![]() |
Visibility and safety are two key factors built into the cabs and controls on the newest models of scrap handling equipment.
Having a good line of sight contributes to work safety; operators must be able to safely handle materials from massive scrap piles, then just as safely and efficiently load those materials into what are oftentimes tall-sided containers.
Additional safety features also come into play, such as comfort, accessing and exiting the vehicle and controlling the boom and stick with precision. These attributes are continually being addressed and improved upon by scrap handler manufacturers, who have devised numerous ways to help increase productivity, optimize controls, reduce accidents and keep operator fatigue at bay.
Visual Considerations
“If you’re a material handler up in the air, you need better visibility for the operator, because that’s just the nature of the business,” observes Andreas Ernst, regional sales and marketing manager for Sennebogen LLC, based in Stanley, N.C.
Ernst says Sennebogen has attacked the issue of visibility by using “as much glass in the cab as possible.” And in recent years the company has worked to remove clutter in front of the operator by switching to joystick steering on its 835 models and larger.
“The visibility in front is far better than having a steering wheel in front blocking your view,” Ernst says. He adds that joystick steering is more comfortable and requires less physical effort.
Another related Sennebogen change has been the standard inclusion of two cameras on its machines: one facing the rear and another pointed to the right side of the machine. He says the right-side camera improves visibility because it allows the operator to see beyond the boom, which is always to the right.
Liebherr Construction Equipment also addressed the topic of visibility with its new wheeled material handlers introduced to the market in April: the LH 60M and the LH 80M. The handlers replace the company’s A944 and A954 material handlers and offer a number of cab and control changes designed to offer safety, visibility and comfort, explains Paul Hill, senior product manager, industrial handlers, for Liebherr Construction Equipment Co., based in Newport News, Va.
The new LH series handlers feature a longer cabin, at 70.8 inches, and a windshield that’s 2.4 inches longer. As with all Liebherr scrap material handlers, the new LH handlers come standard with bulletproof glass on the front and roof windows.
“Liebherr takes the safety of the machines’ operators very seriously, and that’s why for industrial handling machines we specify the bulletproof glass.”
When it comes to visibility improvements, Hill says Liebherr also has worked to engineer better visibility with less obstruction, while maintaining FOPS/ROPS safety standards (falling object protection structures/rollover protection structures) with its LH units.
Control Issues
Terex Fuchs has redesigned its cabins and control panels in recent years with a focus on operator comfort and productivity. The changes were introduced in 2010 on its second generation D-series machines as well as on the company’s newest E-series line this year.
On these models the company replaced a throttle lever responsible for engine speed control with a multifunction knob that can control a host of handler functions, including engine speed.
“It’s an ergonomic device that not only functions as a throttle but also as a navigation tool to go through the menus on the color display,” explains Steve Brezinski, product manager, material handlers, for Terex Construction Americas, Southaven, Miss. Brezinski says the button can be turned clockwise or counterclockwise to page through different menus and also features its own joystick and selector button, so it can be used much like a computer mouse.
The company also redesigned and repositioned its control system in 2010 when it added an integrated control panel console. Besides adding functionality to the control panel, Terex says it also replaced toggle switches with simpler push buttons.
“In general our concept has been to centralize the controls in front of the operator so they’re not spread all over the cabin,” Brezinski explains. He notes that the more frequently used functions, such as cabin up and down and the dipper stick limiter, are now push buttons on the console itself, while the less frequently used functions are located in the various navigation menus displayed on the screen. “So there’s a lot more functionality in the display monitor as we’ve progressed over time,” Brezinski adds.
“Going to a little bit larger display with the new Tier 4 interim machines allows you to present more material on the screen,” Brezinski says. The larger display also provides higher contrast and anti-glare features, he says, and is easier to see in bright sunlight. And he points out that having the larger screen is particularly useful for Tier 4 interim machines, which also have additional emissions components that the operator must monitor.
“If the controls are more easily accessible, if the information is clear and the operator can see the working environment, that all enhances production and the overall efficiency of the operation of the machine,” Brezinski says.
