MUNICIPAL RECYCLING
Chicago Expands Recycling Program
Chicago Mayor Rahm Emanuel has announced that more than 131,000 households will begin receiving blue cart recycling services in March and April of this year as the recycling program expands citywide. The expansion is part of Emanuel’s 2013 budget initiative to provide recycling citywide.
“Chicago will no longer be a tale of two cities when it comes to recycling,” Emanuel says in a statement. “Adopting new strategies will allow us to expand blue cart recycling to every community in 2013, and residents will soon have greater access to recycling services, which will make Chicago a greener, more environmentally friendly city.”
The blue cart recycling program provides biweekly recycling collection services to residents living in single-family homes and in two-, three- and four-flat buildings. The expansion will include 340,000 households and is scheduled to be complete by this fall. Currently, 260,000 households in the city receive blue cart recycling service.
The Mayor’s Office notes that in October of 2011, Emanuel implemented a managed competition for recycling services to create efficiencies and to reduce operational costs to taxpayers.
According to Emanuel, in one year the competition decreased recycling costs by $4.7 million and paved the way for the citywide recycling expansion. Chicago projects an annual $19.2 million investment for citywide recycling operations, compared with $31.1 million without adopting managed competition—a 38 percent decrease.
To ensure a smooth transition, each of the six city service areas will undergo a gradual expansion of households receiving new recycling services. Subsequent phases will be announced as collection schedules and routes are finalized.
Chicago’s recycling service providers include the Chicago Department of Streets and Sanitation, Sims Municipal Recycling and Waste Management.
METALS
Gerdau Acquires Cycle Systems
Gerdau, with North American headquarters in Tampa, Fla., has acquired “certain operating assets” of the scrap metal company Cycle Systems, headquartered in Roanoke, Va. Cycle Systems, which operates nine locations throughout Virginia, including an auto shredder and a number of feeder yards, processed approximately 185,000 tons of metal in 2011, according to Gerdau.
Gerdau, which operates a steel mill in Petersburg, Va., says the deal will expand its presence to the mid-Atlantic region.
“This purchase supports our goal to minimize billet cost by having scrap sources closer to our steel mills,” says Guilherme Johannpeter, president of Gerdau’s North American long steel division. “It will be a great advantage for our mill in Petersburg, Va., and other nearby operations.”
Matt Yeatman, vice president of metallics and raw materials at Gerdau’s North American long steel division, says, “In addition to supporting our sourcing strategy, it will also grow our commitment to sustainability and the Petersburg community.”
A source at Cycle Systems says Gerdau was among several companies that had been looking at acquiring the scrap metal company since late last year.
CORPORATE SUSTAINABILTY
GM Seeks to Boost Recycling Infrastructure
General Motors (GM), Detroit, has announced plans to take a regional approach to boosting its recycling infrastructure. In a news release issued in mid-February, the company says it will first address its manufacturing operations in the Southeast.
The company created the Suppliers’ Partnership for the Environment Southern Network forum, hosting a meeting of automakers, suppliers, recycling partners and government officials at its Spring Hill, Tenn., complex in February to discuss recycling opportunities and capabilities.
The forum is part of GM’s stated plan to increase the number of its landfill-free facilities from 104 to 125 by 2020. The company is crediting its waste reduction leadership in part to its network of partners.
Suppliers Partnership, according to GM, collaborates with and mentors members within the automotive supply base on environmental and social issues. GM says it envisions the new Southern Network forum as the first step in a growing regional recycling and job development network with the potential to increase recycling and waste treatment options.
“Compared to other regions where GM has plants, the Southeast has the opportunity to build up its recycling economy,” says John Bradburn, GM manager of waste reduction efforts. “By connecting local recyclers—and those with potential—with area companies, we can start to address the gaps and build a more robust infrastructure that will help the auto industry and beyond to leave a smaller footprint.”
ELECTRONICS
4th Bin Receives E-Stewards Certification
New York-based 4th Bin has announced that it has received e-Stewards certification, making it the only electronics recycler in New York City to achieve the certification that was developed by the Seattle-based Basel Action Network (BAN).
