Over the last few years, mixed waste processing plants have been installed in many areas of the country. These mixed waste material recovery facilities (MRFs) use similar equipment and processes as single-stream MRFs, but additional processing equipment often is needed to help remove contaminants from the recyclables. Additional processes on the front end of the system and more sensitive separation equipment throughout the system aid recovering marketable grades of paper, plastics and metals, as well as organics, from municipal solid waste (MSW).
Companies that manufacture and install MRF equipment note an increased interest in mixed waste processing system designs. While the reasons vary from customer to customer, interest in further organics recovery or alternative energy are often the main drivers. California’s requirement of 75 percent diversion by 2015, for example, has made mixed waste processing an appealing proposition as it enables a greater amount of material to be diverted from the entire waste stream as opposed to single-stream recycling, which only processes recyclables collected from those residents who choose to participate in curbside recycling programs.
Changing times
Unlike the “dirty MRFs” of 30 years ago, which were designed to capture high-value recyclables from the waste stream, achieving a 30 percent diversion rate on average, the mixed waste processing facilities of today are designed to recover as much as possible from the waste stream—70 percent or more, their adherents says.
Single-stream MRFs start out with a cleaner stream of material than a MRF processing MSW does, but automated technology designed specifically for mixed waste processing facilities is producing successfully salable commodities, according to sources.
Chris Hawn, North American sales manager for Machinex, Plessisville, Quebec, says when it comes to mixed waste MRFs and single-stream MRFs, “There is not a one-size-fits-all solution. Some of the components can cross over between the applications, but there is not a single technology that is a silver bullet.”
Machinex has installed several processing systems in the last couple of years, and, Hawn says, “Each one has a different application with a different desired result.”
One system was designed with the capability to remove source-separated organics (SSO) in biodegradable blue bags from the waste stream while using separation equipment to capture recyclables. Another installation was designed as a refuse-derived fuel (RDF) preparation facility that required removal of undesirable contaminants and drying of the material.
In the system designed for removal of SSO, components of a typical single-stream MRF were removed or replaced by what Hawn describes as “similar technology with better operational benefits while not sacrificing efficiency.
“I would suggest that a system designed for MSW can be engineered such that processing single stream is not a problem. In reverse, a system designed for single stream is not as easy of a transition to [processing]MSW unless the customer is prepared to sacrifice the operations,” Hawn continues, noting higher maintenance requirements and increased wear and tear as a result.
The differences
Dirk Kantak, director of sales for San Diego-based CP Group, describes the major configuration differences between mixed waste MRFs and single-stream MRFs. He says mixed waste processing facilities typically start with a trommel screen after the presort to split the waste into fractions based on size and weight. Single-stream systems typically begin with an old corrugated containers (OCC) screen following the presort. MSW processing systems also tend to use more air separation than single-stream systems.
The major differences between processing materials in a mixed waste MRF versus a single-stream MRF are seen at the front end of systems. John Green, president of Green Machine, Hampstead, New Hampshire, says presorting at the mixed waste MRF occurs to “remove nasty materials.”
Bag opening devices and manual presorts remove bulky items that could damage the downstream equipment. Air drums separate heavy materials from light materials. The light fraction is then delivered to a “more traditional single-stream-like system,” Green says. However, he adds, “It is highly contaminated and requires a great deal of additional labor to inspect the material in order to make [recyclable commodities suitable for] current markets.”
The heavy fraction undergoes additional screening to remove fines and glass and to further remove ferrous metals. Compostable and aggregate materials also are identified for recycling.
“Mixed waste MRFs have to be ready for anything, including the kitchen sink,” says Brian Wells, sales operations manager for Eugene, Oregon-based Bulk Handling Systems (BHS). “The most significant challenge when processing MSW is conditioning the waste stream to allow for efficient recovery of the available recyclables.”
Wells continues, “In single stream, the material is mostly predictable, and the vast majority of what goes into a plant should come out as a recyclable commodity.
“In mixed waste processing,” he says, “we can still recover a very high percentage and achieve best-in-class diversion rates, but additional equipment is required due to the challenges the material provides.”
Wells says most single-stream plants operating today would struggle to efficiently process mixed waste. “The contamination levels are simply beyond what those facilities were designed to effectively handle.”
While Wells contends that processing systems can handle both MSW and single stream, it all comes back to the conditioning steps—removing the organics and inert materials prior to the final sort.
Many mixed waste processing plants designed by BHS incorporate its Debris Roll screen (DRS) and Nihot Single Drum separator (SDS) to eliminate those types of materials. The DRS removes the fines and organics, while the SDS classifies the stream according to density.
Wells says the next steps in a mixed waste processing system also are used in single-stream systems: the BHS polishing screen to separate the 2-D material from the 3-D material and NRT optical sorters for final recovery of recyclables.
