Orange, Calif.-based SA Recycling, a joint venture between Adams Steel of California and Sims Metal Management, headquartered in New York City, operates a fleet of 115 trucks. Ron Camp, equipment manager for SA Recycling, says roll-off trucks comprise the majority of the company’s fleet, while tractor trailers account for 15 of the vehicles. These vehicles have an average age of 11 years, he adds.
SA Recycling has 54 sites, though not all of the company’s locations dispatch trucks, Camp says. “If we have two sites that are close to each other, one will have trucks and one will not,” he adds. Among the sites with truck fleets, the number of vehicles varies widely by location, Camp says, with some sites having as many as 12 trucks and others as few as one.
An assist from technology
To keep track of its truck fleet, SA Recycling uses some help from technology, which includes ScrapRunner, Jacksonville, Fla.
According to ScrapRunner’s website, www.scraprunner.com, it is “a complete system” that offers users “automated trip entry, container control, trip and driver management [and] driver mobile data.” The company says ScrapRunner also can interface with customers’ existing accounting systems.
ScrapRunner says it builds upon technology used in Synergy Dispatch, a leading software solution in the LTL (less-than-truckload) trucking industry since the early 1990s.
Camp says a yard’s general manager will schedule trucks using ScrapRunner; however, some SA Recycling yards that operate small fleets may opt for manual scheduling instead.
SA Recycling currently does not use telematics or GPS, he says; however, the company has experimented with this technology and finds it beneficial.
Telematics combines telecommunications and computing to transmit data from a vehicle to a company in real time, enabling the company to track vehicle use, maintenance requirements and servicing. Telematics and GPS also allow users to track driver behavior, alerting a company if a driver has left his or her set geographic area, if a stop took more time than anticipated or if the driver was speeding.
DPL Telematics introduces vehicle tracking system DPL Telematics, a Melo Park, Calif.-based provider of asset monitoring and telemetry technologies, has released the Skyhawk OBDII vehicle tracking system. The Skyhawk OBDII is a solution for wireless monitoring and remote tracking of vehicles designed to increase driver safety and productivity while reducing fleet costs. The GPS unit has no external wiring or antenna and plugs into the existing OBDII port of most vehicles, installing in seconds, DPL says. The Skyhawk OBDII allows managers to wirelessly monitor all their vehicles continually from an Internet-based software package. Using the data, fleet owners can remotely track and receive safety alerts, such as air bag deployments, driving without the seat belt, harsh braking, rapid acceleration, speeding, towing and much more. To determine emission test readiness, the Skyhawk OBDII constantly tracks the 11 vehicle system components required for an emissions test and notifies if any fail to complete their cycle, DPL says. The Skyhawk ODBII also monitors the vehicle’s supported temperatures, pressures and diagnostic fault codes, which are wirelessly transmitted and archived on the software for remote asset diagnosis. All data are accessible from any Internet connected device, DPL says. Additional machine data include fuel level, fuel remaining, mileage driven, engine runtime hours, idling hours and RPM. These production metrics are used to properly assess working time and curb excessive idling, which negatively affect fuel consumption, asset wear, service costs and warranty. The Skyhawk OBDII also is designed to deliver automatic vehicle status and location updates, creating a daily driver log of activity that can be mapped as a “bread crumb trail.” This assists fleet managers with fleet management decisions, DPL says. Customer configured geofence and curfew parameters are standard functionality to reduce theft and unauthorized use of the vehicles. More information is available at www.dpltel.com |
“It works,” Camp says of telematics. The technology provided insight into a number of citations SA Recycling’s drivers were receiving. These citations had to do with grease leaking from the truck, missing mud flaps and the like. With this information, he says, “It was very clear what we had to do” to correct citations.
Telematics also alerted the company when drivers were spending too much time at yards or with customers, Camp says, allowing SA Recycling to address these issues with drivers.
The technology also contributed to fuel savings, he says.
Regarding SA Recycling’s implementation of telematics and GPS technology going forward, Camp says the company is “waiting for the right time.” He says he expects SA Recycling to begin integrating this technology within the next two years.
SA Recycling also uses software to track vehicle maintenance. The company’s program of choice is Bentley’s AssetWise Ivara Performance Management software. Bentley says AssetWise Ivara “supports and drives a business process to improve the reliability, integrity and performance of infrastructure assets throughout their operating life” by helping companies minimize business risk resulting from equipment failure, reduce operating costs, ensure safe and compliant operation, extend the life of the asset and improve its return on investment.
