Attempts to gather input on the state of the market from two of North America’s largest iron foundry operators in the first quarter of 2015 elicited an identical response: Both companies were in a “quiet” period and would be unable to comment before the deadline.
Both Waupaca Foundry and Grede Holdings are owned by publicly traded entities that at press time were still preparing earnings reports that would later disclose some of the information they were not yet ready to discuss with the press.
The quiet periods adhered to by these publicly traded entities are certainly preferable to the outright periods of slumber the foundry sector has been through at times in the prior two decades.
Thanks in part to previous industry shakeouts and a healthy automotive industry, many iron and aluminum foundries are experiencing sufficient demand to keep furnaces charged and melting. For scrap processors, that ideally means the foundry sector can be one of the bright spots in 2015.
Follow the money
Creators of apps, designers of tech gadgets and online retailers continue to receive healthy amounts of investment capital and attention, but the foundry sector—one of the world’s oldest heavy industries—recently has garnered some capital flows of its own.
A clearer picture (and less dross?) Scientists at Brunel University in London say they have confirmed that treating molten aluminum with ultrasound is what they call “a cleaner, greener and more efficient route to produce high-quality castings.” Molten aluminum alloys at 1,292 degrees Fahrenheit (700 degrees Celsius) naturally contain a high percentage of dissolved hydrogen and, left untreated, the resulting solid metal is highly porous. The most widely used method of hydrogen removal is argon rotary degassing, which can be energy intensive and may require costly components, according to the Brunel researchers. In pilot scale trials funded by the EU Framework Seven Programme, a team at Brunel, led by Professor Dmitry Eskin of the Brunel Centre for Advanced Solidification Technology, found that ultrasound was just as efficient as the standard method but produced far less scrap material (dross). “We know from industry that the price of argon gas continues to rise because making it requires producers to liquefy air, which takes a lot of energy,” Eskin says. “There are also issues with the graphite impellers used. If they break in use, the entire batch of alloy [can be] contaminated and useless.” He continues, “Our pilot scale research with quantities of up to 150 kilograms (330 pounds) confirmed earlier laboratory tests that a moving ultrasound probe could achieve the similar end results (in terms of the resulting casting quality) to using argon but with the advantages of not relying on expensive and fragile graphite rods and expensive gas that cannot be captured and recycled.” Eskin adds, “The fivefold reduction of the amount of dross created is another benefit. Recovering usable metal from dross is also an expensive and energy-intensive process that involves electrolysis.” The next aim of Eskin’s team is to scale up the trials to a level of 0.5 metric ton. The research team says the eventual aim is to introduce cost-effective ultrasound degassing earlier in the production cycle. “Economic drivers like producing lighter engines and lighter car bodies are pushing process improvements in producing higher-quality alloys much further back in the production cycle to where alloys are first smelted,” Eskin says. “Ultrasound treatment holds out the promise of being able to degas effectively and continuously, and we have already made some steps toward achieving this on the pilot level.” |
Foundries, which have been melting scrap metals and casting components in processes that change only gradually over the course of decades, are being purchased for large amounts and issuing initial public stock offerings (IPOs) as the components they make are in demand from a healthy automotive sector.
In November 2014, a subsidiary of Japanese conglomerate Hitachi completed its purchase of Wisconsin-based Waupaca Foundry Inc. for $1.3 billion. The very next month, the holding company that owns Grede Holdings LLC, Southfield, Michigan, announced an IPO targeted to raise $150 million.
The scrap melting and hot metal casting performed by foundries may not be convertible into a sexy smartphone app, but investors seemingly appreciate the industry sector’s tie-in to the ongoing love Americans have for automobiles, light trucks and other forms of transportation.
In its November announcement, Hitachi referred to Waupaca Foundry as “the world’s largest producer of ductile iron and gray iron castings,” adding that the “postmerger integration [with Hitachi Metals] will create a global leader in the automotive, commercial vehicle, off-highway and other industrial sectors.”
Waupaca operates four plants in Wisconsin and one plant each in Tennessee and Indiana and uses ferrous scrap as its primary feedstock at all of its foundries. (The company also says it recycles or repurposes 800,000 tons of foundry sand each year.)
In the light-vehicle market, Waupaca’s foundries produce numerous components, including brake drums, rotors and calipers; flywheels; crankshafts; and differential components. The company says it works closely with automakers and their suppliers to produce the lightweight (yet sturdy) components that are increasingly in demand.
At the time of Hitachi’s purchase of Waupaca Foundry, Hitachi Metals Ltd. Chairman and CEO Kazuyuki Konishi expressed no reservations about the $1.3 billion price tag, saying, “I expect that Hitachi Metals and Waupaca’s role will be ever larger in the global environment. Waupaca will be the foundation of the growth of Hitachi Metals group.”
