Pacific Recycling adds shredder in Oregon
Pacific Recycling of Eugene, Oregon, has installed a complete auto shredder system from U.S. Shredder and Castings Group, Miramar Beach, Florida.
The heavy-duty 80108 shredder was engineered as a turnkey system, including the motor house design, hydraulic and electrical systems as well as civil and foundation requirements. U.S. Shredder also provided mechanical installation of the system.
U.S. Shredder says the automobile shredder includes its heavy-duty Spider Rotor as well as castings and wear parts from its wear parts division.
A 4,000-horsepower DC drive system supplied by AmeriMex of Houston powers the system.
U.S. Conveyor of Mackinaw, Illinois, supplied the conveyors for the project.
The nonferrous system includes a trommel, three eddy current separators and sensors. According to U.S. Shredder, the system is designed to produce up to 150 tons per hour.
The U.S. Shredder and Castings Group offers scrap shredders, control systems, downstream systems, nonferrous recovery and air systems as well as shredder castings, service, engineering, construction and installation to the worldwide scrap industry.
More information is available from Bill Tigner at 205-999-7670 or at bill.tigner@usshredder.com.
Machinex installs processing system in Florida
When St. Lucie County, Florida, decided to switch from dual-stream residential recycling to single-stream recycling, the county also decided to build its own material recovery facility (MRF) to process the collected recyclables. In May 2014, St. Lucie County began single-stream collection, and construction on the MRF was completed in late September of that same year.
According to a news release issued by Machinex, Plessisville, Quebec, the county researched equipment suppliers, emailing some of their customers for their opinions. Machinex was the only manufacturer that got a near-100-percent-positive response from its respective customers, the company says. While the county had multiple selection criteria, including price and design, these factors favored Machinex.
The system St. Lucie County purchased is designed to process 15 tons per hour of residential single-stream recyclables and features a drum feeder, a Mach OCC (old corrugated containers) Screen, Mach ONP Screen, Mach Finishing Screen, a dual-eject optical sorter for PET (polyethylene terephthalate) and HDPE (high-density polyethylene), a magnet for steel cans, an eddy current for aluminum and a two-ram baler. Oct. 24, 2014, marked the MRF’s official startup and ribbon-cutting.
Ron Roberts, solid waste division director for St. Lucie County, says, “The Machinex staff was detail oriented throughout the system design, installation, training and startup of the system, and all equipment is performing as designed and guaranteed.”
Machinex says it supplied the county with “aggressive efficiency and purity performance guarantees for every commodity in the system.”
According to Allison Lankow, education and marketing coordinator for the county, the recycling rate in terms of tonnage and participation has increased by more than 50 percent since the introduction of single-stream recycling last May. She adds that the county invested time and money to educate residents on acceptable items for recycling.
Machinex is a leading supplier of recycling sorting systems. The company has designed and installed more than 300 turnkey facilities in partnership with leading MRF operators in Canada, the United States and Europe.
Vortex to distribute Roter balers
Vortex De-pollution and Recycling Equipment, Denver, has announced that it has taken on distributorship of the Roter car and metal baler range for North America.
Vortex CEO Nigel Dove says that although Italy-based Roter is a relatively new name in the industry, the company has years of experience in baler manufacturing and has quickly established a name for powerful and robustly built machines in Europe.
Roter will launch its new shear baler soon to complete its range, Dove says.
Vortex seeks to offer a full range of equipment to the vehicle and metal processing sector, he adds. “With the Roter balers we now have 140 product line items in our catalogue, all supported from our Denver HQ.”
Vortex President Willem Geyer says the company had been searching for the right baler/logger—one that would stand up to the rigors of the U.S. market and its bigger vehicles—for more than a year. He says, “When we saw the Roter product, I knew this was what we were searching for to add to the Vortex product range of vehicle and metal processing equipment.”
Lindner installs system at Iowa plastics recycler
Plastics recycling company Cedar Poly LLC, Tipton, Iowa, has commissioned a plastics washing system from Lindner WashTech of Grossbottwar, Germany, that is designed to significantly increase its recycling capacity and material quality.
Scott Rogers and Jeremy Rogers, Cedar Poly managing directors, have selected Lindner WashTech’s modular washing system for their plastic recycling plant in Tipton, Iowa.
According to Lindner, Cedar Poly is using the new system as part of its recycling line for postconsumer HDPE (high-density polyethylene), which consists primarily of containers and bottles.
Cedar Poly’s managing directors say the system has kept material clean.
The two men say the company’s previous system had a maximum throughput limit of 660 pounds (300 kilograms) per hour and its cleaning performance was not sufficient to produce a recyclate suitable for direct further processing.
