Winter often has provided challenges to ferrous scrap processors, especially in parts of the country where snow and ice certainly can interrupt travel and discourage outdoor work.
The winter months of the first quarter of 2015 proved no exception to this pattern, in many ways surpassing prior winters on the misery index by including sharp drops in ferrous scrap pricing that caused some small dealers and scrap generators to hold on to material.
As scrap yard operators and ferrous scrap traders moved into the spring months, they were eager to put the first quarter of the year behind them and ideally find weather and market conditions that had warmed up.
Recyclers contacted in late March and early April, if not necessarily optimistic, cite several reasons why the remainder of 2015 may play out differently from the first three months of the year.
Starting from a low point
The first quarter of 2015 was an unpleasant one for ferrous scrap processors measured not only by reduced scrap flow but also by the plummeting per ton prices paid by domestic steel mills and export brokers alike.
Don Zulanch of scrap processing firm Cohen, Middletown, Ohio, estimates that “flows of all retail material are off 20 percent, at least” in his company’s Ohio Valley operating region. Even with reduced buying interest from mills, “It is very hard to hold inventories,” Zulanch says.
On the East Coast, David Caffee of Atlantic Recycling Group, Rockville, Maryland, witnessed a similar first quarter of 2015. “Flows were devastated by weather and by price in February,” he says. “In March it has picked back up, but flows were still down 20 percent from last year’s average—which must be a function of price.” After scale prices drop so steeply, Caffee says, “There is not as much incentive to be a collector.”
Rich Brady, executive vice president of OmniSource Corp., Fort Wayne, Indiana, comments, “Obsolete scrap flows were dramatically lower in the first quarter due to weather and the downward pressure on scrap pricing, which was driven primarily by a lack of demand from domestic steelmakers and the strength of the dollar (limiting exports [and] increasing available supply).”
Prices plunged in February—from $85 to $99 per ton, as measured by the Raw Material Data Aggregation Service (RMDAS) of MSA Inc., Pittsburgh—causing some scrap to go into hiding before it could reach consumers or shredders.
“Scrap flows are certainly reduced, with many individual customers (nondealers, even) holding on to material when they find out how relatively little they are getting for their scrap—both ferrous and nonferrous, too,” says Keith Highiet of Modesto Junk Co., Modesto, California.
A recycler in Florida, who preferred to remain anonymous, says the phenomenon was widespread in his part of the country. “Some dealers were caught with high-cost inventory, not expecting the downturn to be so severe,” he comments. For other companies in the processing chain, “The challenge is to replace tons at pricing that is not attracting a high level of peddler activity.”
As of late March, the Florida recycler says, “This is leading many dealers and auto parts yards to hold inventory in anticipation of a price correction,” though he says their ability to do so is “limited by space and capitalization.”
Brady says he does not expect hoarding of scrap to last for very long. “There was likely some speculating on automobile hulks, but by and large most scrap processors continued to turn inventories given uncertainty in the domestic steel and scrap markets,” he comments. “Notably, the ‘correction’ in the ferrous scrap price has left many players acknowledging a new price range will prevail in 2015 more in line with global steel and scrap prices.”
As these recyclers assess the inventory situation at yards and mills, they see a likely incentive being readied for flows to increase. “Scrap inventories throughout the supply chain have been declining since the beginning of the year as yards and mills relieved inventories in an effort to reset metal spreads,” Brady says.
While that is no guarantee that mills are prepared to begin offering more dollars per ton for scrap, it’s often a precursor.
Building up expectations
Regarding potential kick-starts for an improved ferrous scrap market, the construction and demolition sectors provide one possibility, especially as the ground thaws in the temperate regions that experienced a harsh winter.
In terms of reduced generation in the first quarter of 2015, the prompt grades generated by durable goods manufacturers were not a primary culprit. “Industrial generations of prime grades remained relatively steady during the period, however, pricing on these grades contracted as well in response to the demand-supply dynamics,” Brady says.
