NONFERROUS
Kaiser Aluminum, Boeing form aluminum recycling program
Kaiser Aluminum Corp., headquartered in Foothill Ranch, Calif., and the aerospace firm Boeing, headquartered in Chicago, have formed a closed-loop recycling program that is expected to capture 22 million pounds of aluminum during the 2014-2015 production period, the companies say.
John Byrne, vice president of Boeing Aircraft Materials and Structures, says, “Boeing is focused on reducing the environmental footprint of commercial aviation through the aircraft’s life cycle, which includes working with suppliers to increase materials recyclability and reduce manufacturing waste.
“Our collaboration with Kaiser Aluminum to capture 22 million pounds of aluminum alloy scrap for reuse in our aircraft production is a significant opportunity to make progress toward this important goal.”
Kaiser, which produces semifabricated specialty aluminum products at a dozen plants in North America, says the program captures 7XXX and 2XXX aluminum alloy scrap generated at multiple Boeing plants during production of commercial aircraft. The scrap will be used to produce aerospace sheet and plate at Kaiser’s Trentwood plant in Spokane, Wash.
Kaiser says its North American operations produce and ship more than 500 million pounds of product annually. The company also has a 49 percent ownership interest in Anglesey Aluminum, which owns and operates a secondary remelt and casting plant in Wales.
“The recycling agreement illustrates our collaborative relationship with Boeing,” says Jack Hockema, Kaiser president, CEO and chairman. “We look forward to continuing to develop opportunities with our customers to enhance the efficiency of the overall value stream.”
LEGISLATION & REGULATIONS
Recycling Reinvented releases American EPR study
Recycling Reinvented, Shoreview, Minn., has released the full results of a study on an American-designed extended producer responsibility (EPR) recycling model. The results demonstrate that EPR for packaging and printed paper (PPP) can significantly increase stagnant recycling rates for packaging at similar costs to current methods and be financed directly by industry with limited impacts, according to Recycling Reinvented.
Recycling Reinvented contracted with Reclay StewardEdge Inc. on the project.
The study analyzes a proposed model of EPR for PPP that is administered and managed by industry producers and implemented at the state level. The full scope of the study lays out the definitions for the proposed system, analyzes the potential benefits and expenses of such a system and determines the potential fees on packaging types to finance the system.
Full study results and other documents can be found on the websites http://marketbasedrecycling.com and http://Recycling-Reinvented.org.
“We set out to give industry leaders, policymakers and advocates the real data and analysis they need to make informed decisions on an EPR system designed for American markets,” says Paul Gardner, executive director for Recycling Reinvented and a former state legislator. “We’ve achieved that purpose, and the result is a truly positive story.”
Previously released results demonstrated that the proposed EPR model is likely to increase recycling rates with costs similar to the current system, according to Recycling Reinvented. In the final study report, one of the most important findings for stakeholders has to do with the fees that would be assessed on packaging materials to finance the system. Results show that across most materials, fees on producers would be fractions of a penny per unit. In the case of products with high postconsumer value and well-developed markets, producers may even receive credits, the nonprofit says.
When compared with other systems designed to increase recycling rates, according to Recycling Reinvented, the study demonstrates that EPR will provide similar results for more materials at significantly less cost to producers.
The study was reviewed by more than two dozen recycling experts at three major stages throughout the process, the nonprofit says. Reviewers’ comments influenced the design of the EPR model, the findings on projected outcomes and expenses and the fees assessed to producers on each packaging material. Throughout the study, working papers have been available for public comment in an effort for the process to be collaborative and transparent, Recycling Reinvented says.
“As the largest producer of bottled water in North America, we feel strongly about issues affecting packaging and we see the coming impacts of commodity shortages of postconsumer recycled materials,” says Brian Flaherty of Nestlé Waters North America. “We are pleased that Recycling Reinvented encouraged participation of a broad list of stakeholders in this study and stayed true to their mission to establish a factual baseline for American EPR.”
Recycling Reinvented promotes increasing recycling rates of waste packaging and printed material in the United States through an EPR model.
Reclay StewardEdge is based in Toronto with offices in Manitoba and Florida. The company provides consulting and program management services related to product stewardship on behalf of clients in North America and internationally.