Metaldyne Performance Group (MPG), the Plymouth, Michigan-based holding company whose subsidiaries include Grede Holdings LLC, announced $15-per-share pricing for its December 2014 IPO of 10 million shares of common stock.
The company’s stock, now trading on the New York Stock Exchange under the symbol MPG, was valued at $18.70 per share as of mid-March 2015.
The stock price reflected the initial reaction to MPG’s fourth quarter 2014 earnings report, which was released just as this issue of Recycling Today went to press in mid-March.
The year-end report was the first since MPG’s acquisition of Grede Holdings in 2014, and in it MPG CEO George Thanopoulos expresses optimism about the future of the holding company with Grede as one of its three core companies.
“MPG’s financial performance improved in all facets, notably adjusted free cash flow and adjusted EBITDA (earnings before interest, taxes, depreciation and amortization) margins,” says Thanopoulos. “In addition, we successfully merged three great companies and recapitalized our balance sheet through our October 2014 refinancing and our December 2014 IPO. All of these actions have aligned our business to take advantage of future profitable growth and realize the combined capabilities of the consolidated organization,” Thanopoulos adds.
More than one material
In its public statements, Grede, like Waupaca, points to the importance of lightweighting in the transportation market and the battle for market share between ductile iron and aluminum in the castings and automotive components sectors.
Grede says it is meeting the lightweighting needs of its customers by developing and producing lightweight, ultra-high-strength, cast ductile iron components for automotive and commercial vehicle chassis and powertrain applications.
The company’s melting of iron and steel scrap to manufacture cast, machined and assembled components takes place at 14 foundries and three machining operations in North America.
“The challenge for cast iron manufacturers like Grede, [which] produce robust engine, drivetrain, axle, steering and other major components for light-duty and commercial vehicles, is to reduce weight without sacrificing performance, durability or safety considerations,” the company says on its website.
One way Grede Holdings has done that is with a material called SiboDur, developed with Japanese manufacturer Riken and now produced at two Grede foundries (one in Minnesota and another in Wisconsin).
“SiboDur is an ultra-high-strength ductile iron [that] is providing customers strong value in achieving lightweight, cost-competitive solutions,” says Jay Solomond, vice president of engineering and technology at Grede. “Parts made from the innovative alloy compete favorably with aluminum in terms of weight reduction and offer exceptional value in durability and performance as well as integration of parts to reduce complexity,” he adds.
With the price of iron or steel remaining 10 percent or less that of aluminum, iron foundries maintain that crucial cost advantage. The aluminum industry, however, continues to compete aggressively in the vehicle component market, with the nonferrous metal’s light weight a major selling point.
“We’re seeing steady demand growth across many of our key markets,” says Ryan Olsen of the Aluminum Association, pointing to the 5 percent increase in demand for aluminum in the United States 2014 compared with the year before.
The association also says its members are investing more than $2.3 billion in current plant expansions and upgrades. “These investments are intended to capture and meet anticipated demand growth for aluminum in the automotive sector as automakers strive to make lighter and more fuel-efficient vehicles,” the Arlington, Virginia-based trade group says.
Tempering the optimism somewhat for scrap processors are the ongoing efforts by the foundry sector (both iron and nonferrous) to minimize the scrap they create. (See the sidebar, “A Clearer Picture [and Less Dross?],” above.)
On balance, however, if Americans continue to purchase vehicles in numbers similar to what they were able to do in 2014, scrap processors are likely to have a steady flow of end-of-life vehicle scrap on the buy side and a stable foundry sector on the sell side.
The author is editor of Recycling Today and can be contacted at btaylor@gie.net.
Get curated news on YOUR industry.
Enter your email to receive our newsletters.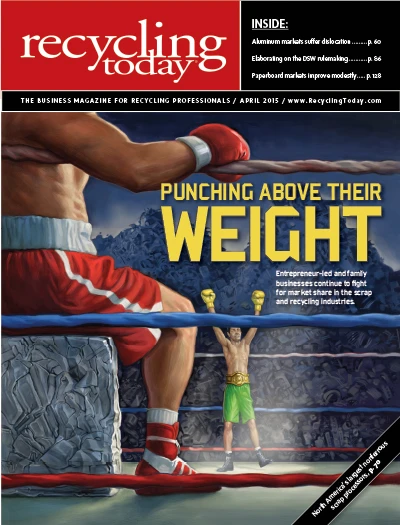
Explore the April 2015 Issue
Check out more from this issue and find your next story to read.
Latest from Recycling Today
- Copper exempted from latest round of tariffs
- Interchange Recycling's EPR stewardship plan approved in Yukon
- Making the case for polycoated paper recovery
- Novolex, Pactiv Evergreen finalize merger
- In memoriam: Danny Rifkin
- BIR adds to communications team
- Greenwave asks for SEC filing extension
- EU levies ELV recycling fines against 15 automakers