> PLASTICS
Plastics Recycling Plant Opens in Oregon
Pacific PET Recycling LLC, a newly formed company that is a joint venture among the owners of Denton Plastics, RGN Investments and the Oregon Beverage Recycling Cooperative (OBRC), has officially opened its processing plant in St. Helens, Ore.
When fully operational, the $10 million, 50,000-square-foot plant will be able to wash and grind from 25 to 30 million pounds of PET plastics per year.
Dennis Denton, president of Denton Plastics and a principal of Pacific PET Recycling, says the company will consume PET bottles collected through the OBRC program as well as from independent recycling companies in the Northwestern U.S. Once the material is washed and ground, the plastics will be sold to a number of domestic consumers that will convert the material into a wide range of applications.
To help with the project, Pacific PET Recycling LLC received loan guarantees from the USDA (U.S. Department of Agriculture) as well as incentives from state and local government agencies.
The company already has sold 25 truckloads of the processed PET on the spot market and is in negotiations with major consumers to take in more of the material, Denton says.
> PAPER
Futuremark’s Parent Company to Acquire Manistique Papers
The Watermill Group, a private investment firm headquartered in Lexington, Mass., has received court approval to acquire Manistique Papers, the only company in North America producing high-value uncoated printing and writing paper exclusively from 100-percent-recycled fiber. The purchase agreement was finalized following an auction and confidential bidding process.
According to a news release issued by Watermill, Manistique will enhance its portfolio of environmental paper manufacturers, which includes the recycled coated paper producer FutureMark Paper Co. With the acquisition, Watermill brings together two paper companies that produce 100-percent-recycled paper in both the coated and uncoated markets. Combined, the two mills produce nearly 300,000 tons of recycled paper per year.
“Over the past three to five years, sustainability has moved from a corporate nice-to-have to a corporate must-have, especially among Fortune 500s,” says Steven Karol, Watermill founder and managing partner. “This development is reflected in the success of our FutureMark investment, which has leveraged its unrivaled environmental position to significantly outperform competitors in a declining sector.” He adds, “We’ll use the strategies proven at FutureMark to revitalize and grow Manistique, building a stronger employer for the local community, driving new investor value by leading the high-value market for sustainable paper and creating a wider assortment of environmental paper products for our Fortune 500 customers.”
Manistique Papers has a 72-acre manufacturing site in Manistique, Mich., which can produce up to 500 tons of recycled pulp per day.
> MUNICIPAL
ReCommunity Opens New MRF in New York State
ReCommunity, headquartered in Charlotte, N.C., has opened its Beacon, N.Y., material recovery facility (MRF). The company invested roughly $7.5 million in the 52,000-square-foot MRF, which will recover plastics, old newspapers, most grades of paper, old corrugated containers, tin and aluminum cans and glass containers from single-stream residential recyclables.
ReCommunity also has partnered with Hudson Valley Pattern for Progress Fellows Program to launch an education program designed to increase recycling in the area. Members of Pattern for Progress are developing a pilot program at the Beacon City School District to educate students about recycling.
The Beacon MRF will service municipalities throughout the Northeast, including the greater Hudson Valley counties of Dutchess, Ulster, Sullivan, Orange and Putnam in New York and parts of southwest Connecticut.
“ReCommunity is committed to what we call ‘leading the recovery revolution,’ and we are happy to bring our services, along with new green jobs, to the Greater Hudson Valley,” says Jim Bohlig, ReCommunity CEO.
Jonathan Drapkin, president and CEO of Hudson Valley Pattern for Progress, says, “Pattern for Progress believes in regional solutions to issues such as recycling, which clearly requires strategies that cross municipal borders. We applaud ReCommunity.”
> PLASTICS
InterGroup International Joins the Sustainable Packaging Coalition
InterGroup International Ltd., Euclid, Ohio, has been accepted as a member of the Sustainable Packaging Coalition (SPC), a project of GreenBlue, Charlottesville, Va.
