Portable, flexible, time-efficient and more exacting. These are just of few of the themes that seem to be common to many of the latest equipment and new product launches over the past year.
Taking stock of some of the most recent introductions and product innovations, equipment manufacturers seem to be intent on offering products and systems that can offer more utility, either with flexibly designed features, more appropriate capacities or the ability to perform a multitude of tasks with one piece of equipment.
Some of the latest product launches also mirror the changing recycling economy, which today seems more focused on higher quality final products that have been upgraded to new levels.
What follows is a rundown of some of these innovations, released over the past year, and designed to capitalize on the industry’s latest demands and concerns.
Bunting separation conveyors
Bunting Magnetics Co., Newton, Kan., has introduced a new line of high-intensity separation conveyors designed to provide extremely high magnetic fields, enabling removal of lightly magnetic tramp metal fines.
The high-intensity magnetic fields also separate work-hardened 300-series stainless steel from the material stream, increasing separation effectiveness for medical waste as well as for automotive and electronic scrap, Bunting says. The conveyor’s frames are constructed of 300-series stainless steel.
The unit’s urethane belts help to maximize magnetic field exposure to the material being conveyed, Bunting says.
Optional vibratory feeder trays also are available for use with the conveyors.
Visit www.buntingmagnetics.com for more information.
Danieli Centro Recycling deduster
Italy-based Danieli Centro Recycling has installed a new, patented system designed to clean gas and to control volatile organic compound (VOC) emissions at automobile shredding facilities. The solution achieves project targets, with total VOC emissions lower than 5 milligrams (mg) per cubic nanometer (Nm3), according to the equipment supplier.
The shredding facility that commissioned Danieli’s system treats a variety of scrap, including compacted end-of-life vehicles.
Danieli’s technology involves controlling VOCs using a bed of activated carbon and processing the primary air flow from the shredder together with a secondary flow from the air separation equipment installed at the fluff separator. The primary fumes are dedusted with a cyclone and then a wet scrubber, the company says. The secondary flow is prefiltered with a bag filter and heated by an external fuel burner prior to mixing with the primary air flow (from the shredder). Because the temperature of the mixed flow is higher than ambient temperature, condensation in the carbon bed is prevented.
The advantage of this technology, according to Danieli, is that a free flame can be used to heat only the secondary flow of air, which does not contain VOCs. The flow rate of air treated by the activated carbon bed does not increase significantly because the secondary flow is only one fraction (about one-fifth) of the primary flow.
The combination of the lines is economically favorable because only one induced draft fan and one stack instead of two are needed, according to Danieli. Furthermore, the company says this technology allows for the abatement of VOCs where other approaches, such as oxidation or direct treatment of the primary air flow, would not be viable. Visit www.danieli-centro-recycling.com for details.
Eriez Metal Loss Monitor
New from Eriez, Erie, Pa., is the Metal Loss Monitor (MLM), an automatic analytical device designed to help recyclers determine the quantity of metals passing through scrap yard operations unrecovered. According to Eriez, the MLM continually scans the residue stream for metal that has escaped the process and is headed for landfill disposal. It can also alert operations managers remotely via text message when metal has been detected.
Users have the ability to monitor the performance of their systems for variations over time, allowing managers to be alerted to maintenance issues or adjustment requirements, Eriez says.
The MLM can be positioned upstream to provide hand-picking assistance, or downstream to track system or picking performance. Metal that passes the monitor produces an audible signal, and the event is recorded in a data file. An optional ink marker system allows the MLM to alert pickers of locations to search for lost metal.
This device is designed to be installed easily on conveyor belts after separation equipment, where it scans the waste stream to serve as a final or intermediate gauge to monitor and measure metal loss in shredder residue or fluff streams, Eriez says. Metals counts are logged for predetermined time intervals and the information is sent wirelessly to Eriez’s secured remote data portal.
More information is available at http://en-us.eriez.com/products/metallossmonitor.
General Kinematics Para-Mount IV feeders
General Kinematics (GK), Crystal Lake, Ill., has introduced the Para-Mount IV to its line of vibratory feeders. The company says the Para-Mount IV is designed to negate surge loads as well as to improve the presentation of auto shredder residue (ASR) and other mixed materials streams for metals recovery.
The Para-Mount IV high-stroke feeder is engineered for metals recovery and to improve metals separation from nonmetallics, according to GK. The high stroke transmits more energy to the ASR and features a thicker trough with an integral acceleration plate.
The IV uses two-thirds less horsepower than many other vibratory feeders, the company says.