METALS
Aleris acquires Nichols Aluminum
Cleveland-based secondary aluminum producer Aleris International Inc. has announced that it has signed a definitive agreement to acquire Nichols Aluminum LLC, a wholly owned subsidiary of Quanex Building Products Corp., Houston, for $110 million in an all-cash transaction.
Nichols produces aluminum sheet for a range of North American industries, including transportation, building and construction, machinery and equipment, consumer durables and electrical. The acquisition includes two production facilities in Davenport, Iowa, a facility in Decatur, Ala., and one in Lincolnshire, Ill.
Nichols uses aluminum scrap in its reverberatory furnaces and touts the high recycled content of its aluminum 3105 and 3004A alloy products. The company also is a member of the Institute of Scrap Recycling Industries Inc. (ISRI), Washington, D.C.
“Nichols has a long history of producing flat-rolled aluminum sheet products for customers in a number of key industries across North America, and we look forward to continuing that long-standing tradition,” says Steve Demetriou, Aleris chairman and CEO. “This acquisition is consistent with our strategy to expand our footprint and enhance our capabilities to ensure we are well-positioned to respond to projected growth in our key end uses as the economy begins to recover.”
Bill Griffiths, Quanex chairman, president and CEO, says, “As the housing markets continue to recover, we see great opportunity for both organic and acquisitive growth in our Engineered Products Group. This transaction will allow us to focus all our energies and capital on enhancing our position as a leading window and door component supplier both domestically and internationally. Aleris will provide an excellent home for Nichols as it continues to grow its aluminum presence globally.”
PLASTICS
Resource-One to open new facility
Resource-One, a recycling and waste management firm based in Cincinnati, has announced plans to open its newest facility in Covington, Ohio. Resource-One can handle a range of recyclable materials, including plastics, paper, hazardous waste and other materials.
In addition to its Cincinnati location and the new facility in Covington, Resource-One operates a facility in Bellfontaine, Ohio.
Todd Hormann, Resource-One chief operating officer, says the new location has been designed to serve one customer: American Honda Motor Co. Resource-One’s Covington facility will handle plastic auto parts and metal auto parts generated through American Honda throughout the country, he says. The company says it expects to open the facility by early spring. Resource-One is in the process of updating the facility by installing new equipment, including roll-off containers and security equipment.
The company’s new Covington facility measures roughly 50,000 square feet; its Bellefontaine facility is approximately 20,000 square feet.
ELECTRONICS / LEGISLATION & REGULATIONS
US House-passed legislation discourages cellphone recycling and refurbishment, ISRI warns
The Institute of Scrap Recycling Industries (ISRI), Washington, D.C., has cautioned against the unintended consequences limiting the recycling and refurbishment of cellphones if the Unlocking Consumer Choice and Wireless Competition Act (H.R. 1123), passed in late February in the U.S. House of Representatives, becomes law. While the bill provides the benefit of consumers being able to unlock cellphones without permission from carriers, it makes it illegal for recyclers and refurbishers to unlock cellphones in bulk, ISRI says.
“The recycling industry applauds the effort of H.R. 1123 to give consumers the freedom to unlock their cellphones but is concerned the side effects could be harmful to the economic and environmental benefits of recycling,” ISRI President Robin Wiener says. “By not allowing unlocking phones in bulk, recyclers and refurbishers are placed in a competitive disadvantage and may be forced to outsource the repair jobs to facilities outside of the United States where unlocking is legal.”
Last October, the ISRI board of directors approved a cellphone unlocking policy that called for allowing consumers, including recyclers and refurbishers, the right to lawfully unlock technological devices. By allowing bulk unlocking, recyclers and refurbishers are able to put valuable and working devices back into the domestic and global marketplace where there is a strong demand, ISRI says.
“Unfortunately, rather than allowing refurbishers and recyclers the same right as consumers to unlock phones that they own, this legislation confuses the market and creates an impediment for the proper repair and reuse of such phones,” Wiener says. “It is our hope that the Senate addresses this oversight when it takes up the legislation.”
