Eriez offers fast shipment for 32 feeder models
Eriez, based in Erie, Pa., has introduced the Feeders Fast service as part of its popular EriezXpress quick-ship program.
Through the program, the company offers 32 Eriez feeder models with stock components for shipment within five days from order date for customers with approved credit.
With available tray sizes beginning at 80 square inches and ranging up to 504 square inches and capacities as high as 22 tons per hour, Eriez says its Feeders Fast models can satisfy practically any application requirement, whether large or small.
Feeder models in the Feeders Fast program include a variety of the company’s Model A, Model C, Model HS (hi-speed) and Model HD (high deflection) feeders. Additional vibratory feeders and bin vibrators also are available through the EriezXpress program.
“We developed EriezXpress to streamline the order-to-shipment process by simplifying product ordering, modifying inventory control and designating a dedicated team to make it all happen,” explains Charlie Ingram, vice president of sales and marketing. “When you are facing unexpected product purity, controlling or conveying problems and you need a solution now, EriezXpress is the answer.”
More information on the EriezXpress five-day Feeders Fast program is available on the web at www.eriez.com/products/index/feedersfast.
More information about EriezXpress and the many Eriez stock products offered for quick shipment is available at www.eriez.com/products/index/eriezxpress.
Eriez manufactures a number of separation technologies, including magnetic lift and separation, metal detection, materials feeding, screening, conveying and controlling equipment, suitable for the process, metalworking, packaging, plastics, rubber, recycling, mining, aggregate and textile industries.
SEDA USA celebrates 30 years
SEDA USA, a manufacturer of vehicle depollution equipment for the auto recycling and scrap processing industry, celebrates its 30th year in business in 2014.
Parent company SEDA was founded by Josef Dagn in Austria in 1967. Since then Dagn and his team have grown the SEDA brand to include companies in the U.S., China, Japan, Holland, Austria and Turkey, as well as partner distributors throughout the world, including Australia, Great Britain, France, Germany, Italy and Canada, to name a few.
From the first gas tank drill to the new American-made Patriot, SEDA says it always has focused on quality, efficiency and safety as the backbone of its products.
SEDA USA was originally based in New York. Two years after its founding, the company headquarters were moved to St. Petersburg, Fla. In 2009, SEDA USA relocated to its current location in Fayetteville, Ga., a suburb of Atlanta, where the U.S. corporate hub includes a 3,000-square-foot showroom for in-house product training and demonstration, a 5,000-square-foot maintenance and production warehouse and 2,500 square feet of office space.
In recent years SEDA USA introduced the U.S.-made Mobile Drainage Station, designed to be one of the most affordable and highest quality drainage systems available, according to the company. This year SEDA USA also began working on fire prevention solutions and has introduced its F-500 Encapsulator Agent, which can absorb six to 10 times more heat energy than plain water, the company says.
More information on SEDA products is available at www.SEDA-USA.com.
Rumpke installs ClearSpan protective structure
ClearSpan Fabric Structures, headquartered in South Windsor, Conn., has provided a fabric structure for Rumpke Consolidated Cos. in Cincinnati.
The Hercules truss arch building measures 120 feet wide by 60 feet long and was selected to keep recyclables clean and dry. The structure was installed by ClearSpan’s installation team in a week and a half, the company says, thereby keeping Rumpke’s operations running smoothly.
Rumpke says the 7,200 square-foot structure also is serving additional roles resulting from its ease of installation and ability to be disassembled and relocated.
“We knew at the time of purchase it would need to serve other functions [for recycled glass and heavy equipment storage],” Rumpke engineer Dave Murphy says. “Overall, we are very happy with ClearSpan. The building is performing very well,” he adds.
ClearSpan provides design-build solutions for material, equipment and other storage needs. The buildings are designed to feature abundant natural light and spacious interiors without internal support posts, ClearSpan says. With minimal foundation requirements, the structures can be permanent or temporary and are easy to relocate. The U.S.-made structures can be built to any length, ClearSpan says, and up to 300 feet wide. More information is available at www.ClearSpan.com/ADRT.
VDRS supplies Sims with Bollegraaf system for New York City MRF
Sims Metal Management officially opened its new material recovery facility (MRF) serving New York City in December 2013. The Bollegraaf processing system for the Sunset Park MRF in Brooklyn, N.Y., was supplied by Van Dyk Recycling Solutions (VDRS), Stamford, Conn., and sorts all of the curbside residential rigid plastics, metal, aluminum and glass collected from all five city boroughs.
Sims’ Bollegraaf system is capable of processing 1,000 tons per day of bottles and cans and features 16 of the newest Autosort models of optical sorters from TITECH. The Autosort 4 models, introduced in 2013, eliminate the lamps used on the Autosort 3 models and introduce Flying Beam technology. They will identify and sort 12 different marketable products for the city, according to a press release from VDRS.