![]() |
According to the SPC’s website, the coalition is “an industry working group dedicated to a more robust environmental vision for packaging. Through strong member support, an informed and science-based approach, visionary supply chain collaborations and continuous outreach, we endeavor to build packaging systems that encourage economic prosperity and a sustainable flow of materials.”
With a concentration in recycling packaging, InterGroup International says it is looking forward to making an impact on the sustainability of consumer packaging.
As part of the commitment, InterGroup, in partnership with CEI (Coating Excellence International), participated in the SPC’s first Packaging Stewardship Video Challenge. More than 100 SPC members were invited to submit videos highlighting their progress, innovation and commitment to sustainable packaging.
The theme of 2012’s challenge was “How is your company making the SPC definition of sustainable packaging come to life?”
From the 13 videos that premiered at the SPC spring meeting, the organization’s staff selected its three favorite videos, and the meeting attendees voted for their top video choices in three categories.
The SPC staff selected videos from CEI/InterGroup International, Schwak/Athem and REI, while SPC members selected The Coca Cola Co. as the winner in the Best Innovation category, Starbucks in the Best Implementation of the SPC Definition category and CEI/InterGroup in the Best Video category.
In related news, InterGroup International CEO Neil Gloger also spoke about recycling and brand security for flexible packaging scrap at the CPP (Converting and Package Printing) Expo in Cleveland. Prior to the conference, attendees took part in a tour of InterGroup’s Euclid facility, which includes multi-layer film reclaim, sorting and repelletizing for various grades of plastic scrap.
The company recently opened a plastics recycling facility in southwestern Missouri. This facility, which opened in late 2011, recycles around 2 million pounds of plastic scrap per month.
InterGroup also had announced plans to open a new distribution facility in Cleveland this spring. The 165,000-square-foot facility will presort and consolidate scrap collected from Toronto, Detroit, Baltimore and Louisville, Ky. It is designed to handle more than 10 million pounds per month. The distribution facility is designed to facilitate the addition of three repelletizing lines at InterGroup’s Euclid plant, according to the company.
InterGroup International also says it plans to open a plant in the Atlanta area in the third quarter of 2012.
The company, which buys, reprocesses and sells post-industrial scrap plastics, says it helps its vendors work toward zero-waste and sustainable manufacturing goals by implementing environmentally efficient recycling programs through a one-stop-shop approach. Other goals include the production of high-volume, ecologically friendly feedstreams that lower customers’ raw material costs.
> MUNICIPAL
Rhode Island Pilots Recycling Program
The Rhode Island Resource Recovery Corp. (RIRRC), Johnston, R.I., has begun to pilot the state’s new recycling program in the cities of Burrillville and North Smithfield. The pilot program will allow RIRRC to test new sorting machinery and gather feedback from recyclers before the program rolls out statewide in mid-June.
RIRRC, the operator of the state’s central landfill and material recovery facility (MRF), is responsible for sorting and processing the state’s recyclables. The profits from the sale of recyclables are shared with the cities and towns each year.
“We couldn’t be more excited for the arrival of our new recycling program,” says Sarah Kite, director of recycling services for RIRRC. “In order to transfer to the new recycling process, significant modifications were made to the MRF.” She adds, “With help from the residents of Burrillville and North Smithfield, we can be sure that the facility is operating efficiently and correctly processing recyclables before the statewide program launch in June.”
RIRRC mailed Burrillville and North Smithfield residents a brochure that communicates the specifics of the new program. This brochure details the new items that can be recycled, specific recycling “do’s and don’ts” and the announcement that residents can mix all their recyclables together in their existing city- or town-approved bin, cart or box.
Burrillville and North Smithfield residents also received a postcard encouraging them to complete a short, online survey about the new recycling process. A printed version of the survey also was available, RIRRC says.
RIRRC officials will use the results of the survey feedback to help shape how the program is communicated to the rest of the state.