Liebherr also implemented control upgrades in its new LH machines. Those models have a proportional control button on the top of the joystick that allows for joystick-controlled steering, available as an option. The switch allows the machine to be steered hydraulically through the joystick, Hill explains. Hill also notes that the operator’s seat on the LH models now features integrated joysticks that move right along with the seat for improved ease of use.
Meanwhile Iron Ax, a builder of Doosan scrap handling machines, offers operators two options when it comes to controlling the machine. Charlie Hall, president of the Wadley, Ga.-based company, says one recent change has been giving operators of its Doosan scrap handlers a choice between two different control patterns to suit their preference. “They can flip a selector and have the John Deere-style, backhoe pattern, or they can they can have the excavator control pattern in the same machine,” Hall says.
While the double operator pattern was an option in prior years, it became a standard offering in just the last few years.
Peter Kangas, an engineer with Northshore Manufacturing, Two Harbors, Minn., observes that these days, handlers are more frequently operated with joysticks. The company builds the Builtrite brand of handlers and has added improvements to joysticks in recent years. “The hand joystick handles are provided with better ergonomic feel for the hand and each is tilted to provide better ergonomic feel for the wrist and arm,” Kangas says.
More customization in terms of control feel and speed variations is another trend Kangas has witnessed and that Northshore has worked to offer. “Customers appreciate the willingness to respond to their requests regarding control variations to suit their need,” he says, adding that the company is increasingly considering the use of electronic controls, rather than hydraulic, as they can make changes in control configuration, feel and function speeds much easier to tune to individual users of the machine.
Matt Keeley, product manager for Peoria, Ill.-based Caterpillar’s Industrial and Waste Group, says Exodus branded scrap handlers, which are part of the recent Exodus-Caterpillar alliance, feature the company’s newest control and cab designs. Keeley says the Exodus MX447 and MX457 feature joystick controls for all implement and travel functions. “Operators can fine-tune their control of the machine to adapt for desired speed and implement speed match,” Keeley says. In addition, seat-mounted joysticks are designed to reduce fatigue and increase productivity.
Access & Comfort
Accessing and exiting the cab, which is often several feet off the ground, has been another focus area among manufacturers.
Exodus addressed this situation with the introduction of a ground-access cab, available on its MX447 and MX457 handlers. “Access and egress are very important, as operators climb in and out of material handling machines several times every day,” Keeley explains.
Sennebogen also debuted an access feature in recent years starting with the company’s D-series machines and continued on new models. The Sennebogen MaXCab is a sliding entry door with a handrail and catwalk. Having the sliding door, Ernst says, has allowed the company to add a small catwalk on the machine where a second individual can stand for training purposes. The operator also can exit the cab without lowering it to deck level, the company says. “We are the only ones doing that in the industry,” he says.
Meanwhile Hall says Iron Ax’s Doosan machines also now feature self-elevating cabs, “so you don’t have to climb the ladder to get in the cab,” he says. “We are the only company that makes the Doosan machine with the self-elevating cabs that I know about,” he adds.
Operator comfort is another area that has not been overlooked. Liebherr’s Hill says the company has upgraded the air conditioning system in its LH machines, offering increased airflow throughout the cab. “But at the same time we’ve managed to make the cab quieter,” he adds.
Ernst says Sennebogen always has focused on operator comfort, and cabins come standard with climate control and an air-suspended operator seat with lumbar support, heater and head rests. “It’s really a top-quality seat the operator is in for his 10- or 12-hour shift,” he says.
The author is managing editor of Recycling Today Global Edition and can be contacted at lmckenna@gie.net.
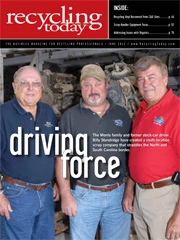
Explore the June 2012 Issue
Check out more from this issue and find your next story to read.
Latest from Recycling Today
- Two factors raise ferrous export questions in April
- Analyst: Scrap imbalance lost amid copper’s critical status
- AF&PA report shows decrease in packaging paper shipments
- GreenMantra names new CEO
- Agilyx says Styrenyx technology reduces carbon footprint in styrene production
- SABIC’s Trucircle PE used for greenhouse roofing
- Hydro to add wire rod casthouse in Norway
- Hindalco to invest in copper, aluminum business in India