Since the technology’s introduction in the 1980s, tailored metal blanks have saved automakers millions of tons of steel. By combining thick and thin steel sheets that get stamped into shape in automotive press shops, they support complex structural parts in most cars and trucks.
Tailoring blanks allows companies to make door panels that are stronger and thicker where they have to absorb crash damage but thinner everywhere else, reducing metal use and lowering vehicle weights. But it’s a steel-born technology, and tailoring blanks is much harder to do in other metals—a problem as automotive companies transition many parts from steel to aluminum.
Blank producer Shiloh Industries thinks it has a solution—laser-welded aluminum blanks that act much like their steel counterparts in stamping presses.
“We’re developing these things now—not because we’re getting requests for it. This is our thinking on where the industry is going,” says Bernhard Hoffmann, executive director, application engineering, for the Valley City, Ohio, company. “Our customers, as they go to aluminum, they’re going to need this.”
Less metal equals less weight
Automakers use laser-welded steel blanks to place small amounts of heavy, high-strength steel in the middle of body structures, surrounding that metal with thin gauges of less expensive material. Hoffmann estimates that an inner door panel, the portion of the door assembly that adds structure and crash protection, weighs about 21 pounds when made from a single-width sheet of steel. Laser-welded steel blanks cut that to about 17 pounds, a 20 percent savings per door, per car.
Simply switching from steel to aluminum generates huge weight savings. With aluminum, inner door panels made from single-width sheets of metal add about 9 pounds to the vehicle, nearly half that of a steel laser-welded blank. However, aluminum is about three times as expensive as steel, so that lower weight comes at a higher cost.
Shiloh Industries has produced test doors using its laser-welding technology on aluminum panels, bringing weights down to 7.6 pounds per door inner, a 16.2 percent drop from the uniform-width aluminum part. Hoffmann explains, “Because aluminum is that much more expensive, it makes this technology that much more valuable.”
Also, not all of the metal in the final door panel makes it onto the car. Some gets cut from the sheets during the blanking, stamping and forming phases. Switching from single-width stampings to laser-welded blanks reduces total material used from 17 pounds of aluminum to about 15 pounds, a 17.7 percent drop. That 8 pound material cut per four-door vehicle can add up when producing more than 100,000 cars or trucks.
As automakers balance their weight-saving needs with materials costs, technologies that minimize aluminum use are going to be very welcome, which is not necessarily good news for aluminum scrap dealers. Hoffmann adds, “If you take a look at the cost-per-pound savings, (laser welding is) going to be a more viable option than going to monolithic stampings.”
Precision welding aluminum
The problem with creating highly tailored aluminum blanks is that the metal isn’t as friendly to processing as steel. In both welding and stamping, the finicky aluminum requires new manufacturing processes.
“The main difference between working with steel and aluminum: When you weld steel, it gets martensitic; it becomes very strong,” Hoffmann explains. “When you weld aluminum, you change the grain size, and it becomes a lot softer.”
For Shiloh, the challenge was twofold: welding aluminum sheets together and creating welds strong enough to handle the stamping process. Hoffman says both problems required research, engineering and a decent amount of trial and error.
Initially, applying laser-welding technology used for steel panels looked like it would be easy. Engineers joined several panels, giving them hope that Shiloh could use existing equipment and processes in new materials. But the welds in those multithickness aluminum sheets split in the stamping presses.
Alternative joining techniques
Automotive customers need consistent, predictable results from parts, so Shiloh’s engineers considered alternative joining methods. One of the first considered was friction-stir welding.
“It’s a cold-transfer, effectively stirring the two metals together,” Hoffmann says.
In friction-stir welding, a spinning tool rolls across the surface of the metal sheets, creating friction that softens but doesn’t quite melt the panels, bringing the metal into a plastic state. Hoffmann says the technology joined the aluminum panels quite nicely, but, he adds, the results weren’t consistent.
“When you try to form it and bend it in multiple directions, we saw a lot of issues,” Hoffmann says. “It made a good part, and then two days later, it would make a crack.”
Intermittent cracks weren’t acceptable either, so that sent Shiloh back to lasers, where Hoffman’s team eventually found the right combination of processes to control the welding. The key was understanding aluminum’s metallurgical properties and using them to create reliable work processes, Hoffman says.