METALS
Upstate Shredding to expand New York port facility
The Albany Port District Commission has voted unanimously in favor of allowing Ben Weitsman of Albany LLC to purchase additional land at its facility at New York’s Port of Albany.
The new 12-acre site is on the same road as Ben Weitsman of Albany’s current 18-acre retail scrap yard and port facility, which opened in August 2013.
“We are very pleased with the decision in our favor by the Albany Port District Commission,” says Adam Weitsman, owner of Upstate Shredding – Ben Weitsman, based in Owego, N.Y. “We love being in the capital district and look forward to continuing to grow, add jobs and help those within the community.”
According to Upstate Shredding, several companies bid on the facility, previously home to Hudson River Recycling/Sims, including the recycling companies Rensselaer Iron and Steel Inc. and Materials Recovery Co.
Weitsman says the new site will enable the current Ben Weitsman yard to expand its operations and provide additional space for the installation of a new auto shredder and full downstream sorting system, which are currently under construction.
“The new shredder will be operational in April of [2014], and it couldn’t come at a better time as we continue to acquire new yards and expand our footprint in the region. Our Albany location continues to grow in customers and scrap volume, so having the extra space fits in very well with our current plan for new acquisitions,” Weitsman adds.
Upstate Shredding – Ben Weitsman acquired the assets of Capitol Scrap Metal Co., a family-owned and operated yard, early in 2014. The company merged the operations of Capitol Scrap, located near the current Ben Weitsman retail scrap yard in Albany, to create its Port of Albany facility.
In other news, Upstate Shredding recently acquired the assets of Brant Auto Parts, Irving, N.Y.
Brant Auto Parts, founded in 2003, has been serving Buffalo, Hamburg and Dunkirk, N.Y., and the surrounding areas for more than 10 years.
“This location is perfect for our western expansion plans as we continue to build out our footprint and acquire yards that are strategically located in the Northeast,” Weitsman says.
PLASTICS
GDB opens new building
GDB International, a New Jersey-based recycler of paper, plastics, metal and paint, has recently opened a building in South Brunswick, N.J., that is designed to allow the company to boost the volume of recyclables it can handle. (GDB was profiled in the January 2012 issue of Recycling Today.) The new plant is less than 10 miles from the company’s main facility.
Howard Schamach, senior vice president of GDB, says the company will move its plastics recycling operations to the new location while its other facility will handle paper and metals.
“We are looking to grow our business, and we felt opening a new building would give us the space we needed. It also allowed us to split up our operations,” Schamach says.
GDB has purchased an American Baler two-ram baler and a Hustler Conveyor line for the new plant. Schamach says he expects the equipment to be installed by the end of March 2014.
ELECTRONICS
Number of R2 certified companies passes 500
Boulder, Colo.-based R2 Solutions has announced that a total of 508 electronics recycling companies have been certified to the Responsible Recycling Practices (R2) standard as of mid-February.
R2 Solutions is the governing body that administers the R2 certification program, which is designed to certify that electronics recycling and refurbishing facilities conform to the R2 Standard, which is based on best practices in environmental health and worker safety, data security and applicable laws.
The updated R2:2013 standard emphasizes repair and reuse, record keeping and reporting and data security, among other things, R2 Solutions says.
Of the 508 facilities certified, many are seeking certification under R2:2013, with the first facility, XTechnology Global, Danvers, Mass., successfully certified in January 2014, R2 Solutions says.
In the year ahead, all R2:2008 certified facilities will need to recertify to the R2:2013 standard, the group says.
Henry Leineweber, R2 Solutions program director, says, “R2 certified facilities are now present in 14 countries, and we expect this number to grow significantly this year.”
PLASTICS
Cereplast files for bankruptcy protection
Manufacturer of compostable bioplastics Cereplast Inc., Seymour, Ind., has filed for Chapter 11 bankruptcy protection in the U.S. Bankruptcy Court for the Southern District of Indiana. The company says it has taken this action to strengthen its balance sheet, cleanup its capitalization structure and gain financial flexibility as it looks to realign its operations.
“We intend to use the reorganization process to help implement our plan to lower costs, stabilize our businesses, grow revenue and diversify our product lines,” says CEO Frederic Scheer.
