Editors’ Note: The following article is an edited excerpt of “Improving Aluminum Recycling: A Survey of Sorting and Impurity Removal Technologies,” which was published in Resources, Conservation and Recycling, www.elsevier.com/locate/resconrec, and is reprinted with permission of the Massachusetts Institute of Technology. The full paper includes melt technologies that assist in the removal of tramp elements as well as inclusion and hydrogen removal. To access the full document, click here.
Aluminum recycling has a number of key environmental and economic benefits. Compared with other high volume materials, aluminum production has one of the largest energy differences between primary and secondary production: 186 megajoules per kilogram for primary compared with 10 to 20 megajoules per kilogram for secondary. With energy and cost savings in mind, many producers now have targets of increasing their usage of secondary materials.
However, the accumulation of impurities in these recycled material streams provides a significant, long-term compositional barrier to these goals.
Contamination Concerns
A growing number of studies suggest that accumulation of unwanted elements is a growing problem in recycled material streams. In the case of aluminum, the list of problematic impurities is quite large, including silicon, magnesium, nickel, zinc, lead, chromium, iron, copper, vanadium and manganese.
Metal recycling is a metallurgical process and is, therefore, governed by the laws of thermodynamics. The removal of unwanted elements in the scrap stream is dictated by the energy considerations of the melt process. Compared with many metals, aluminum presents a high degree of difficulty in the removal of tramp elements because of thermodynamic barriers. Therefore, with no simple thermodynamic solution, producers must identify strategies throughout the production process to mitigate this elemental accumulation.
There are a variety of solutions to deal with the negative impact on recycling because of accumulation of undesired elements; each presents a trade-off between cost and improvement in scrap utilization (or recycling) potential. Dilution with primary is the most common solution used today; this has a negative impact on recycling. “Down-cycling,” where materials are recycled into lower value products, is another common method of dealing with contaminated secondary materials; this enables higher usage of recycled materials but negatively affects recycling economics. A specific example of down-cycling is when wrought scrap is used in cast products because of their ability to accommodate higher silicon contamination.
As important as these operational strategies are to mitigating the negative effects of accumulation, there are far more technological strategies available to the producer when these operational strategies become ineffective.
Pre-Melt Technologies
While physical separation technologies can be applied to a wide range of scrap streams, they are typically used for scrap that has been shredded.
Magnetic Separation. Magnetic separation is a way to separate nonferrous and ferrous scrap components. Typically, scrap is transported on a conveyor belt equipped with neodymium magnets. As the scrap nears the magnet, the ferromagnetic portion (mainly steel and some iron) is attracted to the magnet and pulled onto a second conveyor, while the nonferrous portion falls into a collection bin. This technology is used extensively in the secondary aluminum industry. Its main limitations are that further separation of the nonferrous scrap stream is not possible and it may still contain many contaminating portions that are not magnetic, such as plastic, glass, rubber, stainless steel, copper, zinc and magnesium.
Air Separation. Technologies using air to separate scrap streams are known by many different names: windsifting, air-knives, elutriation, winnowing, air columns, etc. Their differing names refer to the slightly different mechanisms by which they work.
Conveyor belt systems often use suction to pull off lightweight materials present in shredded automobiles, such as plastic, rubber and foam. These lightweight components are often referred to as auto shredder residue and are commonly landfilled.
In a vertical air separation system, the scrap stream is fed through a column with air pushing upwards; the heavy metals are collected at the bottom, while other materials are pushed through various feeds farther up. Most secondary remelt facilities use some sort of air separation technique to create a mostly metallic scrap stream. The main drawback is the loss of lightweight metallic products, such as used beverage cans and smaller shredded pieces.
Eddy-Current Separation. Eddy-current separation takes advantage of the large range in conductivities of many of the mixed metals present in commingled automotive scrap. Eddy-current separation is similar to magnetic separation. A rotor is lined with neodymium magnets with alternating north and south poles. The rotor produces an external magnetic field that repels nonmagnetic electrically conductive metals. This results in their expulsion from the scrap stream, leaving the nonmetallic particles. The rotor’s speed controls the magnetic field.
Because this technology relies on the magnetic repulsion force generated within the material, some shapes such as wires and foils fail to be separated, as they do not produce a sufficient eddy current.
The extension of this technology takes advantage of the fact that metals with varying conductivity will produce varying eddy currents and will, therefore, be thrown different distances. By setting up collection bins at these varying distances from the rotor, it is possible to separate the scrap stream by base metal.
Sink-Float/Heavy Media Separation. Sink-float separation uses water-based slurries with known specific gravity to separate nonferrous materials with differing densities. To control the specific gravity of the bath, magnetite or ferrosilicon powder is added. For example, in the case of a shredded automotive scrap stream, many of the components have different densities, making it an excellent application of this technology. Fine particles are first screened out of the process; these are often landfilled or shipped to hand-sorting facilities.
For a typical three-step process, the resulting course fraction starts in a water bath (specific gravity of one), which enables separation of much of the nonmetallic fraction (plastics, foams, wood, etc.). Next, a 2.5-specific-gravity bath separates magnesium and higher density plastics. The third bath has specific gravity of 3.5, separating cast and wrought aluminum metals, leaving behind heavier metals, such as copper, zinc and lead.
Drawbacks of this technology include the high cost of maintaining the constant density slurries as well as the loss of hollow or boat-shaped metal components.
