Downtime is unthinkable in scrap processing operations, particularly those operating automobile shredders.
Wear and tear—normal and exceptional—is what causes downtime.
“Downtime is my biggest concern,” says Adam Weitsman, owner and president of Upstate Shredding, Owego, N.Y. One of the high-volume shredders in upstate New York, the company operates six days per week. On a typical day, 3,000 to 3,500 tons of material are processed through the company’s auto shredder in Owego.
Upstate Shredding stockpiles a variety of wear parts, including hammers, anvils, rotor caps, end disk caps, pin protectors, side liners, grates and reject doors, to keep downtime to a minimum, Weitsman says.
Parts on Hand
While everything within the shredder box will eventually need to be replaced, the degree of wear varies for each part. Shredder operators expect to replace components like bottom grates, anvils/cutter bars, rotor caps, pin protectors and upper anvils/upper breaker bars, too.
“We stock things, so we are not worried about lead times for replacement parts,” Weitsman says.
Upstate Shredding’s auto shredder features a 122-inch mill and uses 1,200-pound hammers. Because a machine of that size is larger than normal, getting replacement parts can take weeks rather than days.
Since Upstate Shredding performs its own maintenance and repairs, price, rather than service, is the primary concern when the company purchases equipment and wear parts. “It is important we keep (repair) materials here,” Weitsman adds.
Upstate can just about rebuild its entire auto shredder from parts it has in inventory. However, in a business where downtime is costly, that is not an unusual approach.
Even operations with more commonly sized auto shredders stock multiple spares. “We stock a complete inventory of every single wear part,” says Gary Chandler, chief operating officer of LNM Holdings LLC, Girard, Ohio. In fact, the company stocks at least two replacements for each wear part. Otherwise, “at the point you install the new one, you have no backup,” he says.
LNM operates an 80x104 shredder from American Pulverizer (APCO), St. Louis. The shredder is powered by two 2,000-horsepower DC motors running in tandem.
“I like to see 800 to 1,000 tons out per day. And I want to get 100,000 total tons before replacing grates and anvils,” Chandler says. He says he expects to be able to process 180,000 to 200,000 tons on the lower liners before replacing them.
LNM aims to produce 4,100 gross tons of shred per set of hammers, Chandler says. That gives the company about 3,200 net tons of shredded ferrous scrap. The rest is auto shredder residue (ASR), aluminum, copper, brass and wire.
The company uses disc, not finger-style, hammers. However, regardless of the hammer style, evening out the flow of material to the shredder helps to spread the wear.
At the other end of the wear parts inventory spectrum is Complete Auto Recycling Service (CARS), Farmington, Mo.
“Because APCO is located so close, I don’t keep much in stock,” says Jason Shipman, president of CARS. For him, same-day or next-day delivery is normal. As a result, CARS keeps only hammers, caps, pins and disc end caps—parts that are more consumable than structural— in stock.
Still, Shipman says he is well-aware of the problems faced by other recyclers who need parts delivered yesterday. “This was a major concern for me,” Shipman says. “I hear of guys with other brand machines waiting weeks for foreign parts.”
He continues, “Our situation is unusual because we are only 75 miles from the manufacturer. We don’t keep much on hand because it is rare that they don’t have something we need.”
A real advantage is that CARS does not tie up much money in its spare parts inventory.
“Normally, we stock one to two sets of consumables. But grates or rotors we buy on a supply-and-demand basis,” says Nick Schlipp, vice president of Indiana Metal Group (IMG), New Carlisle, Ind.
Like LNM, the company runs an 80x104 American Pulverizer shredder. A typical day sees IMG processing 80 to 100 tons per hour.
Schlipp says he finds that more vendors are doing a better job of stocking inventory, which makes it more practical for IMG to order replacement parts just in time.
“Grates are not only about tonnage,” Chandler of LNM says. “If your product gets too big, you lose density and get bigger frag. Then the nonferrous yield drops off. In this business, it’s all about nonferrous yield…if you have a good back end,” he adds.
LNM switches hammers daily. “We like new edges,” Chandler says.
A key to maximizing hammer wear is getting the proper mix of material into the shredder.
For instance, an operator seeing a load of domestic transmissions heading for the shredder may expect the mainly aluminum material to shred like butter. However, it contains hardened steel tool parts, which are hard on hammers.
“We try to avoid a large volume of hardened steel early in the day,” Chandler explains. “We space it out through the day.”
While monitoring feedstock is important, maintenance also plays a big role in keeping the machinery operating.
Keep in Mind
It does not have to be costly to keep things in good shape. Simply being mindful when wear parts are being broken in can help.
