Recyclers know that in order to keep a scrap yard profitable, it must stay in motion. On any given day, thousands of equipment components—from the hydraulic hoses on a scrap handler to the buttons on the truck scale—must operate correctly and in sync with the pace of the scrap yard.
Scrap handlers, in particular, are valuable tools for those who operate a scrap yard. Recyclers use them to load and unload material from trucks and railcars and to feed shredders and other processing equipment. Scrap handlers also can help sort material or simply move material from one side of the yard to the other.
Proper maintenance and skillful use can help operators to get the most out of these machines, but ultimately they will run their course and will have to be replaced.
Scrap handlers wear out, become outdated or can no longer keep up with the processing equipment being used at the scrap yard. Companies also may need to expand their scrap handler fleets in order to keep up with the growth of their facilities.
Operations Manager Tom Bishop, of Recycling West Virginia, located in Princeton, W. Va., has not been operating his equipment long enough to need to replace a scrap handler because of old age. However, he says, it recently became apparent to him that he would need to upgrade the size of his company’s scrap handler to keep up with a new shredder his team had purchased for the yard.
At times, it will be crucial for a scrap processing company to add to its scrap handler fleet, while other situations might stem from potential growth and opportunity may prompt the addition.
There are not always black and white answers as to when is the right time to add to a scrap handler fleet, though Shaun Stroble of B & D Scrap Metal, located in North Charleston, S.C., says a good sign might be when “you start seeing trucks backing up at the gate.”
However, there are situations recyclers have come across time and again while operating their scrap yards that indicate a new addition is necessary.
Broken down
A broken scrap handler can disrupt the flow of material through a yard and how quickly material can be moved into the yard, unloaded and processed.
As soon as a scrap handler stops working, recyclers know it is important to determine if the machine can be repaired or if it should be replaced with another scrap handler. The longer a scrap yard performs minus a piece of equipment, the more likely it is the yard’s profits will begin to dwindle, sources say.
Bishop says he has experienced this firsthand. One of his scrap handlers had stopped working, and very quickly, he says, the yard’s ability to process material on schedule began to suffer.
He says, “We started looking when we had one piece of equipment down in the yard and realized that with just that one piece of equipment down, it dramatically slowed how we moved stuff across the yard. The next day, I was calling to get quotes.”
Backup plan
If a scrap handler has stopped working because of a busted part, but the machine still has potential, repairs will have to be made to the machine. Repairs mean downtime, which will cost a scrap yard money.
If possible, operations managers like Bishop recommend investing in a backup scrap handler for those days when things go wrong. Having a backup machine on-call can save a scrap yard many hours of downtime and missed opportunities to unload and process material. Bishop recommends looking at it as an investment in the future.
“You have to have the material handlers to keep the machines fed, and you’ve got to have backups there in case you bust a hose,” Bishop says. “Think of it as a just-in- case to keep you going,” he suggests.
KNnow when to fold
Old equipment also can slow down the productivity of a scrap yard. If maintenance employees are devoting too much time—time that could be spent maintaining other equipment—to fix old, troublesome scrap handlers, it may be time to consider adding to the fleet. Stroble says recyclers should know when enough is enough and it is time to retire an old scrap handler.
Stroble says, “I usually upgrade whenever [a scrap handler] is old, and I have already depreciated all of the value that I can from it. Or sometimes it is just too far out dated and is costing me too much money to keep up with it, so I’ll go from there. That is how I try to do to it.” He adds, “ Sometimes it does not work as smoothly as we would like it to.”
It would be wise to start thinking about replacing a scrap handler before the machine has outlived its value, Stroble advises.
Keeping updated records for each machine can help determine when it will be time to replace a scrap handler.
Upgrade all around
Recycle West Virginia’s Bishop says it might be time to replace a scrap handler when a yard has upgraded another piece of equipment.
Once a scrap yard has installed a shredder with more power, for example, it will need a scrap handler that can keep up with it. Chances are, the scrap handler that matched the old shredder will not be suitable for the upgraded piece of equipment.
Bishop says, “When we switched out our shredder to a 4,300- horsepower 98-inch [hammer swing] Harris machine, we saw an instant need to keep it fed. We had a Sennebogen 830 that did not have enough capacity to keep the shredder fed. So, we purchased the 840, which is the 125,000-to-130,000-pound Sennebogen machine.”
Bishop says his team at Recycling West Virginia saw an immediate difference in how they were able to feed the shredder. Overall, he says, the process of moving scrap around the yard went a lot faster with the Sennebogen 840 than with the 830.
Smooth moves
In order to stay in business, a scrap yard needs to be able to properly manage the commercial and peddler traffic that arrives at the gates of the facility.
When Stroble notices traffic at B & D Scrap Metal has been exceeding what the yard is prepared to handle on any given day, he says it might be an indication that it is time to start shopping for an additional handler for the yard’s fleet.
“I’m either adding another piece of equipment to help with the load and unload process or just to keep things moving a little more smoothly,” Stroble says.
Scrap handlers are vital tools in a scrap yard, and recyclers like Stroble and Bishop have learned how difficult it can be to try to operate a facility without an adequate fleet.
Preemptive moves such as those they suggest can be good for business if a company has the capital available to invest in new machinery. After all, the last thing operations managers want to see each day are “trucks backing up from the gate.”
The author is assistant editor of Recycling Today magazine and can be contacted at kstoklosa@gie.net.
Get curated news on YOUR industry.
Enter your email to receive our newsletters.
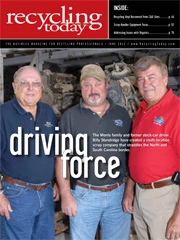
Explore the June 2012 Issue
Check out more from this issue and find your next story to read.
Latest from Recycling Today
- Returpack reports increased DRS activity in Sweden
- Trade groups align against European export restrictions
- Construction, auto sectors show mixed signals
- Politics in Turkey threaten recycled steel outlet
- Toppoint Holdings expands chassis fleet
- Lego creates miniature tire recycling market
- Lux Research webinar examines chemical recycling timetables
- Plastics producer tracks pulse of wire recycling market