“Our customers not only expect but demand the highest standards when it comes to responsible electronics recycling,” says Michael Deutsch, co-founder and CEO of the 4th Bin. “In becoming certified as an e-Steward recycler, the 4th Bin is demonstrating that our ethical position in the industry is more than just words and fluff. We are willing to take action. And there’s really no better way to do just that than to achieve the industry’s highest level of certification.”
John Kirsch, co-founder and senior vice president of business development at the 4th Bin, adds, “As NYC’s leading electronics recycler, we take our commitment to both ethical recycling and our community seriously. In becoming the city’s only certified e-Stewards recycler, we are determined to set the bar high, encouraging others to strive for the ultimate level of environmentally responsible behavior.”
4th Bin also has pursued other certifications, including ISO 14001 and R2 (Responsible Recycling Practices), which focuses on the performance of electronics recyclers in the areas of environmental and public health, worker health and safety, data and facility security as well as the whole of the recycling process and custody of materials through final disposition.
The company says it is one of the initial members in the Coalition for American Electronics Recycling (CAER), supporting the Responsible Electronics Recycling Act (HR 2284).
METALS
Universal Scrap Metals Expands to Kentucky
Chicago-based Universal Scrap Metals (USM) has expanded its operations with the purchase of the facility and equipment used by Anheuser-Busch Recycling Corp.’s (ABRC’s) aluminum recycling facility in Georgetown, Ky. According to USM, ABRC has a long relationship with USM and is fully supportive of USM’s efforts to expand.
USM says the new location, to be called USM Alumacycle, will allow the company to service customers in a new region. The new equipment at the facility also is expected to allow USM to offer higher recovery of off-spec used beverage cans (UBC) and aluminum alloys to manufacturers, dealers, waste companies and mills. The company now operates eight locations throughout the Chicago area, central Illinois and Kentucky.
USM Alumacycle is a group investment between Universal Scrap Metals Inc., USM Processing Ltd. and USMe LLC. USM says the recycling facility was designed and engineered from the ground up three years ago by the equipment company Machinex Technologies, Plessisville, Quebec, and has the capability of shredding, sorting and processing 5 million pounds of aluminum per month. The facility also is near some of North America’s largest aluminum sheet mills, eliminating many logistical issues and transportation costs, according to the company.
“I’m excited to see USM’s aggressive growth strategy continue,” says Jason Zeid, president of USM Alumacycle. “This recycling facility in Kentucky will expand USM’s already vast aluminum processing capability and allow us to service more customers in the South.”
“Operating this new facility is a monumental step in line with our goal of providing the best recycling and processing solutions possible,” says Pat Madison, USM chief operations officer. “This will allow USM to process off-spec and used beverage cans and other aluminum alloys in a state-of-the-art facility that is unique to the industry and, in turn, allow us to offer higher recovery on these cans and aluminum alloys to manufacturers, dealers, waste companies and mills.”
EVENTS
Inaugural Paper Recycling Conference Asia Announces Full Program
The full program for Paper Recycling Conference Asia, launching May 30-31, 2013, has been announced. The extension of the success Paper Recycling Conference series, produced by the Recycling Today Media Group and Smithers Pira in cooperation with China TAPI, into Asia provides an opportunity for companies in North America, Europe and the rest of the world to meet buyers in the Asian market.
Highlights include the opening keynote address, The Role of Recyclables in China’s Economic Resurgence, presented by Professor Wang of the Chinese Ministry of Environmental Protection; an overview of macroeconomic trends affecting Asia’s recovered paper industry from Sally Sun, Deloitte China; and an exclusive one-on-one interview with Ross Li of Lee & Man.
Attendees also will hear from Randy Kim, Ekman Recycling; Henri Vermeulen, Smurfit Kappa Group; Niu Qingmin, Jiangsu Paper Association; Yoshimitsu Tanaka, Kaneko; and others on recovered paper supply, infrastructure and quality issues and challenges.
“We’re excited about launching a paper recycling conference in Asia, particularly as Asian demand continues to represent the major growth area for recovered paper,” says Jim Keefe, executive vice president and group publisher, Recycling Today Media Group. “Since this inaugural event replicates the design of our existing events’, attracting merchants, brokers, suppliers of recovered fiber and mills from around the globe, it’s sure to represent a unique and powerful opportunity for the world’s suppliers and consumers of recovered paper to meet.”