“You need very tight control of the grain growth and heat-affected zones in that area, so you don’t get discontinuities,” Hoffman says. “A lot of the expertise came from the casting side, understanding how aluminum melts and how to control that.”
Blank producers test their products by subjecting them to bend-and-stretch torture tests, simulating the industrial environments of automotive stamping presses. The parts get tested until they fail. A successful test piece breaks where the metal is thinnest, where logically, the parts should be weakest. Failure is when the test piece breaks at the weld joint.
“We’ve run thousands of parts and thousands of test samples and never had a failure inside the weld,” Hoffman says. “We think we have this process down to a tee,” he adds.
Simplified manufacturing
Laser-welded aluminum blanks can reduce the complexity of automotive part making. With steel, tailoring blanks has allowed companies to replace two- and three-part assemblies with one complex piece. With aluminum, some designers have been moving backward, replacing single-piece structures with multipiece assemblies that have to be joined after stamping. Aluminum’s low mass provides weight savings, but material costs and cycle times are higher.
“When people first started asking for aluminum parts, they thought we’d have to do a two-piece assembly,” Hoffmann states. “Using these laser-welded blanks takes another step out of the assembly for the OEMs and Tier 1 suppliers.”
With the industry moving to new materials, Hoffman adds that companies are going to be looking for the technologies that support the precision and speed they’ve achieved in steel. Producers are already moving to more expensive materials. If build times grow as well, lightweighting manufacturing costs could eclipse benefits.
“We make blanks, and we stamp parts, so we’re really aware of both sides,” Hoffman explains. “We’re very conscious of the cycle times and the need to support single-piece assemblies.”
Market opportunity
Developing laser-welding technology for automotive aluminum, before customers request such parts, is a key part of Shiloh’s growth strategy, Hoffmann says. To meet the 2025 Corporate Average Fuel Economy standards of 54.5 mpg, lightweighting has become crucial for every automaker. And Shiloh’s leaders say they believe they’re going to see a flood of parts requests in the near future.
“More of the pickups and SUVs— E-segment vehicles that have full-frame doors—this is where you’re going to get the biggest savings, the biggest bang for your buck,” Hoffman says, adding that he expects most vehicle doors and closures to be constructed from aluminum in the next three years.
The industry has been moving in that direction for several years. Almost all pickup hoods are made of aluminum, as are many trunk lids. Automakers started with those parts because they’re fairly simple, serving mainly as protection against the elements. Door panels are tougher because they need to absorb damage in car crashes.
“The closures are hang-on panels. It does not change the whole body shop,” Hoffman says. Making doors out of aluminum is less costly than switching all exterior body panels to the lightweight metal. “You don’t have to do a complete tear-up like Ford is doing [at its pickup plant in] Dearborn [Michigan].”
Since Shiloh began showing off its test door panels in 2014, Hoffmann says the reaction has been overwhelmingly positive. Automakers want to cut weight from vehicles, but they also want to stick to proven technologies. Suppliers that can adapt familiar processes to new materials are going to be the ones to get a lot of attention.
The author is the editor of Today’s Motor Vehicles, a publication of GIE Media, which also publishes Recycling Today. He can be reached at rschoenberger@gie.net.
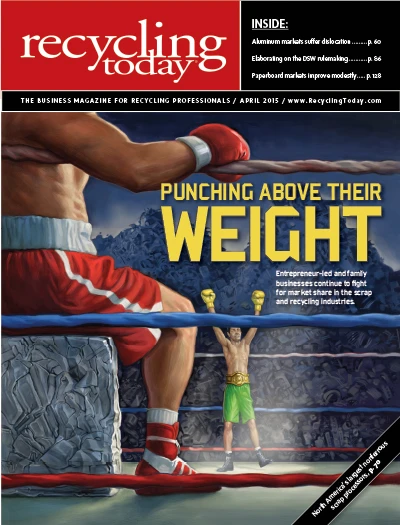
Explore the April 2015 Issue
Check out more from this issue and find your next story to read.
Latest from Recycling Today
- Ferrous price hikes may be poised to pause
- BIR prepares for Spanish exhibition
- Copper exempted from latest round of tariffs
- Interchange Recycling's EPR stewardship plan approved in Yukon
- Making the case for polycoated paper recovery
- Novolex, Pactiv Evergreen finalize merger
- In memoriam: Danny Rifkin
- BIR adds to communications team