![]() |
When Kenny Burgess opened Midwest Scrap Management in St. Joseph, Mo., nearly 40 years ago, even he could not envision the company’s tremendous growth and expansion. What began as a single-man operation in a pickup truck in 1973 has turned into one of the largest scrap operations in the Midwest, employing more than 100 people.
“It’s been a lot of hard work and long hours,” says Burgess, general manager of Midwest Scrap Management.
This strong work ethic and customer service commitment has expanded the operation’s reach to a 200-mile radius of its Missouri locations, serving customers in four states. Processing nearly 1,500 tons of ferrous and 30 tons of nonferrous material per day, the company has notable accounts such as Harley Davidson Manufacturing, UPS and FedEx.
A pivotal event in the company’s growth can be attributed to its expansion into the Kansas City, Mo., market.
“Kenny had plans to bring a high-capacity shredder to this market,” explains Jay Young, scrap and recycling sales manager for Roadbuilders Machinery and Supply Co. Inc., a Terex Fuchs equipment dealer headquartered in Kansas City, Kan. “Even though his competition said it couldn’t be done, Kenny had his sights on 59 acres of land ideally suited for a scrap operation.”
The Right Solution
Before expanding to Kansas City, Midwest Scrap honed its scrap processing and handling practices into a model of efficiency. The St. Joseph branch experimented with different equipment solutions that would allow the yard to capitalize on the opportunities in the Kansas City market.
Initially, the St. Joseph location began shredding No. 2 material with a small shredder. However, the shredder did not fit the company’s needs, so Midwest Scrap Management got rid of it.
After a short hiatus, Midwest Scrap invested in a 1,200-horsepower shredder in 2002, which proved to be the right fit to handle the inflow of vehicles at the St. Joseph yard, improving cash flow.
“The income generated by the shredder gave Kenny the necessary capital to add the Kansas City location,” says Midwest Scrap Management Operations Manager Jim Summers.
The St. Joseph location also ran a series of trials to find the right scrap handler to keep up with its production needs. Unpaved, the yard made the track-driven Terex Fuchs RHL340 a good solution.
“The RHL340 was the first hydraulic crane the company bought,” Burgess says.
Midwest Scrap’s RHL340 gave the operators a machine with a 41-foot reach and a maximum lift capacity in excess of 31,000 pounds.
Even though the tracked handler delivered solid performance, Midwest Scrap wanted to test a variety of handlers from different manufacturers, and Burgess admits he tried some because he could get a good deal. “Zero-percent financing was attractive for one make,” he says, “but we were not impressed with the machine’s performance.”
In all, Midwest Scrap experimented with three different handler makes and various models at its St. Joseph headquarters to compare performance against the Terex Fuchs handlers and to prepare for expansion into the Kansas City market.
Burgess saw potential in the industrial property in Kansas City that other operations in the region had overlooked.
“He targeted the old Sheffield Steel/GSTC site,” Young says. “The property sat dormant for years before businesses started renting portions of the land. Kenny purchased 59 acres for the branch location.”
With convenient rail and highway access, there was potential for this location to be a high-volume yard. Midwest Scrap Management installed a 350-ton-per-hour, 7,000-horsepower shredder to process the flood of materials for its No. 2 shred. In addition to cars, “the shredder allows us to run up to 1.5-inch thick skeleton plate and rebar though it,” says Summers. This heavy steel would have otherwise required torch cutting.
Today, the vital Kansas City yard accepts and processes ferrous and nonferrous material. The branch supplies No. 1 and No. 2 shred, heavy melt, bundles, clips, turnings and nonferrous metals to its customers.
Since 2006, Midwest Scrap has run more than 1.3 million tons of scrap through its Kansas City shredder. “In 2011, we processed and shipped on average 35,000 tons of scrap material per month, of which 25,000 tons was No. 2 shred,” Summers says.
The company’s final ferrous products are shipped throughout the U.S., and its nonferrous metals go to domestic and international customers.
Longer Reach, More Efficient
Midwest Scrap needed to select the right size and type of material handler to take advantage of the shredder’s capacity and the high volume of material flowing into and out of the Kansas City yard. Engine and generator issues with some of the tested competitive handlers signaled an end to experimentation and standardization on one particular brand.
“We started with Terex Fuchs,” Burgess says, “and we are back with Terex Fuchs. That says a lot about the handler.”
One difference between the St. Joseph and Kansas City yards is that Midwest Scrap invested more than $2 million in paving the Kansas City yard with concrete.
“Initially, we made the investments for environmental reasons,” says Summers. “However, we have found that the customers like driving on the paved surface better, and it has increased traffic into our yard.”
Paving also made the prospect of purchasing Terex Fuchs material handlers on wheels attractive. Crews could more easily keep the concrete free of scrap debris, reducing the chance for tire damage. “It also makes getting from one part of the yard to another a lot easier than with a track machine,” Summers adds.