> PAPER
Market2Mill to Include SOP, Mixed Paper Prices
Market2Mill, the recovered fiber price report and benchmark from Forest2Market, Charlotte, N.C., will begin reporting sorted office paper (SOP) prices and market trends in June 2012.
Forest2Market recently announced that it would be adding mixed paper pricing and trends to the Market2Mill report in June. According to Forest2Market, Market2Mill will next add export prices.
According to attorney James R. McGibbon, who rendered the anti-trust opinion that paves the way for the addition, the inclusion of SOP prices in Market2Mill will have significant effects on the industry.
“There is very little transparency in sorted office paper pricing at present due to the lack of market reporting, and it seems quite possible that there are gross and unjustified discrepancies in prices of what are essentially commodity products,” he says. “Improved pricing data to both sides in a competitive market should lead to more accurate pricing based on economic factors of supply and demand, thus improving market efficiency.”
Launched in April 2011, Market2Mill covered DLK (double-lined kraft) and OCC (old corrugated containers). Forest2Market says it quickly accumulated enough data to split OCC prices into two categories: those traded under contract and those traded on the open market.
According to Barbara Hudson, manager of Forest2Market’s recovered fiber practice, this addition further establishes Market2Mill as the industry standard.
“Our recovered fiber business has experienced strong and consistent growth,” she says. “We’ve doubled the number of products we report in just one year and increased the segments of the recovered fiber industry that we serve.”
Hudson continues, “With the inclusion of SOP prices in our price report and benchmarks, document destruction companies will—for the first time—have the tools they need to compare their performance to, and improve their performance against, the market.”
Regarding the addition of export pricing to Market2Mill’s reports, Hudson says, “Export markets have been drawing high volumes of fiber away from the U.S. domestic supply. The strength of demand coming out of Asia in particular has created a price differential between export and domestic markets. By adding export prices to our reports, Market2Mill subscribers will have a global picture of the market.”
Forest2Market says it expects to add export pricing to its Market2Mill reports in the second half of June 2012.
Market2Mill reports volume-weighted average prices derived from actual transactions submitted by subscribers, who use this to assess their performance against the market and to develop forward-looking pricing strategies.
Forest2Market provides market pricing data and supply chain expertise to customers in the forest, wood products, pulp and paper, recovered fiber, lumber and bioenergy industries, with the goal of providing business solutions that support decision making and planning. The company was founded in 2000 by Pete Stewart, who remains president and CEO.
Forest2Market has posted a new video featuring the story of the company’s inception and growth, which can be accessed through Forest2Market’s website at www.forest2market.com.
> METALS
Upstate Continues to Grow
Owego, N.Y.-based scrap metal recycling company Upstate Shredding LLC-Ben Weitsman & Son Inc. has announced plans to open a new scrap metal facility in Port Albany, N.Y. The company says it expects the yard to be operational by May 2013.
The full-service scrap metal facility, which will operate 12 hours per day, seven days per week, will handle ferrous and nonferrous metals. The 40-acre facility is expected to cost between $25 million to $30 million.
The site will include a Sennebogen 880 EQ pedestal electric crane with a 10-yard grapple to load Handymax vessels for export shipments. The facility also will be equipped with mobile shears, mobile cranes and loaders, as well as three 90-foot scales, a nonferrous warehouse with an Harris HRB baler and roll-off trucks.
The site is approximately two hours from Upstate Shredding’s 10,000-horsepower auto shredder in Owego, N.Y.
The new facility provides Upstate Shredding direct access to the Upper Hudson River. A spokesman for Upstate Shredding says the location is ideal because the company needed access to international markets as well as a means to purchase scrap from other scrap yards in the five-state region.
While the Port Albany location will provide Upstate Shredding LLC-Ben Weitsman & Son Inc. with direct access to offshore shipments, the company also will have rail access.
> ELECTRONICS
HP, Staples Partner on Recycling Initiative
Technology company HP, based in Palo Alto, and office products company Staples Inc., based in Framingham, Mass., have partnered to provide free electronics recycling for all brands of office electronics at Staples stores nationwide.