When steelmakers and scrap processors complain about weather-related effects, one of the reasons is reduced construction and demolition activity. Regarding OmniSource operations in the Midwest, Brady says, “Demolition activity was minimal in the first quarter due primarily to seasonality and weaker prices.”
In central California, Highiet doesn’t blame the weather for a lack of activity but rather a lackluster regional economy. “Demolition scrap is not too [prominent] in the northern San Joaquin Valley area of California; construction has not been robust here since 2008,” he remarks.
Oil field uncertainty One of America’s largest steelmakers made two announcements within one week of each other that point to the uncertainties of supplying America’s oil drilling, production and pipeline sector. In late March, Pittsburgh-based United States Steel Corp. (U.S. Steel) announced plans to temporarily idle its Granite City Works operations in Granite City, Illinois, which employs more than 2,000 people. “As the primary flat-roll supplier of U.S. Steel’s Lone Star Tubular Operations, the [shutdown] is part of the company’s ongoing adjustment of steelmaking operations throughout North America to match customer demands,” the company stated in a March 25 news release. U.S. Steel referred to the move as a consolidation of operations, commenting, “The consolidation is a result of challenging market conditions that reflect the cyclical nature of the industry. Global influences in the market, like reduced steel prices, unfair trade, imports and fluctuating oil prices, continue to have an impact on the business.” The company also is reportedly laying off several hundred workers at its integrated Fairfield complex in Birmingham, Alabama, but at the same time it announced capital investment projects there tied to oil industry products and new scrap-consuming electric arc furnace (EAF) capacity. In its March 19 news release, U.S. Steel referred to “two capital investment projects valued at a total of $277.5 million” in Alabama. “The first capital project is the construction of a technologically advanced EAF steelmaking facility at [the] Fairfield Works in Birmingham. The company also will construct a tubular products coupling facility at Fairfield Works to manufacture couplings with premium, semipremium and American Petroleum Institute (API) connections for customers in the oil and gas industries.” U.S. Steel President and CEO Mario Longhi pointed to long-term benefits of the projects, saying, “These investments will directly support U. S. Steel’s ongoing transformation journey.” Construction of the EAF will begin in the second quarter of 2015 with construction expected to be completed in the third quarter of 2016, U.S. Steel says. From a scrap recycler’s viewpoint, the oil industry slowdown is noticeable. A recycler in the Southeast comments, “Flat roll mills that have exposure to the oil and gas industry are reporting higher inventories due to production cutbacks and a prime scrap supply that is inelastic.” |
The recycler based in Florida is more optimistic about demolition activity, not only in the Sunshine State but throughout the South. “Demo projects in this region appear to be picking up, with the General Motors plant outside of Atlanta being a significant project,” he comments. “A rebound in commercial construction has been helped by historically low interest rates and pent-up demand coming off the real estate decline approximately five years ago,” he adds.
In Ohio, Zulanch does not point to a booming construction sector, but he does point to a strategic advantage he says Cohen enjoys. “Not much has changed for the better on the overall generation of demo scrap, but we are certainly getting our share. We have Drew Lammers on staff who is our contact with the demo industry. He used to be a manager in that sector and was formerly the president of the National Demolition Association.”
Construction contractors are ramping up for a busier spring as measured by construction employment figures distributed by the Associated General Contractors (AGC), Arlington, Virginia.
AGC says construction sector employers in 33 states added jobs in February, with California, Colorado, North Carolina and Ohio among the biggest gainers. Bucking the trend and shedding construction jobs were New York, Pennsylvania, Maryland, Nevada and Wisconsin.
Flowing in new directions
No matter how much ferrous scrap flows into yards in the spring and summer of 2015, pricing may hit a ceiling if export demand continues to dwindle as it has for the past three years.
After peaking in 2011, demand for U.S. ferrous scrap from overseas buyers has declined steadily, and 2015 is thus far pointing to a continuation of that trend. Recyclers cite several reasons for the phenomenon and several ways it has affected ferrous scrap flows within North America.