“The result is exceptionally high recovery and product quality previously unheard of in the old world of ‘dirty MRFs’. These are advanced, modern production facilities, and using that old moniker really does them a disservice,” he says.
Stamford, Connecticut-based Van Dyk Recycling Systems (VDRS) will incorporate a bag opener or primary size reducer at the front end of the mixed waste processing facilities it installs. Brian Schellati, VDRS director of business development, says the company applies a variety of technologies to handle the variability of the waste, including Walair density separators, Lubo AWS (antiwrapping) screens and Titech sensor-based sorters.
Quality concerns
Concerns about quality regarding the secondary commodities recovered from mixed waste processing facilities do not come as a surprise to systems suppliers.
“We have found the most outspoken opponents usually represent buyers who are worried about inbound material quality, and that is understandable,” Wells says.
“We heard these same concerns during the rise of single-stream recycling—mills and processors were worried about contamination from a mixed stream,” he continues. “As single stream became more prevalent, those voices died down because the technology performed. Increased participation rates and efficiencies won out, as we expect to be the case with MSW processing,” he says.
Hawn agrees that quality concerns are valid. “Trying to simply put a positive spin on it is not doing the industry any service.”
While plastic and metal containers recovered from mixed waste processing systems seem to be of suitable quality, the fiber stream is a different story. “In the scenario where household organics are loose in the stream, there is no question that fiber quality suffers,” he says. “Programs such as blue bag or SSO can improve the quality.”
The input percentages also differ greatly between a single-stream MRF and a mixed waste MRF. That being the case, Schellati says recovery percentages from both types of facilities are about the same.
Schellati’s colleague Wilfred Poiesz, western region vice president for VDRS, explains that mixed waste processing facilities achieve 70 to 80 percent recovery of recyclables from 100 percent of the MSW stream. He says these facilities “easily achieve high recovery of hard plastics, metals and nonferrous metals.”
Recovery of plastic film is possible, he says, but relatively expensive.
“The best strategy is to extract mixed film, then sort the high-quality clean film,” Poiesz says. The remaining material would be a low-grade mix or can be used in fuel.
Paper can be separated at multiple levels of the processing system to produce multiple grades, including clean fiber, wet fiber (drying required) and a fraction to be used in the organics, which is composted or used in anaerobic digestion.
The wave of the future
Green says he isn’t convinced mixed waste processing facilities can be profitable in the current market because of their high capital costs and the manpower needed to produce marketable commodities.
Green continues, “It is my belief that technologies currently don’t exist that are capable of efficiently removing recyclable materials from a highly contaminated waste stream.”
That being the case, he adds, “Green Machine is seeking and developing technologies” for mixed waste processing. “Green Machine does feel strongly it will be the wave of the future once the technology improves and landfill costs increase, but we are not there yet,” Green says.
Hawn shares his skepticism regarding conversion technologies, which are a driver for many mixed waste processing facilities, saying the commercialization of conversion technologies and alternative energy “is limited and, aside from mass-burn, there is very little long-term experience in this market.”
He adds that some recent installations have not yet added conversion technologies to the back ends of their systems to fully prove themselves.
Schellati says mixed waste processing facilities in Europe use a combination of conversion technologies effectively to reduce residuals.
“The preprocessing systems and separation technology that we supply for these conversion technologies is already commercially proven, but the challenge is just getting both technologies working together on the same scale and have them be financially viable,” he says.
The author is a managing editor for the Recycling Today Media Group and can be reached at ksmith@gie.net.
WANT MORE?
Enter your email to receive our newsletters.
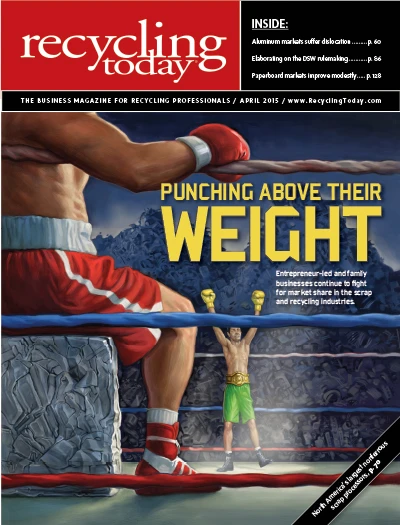
Explore the April 2015 Issue
Check out more from this issue and find your next story to read.
Latest from Recycling Today
- EU levies ELV recycling fines against 15 automakers
- Call2Recycle Canada launches program in Alberta
- The history of SAS Forks: Celebrating 50 years
- SAS Forks partners with NED at Green Recycling in Houston, Texas
- DRKhorse’s RCC series at Gorick Construction in Endicott, New York
- Balar Equipment to operate under Enviro-Clean Equipment name
- Li-Cycle reports 2024 financials
- Wisconsin Aluminum Foundry acquires Anderson Global