
For many years, when a scrap processing company bought a shredder system, it would receive basic installation drawings and the necessary loads of the equipment to build the appropriate foundations and support structures. However, more recently, several automobile shredder manufacturers have increased the scope of their product offerings as well as the range of their services to provide much more than equipment. By using the services of a company that provides full-service system integration, recycling operations may be able to save time as well as money.
Beyond shredder selection
A scrap processor without shredding experience needs to consider many aspects prior to an auto shredder installation. Missing just one of these concerns can have expensive consequences for an operation. Experienced project management from the earliest stages of planning is the key to a successful project that is on time and within budget.
Twenty-two years ago when I first became involved with shredders, few if any companies wanted to take on turnkey projects. Some shredder providers, when asked about turnkey installations, will say they are equipment manufacturers, not construction companies. Yet, who knows how to assemble a shredder plant better than the company who supplied it?
Today, many scrap processors are recognizing the value that an experienced system integrator can bring to an auto shredder installation. Areas where experience can play a major role in ensuring a successful installation include:
Permitting – Potential shredding operations need to consider the current permitting requirements at their sites as well as any future requirements that could be expected. Environmental controls for water and air emissions are continuing to increase. Planning for the future can save thousands of dollars in retrofits. For example, adjusting site general arrangements and equipment locations now, at minimal cost, may allow future upgrades/additions of environmental control equipment without costly relocations. A system integrator should have the experience and resources to plan for those needs.
Engineering – Many aspects of a shredder’s installation require professional engineers. Examples of these aspects are the foundations and pier locations for numerous conveyors, motors, shredder and separation equipment; hydraulic and electrical installation; the design of stairs, platforms and bunkers; the design of system electrical utilities, including HVAC, lighting, power and telecommunication pathways; and construction administration, including review of all inspection and test reports.
Our experience also has taught us that designing and building a motor house can lead to cost overruns on a project. Many contractors and engineers who are unfamiliar with a shredder system may spend many hours trying to custom design new solutions instead of using a time-tested and refined design that is far more durable and easier to maintain. New containerized electrical and hydraulic rooms also can reduce the size of these buildings. For instance, my company, U.S. Shredder, based in Miramar Beach, Florida, has proven and successful designs that we share with our customers as a value-added service.
Civil and concrete construction – Although this is one area that can be handled through local contractors, some system integrators have experienced installation teams on staff that can handle the ground preparation and the concrete for a project. The advantage of having a system integrator do all of this work is that during this stage, other projects, such as staging and preparing the conveyors and other shredder system components for installation, can occur simultaneously.
Mechanical installation – This is an area where we find systems integrators can realize tremendous savings for their customers in the installation process. The system integrator’s crews are familiar with the company’s equipment. I’ve been on many installation sites where the mechanical installer spends hours on the phone with the factory that manufactured the equipment to be installed, asking questions about the correct procedure for the installation of a piece of equipment. Since installation space is tightly constrained, having the correct sequence for the installation and coordination between crafts is critical to maximizing concurrent and parallel installation efforts, so one craft is not delayed by another. Our crew, for instance, has completed many installations of our equipment while integrating with local craft labor for electrical, piping and structural steel, resulting in faster and more efficient installation. The amount of time that rental equipment, such as cranes, is needed is reduced, as well, further adding to the savings.
Site layout and traffic flow – Scrap processors who have never operated a shredder system before often learn lessons after they are up and running that make equipment and customer traffic flow more efficient. System integrators can use their experience with previous successful shredder installations to assist customers with proven ideas on scale locations, unloading, locating unprepared and shredded material and rules and regulations to keep employees and customers safe while in the area.
Peripheral equipment, building and piping advances – Over the years, system integrators have learned numerous techniques when placing buildings and other required structures and systems that save time and money during the installation phase. As previously mentioned, prewired and prepiped hydraulic containers save tremendous time and lessen the size of the motor house. Electrical containers holding the motor control center, PLCs (programmable logic controllers) and even operators stations are another option that yields savings. New hydraulic “flex” piping, although it costs more initially, saves installation time and greatly reduces the amount of welding needed, thus reducing the time needed to flush the hydraulic system before startup.
Nonferrous recovery systems – The equipment available to extract the maximum amount of nonferrous metals from the ASR (auto shredder residue) stream is more sophisticated than ever. The effectiveness of state-of-the-art sensors for the recovery of stainless steel, copper wire and other nonferrous metals greatly depends on how the material is presented for processing. Air aspiration and air density tables have been added to systems where once only trommel and screen separation were used. The integration of these systems requires an experienced team that knows how to link all of these technologies for maximum separation.
Expanded capabilities
These are just a few of the many factors scrap recycling operations must consider before installing new shredders or downstream systems.
The experience and expertise of system integrators often means they can work with the customer to offer a detailed plan for the shredder installation and the site and often can give a “not to exceed” quotation. This takes the guesswork out of a recycling company’s budget and financing for such a project.
Just as shredders and downstream equipment have advanced over the years, so have the capabilities of many of the companies that supply them. On system upgrades and retrofits, for instance, system integrators like U.S. Shredder often will use a three-dimensional scanning device to scan the existing equipment and create a CAD (computer-aided design) drawing for exact measurements and dimensions. This new application is extremely helpful for older systems that may not have accurate engineering drawings on file.
Sponsored Content
Still relying on manual sorters?
Let AI do the heavy lifting. Waste Robotics delivers reliable, high-performance robots tailored for complex waste streams. They require minimal maintenance, are easy to operate, and are designed to boost your recovery rates. Smarter sorting starts with the right partner. Waste Expo Booth #1969 & REMA #2843
Click here to see our robots in action!The next time a recycling operation plans a system upgrade or a greenfield site, they should consider contacting the system integrators in our industry to see if a turnkey installation is the right approach.
The author, president of U.S. Shredder and Castings Group, Miramar Beach, Florida, can be reached at bill.tigner@usshredder.com.
Get curated news on YOUR industry.
Enter your email to receive our newsletters.
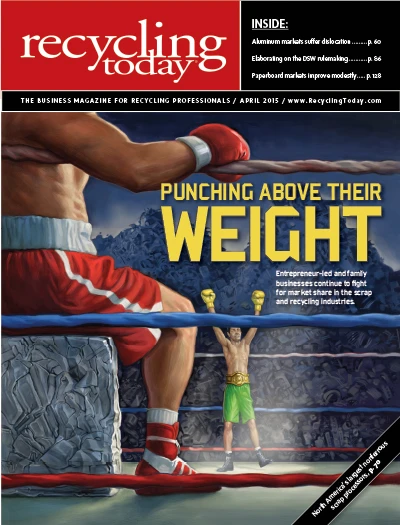
Explore the April 2015 Issue
Check out more from this issue and find your next story to read.
Latest from Recycling Today
- Greenwave asks for SEC filing extension
- EU levies ELV recycling fines against 15 automakers
- Call2Recycle Canada launches program in Alberta
- The history of SAS Forks: Celebrating 50 years
- SAS Forks partners with NED at Green Recycling in Houston, Texas
- DRKhorse’s RCC series at Gorick Construction in Endicott, New York
- Balar Equipment to operate under Enviro-Clean Equipment name
- Li-Cycle reports 2024 financials