After thorough investigation, Cedar Poly opted to purchase a Lindner WashTech system, with Scott Rogers and Jeremy Rogers saying, “In Lindner WashTech, we found a partner who possesses an extensive know-how in plastic recycling, prepared to design, build and install a system tailored to our needs.”
The custom-designed washing system comprises multiple stages:
In the first step, the shredded HDPE flakes pass a prewashing cycle where they are soaked and contamination, such as stones, metals and glass, is removed.
- In the next stage, paper label residue and other contaminants are separated by two WashTech LF 600 friction washers. These washing units feature replaceable paddles and screens designed to help reduce the overall operating cost, Lindner says. The rotor provides effective cleaning thanks to the optimized dwell time of the material, the company adds.
- Heavier plastic fractions, such as PET (polyethylene terephthalate), ABS (acrylonitrile butadiene styrene) or PVC (polyvinyl chloride), are removed in a further separation stage.
- The material is then sent through a WashTech LMD 2000/1200 mechanical dryer, which features a “gentle” drying action, according to Lindner.
- The final stage is an air wash system, where remaining fines and film particles are separated.
The cleaned and dried HDPE flakes have less than 1 percent residual moisture, Lindner says. Despite the low moisture level and the high supported throughput rates, the company says the operating costs of the advanced washing system are fairly low because no thermal drying is needed and the water consumption amounts to only around 177 cubic feet (5 cubic meters) per hour.
Cedar Poly says that with the new system it is able to achieve throughput rates of up to 5,500 pounds (2,500 kilograms) per hour. And, because of the superior cleaning performance, the recycling company says it can produce high-grade material in-house.
Lindner WashTech is a company within the Linder Group of companies, which is headquartered in Austria and operates U.S. subsidiaries in Raleigh, North Carolina, and in Atlanta.
More information is available at www.lindner-washtech.com/en.
Starlinger introduces RecoStar line
The equipment company Starlinger, based in Vienna, introduced its RecoStar recycling line at the international plastics showcase NPE 2015, March 23-27, in Orlando.
Starlinger says the machine concept is characterized by a very energy-efficient production process as well as by a high degree of automation, which account for reliable and constant production, higher output and great flexibility with input materials.
The RecoStar line also will be the first of the Starlinger recycling lines to carry the “rECO” stamp. “With this stamp, we are highlighting the comprehensive energy-efficient design of the new machine concept,” says Elfriede Hell, general manager of Starlinger recycling technology. By using only motors with the best efficiency ratings, the company says, energy consumption and carbon dioxide emissions are significantly reduced. Features such as energy recovery systems in various process steps as well as infrared heating further reduce energy costs for machine operation.
Designed for recycling plastic scrap from industrial and postconsumer applications, RecoStar lines are suited for lightweight, wet and hygroscopic materials. The Smart feeder optimally prepares the material and feeds it into the extruder. The dynamic automation package ensures the system is running at the ideal operating point, the company says. Consequently, higher output is achieved with lower energy consumption, and higher levels of humidity can be processed. The produced high-quality regranulate is suitable for a wide range of applications.
In addition to Starlinger recycling technology, the company’s divisions for consumer bags, textile packaging and viscotec presented their latest technical products and innovations at NPE.
Get curated news on YOUR industry.
Enter your email to receive our newsletters.
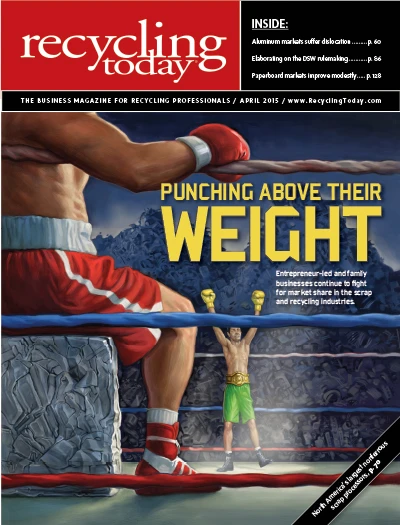
Explore the April 2015 Issue
Check out more from this issue and find your next story to read.
Latest from Recycling Today
- Celsa Group welcomes new Spanish investor
- Ferrous price hikes may be poised to pause
- BIR prepares for Spanish exhibition
- Copper exempted from latest round of tariffs
- Interchange Recycling's EPR stewardship plan approved in Yukon
- Making the case for polycoated paper recovery
- Novolex, Pactiv Evergreen finalize merger
- In memoriam: Danny Rifkin