MUNICIPAL
GBB to Assist in Evaluating Cleveland’s Waste-to-Energy Options
Gershman, Brickner & Bratton Inc. (GBB), Fairfax, Va., is continuing its evaluation of development options for the city of Cleveland Recycling and Energy Generation (CREG) Center. Cleveland hired GBB to review options for the CREG Center project, which seeks to better manage the city’s municipal solid waste and potentially to use waste as a source for locally produced energy.
Joining GBB for this assignment are five firms that will bring their local understanding and experience in keys areas of expertise for the project, according to the company. NTH Consultants Ltd., McGuiness Unlimited Inc. and Whelan Communications Inc. all are based in Cleveland, while GT Environmental Inc. is based in Akron, Ohio, and RMF Engineering Inc. is in Charlottesville, Va.
“Cleveland has been investigating the use of municipal solid waste (MSW) for the production of energy since at least 2007,” says Ken Silliman, chief of staff for Cleveland Mayor Frank Jackson. “Our goals, in part, are to reduce Cleveland’s dependence on fossil fuels, develop local energy generation capacity and recover marketable byproducts such as recyclables from MSW.
She adds, “The GBB Project Team is in a unique position to assist us in developing a successful project due to its background, project understanding, local offices and resources and experience. We anticipate this process will result in a short listing of qualified companies and a request for proposals by the fall of 2013.”
In September 2011, the Division of Cleveland Public Power (CPP) issued a request for information and qualifications (RFIQ), followed by a supplemental request for information and qualification (SRIQ), which targeted a variety of waste conversion and management approaches, including thermal conversion, pyrolysis, gasification, recycling and fuel production as well as consulting and financial firms to assist in project development.
The GBB project team will review, analyze and evaluate the responses; evaluate gasification-to-energy development efforts; provide a comparison of the best options; and make recommendations.
ELECTRONICS
Appliance Recycling Plant on Track in South Carolina
Recleim, a startup recycling firm based in Atlanta, has announced plans to open an appliance and electronics recycling facility in Aiken County, S.C. At the RecylonomicsSC event in South Carolina, the company said it would commit $40.6 million to build the facility. When fully operational, Recleim says it expects to employ 200 people at the plant.
The company will focus on resource recovery from appliances, white goods and electronic scrap, specializing in refrigerators, freezers and cooling units. Recleim is currently updating a 110,000-square-foot building to accommodate three demanufacturing and production lines. When fully operational, the company says the plant will be able to process between 400,000 and 600,000 units per year.
“We are pleased to move forward with plans to open our new facility in Aiken County,” says Ben Hirokawa, Recleim CEO. “South Carolina provides us with an excellent business environment and the skilled workforce we need for our operations.”
ELECTRONICS
Texas Reports Electronics Recycling Results
The Texas Commission on Environmental Quality (TCEQ) has reported that residents of the state turned in more than 43 million pounds (21,500 tons) of electronics to computer manufacturers for recycling in 2012. The TCEQ says that in addition to recycling covered computer equipment, many computer manufacturers also voluntarily collect televisions and other electronics for recycling.
The TCEQ allows computer manufacturers to report collected electronics other than computer equipment covered under the program.
Currently, 90 manufacturers representing 133 brands are participating in the TCEQ computer recycling program. As part of the program, computer manufacturers collected more than 24 million pounds (12,000 tons) of covered computer equipment in 2012. Of that, more than 20 million pounds were recycled and 3.7 million pounds were reused.
The 2012 number is higher than the amount reported for any other reporting year. The second highest level was 2010, when computer manufacturers collected for reuse or recycling a total of 19.5 million pounds of computer equipment.
The TCEQ says it is currently working to implement a new program for the recycling of televisions, which will require television manufacturers that sell in Texas to collect and recycle such products.
More information about recycling computers in the state can be found at www.TexasRecyclesComputers.org. Information on recycling television equipment is at www.TexasRecyclesTVs.org.