Visit www.generalkinematics.com for more information.
Redwave three-way glass sorting machines
Available from Redwave Systems of Austria are the new CX and CXF sensor-based glass sorting machines, offering two- and three-way sorting technology for recycled glass processing. The sorters can process container and float glass from 2 millimeters (mm) to 50 mm in size for a variety of sorting tasks.
The company says the machines can recognize a variety of glass types that have no distinguishing features in the RGB (red-green-blue) color range. Other benefits include reduced air consumption, a compact design and fewer sorting steps without loss of quality or yield, Redwave says.
For more information, visit www.redwave.at.
Saturn Grizzly Super 80 grinder
Available from Granutech-Saturn Systems, based in Grand Prairie, Texas, is the new Super 80 (S-80) Saturn Grizzly grinder.
The company says the S-80 is designed as a medium-speed, stage-two grinder providing efficient, high performance size reduction of industrial scrap, such as tires, rubber scrap, cable scrap, nonferrous metals, biomass, plastics and e-scrap.
According to Granutech, the S-80 is designed for customers who need to process at higher volumes while making a smaller product. It features a new knife and rotor design, the company adds, that works exceptionally well on tires.
Granutech says the S-80 offers an unprecedented capacity of 10 tons per hour in rubber scrap recycling applications, the greatest production capacity for tire recycling of any product on the market, allowing recyclers to potentially match theirgrinding capacity with their shredding capacity in a single machine.
Mike Hinsey, international vice president for Granutech, says the S-80 features several design and performance enhancements from the company’s original Model 80 Grizzly grinder, including an updated knife design, more power and more torque.
The company says the S-80 Grizzly features a single rotor design and application-configurable screens for exact size reduction. By producing smaller, more consistent material, the Saturn S-80 Grizzly improves the performance of downstream equipment or can replace it entirely, the company says.
Additional features include housing liner plates, a two-piece screen design, easy-opening upper hopper, multiedge reusable knives and service platforms and handrails.
The company says staff members will work with customers to design solutions that meet their exact application and processing requirements.
Visit www.granutech.com for more information.
Sennebogen Equilibrium handlers
Sennebogen of Straubing, Germany, has launched the Equilibrium EQ line of balanced material handling machines. EQ material handlers are built to maintain a constant equilibrium via the classic lever principle, Sennebogen says. As such they are designed to offer the highest level of energy efficiency, with operating and energy cost savings of up to 75 percent compared with conventional drive solutions, the company says. The handler’s low energy consumption also results in low operating costs, the company says.
The material handler can be controlled with just two cylinders, Sennebogen says. A counterweight compensates for the weight of the equipment plus the grab and ensures an effective transmission of force, the company says.
Various models and size ranges are available, and EQ handlers also are available for crawler, rail and stationary applications. EQ models are available with diesel engines and electro-hydraulic drive. The unit may also be able to handle the work of two comparable mobile machines, Sennebogen says.
Visit www.sennebogen.com for more information.
Steinert mobile separation plants
New from Steinert US, Walton, Ky., is a series of mobile processing plants for recycling applications. The Steinert mobile series is designed to provide precise recovery anywhere a power source and fairly level ground can be found, the company says. Included in the lineup is Steinert’s CoarseMaster, FinesMaster, ISS induction system and its NES eddy current systems.
The CoarseMaster is suitable for processing material sized between 0.5 inch and 5 inches and offers a flexible combination for ferrous and nonferrous recovery. The full-scale production unit features a single-stage ferrous preseparator designed with a small footprint and easy maintenance access.
Steinert’s FinesMaster is designed as a complete solution for metal separation of fines material sized between 0.13 inch and 2 inches. This unit features a dual-stage ferrous preseparator, built-in loading station and wide tuning flexibility, the company says.
The Steinert ISS induction system is an all-metal sorter that is offered in several configurations for different applications. The ISS features a built-in compressed air filter and drying system.
Steinert says its NES mobile eddy current is designed as an affordable nonferrous recovery solution, offered in multiple configurations for material sized between 0.13 inch up to 10 inches.
Visit www.steinertus.com for more information.
TSC Portable 6060 Little Rascal shredder system
New from The Shredder Co., Canutillo, Texas, is the portable 6060 Little Rascal top and bottom discharge (TBD) shredder system. The company reports this new shredder offers a tilt table and feed system with 40-degree feed ramp.
The shredder features a single-feed roll with hydraulic drive and PLC (programmable logic controller) Smart Shredder System (SSS), casting design and rotor design. The 6060 Little Rascal also includes a ferrous separation system.