Fluidized bed sink float technology is a dry technique using a bed of sand and forced airflow through the bed. By changing the speed of the airflow, one controls the density of the sand, separating different density scrap without transferring them to different liquid baths.
Problems with lubricants on the scrap and difficulties in controlling convection currents have prevented commercialization of this technology.
Color Sorting. Color sorting takes advantage of the color difference between scrap to separate zinc, copper, brass and stainless steel from aluminum in a nonferrous scrap stream. The most basic application of color sorting is when metals are sorted by hand, a prevalent practice in countries with low labor costs. Because of distinctive surface characteristics, hand sorting is capable of sorting wrought and cast aluminum fractions.
Color sorting also can be automated. A computer analyzes images of each piece of scrap and, based on specified color ranges, directs them to different feeds. The technology is not affected by the particle size or shape of the scrap, so it has many capabilities lacking in heavy media and eddy-current separation.
To further separate nonferrous metallic fractions, chemical etching is often used in conjunction with color sorting. This technology has the capability to separate aluminum by alloy family. Two key barriers remain to widespread use of this method, however: (1) the environmental and economic impact of the etching chemicals and (2) surface roughness and the effect of heat treatments done in processing can greatly affect the resulting color of the scrap and final identification and separation.
Other Spectrographic Techniques. Spectroscopy has become more widely used for identification and sorting of aluminum and magnesium alloys in recent years. In this technology, various scrap pieces pass by an array of sensors that trigger one of three main activation methods: (1) X-rays, (2) neutron flux and (3) pulse laser. The relevant source hits the metal, which produces an emission: X-ray fluorescence by the X-rays, gamma ray fluorescence by the neutron flux and optical emission for the pulse laser. Varying types of detectors read these spectra, and a computer signal sends the piece of scrap to the appropriate bin.
Handheld X-ray fluorescence (XRF) units are currently in use. For XRF, the spectral ratios of scrap materials are determined according to their major alloying element, because aluminum has a very low characteristic radiation that cannot be read unless under vacuum. Studies on the commercial applicability of XRF in sorting have shown it to be capable of separating by major alloy family but it cannot determine specific alloys. Neutron activation requires long exposure times to the neutron flux because of its limited intensity.
One technology in particular, laser induced breakdown spectroscopy (LIBS), which uses a pulse laser and optical emission spectroscopy, has shown great promise for sorting wrought and cast aluminum. LIBS was first developed by Los Alamos National Laboratory. Its first application to composition identification of metallic scrap pieces was in 1990 in a joint project with Metallgesellschaft, formerly a large mining and engineering company based in Germany. In this method, a sensor detects a piece of scrap, which activates a pulse laser. The laser hits the surface of the metal and produces an atomic emission. The optical spectra are read by a polychromator and a photodiode detector, which send a signal to a computer system. The system then directs the scrap to an appropriate bin using a mechanical arm. Another system uses an air table, where the detector sends a signal that triggers a burst of air beneath the scrap metal, ejecting it into the correct container.
LIBS has many advantages over current separation technologies for automotive and aerospace applications, as it has the possibility for high speed and high volume. It has capabilities to separate wrought and cast alloys and to sort wrought alloys by alloy family.
However, drawbacks to commercial use remain. Pulse lasers can only penetrate a small distance into the surface of a metal, and, therefore, the scrap must be free of lubricants, paint and other coatings. Oxide formation on the surface also can cause erroneous readings.
Hot Crush. Hot crush is a thermal-mechanical separation method used to separate wrought and cast aluminum alloys. This process takes advantage of the low eutectic temperature of cast alloys, which are high in silicon. Because cast alloys have a lower melting temperature than wrought alloys, holding, or “soaking,” the mixed scrap at a temperature below the eutectic (about 550 degrees Celsius) will result in a weakening of the castings along their grain boundaries.
A subsequent mechanical crushing or grinding causes those alloys to break, and they can be separated from the wrought with various particle size screening. Studies have shown the technology to be 96 percent effective in separating a mixed wrought-cast stream. However, successful segregation requires that the initial scrap be fairly large in size, therefore, separation of shredded scrap streams or smaller products is not possible.
Process Variation
Often, particularly in the case of shredded automotive hulks, commingled scrap will be subjected to a variety of these physical separation technologies to achieve a relatively pure aluminum scrap stream for melting. The sorting technologies used and their sequence of use varies among different secondary producers and scrap processors.
G. Gaustad is with the Golisano Institute for Sustainability, Rochester Institute of Technology, Rochester, N.Y., while E. Olivetti and R. Kirchain are with the Materials Systems Lab at the Massachusetts Institute of Technology, Cambridge, Mass.
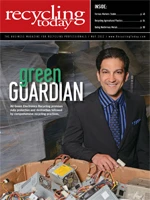
Explore the May 2012 Issue
Check out more from this issue and find your next story to read.
Latest from Recycling Today
- Reconomy brands receive platinum ratings from EcoVadis
- Sortera Technologies ‘owning and operating’ aluminum sorting solutions
- IDTechEx sees electric-powered construction equipment growth
- Global steel output recedes in November
- Fitch Ratings sees reasons for steel optimism in 2025
- P+PB adds new board members
- BlueScope, BHP & Rio Tinto select site for electric smelting furnace pilot plant
- Magnomer joins Canada Plastics Pact