He continues, “We have taken a number of steps to improve our operations over the past few months, and we were making great progress; however, the lack of traction of bioplastics demand in the United States, the repetitive delays in implementation of the bioplastic regulation in Europe and especially in Italy combined with the legal problems created by several of our lenders made clear to our board that reorganization was the proper path forward.”
Sheer says Cereplast employees will be affected during the transition period as staff will be trimmed.
Cereplast also is negotiating debtor-in-possession financing.
METALS
Scrap metal recycler clears hurdle in Chicago
The city of Chicago’s Zoning Board of Appeals has voted in favor of a special-use permit that will allow Pure Metal Recycling to go forward with the installation of an auto shredder in the Pilsen area of the city. The board approved the permit in a 3-0 vote. Two of the board’s five members were not in attendance.
According to local press reports, the company was looking for a special-use permit to build a $30 million scrap metal and shredding operation on 15 acres in the city.
Following the approval of the land-use permit, Pure Metal Recycling must obtain a construction permit from the city before it can begin construction on the shredder.
Chicago is currently home to three operating automobile shredders: two that are operated by Sims Metal Management, based in New York, and one operated by General Iron Industries, headquartered in Chicago.
INDUSTRIAL
Sonoco facility hits recycling target
Sonoco Recycling LLC says the Sonoco Display and Packaging plant in Rural Hall, N.C., has diverted more than 99 percent of its waste from landfills.
In September 2011, employees at the company’s Rural Hall fulfillment facility formed Team Green to focus on achieving landfill-free status in two years.
Sonoco says one of the major challenges was not only staying on top of the fluctuating material mix but also determining the best outlet for each new recyclable material encountered. The team began its recycling program by reviewing, monitoring and restricting access to waste bins. Common recycling areas were set up in production and office areas and employees were encouraged to bring in their recyclables from home. Once this was accomplished, processes and procedures were put into place to help collect, distribute and assess new recyclables as they were encountered.
“In just two years, Team Green was able to divert over 99 percent of Rural Hall’s waste through a mix of recycling, reuse and waste to energy,” says Rodger Fuller, Sonoco group vice president, Paper and Industrial Converted, North America. “They’ve shown great initiative in achieving landfill-free status.”
Created to recognize customer and Sonoco facilities for achieving significant milestones in landfill diversion and waste stream reduction, the Sustainability Star Award program is composed of three tiers:
- Gold Star Awards, which recognize facilities that have achieved 99 percent landfill diversion;
- Silver Star Recognition, which is awarded to facilities achieving 95 percent landfill diversion; and
- Bronze Awards, which recognize facilities that have made significant waste reduction achievements.
Sonoco Recycling, Hartsville, S.C., operates five material recovery facilities (MRFs) and serves nearly 150 communities in which curbside collected residential and commercial materials are processed. The company also provides recycling programs that identify waste reduction opportunities that reduce operating expenses for many of the largest consumer product companies in the United States.
ELECTRONICS
Securis awards franchises serving Maryland and Delaware
Securis Franchising Inc., headquartered in Chantilly, Va., has announced that it has awarded its first three franchises in the Mid-Atlantic region. Securis says its franchising strategy is part of the company’s national expansion to serve growing demand for electronics recycling and data destruction services, a market that is estimated at between $6 billion to $9 billion globally, according to reports by IDC and Transparent Research.
Awards include counties in the Maryland suburbs outside of Washington, D.C., as well as the state of Delaware, with service in these territories slated to begin by summer of 2014. Numerous additional protected territories are available in Pennsylvania; New Jersey; Washington, D.C.; and North Carolina, with more expected to be released in 2014 and beyond, the company says.
“From the moment we launched the Securis franchise concept in spring 2013, we’ve seen intense interest from hundreds of aspiring business owners who recognize the unique opportunity,” Securis CEO and founder Jeremy Farber says. “After meeting with dozens of prospects, we are very excited to have selected our first three franchisees and look forward to awarding additional territories in 2014.”
Farber adds, “Securis’ clients, including organizations in the federal government, financial services, health care and government contracting sectors, demand world-class data security and environmental stewardship that is delivered consistently across all of their locations. Our franchise expansion helps us put our operations closer to these customer locations so we can better serve them.”
