Wasted food is a huge topic of discussion lately—and that’s a good thing. More than 36 million tons of food waste per year are disposed of in landfills in the United States alone.
While volumes could be written on the societal issues connected to why so much food is wasted in the first place, this article will instead focus on how to put wasted food to good use by diverting it for energy generation. It also will look at sources and effects of contamination on the process.
Several states and major metro areas recently implemented bans on the landfilling of food waste and, instead, indicated sending the discarded food to composting or anaerobic digestion (AD) operations. Wasted food is typically an excellent source of energy in an anaerobic digester.
AD relies on ancient bacteria from the methanogenic archaea domain of microbes that function in oxygen-free digesters. In this oxygen-free environment, bacteria can convert organic material into methane—or renewable energy. For these bacteria to convert food waste to energy, they must make good contact with the food for a sufficient time.
However, depending on its source, food waste can be highly contaminated with a variety of other materials. This contamination interferes not only with the good contact needed between bacteria and organic material but also can cause significant operational issues for digester components.
Let’s consider a number of different sources for wasted food. Each food waste stream has its own set of obstacles, some more challenging than others. Referring to the table below, different sources of food waste have been generally characterized by their degree of contamination using a scale from one to five, with five containing the most contamination.
The contamination level becomes much more significant once food has gone through the hands of the consumer, and simple screening often will not suffice. Many institutions or commercial facilities implement educational programs encouraging consumers to dispose of food in specially marked bins; programs such as these can have a tremendous impact on contamination reduction.
Optimizing the energy potential of various wastes and their contaminants requires careful review and selection of appropriate digester technology.
Wet versus dry technology
Digestion methodology is divided into two major categories: wet or dry fermentation.
Wet digesters come in various configurations, such as complete-mix stirred, plug flow, mixed plug-flow and variations of these. The primary distinguishing factor between the configurations is the percent solids, or percent TS (total solids), that the digester operates at. Wet digesters typically handle input waste that is pumpable and operates anywhere from 7 percent to 15 percent TS. Even on the higher end of the wet digestion spectrum with a 15 percent TS, the material is still fairly wet. (Note, discussion of wet digestion in this article does not include high-rate digesters, which operate at 1 percent to 2 percent TS).
Wastes with little contamination or requiring only simple prescreening often make their way into wet digesters. One such scenario could involve screened and pulped waste collected from a university kitchen or a grocery store’s prepared foods kitchen. If available, these wastes could be combined with material from a nearby potato chip manufacturer. These combined wastes easily can be pumped into a wet digester and have the potential to produce significant volumes of methane for energy use.
Dry digesters, on the other hand, are typically batch-operated tunnels or bays that operate with input material that has a TS of 20 percent and higher. Feedstock or wastes loaded into a dry digester are typically stackable and cannot be pumped. Dry digesters are extremely useful in applications where liquid wastes are not available for creating pumpable slurries as is done in wet digestion.
Expired foods or rejected produce from large grocers are scenarios where dry digestion may be the best option; here, the waste itself can be made up of large items, i.e., watermelons, heads of lettuce, ends of deli meats, etc. This type of stream lends itself to use in a dry digester where pulping the material is not necessary.
Municipal collection of green bins or municipal solid waste garbage bins typically results in the most contaminated streams. This waste material often contains a variety of contamination and requires the highest level of sorting and screening to produce a stream suitable for digester use; however, not all the contamination is removed.
Consider a typical collected garbage bag. Its contents may include glass bottles, plastic yogurt cups, batteries, various assorted packaging, shoes, even electronics; glass could break, plastics might crack and so on. Many of these inorganic materials will pose little problem as most modern waste receiving stations can remove metals with magnets, float out plastics, sort out large items and screen small items down to 2 inches in diameter. The resulting 2-inch organic fraction—though still containing some glass, plastic or other contaminants—becomes suitable for use in a dry digester, since maceration and pumping are not required.
If wet digestion is to be used with the 2-inch fraction, then additional screening is required to protect equipment from the effects of excess ground glass.
Understanding the economics
The degree of contamination not only influences the type of digester technology used but project economics as well. In the table on page 108, various food waste sources are noted by their potential available energy. Potential energy is measured by a series of lab scale digestion tests called biochemical methane potential (BMP). Using data such as these is useful for project planning to begin understanding the potential economic benefits and which technology would be the best fit.
For example, if a project is to be developed using 5,000 tons per year of postconsumer waste plus another 10,000 tons per year of green bin waste, the expected energy output would be in the range of 600 to 650 kilowatts (kW) or 45,000 to 50,000 million British thermal units (MMBtu) annually, not including any thermal recovery from the use of a combined heat and power (CHP) gen-set. Depending on the market for this energy, the project may earn in excess of $500,000 per year in electric energy sales. However, these earnings must be weighed against the necessary infrastructure required to receive and prepare the food waste required for such a system.
The author is vice president of development and technology of BIOFerm Energy Systems (www.biofermenergy.com), headquartered in Madison, Wisconsin. She has been engaged in the water and wastewater arena for 28 years, actively designing, constructing, operating and troubleshooting projects in anaerobic and aerobic treatment. A version of this article first ran in the March/April issue of Renewable Energy from Waste, another Recycling Today Media Group publication.
Summer school
Renewable Energy from Waste (REW) magazine, a sister publication to Recycling Today, based in Valley View, Ohio, has partnered with solid waste management consultants Gershman, Brickner & Bratton Inc. (GBB), Fairfax, Virginia, to offer a series of webinars to educate and broaden attendees’ knowledge of what is becoming the fastest-growing waste-conversion technology being deployed in North America.
The REW Summer School Series: Anaerobic Digestion, will provide key insights into the process of anaerobic digestion (AD), imperative to municipalities and companies looking into this waste-conversion process as a method of organic waste reduction and energy production.
A four-part series allows attendees to increase their understanding in key areas of AD, from feedstock preparation to technology considerations and energy output possibilities. Those interested can sign up for one or more sessions in this series and listen from the convenience of their desks as speakers share how AD can create value for their operations and how the technology can vary from input to output.
More information, including webinar registration, can be found at www.REWmag.com/REWSummerSchool.
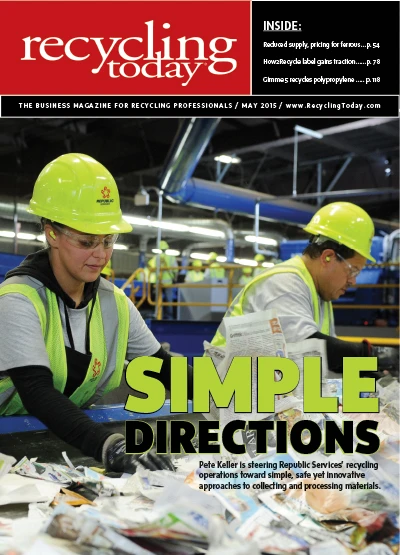
Explore the May 2015 Issue
Check out more from this issue and find your next story to read.
Latest from Recycling Today
- Aqua Metals secures $1.5M loan, reports operational strides
- AF&PA urges veto of NY bill
- Aluminum Association includes recycling among 2025 policy priorities
- AISI applauds waterways spending bill
- Lux Research questions hydrogen’s transportation role
- Sonoco selling thermoformed, flexible packaging business to Toppan for $1.8B
- ReMA offers Superfund informational reports
- Hyster-Yale commits to US production