When China launched its Operation Green Fence initiative in early 2013, the effort aimed to closely manage containerized scrap imports to keep out undesirable material. Not only has the East Asian country recognized that some recyclers have cleaned up their acts, and scrap bales, under the country’s pressure, but recyclers here in the states also are reaping the benefits.
Ross Stoller, a 25-year plant manager for Modern Plastics Recovery, based in Haviland, Ohio, says his plastics recycling company has “most definitely” seen cleaner bales from material recovery facilities (MRFs) since the inception of Operation Green Fence. Bales of milk jugs, detergent bottles and other postconsumer high-density polyethylene (HDPE) plastics have included less polyethylene terephthalate (PET) bottles, ferrous and nonferrous metals, glass and other unwelcome materials, including wood, Stoller says.
Modern Plastics Recovery always has accepted clean and dirty material in 1,000-to-1,200-pound bales. Bale quality that Stoller characterizes as once “horrible” is today often much cleaner. However, the company does still see quite a bit of contamination, “but Green Fence has definitely helped us get more foreign material out of the recycling stream,” Stoller says.
“Prior to Green Fence, China was buying everything they could get their hands on, and they didn’t care about quality,” Stoller explains, adding, “Green Fence has helped to clean up the foreign material in the bales.”
He continues, “We were able to say we want the bales cleaned up, too. It didn’t change the way we did business, but it helped in how we did business because the bales are easier to clean.”
Contaminating convenience
Contaminants have remained at the forefront of challenges for recycled plastics consumers.
Powering production When it comes to trying new things in an effort to better business, one Ohio-based plastics recycler and plastic container manufacturer has proved it is not too timid. Haviland Plastics Products, based in Haviland, Ohio, manufactures 100-percent-recycled postconsumer and postindustrial high-density polyethylene (HDPE) plastic containers mostly for the nursery industry. Haviland Plastics has mastered an in-house process that converts HDPE plastic scrap into flakes, which are washed, dried and aspirated to help pull out contaminants to produce a clean finished product, explains Ross Stoller, a 25-year plant manager for Modern Plastics Recovery, a sister company to Haviland Plastics based in the same city that handles the buying and selling of material for the manufacturer. The flakes are screened, tested and blended to obtain the desired quality and consistency. Carbon black is added to the flakes to increase the durability and longevity of the containers. Stoller says to encourage the recycling of Haviland Plastics’ nursery containers, the company launched a take-back program. Haviland covers its customers’ freight costs and offers them credits toward future purchases based on bale cleanliness, material uniformity and weight. Haviland Plastics says it diverts more than 30 million pounds of plastic scrap annually from landfills through its closed-loop container recycling program. The company also opened an in-house renewable energy facility several years ago. The energy facility consists of an anaerobic digester, primarily using food waste, and direct-drive wind turbines, including three 1.5-megawatt windmills. Power produced from Haviland’s energy facility is used in making the HDPE containers, Stoller says. The facility can provide up to 80 percent of the annual electrical usage at Haviland Plastics. “And when it’s not in use, like on Sundays when we don’t run, the power is sold back to the grid,” Stoller says. |
Regarding incoming material from MRFs, Stoller asks, “How much contamination is too much contamination when you’re purchasing dirty products?”
He notes that public education is needed and necessary. Cutting down contamination levels has an inverse correlation to convenience. “If it’s not convenient to recycle, a good deal of the public will not recycle,” Stoller says.
Convenience also plays a role in Modern Plastics Recovery’s purchasing decisions, Stoller points out.
Modern Plastics Recovery buys and sells postconsumer HDPE plastics for its sister company Haviland Plastics Products. A manufacturer of a range of plastic products for the nursery industry, Haviland Plastics Products focuses on its 100-percent-recycled HDPE black nursery pots.
Modern also handles the buying and selling for its parent company, Haviland Drainage Products Co., a manufacturer of heavy-duty agricultural pipe and tubing made of HDPE and polyethylene (PE).
All of these companies are based in the same city and are family owned.
Modern Plastics Recovery’s warehouse in northwest Ohio stores the plastics recycling companies’ 3-to-5-foot bales. The incoming dirty bales are sorted using automation to remove contaminants, with wood being removed manually, and the plastic is then sent to a Rotogran granulator. Once the plastics are processed into flake form, they are washed, dried and then finally travel through an aspiration system, which helps to pull out even more contaminants for a clean finished product, Stoller describes.