Those interested in learning more about Securis franchise opportunities can visit www.securisfranchise.com/2014.
Originally founded as PC Recycler in 2000 and based in the Washington, D.C.-metro area, Securis is an industry-leading provider of information technology asset disposal (ITAD), including electronics recycling, auditing, hard drive shredding and other data destruction services for PCs, laptops, mobile phones, servers, monitors, copiers, printers and other data storage devices and electronic scrap. In 2012 and 2013, the company was named to the Inc. 500/5000 list as one of the fastest growing private companies in the United States.
Securis has earned an R2 (Responsible Recycling) certification, which is designed to ensure the company uses practices that protect the environment, human health and safety and the security of the recycling process. Additionally, Securis is approved by the U.S. General Services Administration (GSA) and certified by National Association for Information Destruction (NAID), Phoenix, as well as the U.S. Defense Logistics Agency (DLA) Logistics Information Service.
METALS
Metallix receives regional award
Precious metals refining company Metallix Refining Inc., based in Shrewsbury, N.J., has been selected as Industry of the Year for 2013-2014 by Pitt County, N.C.
Each year the Pitt County Development Commission requests nominations from county citizens to recognize a manufacturer or distributor best representing the community as a model corporate citizen in specific selection criteria, including social, economic and environmental sustainability.
Metallix purchased an 85,000-square-foot facility in Greenville, N.C., in 2004. In 2010, Metallix opened a facility in the state to recycle smaller lots of high-grade precious metals with the establishment of Metallix Direct Gold LLC. Additionally, Metallix opened a new facility in 2013 that specializes in purchasing scrap catalytic converters from automobiles.
PLASTICS
Dart Container launches new website
The plastics packaging firm Dart Container Corp., Mason, Mich., has launched a new website, www.HomeforFoam.com, which has been designed to educate businesses, city governments and schools about how polystyrene foam No. 6 can be recycled. The website provides a list of markets for the material, a list of the environmental and economic benefits to recycling foam and a list of locations that accept foam plastic for recycling purposes.
Dart Container adds that city governments and businesses can download sample press releases, social media posts and other features to promote their foam recycling programs. The website also provides educators with free recycling lesson plan ideas, intercom announcements as well as other informational tools.
Foam recyclers can find markets through the company’s website by connecting with brokers and reclaimers who resell or use the material to manufacture new products, such as picture frames and crown molding.
“Dart has been recycling postconsumer foam cups, containers and packaging since 1990, and we are excited to share some of our knowledge by assembling a website dedicated to advancing foam recycling,” says Michael Westerfield, corporate director of recycling programs at Dart. “This site is a one-stop shop for those wishing to learn how to implement their own program,” he adds.
Dart says HomeforFoam.com aims to promote the growth of all foam No. 6 recycling, including medical coolers, egg cartons, ice chests foam used to package electronics as well as other products.
ELECTRONICS
Research points to ongoing M&A activity in electronics recycling sector
The Miami-based research group Compliance Standards has released a report that addresses the changing landscape of the electronics recycling industry. The report, titled “The ITAD and Electronic Recycling Competitive Landscape: The Momentary Vanishing of the Pure-Play ITAD Companies,” forecasts that the electronics recycling and IT sectors are in the middle of a mergers and acquisitions (M&A) wave. The M&A push will be driven by large corporations and investors looking to take advantage of expected solid growth prospects in the broad environmental sector, Compliance Standards says.
The report says small, independent firms that are active in the market are being acquired, leaving a vacuum in the space. This move is creating longer-term potential for mergers among smaller entities that will remain active in the market and will seek to be competitive.
“Despite investor interest in the ITAD (IT asset disposition) and e-cycling companies, ongoing challenges are the same we’ve seen in the recent past, including the need to aggregate aging and soon-to-be obsolete assets for decommissioning purposes in manners that make economic sense,” says Alec Gordon, an analyst with Compliance Standards overseeing M&A activity.
“Our report looks at the most active companies on the M&A front, what they are looking for, and profiles those involved in electronics recycling and ITAD,” says David Daoud, managing director and principal analyst at Compliance Standards.