Consumers and small businesses are invited to recycle their electronics at the 1,500 Staples locations in the lower 48 states, excluding Staples Copy and Print Shops, regardless of where the devices were purchased.
Additionally HP says it is offering dropoff and free shipping and recycling for HP consumer products at FedEx Office locations (a voucher is required).
Electronic Recyclers International (ERI), based in Fresno, Calif., will recycle the devices collected at Staples stores. Mark Buckley, Staples vice president of environmental affairs, says ERI’s locations are well-suited to Staples’ logistics network.
“We are confident that we have chosen a responsible and credible partner in this endeavor,” Buckley adds.
Chris Librie, director of environmental affairs for HP, says his company and Staples share commitments to the environment and sustainability.
He adds that Staples network of more than 1,500 stores is a great way to offer close, free recycling services to consumers and small businesses.
“HP is a leader in the technology industry in product reuse and recycling,” says Gabi Zedlmayer, HP vice president of sustainability and social innovation. “We recently celebrated reaching our goal of recycling 2 billion pounds of electronic products and supplies since 1987, and our collaboration with Staples will build upon this achievement and focus on increasing electronics recycling in all states.”
The Staples technology recycling program, which is funded by HP, accepts all brands of the following electronics for free:
- Desktop computers, laptops, netbooks, tablet PCs, external hard drives and small servers;
- All computer monitors;
- Printers, desktop copiers, faxes and all-in-one devices;
- Mice, keyboards, modems/routers networking and PC speakers;
- Shredders, streaming devices, phones and universal power supplies (UPS battery backup); and
- Mobile phones, GPS devices, MP3 players, digital camcorders and digital cameras.
Customers can drop off up to six electronic devices per day for recycling at the service desk of their local Staples stores, Buckley says. Staples will use its logistics networks to collect the devices and consolidate them at its distribution centers. ERI, a certified e-Stewards and Responsible Recycling Practices (R2) recycler, will arrange to have the materials transported to one of its processing centers for recycling.
HP says it has more than 3,700 recycling dropoff locations throughout the United States. Additional information is available at HP’s and Staples’ websites, www.hp.com/us/go/recycling or www.staples.com/recycle, respectively.
> PLASTICS
SirNaik LLC to Open Green Research Center
Plastics recycling company SirNaik LLC, Columbia, Md., has announced that it has invested $10 million in the 200,000-square-foot Green Research Center. The center, which is dedicated to finding solutions for post-consumer plastics, is scheduled to open in the fall of 2012 in West Virginia.
SirNaik LLC, formerly the Naik Group of Industries, was founded 25 years ago. The group’s first subsidiary was post-industrial plastics recycler Intercontinental Export-Import. SirNaik operates facilities in the United States, Canada, India and Europe.
“Ample opportunity exists to engage a new stream of feedstock,” SirNaik states in a press release, “but a tremendous amount of research is required because post-consumer feedstock has a high degree of variability. By utilizing multiple unit processes, the Green Research Center will develop the best continuous process for recycling post-consumer material.”
According to SirNaik, the Green Research Center will house every recycling process imaginable for plastics under a single roof. Its services will be available to anyone invested or interested in closed-loop recycling and product stewardship.
The Green Research Center will process scrap plastics, certify the material and return it to the manufacturer for reuse. “Through closed-loop recycling, manufacturers will receive a better value for their own scrap,” according to the company.
“With product stewardship, the Green Research Center will aid companies in better understanding, controlling and communicating a product’s environmental, health and safety related effects through its life cycle, from production to final disposal or reuse,” SirNaik says.
> LEGISLATION/METALS
Georgia Governor Signs Anti-Theft Bill
Georgia has become the most recent state to pass legislation that attempts to deal with metal theft with the signing of a bill that tightens restrictions on the scrap metal trade. The law will go into effect July 1, 2012.