The flakes are screened, tested and blended to obtain the desired quality and consistency. Carbon black is added to the recycled HDPE flakes to increase the durability and longevity of the containers and to produce a uniform color. Other than the machine from Concord, Ontario-based Rotogran, Stoller says the rest of the equipment the company uses daily was designed and manufactured in-house.
Concentrating on Haviland Plastics Products, Stoller says the company rarely brings in injection-grade HDPE and instead uses postconsumer and postindustrial fractional-melt HDPE in its pots.
Stoller explains that using recycled plastics in Haviland’s containers makes economic sense as recycled plastic often is cheaper than virgin material.
“By using recycled plastics, we can keep a good, constant feedstock of material,” Stoller says. “We’re able to buy it more cheaply than virgin and pass it through the line to sell the product more cheaply.”
Plastics pricing
While it is not convenient to jump to different suppliers, Stoller says, the company’s purchasing decisions are based predominantly on pricing and supply and demand. “There are always challenges [in the recycled plastics market], and it is all about supply and demand,” Stoller concedes.
Pricing also affects the regions where Modern Plastics chooses to do business. Over the years, the company has purchased plastics from Canada and Mexico, as well as from across America—from the East Coast to the West Coast.
When rail transportation costs dropped, Stoller says, Modern bought a fair amount of material from California. “The price of rail was cheap, so we were able to do that with a nice price. That has changed as rail costs went up,” he says.
As far as what is driving pricing for the company’s finished product, Stoller says the housing market has a “huge” effect on its market. After a slowdown in business arising from the recession of 2008, business relating to Haviland Plastics Products’ 100-percent-recycled HDPE pots has since picked back up, Stoller notes. He acknowledges that when Americans consider cutting costs at home, “something like landscaping or home improvements would be one of the first items to go.”
More recently, however, he says, “New houses need new landscaping, and that’s definitely an area we’ve seen nice support.”
Closed loop
Where he has seen consistency is with Haviland Plastics’ take-back recycling program. Haviland Plastics accepts used, baled containers from its customers and recycles them back into pots.
The company pays the freight costs and offers credits toward future purchases based on bale cleanliness, material uniformity and weight. Stoller recognizes that it can be challenging to get enough weight on a load to make it worthwhile. Nurseries typically pack a less-dense load than MRF operators, he says. Another challenge with the returned baled containers is that the dirt content is typically much higher than the company prefers, Stoller says.
Foreign material, including mulch, bark, sand and fertilizer particles, can cause havoc on the company’s grinders.
As for participating nurseries, Stoller says they appreciate the program and put a lot of work into returning the blow-molded pots. Participants recognize the value in recycling, he says.
Haviland Plastics says it diverts more than 30 million pounds of plastic scrap annually from landfills through its closed-loop container recycling program.
“The nursery companies that have done this recycling program have done really well,” Stoller says. “I was leery at first, but they’ve impressed me by cleaning [the pots] up, stacking and loading the trailers. They understand the dollars and sense of it.”
He adds, “It probably would be easier to throw them out or burn them … but it has enabled nurseries to recycle these containers and has kept them from the landfill.”
The author is associate editor of Recycling Today and can be contacted by email at mworkman@gie.net.
Get curated news on YOUR industry.
Enter your email to receive our newsletters.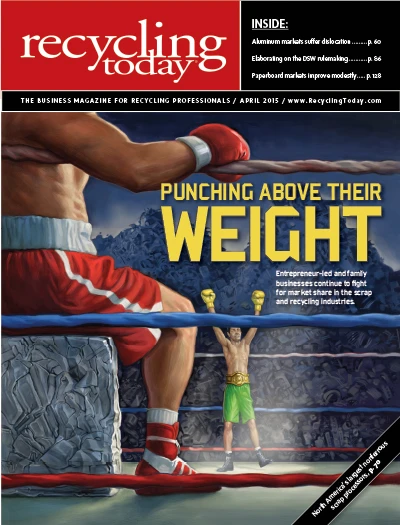
Explore the April 2015 Issue
Check out more from this issue and find your next story to read.
Latest from Recycling Today
- Ferrous price hikes may be poised to pause
- BIR prepares for Spanish exhibition
- Copper exempted from latest round of tariffs
- Interchange Recycling's EPR stewardship plan approved in Yukon
- Making the case for polycoated paper recovery
- Novolex, Pactiv Evergreen finalize merger
- In memoriam: Danny Rifkin
- BIR adds to communications team