“We try to run a little heavier material with new hammers to harden them,” says Shipman. “After half a day, though, it’s back to [processing] everything.”
IMG and LNM follow similar routines.
Schlipp says he finds that the center hammers wear more quickly than those on the side. “We will put a new set in the center to work-harden them and then move them to the outside,” he says. “By moving them to the outside, we get longer life out of them.”
Regular maintenance is another key to extending wear part life, Schlipp says. “We are a bit stricter than most with our maintenance,” he says. Every shift does greasing and visual checking.
“Rather than run a rotor out, we do hard-facing on the rotor,” Schlipp says. That job, like other major maintenance, is done at night.
“Abrasives and dirt will wear out parts faster than anything,” says Weitsman. “Fines and dirt definitely are not good. We try to keep it clean.”
“We weld on our wear parts a little about every day,” Shipman says, noting that they rarely wear evenly. “We weld the low spots,” he explains. But, he says, that job should not be left exclusively to the operator on the floor.
Buying alloy hammers is more expensive but can help. “We are always discussing with our vendors what the best chemistries are,” Chandler says. He relies on the equipment vendors to recommend the best chemistry for his operation’s hammers and the like. “The more tons you push through the shredder, the better,” Chandler says.
Using the proper part chemistry for a yard’s applications also will help extend part life. Shipman says his company learned where to use the different alloys by trial and error.
The Schlipps also work with their vendor to determine an optimum hammer. “The company is working with me on a new hammer with 1 percent more moly (molybdenum),” he says. The idea is to see if it will reduce wear on the hammers.
Extending the useful life of wear parts does not mean babying units. Upstate shows its machinery little mercy. But the company maintains it well, Weitsman says. “We are loading heavy with two grapples,” he adds. “We don’t have time to stop.”
Still, Upstate Shredding does take time to look at different configurations. “We are playing with staggered hammer patterns to see how they work out,” Weitsman says.
Recyclers can try several maintenance practices to reduce wear on parts to prolong their lives. With hammers likely to shorten up a couple of inches in a day’s work, operators have to keep a close eye on the patterns forming. Different hammer patterns will provide different distributions of materials and cause eccentric wear elsewhere. It works the other way around, too. When outside liners are at the end of their useful life, they will push material between the end disc and the end caps.
“We inspect our shredder feed closely to keep the unshreddable stuff out,” Shipman says. “That is priority No. 1 and the most important advice of all,” he says.
Efficiency Gains
Some industry estimates put the average cost of wear parts from $2 to $2.65 per ton of metal shredded. It can be difficult to get a firm fix on that number, because many operations shred a lot of aluminum. Aluminum will produce wear on parts but does not produce any serious tonnage of frag.
IMG tries to keep its auto shredder operating efficiently by using an infeed conveyor and spreading out the material at a steady clip, Schlipp says.
IMG runs more sheet iron than cars on a typical day, Schlipp says. “We do two grapple pulls of sheet iron to one car bundle,” he adds. That helps keep in the inflow mix in a ratio that optimizes the company’s production, he says.
Shipman offers a tongue-in-cheek solution to all of the industry’s shredder wear problems: Take more vacations, he suggests. That, or shred only plastic and wood, he chuckles, and those shredder parts will last forever.
The author is a contributing editor to Recycling Today based in Cleveland. He can be contacted at curt@curtharler.com.
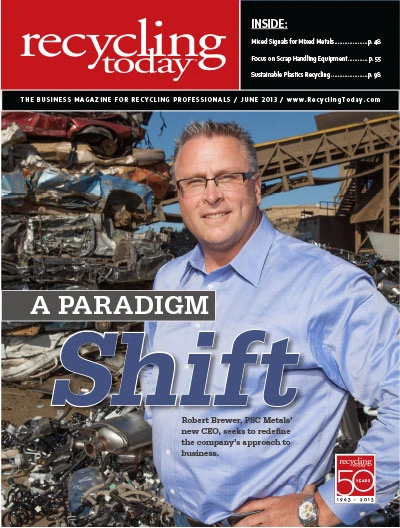
Explore the June 2013 Issue
Check out more from this issue and find your next story to read.
Latest from Recycling Today
- Aqua Metals secures $1.5M loan, reports operational strides
- AF&PA urges veto of NY bill
- Aluminum Association includes recycling among 2025 policy priorities
- AISI applauds waterways spending bill
- Lux Research questions hydrogen’s transportation role
- Sonoco selling thermoformed, flexible packaging business to Toppan for $1.8B
- ReMA offers Superfund informational reports
- Hyster-Yale commits to US production