The report segments the types of companies looking at a competitive position for long-term growth, from OEMs (original equipment manufacturers) to distributors and retailers and from reverse logistics firms to contract manufacturers. Non-IT firms vary from freight and transportation companies to waste collection firms.
More information on the report is available at http://compliancestandards.com.
ELECTRONICS
E-Waste Systems holds grand opening
Electronics recycler E-Waste Systems Inc. (EWSI), with corporate offices in London, Shanghai and Cincinnati, has officially opened its new Cincinnati reverse logistics and electronics recycling facility.
“We are pleased to announce the opening of our new facility in Cincinnati and the grand opening on the 20th of March,” says Martin Nielson, founder and CEO of EWSI.
“This facility is strategically located in the logistics golden triangle of the eastern U.S. and will combine to offer all the services available under our brand,” he adds.
EWSI says the facility has the capacity to process as much as 75 million pounds of e-scrap per year. The new building will serve as the headquarters of the operating unit EWSI Cincinnati, which will provide oversight of a recently acquired facility in New York state.
The company says its Cincinnati unit will become a strategic operational hub and will provide the basis for further expansion in the Northeast.
Nielson adds, “In late 2013 EWSI Cincinnati acquired equipment for operations in Ohio and New York, and this is the next step in the implementation of that transaction. Our teams in both locations are doing a great job. This facility is a very important part of our eastern U.S. operations.”
The Cincinnati plant measures more than 50,000 square feet and can be expanded as demand increases, EWSI says. All of the recently acquired assets, including the shredding and separation and CRT (cathode ray tube) processing lines, are being installed at the Cincinnati facility. Simultaneously, the asset recovery, data destruction and repair and refurbishment functionality, much of which was acquired with the 2013 acquisition in California, also is being installed in Cincinnati.
“The facility itself boasts some of the most advanced processing techniques in the industry and combines all of EWSI technologies under one roof, and we are already seeing a profound improvement in our capabilities, functionality and efficiencies,” Nielson says.
“Our new location opens extensive business opportunities and enables us to provide the region with a comprehensive solution to a global problem,” says Julie Peterson, president of EWSI Cincinnati.
PLASTICS
Wegmans joins How2Recycle Label program
Wegmans, with more than 80 stores in the eastern United States, has become the first grocer to join the Sustainable Packaging Coalition’s How2Recycle Label program. With the addition of Wegmans, the How2Recycle Label has surpassed its 2013 goal of 20 participating companies, according to GreenBlue, Charlottesville, Va.
The How2Recycle Label began in 2008 and is a project of GreenBlue’s Sustainable Packaging Coalition. The goal of the group is to have the majority of consumer goods packaging being a part of the program by 2016. The goals of the How2Recycle Label were developed through open discussion with numerous stakeholders and relate to the ultimate vision of a system where packaging materials are beneficially recovered. The goals include:
- reducing confusion by creating a clear, well-understood and nationally harmonized label that enables industry to convey to consumers how to recycle a package;
- improving reliability, completeness and transparency of recyclability claims;
- providing a labeling system that follows Federal Trade Commission Green Guides; and
- increasing the availability and quality of recycled material.
Wegmans is the fifth How2Recycle participant and first retailer to receive a sponsorship from the American Chemistry Council’s (ACC’s) Flexible Film Recycling Group (FFRG) for use of the store drop-off label on its plastic carryout bags.
“Wegmans has accepted used plastic bags and wrapping material for recycling at our stores since 1994 as a way to help make a difference in the communities we serve,” says Jason Wadsworth, Wegmans sustainability coordinator. “Our adoption of the How2Recycle Label is a step in the right direction as we try to clear up the confusion surrounding recycling.”
Wegmans customers will initially see How2Recycle’s Store Drop-off Label on plastic carryout bags, with plans to expand to various flexible plastic materials throughout its stores, including deli and produce bags.
Furthering its goal to educate shoppers about plastic film recycling and to direct them to the correct bin, the grocery store chain also is displaying a prominent educational poster near store entrances.
