decline, with the average weight of a half-liter water bottle dropping by almost 47.8 percent in the past 11 years.
“The bottled water industry utilizes a variety of measures to reduce our environmental footprint,” says Chris Hogan, IBWA vice president of communications. “It turns out that of all the plastics produced in the United States, PET plastic bottled water packaging makes up only 0.92 percent—less than 1 percent. Moreover, plastic bottled water containers make up only one-third of 1 percent of the U.S. waste stream, according to the EPA (Environmental Protection Agency).”
METALS
Wisconsin Scrap Recycler Opens Second Plant
Schulz’s Recycling Inc., which has been in business since 1958, has opened a facility in Wausau, Wis., its second scrap metal location. The company says it will use the Wausau location as a retail business feeder yard for its full-service operation in Merrill, Wis.
Jeff Isroff, who purchased a majority stake in Schulz Recycling two years ago, says the company believes the population in Marathon County, Wis., warrants a new facility that can serve its recycling needs. “We felt that we could benefit from having a retail scrap operation in Wausau,” Isroff says. “We are the only recycler in the city.”
The company officially opened the new facility in late March of 2013. Isroff says Schulz’s Recycling will focus on servicing the retail business in the area. Initially it will not perform any processing at the Wausau location, instead sending material to Merrill to be processed. The company may consider adding equipment later.
The building where Schulz has opened its second location is 23,000 square feet and sits on an 11-acre lot. While the company currently is leasing half the building, Isroff says the company could expand to take over the whole building in the future if business conditions dictate it.
PLASTICS
Plastics Recycler Expands SC Operations
ICE Recycling LLC, a Lake City, S.C.-based recycler of plastics and other materials, has announced plans to expand its operations in South Carolina’s Florence County. The expansion is expected to cost about $1 million and to create 15 new jobs.
“We are excited about expanding our capabilities and aggressively growing our customer base,” says Butch Crawford and Larry Gay Jr., owners of ICE Recycling, in a news release issued by the state of South Carolina. “This new facility will nearly double the amount of overall space under roof for additional processing equipment and growth of operations.”
The investment includes the purchase of an existing building in Lake City in which the company will expand its recycling operations. The company already has started operations at the new 200,000-square-foot facility. The addition of the new space will allow the company to increase its capacity and free up processing space at its original site, also in Lake City.
On its website, ICE Recycling says it specializes in handling “materials from industries [that] would otherwise be sent to landfills. These materials range from scrap fabrics, threads, molded parts, bottles [and] various packaging materials.” A commodity list provided by ICE includes “plastics, polymers, paper, cardboard, aluminum, metal, etc.,” with plastics including “nylon 66, nylon6, PET (polyethylene terephthalate), PP (polypropylene), PE (polyethylene), HIPS (high-impact polystyrene), PS (polystyrene), LDPE (low-density polyethylene), HDPE (high-density polyethylene) [and] postconsumer nylons.”
METALS
Schnitzer to Relocate Headquarters to Downtown Portland
Schnitzer Steel Industries Inc. has announced plans to move its corporate headquarters from the northwest industrial area of Portland, Ore., to the KOIN Center in downtown Portland.
The company says the move will allow it to increase its productivity by providing its employees with a single, unified location rather than the two separate locations the company currently uses. Schnitzer says it expects to make the move by Aug. 1, 2013.
“We are pleased that Schnitzer Steel’s headquarters will remain in Portland,” says Tamara Lundgren, Schnitzer president and CEO. “Our move to downtown Portland reflects our need to consolidate our offices and to provide transportation alternatives to our employees. We appreciate our working relationship with the new administration of the city of Portland and the KOIN Center.”
Schnitzer operates three integrated business segments: metals recycling, auto parts and steel manufacturing.
METALS
Metalico Opens Facility in Greater Pittsburgh
Metalico Inc., Cranford, N.J., has opened its newest scrap metal recycling facility in the Greater Pittsburgh area. The location, in Conway, Pa., is the company’s sixth scrap metal yard in the Pittsburgh area.
