Lockout/tag out is not just for when a piece of equipment breaks down, but that limitation is just one of the many misconceptions Joe Bateman has heard during his three years with the Institute of Scrap Recycling Industries Inc. (ISRI), Washington, D.C. He says he remembers several site visits where a shredder or baler operator did not understand that lockout/tag out was not only to be used when the maintenance staff was coming to fix a piece of equipment.
The ISRI safety outreach manager recalls one instance where an operator was sweeping up around a machine, but Bateman saw no sign of a lockout. Although the operator had rightly turned off the power to the machine, he did not understand that a full lockout should have been implemented.
“In his mind, he had complete control. Of course that is when things tend to go wrong,” Bateman says. “That is why we need a full lockout in every situation like that.”
According to a statement on ISRI’s website, www.isri.org, lockout/tag out was one of the recycling industry’s most commonly cited violations of OSHA (Occupational Safety and Health Administration) standards, with fines totaling more than $400,000 in 2011.
In addition to stressing that lockout/tag out is to be used beyond when things go wrong, Bateman says it is important to establish a clear plan for implementing lockout/tag out procedures. Requiring every employee to practice that plan regularly also is vital to its success.
During a recent webinar, titled “Lockout/Tag Out: Saving Lives,” hosted by ISRI, Bateman outlined how having a strong lockout/tag out plan could prevent shortcomings and failures.
Take Stock
Recyclers should identify each piece of equipment that requires lockout/tag out, Bateman suggested. The first step in doing so is conducting a hazard assessment. The sources of energy—hydraulic, electric, gravity—must be determined and identified.
He also suggested documenting the extent of the potential hazard and any special circumstances.
“Balers, shears, electrical equipment and conveyors are examples of things that need to be locked out,” Bateman said. “Beyond that, there are other items not to overlook, such as trailers and trucking equipment. We don’t always think of loading and unloading as an issue, but it is,” he added.
For vehicles, Bateman recommended looking into things like glad-hand locks, which can keep breaks locked during loading and unloading. The forklift operator would apply the glad-hand breaks, letting the truck driver know that the breaks were locked during loading or unloading.
After establishing the equipment that requires locking out, the next step is deciding what devices can be used to do so. Bateman said he was positive a proper piece of equipment was available for every lockout/tag out situation.
“Someone somewhere has locked out that machine,” he says.
Locks come in all shapes and sizes and are available for everything from a control switch to a seldom used can of argon, he added.
Write It Down
Bateman suggested establishing written procedures for locking out each piece of equipment. He said the process did not need to be fancy; it just needed to be written down. Employees should know where these written procedures are so they can refer to them often, he added.
Bateman reminded recyclers to consider special circumstances that may affect how a lockout procedure needs to be performed.
He recalled once planning a lockout/tag out procedure for a new piece of welding equipment and discovering that the electricians had routed conduit to the far side of the building because they could not draw enough electricity from the welder’s location. However, they neglected to tell the rest of the facility’s employees about the reroute. By moving the lockout point and noting it in writing, employees knew how to act moving forward, he said.
Train Employees
“There are typically two or three classes of people we deal with,” Bateman said. “The authorized employee is the man or woman who actually puts a padlock on a machine. The authorized employee maintains the equipment. That is someone who is thoroughly trained to use lockout/tag out procedures.”
He added that the employee authorized to perform lockout/tag out can sometimes be the operator of the equipment. It is important to determine the difference, Bateman suggested.
The other category is affected employees, he said. Those who fall into this category must know what to do when an authorized employee has set a lockout/tag out into motion.
Training is an ongoing process that should be revisited often, he suggested. New hires will need to go through the training program, and employees who are promoted will require additional training as well. An effective training program takes time and involves face-to-face communication, Bateman added.
“It’s not enough to say we are going to learn about swimming, and then read about swimming,” he said. “You don’t really know if you can swim until you jump in the water. It’s the same with lockout/tag out.”
Don't Share
Bateman suggested recyclers should not use locks designated for lockout/tag out for other purposes around their facilities. For example, a lockout/tag out lock also should not be used as a toolbox lock, he said.
“If all my lockout locks are red, and I see a red lock on a job box, I know I need to have a talk with that mechanic because that waters down your lockout/tag out procedures,” Bateman said.
Additionally, each shift should have its own color lock, he suggested. Employees should know that yellow locks are from second shift, Bateman shared as an example.
If a lock comes with more than one key, Bateman recommended throwing the other keys away. This eliminates the risk of someone with a spare key unlocking that machine unexpectedly.
“Remember: one lock, one key, one person,” he advised.
Bateman also suggested issuing keys individually or having a lockout station on the wall where only authorized employees can pick up their keys.
In the event that more than one person needs to lockout a machine, each person needs to have a lock and tag on the machine. “In the case of a group lockout, there should be a lead lockout person. It’s the first lock on and last lock off,” Bateman said of the lead’s lock.
Make It Clear
“Let your employees know there are potentially dangerous hazards on machines. Don’t always rely on the original equipment manufacturers to make that clear,” Bateman said.
He suggested labeling each lockout point, so it is clear each time a lockout procedure is performed.
Signs need to be in a language that everyone understands, he added. If employees cannot read and understand the signs posted around the facility establishing that red locks mean ‘do not touch,’ those signs are useless, he said.
Bateman recalled several incidents when employees were jeopardized because they could not read signs warning them not to touch specific equipment.
“Don’t just think signs can be written in one language. If they need to be written in Spanish, write them in Spanish. If people at the facility speak Polish, have signs in Polish as well.”
Authorized employees also should use a tag every time they use a lock. Bateman suggests including the employee’s name and cell phone number on each tag. Even if cell phones are not permitted while at work, Bateman said this will allow whoever discovers the lock to get in touch with the authorized employee even when that person is not at work.
Clearly labeling each lock with a name and cell phone number also will eliminate the time it would take to search through the office to find the contact information, he added
“Some places will even put [the authorized employees’] pictures on the locks, and that is a great additional feature,” Bateman said.
The author is assistant editor of Recycling Today and can be reached at kstoklosa@gie.net.
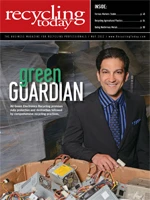
Explore the May 2012 Issue
Check out more from this issue and find your next story to read.
Latest from Recycling Today
- Reconomy brands receive platinum ratings from EcoVadis
- Sortera Technologies ‘owning and operating’ aluminum sorting solutions
- IDTechEx sees electric-powered construction equipment growth
- Global steel output recedes in November
- Fitch Ratings sees reasons for steel optimism in 2025
- P+PB adds new board members
- BlueScope, BHP & Rio Tinto select site for electric smelting furnace pilot plant
- Magnomer joins Canada Plastics Pact