Potomac Metals, with headquarters in Sterling, Virginia, processed nearly 85,000 tons of scrap metal in 2014. The company, which was founded in 1997, specializes in nonferrous metals, specifically copper, brass, aluminum and insulated wires, says Jeremy Wong, who serves as manager of the company.
The privately held scrap metal recycling company serves residential, commercial, industrial and retail accounts and seeks “to provide our varied customer base with the best service and the right pricing in order to generate long-term relationships,” according to the company’s website, www.potomacmetals.com.
The company operates seven scrap processing facilities, with locations in Manassas, Virginia; Springfield, Virginia; Ranson, West Virginia; Waldorf, Maryland; Beltsville, Maryland; and two locations in Sterling. Potomac Metals also operates an electronics recycling facility in Manassas.
Potomac Metals serves customers in northern Virginia, Washington, Maryland and the eastern panhandle of West Virginia. The company offers its industrial customers a number of services.
“As the industry gets more competitive, we have focused on providing mobile pickup services to our industrial clients,” Wong says. “We offer a wide array of services for industrial clients: dump trailers, roll-offs, closed-top containers, carts and boxes for mobile pickup.”
Using its mobile unit, Potomac Metals says it offers same- or next-day service, bringing the scrap yard to its customers by weighing scrap metals and paying its customers at their sites. The company says its trucks are equipped with state-certified scales and lift gates.
Potomac Metals says it offers its mobile pickup service to customers with a minimum of 500 pounds of aluminum, brass, copper and stainless steel for sale.
“Additionally, our seven drive-in facilities service both retail and industrial customers,” Wong adds. “Peak summer days, we see a total of 800-plus customers visit our facilities. We would estimate 60 percent of our drive-in customers are retail and the remaining 40 percent are industrial customers.”
When it comes to selling the nonferrous metals it processes, Potomac Metals sells to the highest bidder, Wong says, adding, “we will package our material any way the customer requests.”
Made to order
To prepare its nonferrous metals for market, the company relies on a variety of baling equipment, Wong says. “We have one Harris Badger horizontal two-ram baler, four International [Baler] horizontal single-ram balers, one Excel horizontal single-ram baler and 10 vertical balers in service currently for our nonferrous metals,” he says.
In deciding whether to install a two-ram or single-ram baler, Potomac Metals considers cost and the amount of material it will be baling, Wong says. “Our single-ram baler can generate a maximum of 10 bales a day, whereas a two-ram automatic-tie baler can process the same amount of material in an hour,” he adds.
Among the items Potomac Metals is baling are aluminum siding, aluminum extrusions, aluminum sheet, insulated copper wire, copper-aluminum radiators and UBCs (used beverage cans), Wong says. “We also bale [stainless steel], copper pipe and aluminum radiators,” he adds, noting that the bales can range in weight from 1,000 pounds for UBCs to 6,500 pounds for heavy-gauge wire.
Prior to entering a baler, Wong says the nonferrous materials are prepped on the ground manually. “We have a labor crew that inspects, sorts and cuts material for our balers.”
When it comes to loading the company’s balers with material, he says, “Uniform loading is key” to achieving optimal bale weights for the various nonferrous materials Potomac Metals bales. “An experienced operator understands that material must be loaded evenly in the charge chamber,” he adds.
Equipment for success
Potomac Metals recently relocated to a new headquarters and processing facility in Sterling. The new location includes a 65,000-square-foot building with a 3,000-square-foot mezzanine that houses the company’s offices as well as a customized warehouse that allows Potomac Metals to streamline operations and provides room for growth, the company says.
The new location also includes two full-size truck scales, multiple ground buy/sell scale platforms that are linked to Potomac Metals’ scale software and an electric material handler.
Wong says the company purchased the Harris Badger for this location, with the key factors for the purchase being the “charge chamber design, motor sizing and the manufacturer response time.”
In fact, these three features have factored heavily into Potomac’s baling equipment purchases over the years, he says.
Wong says that when it comes to the charge chamber, the company is looking for it to be constructed of a material that can stand up to the nonferrous metals the operation is baling every day. “Solid 400 Hardox steel design is typically what we use,” he adds.
Regarding motor size, Potomac Metals believes bigger is better, Wong says. The company typically selects the largest size available, which is generally at least 50 horsepower.
However, in selecting the baler for its newest Sterling location, Potomac Metals kicked it up a few notches. The Badger is a narrow-box two-ram baler equipped with two 100-horsepower motors. According to Harris, the Badger is designed with solid unibody construction, which gives it added strength and rigidity to handle difficult materials. It also features a wider stance to minimize flexing during the baling cycle, according to the manufacturer.
The baler also features the Smart Knife System, which does not use shims, helping to reduce downtime and save operators money, according to the manufacturer, as well as thicker wear liners to increase maintenance intervals.
In-house maintenance
However, Potomac Metals owes its success to more than selecting reliable baling equipment for the nonferrous metals it processes. “Having experienced and knowledgeable operators has been instrumental to our success,” Wong says. “An in-house mechanic with 10-plus years of experience also helps keep downtime to a minimum.”
Potomac Metals maintains its ow baling equipment in-house to minimize downtime, Wong says, adding, “Preventive maintenance is a priority.”
He adds, “Our operators are trained how to clean, tighten/torque bolts and check wear guides on knives and charge chambers.”
The company’s operators are also told of any past issues with its baling equipment and instructed on signs to look for that point to wear on the equipment.
Potomac Metals owes its success in part to these three things, Wong says: properly training its operators, selecting the right baling equipment for the types and volume of nonferrous metals to be baled and properly maintaining that equipment.
The author is managing editor of Recycling Today and can be contacted via email at dtoto@gie.net.
Get curated news on YOUR industry.
Enter your email to receive our newsletters.
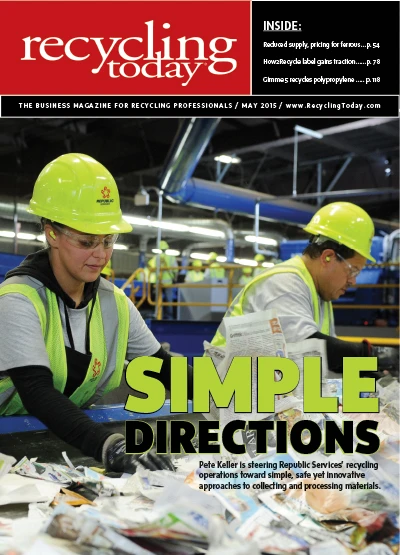
Explore the May 2015 Issue
Check out more from this issue and find your next story to read.
Latest from Recycling Today
- Green Cubes unveils forklift battery line
- Rebar association points to trade turmoil
- LumiCup offers single-use plastic alternative
- European project yields recycled-content ABS
- ICM to host colocated events in Shanghai
- Astera runs into NIMBY concerns in Colorado
- ReMA opposes European efforts seeking export restrictions for recyclables
- Fresh Perspective: Raj Bagaria