SA Recycling’s office personnel enter the miles and costs associated with the company’s trucks by asset number. Every 10,000 miles a truck logs triggers an inspection, Camp says, which can be performed by one of three technicians who work out of the SA Recycling’s corporate office or by a nearby service center.
These inspections require a truck to be out of service for at least two or three hours, he says, depending on the maintenance required.
Camp says SA Recycling used to have spare trucks in its fleet that could be dispatched when vehicles were out for maintenance. However, SA Recycling discontinued the practice in 2011 with the introduction of California Air Resources Board (CARB) air emissions regulations because many of the aging spares weren’t in compliance with state requirements and it would have been too costly to install DPFs, or diesel particulate filters, on these vehicles to bring them into compliance.
In for maintenance
SA Recycling uses its own maintenance staff as well as outside garages to perform preventive maintenance on its truck fleet. However, the company sends vehicles to outside shops for more involved repair jobs, Camp says. “We don’t rebuild engines, transmissions or rear ends,” he adds. Instead, these bigger jobs are done by a local Kenworth or Peterbilt garage, typically. Camp says this approach is more economical in terms of time and cost.
Regarding preventive maintenance, Camp says such work is always cheaper when performed in-house. The company follows the manufacturer’s suggestions pertaining to scheduled maintenance.
SA Recycling typically spends $3,500 per year for regular preventive maintenance on its roll-off trucks, while maintenance on tractor trailers typically costs $5,000 per year, he says. However, when costs begin to escalate beyond these points, Camp says, he begins to question what is going on with the truck. These higher costs are generally related to clutch and transmission replacement, he says, which is why the company prefers to buy trucks with automatic rather than manual transmissions.
SA Recycling does not encounter much tire damage thanks to the cleanliness of its yards and its customers’ sites, he says. However, a tire may get a hole in the sidewall and need to be replaced. Generally, the company replaces tires at 50,000 miles. “We use recaps on the back and new ones on the front,” Camp says.
On top of things
“You have to stay on top of maintenance,” Camp cautions. He also stresses the importance of getting drivers to enter information on the preoperation and postoperation sheets that reflects the condition of the trucks. “If it needs repair, it needs to be on that sheet,” Camp advises.
Once the driver has noted that the vehicle needs attention, the clerk must then be certain to pass that information on to the general manager or maintenance personnel so that it is addressed.
If companies adhere to this process, “Your trucks will be in pretty good shape,” he says.
Camp adds that listening to drivers is key to addressing vehicle issues. If a driver has been warning management of an issue without management taking action to repair the vehicle, the driver may stop drawing attention to such issues. “What I find is that operators will do that to the point that he thinks he’s not being listened to,” Camp says. “Then he stops trying, and then you have a big problem.”
The author is managing editor of Recycling Today and can be reached at dtoto@gie.net.
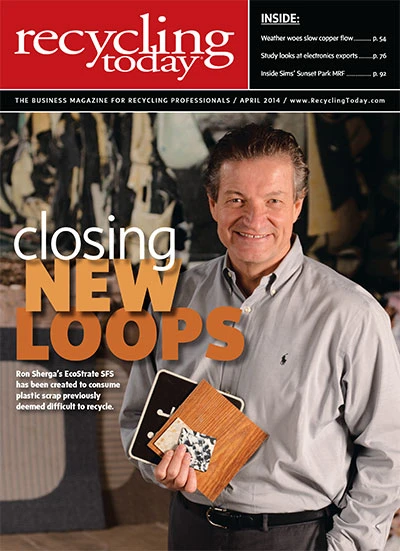
Explore the April 2014 Issue
Check out more from this issue and find your next story to read.
Latest from Recycling Today
- OnePlanet Solar Recycling closes $7M seed financing round
- AMCS launches AMCS Platform Spring 2025 update
- Cyclic Materials to build rare earth recycling facility in Mesa, Arizona
- Ecobat’s Seculene product earns recognition for flame-retardant properties
- IWS’ newest MRF is part of its broader strategy to modernize waste management infrastructure
- PCA reports profitable Q1
- British Steel mill subject of UK government intervention
- NRC seeks speakers for October event