Initially, Roadbuilders consulted with Midwest Scrap on its material handler needs and supplied Terex Fuchs MHL360 D material handlers to feed the shredder, load railcars and offload and sort material from trucks and peddler traffic. “The MHL360s were equivalent in size to the other brands Midwest Scrap was using at the time,” Young comments.
The 249-horsepower MHL360 D material handlers are equipped with a boom-and-stick combination that provides a 59-foot reach—18 feet longer than the Midwest Scrap’s original RHL340 handlers. This improves loading, sorting and stacking efficiency. The machine’s double-row-slewing-ring design offers reliable performance, even when lifting more than 10,000 pounds at a 50-foot reach with its 1-cubic-yard grapple.
The handlers worked well for the Kansas City location. Yet, Summers noticed some areas where efficiency could be further improved. “We averaged 1,200 tons per day through the shredder, but we noticed that two-thirds of this production would take place in the first half of the day,” he says.
Supporting equipment that was stockpiling material to be shredded had a hard time keeping pace with the combination of a high-capacity shedder and the productive MHL360 D. By the afternoon, the feed piles retreated further away from the shredder, so operators had to move the handlers to get the feed material.
Railcar loading efficiency, Summers says, also could be improved at the yard. “The operator loaded two railcars at a time, but it would take until about 5:30 p.m. for him to finish the daily railcar quota,” he adds.
With the goal of tweaking production efficiency, Burgess met with Young to discuss options. All signs pointed to the Kansas City yard requiring a material handler with a longer reach.
Young recommended moving up to the Terex Fuchs MHL380 D. “The MHL380 gives operators 17 percent more reach and offers a 1.8-cubic-yard grapple, so this would help them boost productivity at the shredder and improve loading efficiency,” Young says.
The largest material handler in the Terex Fuchs line, the 366-horsepower MHL380 D delivers a maximum 69-foot reach, allowing operators to pick, stack and sort material from a greater distance without moving. It also features the double-row-slewing-ring design and nearly doubles the 50-foot reach lift capacity. “Additionally, it offers a maximum 20-foot operator eye-level and hydraulic forward extension of the cabin up to 7 feet to assist with job site visibility, loading and unloading material,” says Steve Brezinski, Terex Fuchs product manager.
The additional 10 feet of reach improved loading efficiency at the shredder, the company says. Average shredder throughput increased by 25 percent to 1,500 tons per day. “The extra reach was a huge benefit to increase production,” Summers says. “We knew it would help, but we didn’t realize it would help that much,” he adds.
The new material handler boosted railcar loading efficiency as well. The Terex Fuchs handler’s 69-foot reach allows the operator to load three railcars at a time from a single position, compared with two cars using the MHL360 D. Summers reports Midwest Scrap now moves three railcars into the loading zone at one time. Operators process three additional cars each day—loading 20-plus cars per day—while finishing about 1.5 hours earlier.
In addition to the three MHL360 D handlers working at the St. Joseph yard, Midwest Scrap operates five MHL360 D and now three MHL380 D handlers in Kansas City. Two of the MHL380s are dedicated to feeding the shredder, and one loads railcars and offloads industrial trucks. The MHL360s assist the larger handlers, stacking material for the shredder, offloading incoming material, sorting and separating material and prepping material for shipping.
Future Expansion
Successes at the St. Joseph and Kansas City locations have resulted in another expansion for Midwest Scrap. In the spring of 2012, the company broke ground on its new Park City (Wichita), Kan., yard, broadening its reach in Kansas to the south and west.
Similar to the Kansas City yard, Park City will have a high-capacity shredder, highway access and rail access. The shredder will be slightly smaller—6,000 horsepower with a production capacity of up to 200 tons per hour. “The local market consists of more car bodies and less heavy steel, so we did not require a larger shredder,” Summers says.
When the operation opens in 2013, Burgess knows the type and size of Terex Fuchs material handlers that will be used. The lessons learned and production increases achieved in Kansas City has Midwest Scrap sold on the MHL380 D. “We’ve experienced the benefits of the larger machines,” Summers concludes. “We will go with the MHL380s in the new yard and equip them with larger grapples for feeding the shredder and smaller ones for offloading trucks and peddler traffic,” he says.
The author submitted this feature on behalf of Terex Fuchs and Performance Marketing. More information is available at www.terex.com.
Get curated news on YOUR industry.
Enter your email to receive our newsletters.
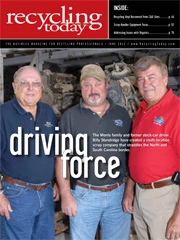
Explore the June 2012 Issue
Check out more from this issue and find your next story to read.
Latest from Recycling Today
- Toyota opens ‘circular factory’ in UK
- Agilyx works with former Plastic Energy CEO on sourcing venture
- Two factors raise ferrous export questions in April
- Analyst: Scrap imbalance lost amid copper’s critical status
- AF&PA report shows decrease in packaging paper shipments
- GreenMantra names new CEO
- Agilyx says Styrenyx technology reduces carbon footprint in styrene production
- SABIC’s Trucircle PE used for greenhouse roofing