With all of the different types of grapples on the market, all the various features and sizes offered and all the manufacturers to choose from, determining which grapple is appropriate for a particular scrap yard can be daunting. Not only does it matter what material is being moved by the grapple, it also matters where the material needs to go and what size carrier the grapple is connected to.
The orange-peel style grapple is one of the most common types of grapples used in the scrap recycling industry, according to Sean Abenstein of Toronto-based Gensco Equipment. The main reason for this choice is the grapple’s versatility.
“They have outstanding capabilities as far as versatility,” he says. “They can grab various types of scrap.” Loose scrap, bundles, No. 1 or No. 2 shred, pig iron, broken steel, cars and automobile shred are just some examples of what an orange-peel grapple can handle, according to Abenstein. But even this type of grapple has variations depending on the specific needs of a scrap yard.
Mix and Match
The first consideration when deciding on a grapple will be the operating weight and lifting capacity of the excavator or material handler the grapple is being mounted to, says Abenstein. “Then they have an idea of the kind of weight and attachment they can put at the end of the stick,” he says.
Ron Szpak of Seattle-based Young Corp. says the machine size and configuration and the boom and arm lengths will contribute to the capabilities of the machine. Manufacturers typically provide a lift chart that illustrates the gross lifting capabilities throughout the boom and arm, he says.
“In scrap handling, a well-designed grapple is capable of getting up to a 20 percent bonus,” says Szpak. He adds that in a scrap processing operation, a grapple is typically sized for near full reach.
“Most yard machines require a great working radius around the machine as they multitask,” he says. “This could involve feeding a baler, shredder or shear and at the same time stacking, reclaiming, sorting, offloading trucks and cleanup. He reiterates, “To prevent having to move or reposition the machine during multitasking, it is best to size the tool for full reach.”
Grapple manufacturers usually offer a range of grapple sizes that correspond with machine size. “A grapple manufacturer should have knowledge of the machine’s hydraulic capabilities, so the grapple hydraulics will be compatible with the machine,” Szpak says.
Once the size of grapple the machine can handle is determined, other factors to consider, according to Szpak, include the type of yard, the type of scrap supplier and the size of the operation.
Szpak says a smaller scrap yard may benefit from a combination magnet grapple or a small carrier with a small grapple. A larger yard, he says, will be more concerned about production, making a larger carrier and tool or a more specialized tool more beneficial.
Szpak adds, “The most important decision is what does the user want to accomplish at the end of the day?”
Maximizing Production
Szpak says different grapple types and design options help optimize production. He recommends the standard four-tine, orange-peel grapple for general purpose use, such as sorting, feeding shears, shredders and balers, loading or unloading trucks and railcars, stacking, reclaiming and cleanup.
Another popular option is the combination magnet grapple. This is used when there is a frequent need to change back and forth from a magnet or a grapple. “The benefit of having the magnet on the grapple is it will prevent frequent changing of the tools,” says Szpak. “The grapple is used for production, and the magnet is used for cleanup or for handling small items in combination with the grapple.”
Dan Raihala, grapple engineer for Genesis Attachments, Superior, Wis., says that as a general rule, “installing the largest grapple that will fit on each specific material handler will be the most efficient way to move materials.”
When a large auto shredder is being fed, Raihala says, “Large capacity grapples are important, however many operators want a grapple that can still fit within the confines of the conveyor system in order to remove items if there is a problem.”
Some grapples are low profile and some are upright with long columns. The low-profile grapples allow operators to reach deep down into the corners of containers and throw material higher up on a pile, according to Abenstein.
Counting Fingers
Grapples are usually made with four, five or six fingers, or tines. Abenstein estimates that 90 percent of scrap yards prefer the four- or five-finger grapples, but adds that one isn’t necessarily better than the other. “It really comes down to preference,” he says. If containers are being loaded, then the operator may want to limit the opening radius of the grapple.
Mark Vandenberg, general manager of Bateman Manufacturing, Shanty Bay, Ontario, says a four-tine grapple is essential for loading trucks and railcars, so that it can access all areas of the trucks and cars. It also is important that the grapple be small enough to fit inside the vessel, he says.
But there are situations when a five-tine grapple is the best fit.
“For an application loading barges and handling smaller debris, a large, five-tine grapple is ideal for less spillage and maximum volume,” Vandenberg says.
When the application involves movement of ferrous material, Vandenberg recommends a magnetic grapple. “Not only is a mag grapple ideal to mag-out and maneuver material, but it also has the ability to assist in cleaning up the area afterwards,” he says.
Raihala says the number of tines, the tine shape (pointed or flat) and tine width are all important features to consider when choosing the proper grapple. “For example, if moving long items, such as pipes or structural beams, a Genesis four-tine, pointed shaped, medium spade will work best. If moving fine, shredded material, a four-tine or five-tine, flat-shaped wide-spade tine will work best.”
Grapple manufacturers agree that 360-degree rotation is an important feature on a grapple. “The rotation helps position the grapple quickly and accurately,” says Szpak. “A skilled operator can position the grapple to lift a single item or go for a bonus pick.” He adds the rotation can position the grapple to help fit in a trailer or a rail car for either loading or unloading.
Vandenberg says 360-degree rotation allows the grapple to be positioned at any point. “It also limits excessive strain and rotation load and allows material to move freely.”
An Upward Trend
Abenstein notes that the grapple industry is very competitive and that one only needs to open up an issue of Recycling Today to see how many different manufacturers are out there advertising.
“The market has been very good. Competition is good,” he says.
Szpak observes that the number of companies manufacturing grapples has increased during the years.
He recently attended the Institute of Scrap Recycling Industries Inc. (ISRI) annual convention in Las Vegas in April. It was his 26th time attending the show. At Szpak’s first convention, he recalls only three grapple manufacturers exhibiting at the convention. This year, he says he counted 14 grapple manufacturers, something he says is a testament to the essentialness of the grapple to the industry. “This only shows how important the grapple is in the scrap processing industry,” Szpak says.
The author is managing editor of Construction & Demolition Recycling, a sister publication of Recycling Today, and can be reached at ksmith@gie.net.
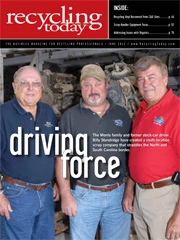
Explore the June 2012 Issue
Check out more from this issue and find your next story to read.
Latest from Recycling Today
- Glass Half Full opens glass recycling facility in Louisiana
- AmpUp partners with Roundtrip EV
- Global Recycling Day event supports Pittsburgh school's recycling efforts
- President signs executive order on critical minerals
- Registration opens for Scrap Expo 2025
- Toyota opens ‘circular factory’ in UK
- Agilyx works with former Plastic Energy CEO on sourcing venture
- 2 factors raise ferrous export questions in April