“We have enjoyed our collaboration with Wegmans. Their well-rounded approach is exactly what we hoped for when we developed the How2Recycle Label program,” says Anne Bedarf, senior manager at GreenBlue, an environmental nonprofit group. “Wegmans’ strategy will provide benefit not only for their own stores and customers but also for How2Recycle’s larger goals, by acting as a positive example for the grocery and recycled film industries overall.”
ELECTRONICS
Sims Recycling Solutions certifies to e-Stewards
Electronics recycling company Sims Recycling Solutions (SRS), with North American headquarters in West Chicago, Ill., has announced that it has achieved e-Stewards certification at all of its U.S. processing sites and at its Toronto plant. The company’s two additional Canadian sites in Vancouver and Montreal are scheduled to be certified this summer, SRS says.
The e-Stewards certification was created by the Basel Action Network (BAN), a Seattle-based nonprofit environmental organization. The accredited, third-party certification program is based on a standard that prohibits the export of electronic scrap to developing countries, landfilling and the use of prison labor in the recycling process. The e-Stewards standard is endorsed by more than 70 environmental groups as well as by more than 70 major enterprise companies and cities, according to BAN.
E-Stewards certification is designed to assure clients of certified electronics recyclers that they provide complete data destruction, uphold environmental and social responsibility and are aware of all relevant laws to ensure responsible recycling, according to SRS.
BAN founder Jim Puckett says, “Sims Recycling Solutions has proven itself to be a company at the forefront of corporate responsibility, often taking unpopular and costly positions to prevent global e-waste pollution.”
Steve Skurnac, president of SRS North America, says, “Among our extensive profile of health, safety and environmental management certifications, the e-Stewards certification will further provide our customers with the assurance that we are handling their material with integrity and accountability.”
SRS says it “works closely with recognized industry associations to ensure business operations follow and exceed established industry standards.” Each facility has full-time managers who oversee internationally recognized corporate safety programs.
Additional certifications maintained by SRS include Responsible Recycling (R2), ISO 9001 and 14001, OHSAS 18001 and Transported Asset Protection Association (TAPA).
METALS
Arkansas agency lifts air permit stay at Big River Steel
The Arkansas Pollution Control and Ecology Commission has lifted a stay on an air permit for Big River Steel (BRS), which plans to build a steel minimill in Arkansas. Nucor Steel, a rival steel company, had filed an appeal on the issuance of the air permit late last year. BRS received the initial approval Oct. 17, 2013.
BRS says delays in issuing the air permit were jeopardizing private investors in the project as well as some state government funding that had criteria that need to be met by June 2014.
Charles Moulton, the administrative law judge for the Arkansas Pollution Control and Ecology Commission, says the steel company needs to meet deadlines under provisions of Amendment 82 of the state’s constitution to be approved for $125 million in bonds.
According to local press reports, the commission is scheduled to meet March 24 to issue its final decision on the permit.
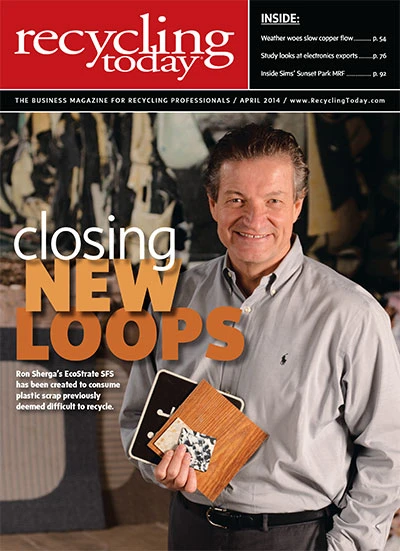
Explore the April 2014 Issue
Check out more from this issue and find your next story to read.
Latest from Recycling Today
- Lautenbach Recycling names business development manager
- Sebright Products partners with German waste management equipment company
- WasteExpo transitions to biennial format for enhanced experiences
- Study highlights progress, challenges in meeting PCR goals for packaging
- Washington legislature passes EPR bill
- PureCycle makes progress on use of PureFive resin in film trials
- New copper alloy achieves unprecedented high-temperature performance
- Gränges boosts profits and sales volume in Q1 2025