Recyclers processing light metals, such as aluminum used beverage containers (UBCs) or tin-plated steel cans, learn to value flexibility. It is a quality they say also is useful in the baling equipment they employ. This often means selecting a baler that is capable of processing more than one type of material. Matching input/output needs with a baler’s cycle time is one consideration, as is whether to use more than one baler because of different materials being baled.
Jeff Highiet, director of operations for Modesto Junk Co., a scrap recycling company based in Modesto, Calif., and Greg Maxwell, senior vice president, Resource Management, a Chicago Ridge, Ill.-based material recovery facility (MRF), process light metals like sheet metal, steel and aluminum cans, in addition to paper and plastics daily. Thanks in part to trial and error, recyclers like Highiet and Maxwell say they have learned how to process nonferrous metals effectively and efficiently throughout the years.
Overcoming Obstacles
The sequence of material being fed to a baler can have a direct effect on the quality of bale produced. For example, feeding steel cans into a machine before completing a bale of aluminum cans can yield a contaminated bale of aluminum cans, and vice versa.
Maxwell suggests, “You have to make sure you properly sequence the materials that the baler is going to bale so that each bale is not contaminated with other materials.”
He adds that the baler operator and the employee feeding the baler can determine how smoothly the baling process goes.
Highiet also stresses how important it is that employees speak with each other about what they are doing throughout the baling process.
“If you have a good operator on both ends, and they communicate on the same page and understand the limits of the machine and/or the items we are baling, everything will be fine,” Highiet says. “If not, [there will be] problems.”
Additionally, the quantity of material to be baled should be taken into account. Maxwell comments, “Ensure that you have a sufficient quantity of uncontaminated material, so when you make a bale, you can make a complete bale that is ready for shipment to market.”
This step can eliminate the need to re-bale and will prevent rejection of material when it is delivered to the buyer.
Multitasking Machinery
When shopping for balers, Highiet says he prefers to take a direct approach. He suggests recyclers start by listening to what the employees using the equipment have to say. This will allow a recycler to start shopping with a strong grasp on what his or her facility needs to perform at its best.
To accommodate the increasingly varied material flow MRFs are seeing these days, Maxwell suggests investigating a baler’s actual performance on each type of material to be processed.
“Since the cost of a baler can be significant,” Maxwell says, “most MRFs are going to want to have a baler that can bale different types of materials.”
He continues, “If you’re handling different types of material from, for example, residential curbside programs, you may be baling steel cans, aluminum cans, plastic containers and different grades of paper. In that case, you may want a baler that has somewhat of a greater efficiency for a certain material. Rather than have a dedicated baler for each type of material, you may very well want to compromise for a baler that has different utilities to handle different types of materials.”
It is important to know exactly what a baler will be used for before purchasing, Maxwell adds.
Input, Output
Recyclers should look at all aspects of their operations to determine if they are baling light metals in an efficient manner.
Highiet says it is vital to understand a customer’s wants and needs to know if a facility is equipped to meet those demands. Recyclers also need to “maximize full freight and weight limits,” he says.
“Ultimately you need to understand where the materials are going,” Maxwell says. “In other words, what size and density of bale are they looking for? Does your baler meet that requirement or will your bale have to be rebaled or handled in a different way?”
The volume of material that is coming into a plant needs to match the output of the baler.
Maxwell says, “You have to look the size of your MRF and the cycle times of the material you are intending to bale and try to match the baler’s size and efficiency to what you are going to try to feed into that baler on any given day.”
A baler’s cycle times can be increased by adding additional power and improving the hydraulics on the machine, sources suggest.
Additional shifts also can improve an operation’s baling output. This spreads the baler’s costs over a greater number of bales being made each day, and some recyclers find that this is a highly economical solution to implement.
“Many of the MRFs are built like factories, and many factories are built to run more than one shift in order to better utilize the equipment,” Maxwell says.
Metal-to-Metal Contact
Because baling metals means metal-to-metal contact, wear and tear is a daily concern for most recyclers. Maintaining balers, as with most equipment, requires daily visual inspection, Highiet says.
Baling light metals such as aluminum and steel cans usually does not cause jamming problems in a conventional baler because loose cans will surge into and out of the compression chamber during repeated compression cycles. Even so, metal cans gradually cause abrasion to the baler floor, side walls and shear points over time.
Highiet says that if baler wear plates are allowed to wear excessively, the structural components of the baler can start to wear and weaken as a result.
The shear knives of balers should be inspected and adjusted when necessary to make sure that specified clearances are maintained, he suggests. If the gap between the shear knives and the platen (face plate) of the ram becomes too large, this can cause jamming at the shear point and put undue stress on the structural components of the baler.
Unusual noises, vibrations or oil leaks should be inspected immediately, as they may be signs a component of the baler is out of adjustment or about to fail, which also could create safety concerns.
“Anything can be a safety issue, and any potential safety issue can be resolved —it just depends on how much anyone cares,” Highiet says.
The author is assistant editor of Recycling Today and can be reached at kstoklosa@gie.net.
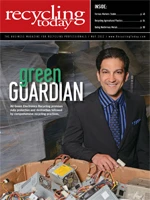
Explore the May 2012 Issue
Check out more from this issue and find your next story to read.
Latest from Recycling Today
- Reconomy brands receive platinum ratings from EcoVadis
- Sortera Technologies ‘owning and operating’ aluminum sorting solutions
- IDTechEx sees electric-powered construction equipment growth
- Global steel output recedes in November
- Fitch Ratings sees reasons for steel optimism in 2025
- P+PB adds new board members
- BlueScope, BHP & Rio Tinto select site for electric smelting furnace pilot plant
- Magnomer joins Canada Plastics Pact