The new site formerly housed Skip’s Recycling, a subsidiary of Three Rivers Scrap Metal Inc. Metalico acquired certain accounts and equipment from Three Rivers Scrap to set up the new facility but did not purchase Skip’s itself or assume any of the liabilities of Skip’s or Three Rivers Scrap Metal, the company says.
The newly acquired facility is near Metalico’s auto shredder in Pittsburgh. The company says the Conway site will provide it with the opportunity to strengthen its penetration into the local scrap market and augment its scrap flow in the Pittsburgh market.
The Conway facility will be operated under the company’s Metalico Pittsburgh subsidiary. Other Pennsylvania locations operating under the subsidiary include scrap metal yards in Neville Island, Brownsville, Hadley, Uniontown and Sharon. The subsidiary also operates a feeder yard in Colliers, W.Va.
Three Rivers Scrap Metal will continue to operate its main nonferrous yard, which is located in Pittsburgh.
PLASTICS/PAPER
National Fiber, Trex Partner on Project
National Fiber, a Belchertown, Mass.-based manufacturer of Cel-Pak cellulose insulation, and Trex Co., a Winchester, Va.-based manufacturer of wood-alternative decking and railing, have joined forces to launch a recycling program that will collect National Fiber’s cellulose packaging in the Northeast. The program is already in operation in Belchertown, and the two companies say they hope to expand the program over the next year to cover National Fiber’s entire distribution area.
National Fiber’s Cel-Pak cellulose insulation consists of 85 percent recycled newspapers. The company says it wants to start more comprehensive recycling of its finished product, however.
“Our installers and their customers are very conscious of the environment, energy savings and doing everything they can to reduce waste,” says Chris White, National Fiber director of sales.
“They want to be able to recycle everything they can. By partnering with Trex Co., we’ve found a way to not just recycle our packaging, but to ‘upcycle’ the bags into another high-quality, sustainable building product.”
National Fiber says it has established collection points for Cel-Pak bags throughout the central Massachusetts area and is working with its distributor network throughout the Northeast to expand collections rapidly.
National Fiber has been manufacturing cellulose insulation in Belchertown since 1978. MacGregor Bay Corp. has owned the business since 1997. The company says all of the old newspapers (ONP) it uses to make its Cel-Pak product are hand-sorted to remove magazines and inserts, which would result in a lower quality product because of the glossy, clay coating.
National Fiber says it does not purchase raw material from solid waste firms to further ensure the quality of the material it uses to make its insulation products.
Trex says its entire line of decking products is manufactured from more than 95 percent recycled content, including reclaimed wood and plastic from many common household items, including case overwraps and retail bags.
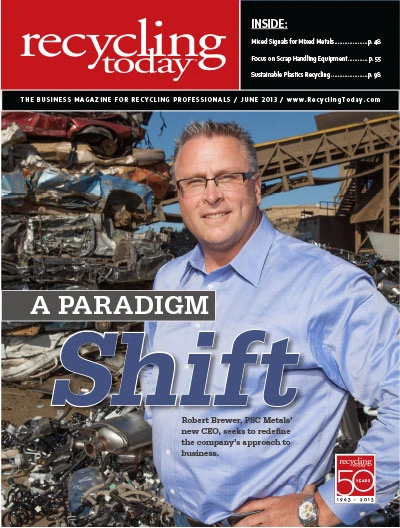
Explore the June 2013 Issue
Check out more from this issue and find your next story to read.
Latest from Recycling Today
- LumiCup offers single-use plastic alternative
- European project yields recycled-content ABS
- ICM to host colocated events in Shanghai
- Astera runs into NIMBY concerns in Colorado
- ReMA opposes European efforts seeking export restrictions for recyclables
- Fresh Perspective: Raj Bagaria
- Saica announces plans for second US site
- Update: Novelis produces first aluminum coil made fully from recycled end-of-life automotive scrap