Signed into law by Gov. Nathan Deal April 16, 2012, House Bill 872 changes the way scrap metal recyclers conduct business. Deal says the goal of the new law is to combat the rising tide of criminal activity by enforcing strict regulations on businesses that purchase ferrous and nonferrous scrap metal. The bill was sponsored by Rep. Jason Shaw.
The law addresses transactions involving ferrous and nonferrous metals, with the sale of used beverage cans being the exemption. The bill also does not affect business-to-business transactions, only retail trade.
Key points of the law include:
- Scrap metal recyclers can purchase coil and certain copper wire from certain persons.
- Scrap metal recyclers can purchase burial objects from certain persons.
- Certain provisions relating to inspections by law enforcement officers have been changed.
- Payment is required by check, voucher or wire transfer; cash payments are banned.
- Scrap dealers are required to register with every city in which they conduct business.
Chip Koplin, governmental and public affairs manager for Schnitzer’s Southeast Region, says the ban on cash payments is the one issue that is of most concern for scrap metal recyclers in the state. He says that for a scrap metal recycler with several hundred transactions per day, the change to a cashless system could create significant challenges.
Certain provisions relating to title transfer procedures with regard to scrapped vehicles also have been revised.
> MUNICIPAL/PAPER
Denver Recycling Program Adds Cartons
Denver Mayor Michael Hancock, in partnership with Waste Management of Colorado, the Carton Council and WhiteWave Foods, has announced that food and beverage cartons are now being collected for recycling through the Denver Public Works’ residential recycling program, Denver Recycles.
Denver households can now place all empty food and beverage cartons in their Denver Recycles cart. Products commonly packaged in cartons include milk, juice, cream, egg whites and egg substitutes, soup and broth, protein drinks, eggnog, wine, tofu and ice cream and frozen yogurt.
“Improving Denver’s recycling and waste diversion is a leading component of our Greenprint Denver initiatives,” says Hancock. “We’re excited to partner with Waste Management, the Carton Council and WhiteWave Foods to bring this new recycling opportunity to our residents.”
The city of Denver has partnered with Waste Management to sort and market the materials collected through Denver Public Works’ Denver Recycles program for close to 20 years. Waste Management says the addition of cartons to the curbside program is possible because of continued efforts to improve its Denver material recovery facility (MRF) and its partnership with the Carton Council to expand recycling market development.
“We are pleased to be able to partner with the city of Denver, the Carton Council and WhiteWave Foods to create the opportunity to recycle more waste,” says Scott Bradley, area vice president, Waste Management.
Blaine McPeak, president of WhiteWave Foods, says, “We’re proud to support carton recycling efforts and to bring valuable information about the benefits of carton recycling to our more than 50 million consumers nationwide.”
Cities in more than 40 states now accept cartons as part of their residential recycling programs. The recovered cartons are shipped to paper mills, which use their paper fiber to produce tissue products.
> METALS
AFRA Publishes Aircraft Recycling Best Practices Guide
The Aircraft Fleet Recycling Association (AFRA), based in Washington, D.C., has published the “Best Management Practices (BMP) Guide” for the recycling of aircraft materials.
The association also has announced that its first accreditations under the new BMP have been awarded to ELG Metals, Los Angeles, and to Huron Valley Fritz West of Tucson, Ariz.
AFRA says the accreditation assures that recycling facilities operate in a safe and environmentally responsible fashion and allow businesses to find sustainable solutions.
According to AFRA, aircraft recyclers represent a growing portion of AFRA membership, and the new guide is designed to help them capture the maximum value from aircraft at the end of their service by increasing the amount of materials that can be recycled and raising their overall residual value.
The guide has been developed by AFRA members, including aircraft and aircraft parts manufacturers, maintenance companies, leasing operations and disassembly companies.