Shredder drives for the portable 6060 are offered in sizes from 500 horsepower to 2,000 horsepower with capacities of 10 tons per hour to 60 tons per hour.
The Little Rascal 6060 is completely portable and designed for trailer transport, according to The Shredder Co.
Visit www.theshredderco.com for more information.
UNTHA Assay Shredder
UNTHA Shredding Technology America Inc., Hampton, N.H., has released the RS Series assay shredder to its line of shredding equipment. The assay shredder has been designed and built with electronics recycling and smelting businesses in mind.
UNTHA Shredding Technology America is a division of Austria-based UNTHA Shredding Technology GmbH.
The company says the RS Series assay shredder is optimized for use within the electronic scrap industry, such as by companies that extract and refine precious metals such as gold, silver, platinum and nickel from used circuit boards.
“The assay shredder is useful to companies on both sides of the equation,” says Charles Hildebrand, UNTHA regional sales manager. “It aids companies selling electronic scrap, allowing them to determine in advance the worth of the material they are selling. And, it is a resource for companies buying electronic scrap, letting them accurately measure the amount of precious metals in a batch of materials.”
Hildebrand says the RS Assay Shredder can shred electronic scrap to a size of 10 millimeters, helping recyclers ascertain the value available in a particular shipment. UNTHA says the RS shredder is hardened to this application, with extra durability built into essential areas to minimize downtime.
UNTHA also says its RS assay shredder offers high reliability and low dust generation.
Visit www.untha-america.com for more information.
U.S. Shredder 6060 nonferrous shredder
U.S. Shredder and Castings Group, Trussville, Ala., has introduced the 6060, a new heavy-duty nonferrous shredder.
U.S. Shredder says the 6060 is designed specifically to liberate nonferrous metals to enable maximum recovery from eddy current systems and other nonferrous separation technologies.
The shredder has been designed to process 25 tons per hour using a 1,000-horsepower DC drive. The shredder also features a unique three-anvil design and round grate holes designed to provide optimal separation and a uniformed shredded product, according to U.S. Shredder.
The company says processors have been looking for a nonferrous metal shredder that can hold up to heavier infeed material than lighter hammermill shredders can withstand. However, low-speed, high-torque shredders would simply rip the material, U.S. Shredder says, leaving much of the nonferrous metals still attached and not ready for separation by the eddy current separator.
Information is available from Chris Melenick at chris@usshredder.com.
Zimmer America STF-LS label scraper
Zimmer America Corp., Cowpens, S.C., has introduced the STF-LS label scraper, which is manufactured by STF Group of Germany. The label scraper is designed to provide dry removal of labels from PET (polyethylene terephthalate) postconsumer bottles.
Zimmer America says the STF-LS provides 95 percent removal of labels and full-body sleeves from PET bottles with minimal damage to bottles and without the loss of necks and caps.
The device is equipped with hardened knife tips that are adjustable for different bottle sizes and throughputs, according to Zimmer America. The company also says the knife tips are durable and provide long wear life between changes.
Label and film pieces can be separated using a ballistic separator or simple suction device for 100 percent recovery, according to the company.
Visit www.zimmer-usa.com for more information.
The author is a managing editor with the Recycling Today Media Group and can be reached via email at lmckenna@gie.net.
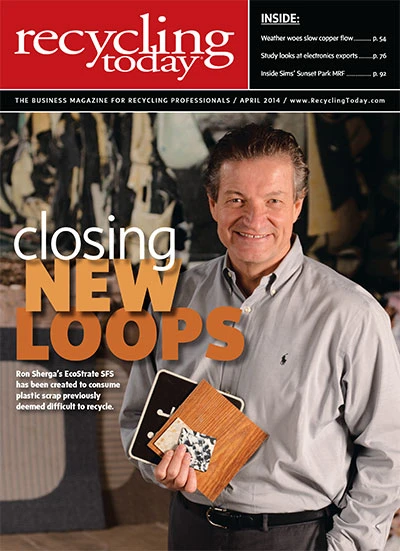
Explore the April 2014 Issue
Check out more from this issue and find your next story to read.
Latest from Recycling Today
- Lautenbach Recycling names business development manager
- Sebright Products partners with German waste management equipment company
- WasteExpo transitions to biennial format for enhanced experiences
- Study highlights progress, challenges in meeting PCR goals for packaging
- Washington legislature passes EPR bill
- PureCycle makes progress on use of PureFive resin in film trials
- New copper alloy achieves unprecedented high-temperature performance
- Gränges boosts profits and sales volume in Q1 2025