All material is debagged and the plastic film and paper are removed using ballistic separators and separated by five TITECH optical sorters into clean end products, the equipment supplier says.
The Sunset Park MRF will assist the city in reaching its goal of diverting 30 percent of the city’s waste from landfills.
VDRS is the exclusive distributor of Bollegraaf, Lubo and TITECH machinery in North America, with more than 2,400 installations.
Vortex to distribute Green Car Depollution System
Vortex De-pollution and Recycling Equipment, based in Denver, has been named the official North American distributor of the Green Car De-pollution System.
Green Car Depollution Systems for automotive fluid recovery use a patented drill design offered in either a standard body or a sight-glass version for fuel quality control. The company says the product is machined by a manufacturer of aerospace components and that the device components are manufactured to provide a high level of precision and to help prevent drill breakdowns.
With this arrangement, Vortex says it is the only company to offer both punch and drill vehicle depollution systems.
“Everyone in the vehicle processing business has an idea of the system they prefer for depolluting a vehicle at its recycling stage,” says Nigel Dove, CEO of Vortex. “For the first time ever, our customers now have the freedom to choose the system they prefer and can mix and match elements of the Vortex and Green Car Depollution systems. We are the only company in the world to offer them both drill and punch solutions.”
Julian Dale, manufacturer of Green Car products, says, “Vortex’s reputation for building robust equipment designed specifically for American vehicles fits well with our new gas tank drill design, which is also specifically designed for the U.S. market.”
Dale refers to the sight-glass option offered in the new drill head, which allows the operator to determine fuel quality before pumping the fuel into the proper storage tank.
Willem Geyer, U.S. president of Vortex, says, “Green Car equipment is built to a higher engineering tolerance than competing drill systems. With increased performance and reduced maintenance costs, we agree with Green Cars’ existing customers that it is the best drill system on the market.”
Geyer continues, “By increasing the choice and quality, with interchangeability of drill products and all of our growing range of metal processing equipment, Vortex is fast becoming the ‘go-to’ supplier for vehicle processing and metal recycling across North America.”
Hardface introduces tire shredding knives
Hardface Technologies, a Cleveland-based business unit of Postle Industries, has introduced a new knife that the company says will be “the ultimate hardfacing wire for tire shredding knives.”
The company says its Postalloy Ultra-Shred 580 is a metal-cored, gas-shielded wire with numerous tightly packed carbides for excellent abrasion resistance under high impact. One-layer deposits exhibit wear characteristics that would be expected from a chromium carbide hardfacing product.
Hardface says the knife’s alloy properties create a resistant cutting edge, even under the high heat conditions created by extreme friction. Deposits are slag-free and exhibit a hardness of 55-58 Rc on the Rockwell scale.
“Postalloy Ultra-Shred 580 has proven to be an exceptional way to hardface tire shredding knives,” says Russ Speese, Hardface Technologies vice president of sales and marketing. “Beyond that application, the product has also seen great success in other areas, including cutting tools, shear blades and hot or cold trim dies.”
Hardface Technologies manufactures a range of what it calls wear-resistant solutions for applications in a variety of industries. The company’s hardfacing products, which it says have been engineered specifically for high-wear environments, are available through Hardface Technologies’ worldwide distribution network.
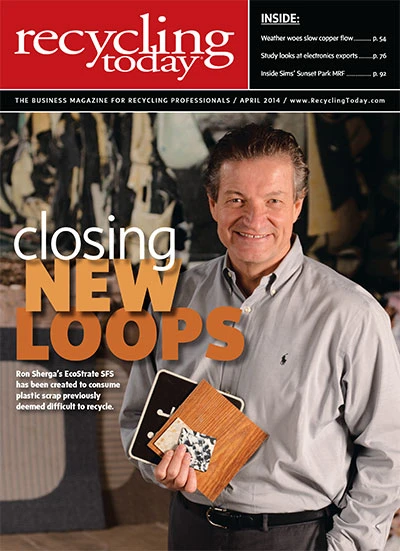
Explore the April 2014 Issue
Check out more from this issue and find your next story to read.
Latest from Recycling Today
- Lautenbach Recycling names business development manager
- Sebright Products partners with German waste management equipment company
- WasteExpo transitions to biennial format for enhanced experiences
- Study highlights progress, challenges in meeting PCR goals for packaging
- Washington legislature passes EPR bill
- PureCycle makes progress on use of PureFive resin in film trials
- New copper alloy achieves unprecedented high-temperature performance
- Gränges boosts profits and sales volume in Q1 2025