AFRA Deputy Director Bill Carberry, who also is a strategy analyst with Boeing Commercial Airlines, played an integral role in helping to develop the guide. “Our idea was to have an industry prescribed document to set the standards for how aircraft should be taken apart in an environmentally responsible way,” Carberry says. He says the document provides training, tools and guidelines to help ensure that disassembly occurs in the proper order. A further objective, Carberry says, is to recover aircraft-grade materials so they can be recycled yet still remain within the aerospace industry.
AFRA says the new BMP guide has been incorporated into its accreditation program, adding aircraft materials recycling to an already extensive list of retired aircraft management activities that were built into previous versions of the program.
> ELECTRONICS
Creative Recycling Systems, Intersection LLC Sign Recapitalization, Strategic Deal
Creative Recycling Systems (CRS), Tampa, Fla., has signed a recapitalization and strategic partnership with Intersection LLC, Westport, Conn. Intersection will provide capital that will allow the electronics recycling company to expand its operations.
CRS, which has been in business for 18 years, supplies companies, government agencies, nonprofit organizations, educational institutions and other clients with solutions for electronic equipment reuse and recycling.
“The Creative Recycling team has dedicated heart and soul over the last 18 years to build a world-class IT asset management and electronics recycling company,” says Jon Yob, CRS CEO. “We are so excited to partner with the Intersection team to scale our platform globally. Intersection has tremendous relevant experience, will be excellent partners for Creative and they share a similar passion for excellence.”
Rich Rakowski, principal at Intersection, adds, “We have been exploring, engaging and committing ourselves to the electronics recycling market for quite some time through the collaboration with a true market-making partner. We have found such a partner in CRS.”
In related news, CRS, along with GreenRock Rare Earth Recovery Corp., has acquired BluBox Rare Earth Processing Technology, a system designed to recover heavy rare-earth elements from electronic scrap. BluBox was manufactured by Bluebox Trading AG, a Swiss company. According to the arrangement, GreenRock has the exclusive rights to the technology in the United States.
“GreenRock and Creative Recycling are making a significant investment in world leading technology, bringing true e-cycling solutions to the U.S.,” Yob says.
> ELECTRONICS
CEA Reports Increase in its eCycling Leadership Initiative in 2011
The Consumer Electronics Association (CEA), Arlington, Va., has reported that it has seen a significant increase in the volume of electronics recycled through its eCycling Leadership Initiative in 2011. The CEA recently released a report on the eCycling Leadership Initiative. Highlights of the report include:
- Participants of the eCycling Leadership Initiative arranged for the recycling of 460 million pounds of consumer electronics, a 53 percent increase from 2010.
- Electronics manufacturers and retailers increased the number of recycling drop-off locations for U.S. consumers to nearly 7,500 from around 5,000 one year ago.
- By the end of 2011, 96 percent of the recycling done by eCycling Leadership Initiative participants was conducted in third-party certified recycling facilities.
- CEA launched GreenerGadgets.org to educate consumers about eCycling and energy consumption. By entering a ZIP code, the CEA says individuals can locate the closest responsible recycling opportunity sponsored by the CE industry and/or third-party certified recycler.
“In the first year of the eCycling Leadership Initiative, our industry has made significant progress toward its goals due to the hard work of our member companies,” says Gary Shapiro, president and CEO of CEA. “We continue to push for a national solution to eCycling that will eliminate the costly and confusing patchwork of state regulations.”
The eCycling Leadership Initiative, also known as the Billion Pound Challenge, represents a collaboration among consumer electronics manufacturers, retailers, collectors, recyclers, nongovernmental organizations and governments at all levels. It aims to responsibly recycle 1 billion pounds annually by 2016.
> PAPER
Cascades to Close Board Mill
Cascades Inc., headquartered in Kingsey Falls, Quebec, has announced plans to close its Norampac containerboard mill in Trenton, Ontario.
The company says the decision follows the rejection of its final offer to the mill’s employees regarding a new collective bargaining agreement. Cascades says it planned to close the mill no later than June 1, 2012.