Brady says the strength of the U.S. dollar is likely to continue limiting exports until it weakens against the euro, the Japanese yen and other currencies, and the Florida recycler concurs. “The strength of the dollar and the U.S. economy compared to Europe and other regions will continue to make exporting a challenge,” he comments.
As of the start of the second quarter, recyclers say they see only modest improvements in demand from overseas. “In spot cases we have seen inquiries from overseas buyers to suppliers who face high transportation costs to get to domestic homes and who have access to export shipping outlets,” the Florida recycler says. “The sharp decline in domestic scrap pricing helped reset the price levels to be more in line with the global market,” he adds.
Farther north on the Atlantic Coast, Caffee reports some signs of optimism. “We are hearing there are more bulk cargoes from U.S. East Coast to Turkey, and the [ferrous] container business is strong and competitive,” he remarks.
On the Pacific Coast, export shipping remains critical (with few nearby domestic options) but has been challenging because of reduced demand and the port workers’ slowdown that lingered for several months in late 2014 and early 2015.
Regarding other options available to California recyclers, Highiet says, “We haven’t had much in the way of calls for shipping scrap to Mexico. Some [of our] ferrous material has found destinations in the United States, though, because of the recent West Coast port situation.”
The flow of ferrous scrap from the coasts to inland mills in the Midwest and Southeast has been a growing trend in the previous 12 to 18 months, recyclers say. “During the past few years, scrap exporters, particularly off the East Coast, have adapted their business model to the changing global scrap dynamics,” Brady says. “East Coast export shippers have positioned themselves operationally and logistically to support both domestic (U.S. coastal and Ohio Valley) and export customers, affording them added flexibility in response to global market influences.”
As indicated by Highiet, a similar repositioning has not been as common on the West Coast, Brady says. “Freights from west to east are cost prohibitive, but East Coast scrap [now] regularly travels into the Midwest and Southern markets,” he says.
Brady’s fellow Midwesterner Zulanch says the phenomenon acts as a price suppressor. “The lack of export markets puts more tons in this country, into the South and Midwest,” he says. “It’s not good for any of us, and I’m not sure how the really big shredder operators can do it. They may need to move 40,000 tons of shred per month at a profit.”
In the midst of volatile prices and changing flow patterns, Zulanch and the other veteran recyclers contacted say maintaining a profit margin is difficult, but challenging business climates are as old as the industry itself.
“The key to profitability and sustainability at lower pricing, and most likely reduced volume, is being a low-cost operator and sizing the business accordingly,” says the Florida recycler.
Caffee says he even sees a positive side to the lower per-ton prices, commenting, “In theory, the price is fine if we can hold a margin and keep up volume. We like operating with lower prices—it’s easier on the letter of credit interest and on cash consumption.”
The author is editor of Recycling Today and can be contacted at btaylor@gie.net.
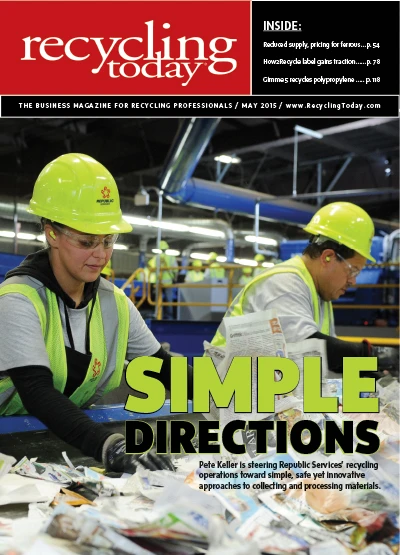
Explore the May 2015 Issue
Check out more from this issue and find your next story to read.
Latest from Recycling Today
- Aqua Metals secures $1.5M loan, reports operational strides
- AF&PA urges veto of NY bill
- Aluminum Association includes recycling among 2025 policy priorities
- AISI applauds waterways spending bill
- Lux Research questions hydrogen’s transportation role
- Sonoco selling thermoformed, flexible packaging business to Toppan for $1.8B
- ReMA offers Superfund informational reports
- Hyster-Yale commits to US production