“Despite substantial investments made by Cascades/Norampac to help increase its profitability, the Trenton mill has incurred significant losses over the years. These losses, combined with unacceptable labor relations, have left us with no other choice but to close the mill,” says Marc-André Dépin, Norampac president and CEO.
Nearly 130 employees will be affected by the closure, Cascades reports.
The mill has an annual production capacity of 150,000 tons and consumes 60 percent wood fiber and 40 percent recycled material to produce its corrugated medium. Its closure could lead to losses of nearly $9.5 million to the local forest industry, Cascades reports.
> METALS
BMG Recycling and Resources, HKRR Merge
BMG Recycling and Resources, a metals and electronics recycler based in Richfield, Ohio, has merged its operations with HKRR LLC, an Asia-based metals recycler, to form HBMR Holdings LLC.
BMG Recycling and Resources has four operations: Bay Metal in Richfield; Itran Electronics Recycling, Richfield; Bay Metal South, Millersville, Tenn.; and Low Country Metal, Hardeeville, S.C.
HKRR has facilities in Chicago; Elkhart, Fort Wayne and Indianapolis, Ind.; Memphis, Tenn.; and Houston.
Manjot Singh, BMG president and chairman of the newly formed HBMR Holdings, says, “By merging BMG Recycling and Resources with HKRR we are able to build off each other’s strengths. BMG Recycling and Resources has the experience in building peddler operations and managing industrial recycling throughout North America, while HKRR opens up the door to more Asian consumers.”
> COMMERCIAL
Alpine to Issue Monthly Reports to Customers
Alpine Waste & Recycling, Commerce City, Colo., has launched a program designed to measure its customers’ recycling and composting efforts.
Alpine reports that it has outfitted its entire fleet of 60 trucks with smart devices that weigh and record the contents of each customer pickup. These data are used to provide monthly automated reports to Alpine’s customers detailing the waste diversion percentage and sustainability impact of their recycling efforts.
“Our automated reports will accurately display the quantity of material recycled, the waste diversion percentage and its impact on the environment for our customers,” says Alpine President John Griffith.
> PLASTICS
Study Highlights Growth in Plastic Bag Recycling Efforts
A study released by Moore Recycling Associates, Sonoma, Calif., claims that more than 91 percent of the U.S. population has nearby facilities that accept plastic bags for recycling. Additionally, according to the report, approximately 75 percent of U.S. residents can recycle other types of flexible plastic wraps locally.
The study, titled “Plastic Film and Bag Recycling Collection: National Reach Study,” looked at flexible polyethylene film and found that more than 15,000 drop-off locations collect the material.
The study adds that despite the availability of collection points, consumers are not yet using this infrastructure to its full potential.
“Plastic bags and wraps are a valuable resource that should be recycled after use,” says Steve Russell, vice president of plastics for the American Chemistry Council. “We’re thrilled that so many Americans have access to recycling and we look forward to working to increase consumer awareness, so we can recycle even more of this material.”
Russell adds, “Education is the next critical step. Awareness and convenience are key to changing behavior, and we frequently see that when awareness meets convenience, consumers are very willing to recycle their plastics.”
Earlier this year, Moore Recycling Associates released a study that found flexible plastics recycling increased by 50 percent during the last five years, reaching close to 1 billion pounds per year in the United States.
Consumers can search for drop-off locations for plastic bags at www.plasticbagrecycling.org.
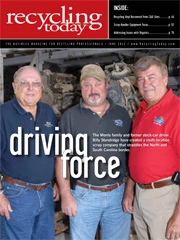
Explore the June 2012 Issue
Check out more from this issue and find your next story to read.
Latest from Recycling Today
- Electrolux commits to recycled content
- Duesenfeld system targets battery cell scrap
- Hyundai says it will make steel in the US
- APR announces Recycling Leadership Award winners
- Glass Half Full opens glass recycling facility in Louisiana
- AmpUp partners with Roundtrip EV
- Global Recycling Day event supports Pittsburgh school's recycling efforts
- President signs executive order on critical minerals