PLASTICS
Plastics Recycler Expands Operations in Pennsylvania
Pennsylvania Gov. Tom Corbett has announced that PGA Inc., a processor of recycled plastics, will relocate its operations to a different facility within its home community of White Haven, Pa. The move will create 28 jobs, according to a news release announcing the project.
The company says it will invest more than $600,000 in land and building acquisitions and in development, building renovations, equipment purchases and employee training.
To assist in the move, the company will receive $56,000 in Job Creation Tax Credits from the Pennsylvania Department of Community and Economic Development when the 28 new employees are hired. PGA has committed to creating at least 28 new jobs within three years and to retaining its current 13 employees.
The expansion was coordinated by the Pennsylvania Governor’s Action Team, which provides site selection assistance, coordinates the involvement of other state agencies and packages the appropriate development funding for the project.
PGA was formed in 2006 as a two-person operation and has grown into a full-service plastics recycler and processor.
LEGISLATION & REGULATIONS/ELECTRONICS
Study Finds Limiting Electronic Scrap Exports Could Create Jobs
Restrictions on electronic scrap exports could create up to 42,000 direct and indirect new jobs with a total payroll of more than $1 billion, according to a study commissioned by the Coalition for American Electronics Recycling (CAER).
“The study further documents how growing an industry with the capacity to manage the volume of e-waste generated within our borders could create tens of thousands of good-paying American jobs by promoting investment in our domestic infrastructure,” says Steve Skurnac, president of Sims Recycling Solutions, based in Chicago, and CAER steering committee member.
CAER members include electronics recyclers and affiliated organizations that support the passage of the Responsible Electronics Recycling Act (RERA), legislation designed to promote fair and responsible e-waste trade, according to the CAER. The bill, which will be reintroduced in the current session of Congress, bans the export of certain types of unprocessed and nonworking electronics and e-waste from the U.S. to developing countries. Fair trade in tested, working electronics and processed e-scrap commodities would not be restricted, the group says.
DSM Environmental Services Inc., a research and consulting firm focused on recycling, materials management and solid waste management strategies, conducted the study. It includes a survey of CAER members and estimates current employment at about 6,850 people in the U.S., with a payroll of roughly $250 million.
While nearly 1.2 billion pounds of electronics were recycled by CAER members in 2012, a comparison to data in a recent U.S. Environmental Protection Agency-funded report determined that another 3.6 billion pounds of electronics were exported, sent to landfills or otherwise processed.
Processing this material in the U.S. would create 21,000 full-time equivalent recycling jobs with a corresponding payroll of $772 million and the potential for 21,000 additional indirect jobs, according to the study. The study says the number of jobs will further increase as e-scrap volumes rise. The U.S. EPA estimates that e-scrap is growing two to three times faster than any other portion of the waste stream.
“The potential for job creation is a major reason RERA continues to attract co-sponsors from both parties,” says Wendy Neu, executive vice president of Hugo Neu Corp. and a CAER member.
METALS
SMM Releases Findings on Inventory Problems
Sims Metal Management Ltd. (SMM), New York, has released its report on its previously announced investigation into inventory valuation issues at two of the company’s facilities in the United Kingdom. The report has determined that a write-down of inventory of $78 million will be required, versus a preliminary assessment of $60 million. The write-down adjustment has been independently verified by SMM’s external auditor PricewaterhouseCoopers (PwC), with $16 million of the inventory write-down to affect the company’s first-half fiscal 2013 results and the balance to be reflected in restatement for prior periods results.
Additionally, the report has found that in light of the losses, SMM’s impairment charges related to goodwill and other intangible assets totaled in the aggregate $354 million. About $291 million of this impairment charge relates to North America metals and will be recorded against the fiscal 2013 result; $63 million of the impairment charge related to U.K. metals and Sims Recycling Solutions (SRS) U.K. and will be reflected in the restatement of results for prior periods.
According the committee, the company undertook a thorough investigation at SMM’s Newport and Long Marston facilities in the U.K. The committee concluded that a write-down of inventory of $78 million will be required, versus the preliminary $60 million assessment. The write-down represents around 29 percent of the value of inventories in the U.K. and 9 percent of inventory on a group-wide basis before the write-down.
Additionally, the committee oversaw inventory valuation processes, accomplished via stock take and other verification procedures, at all other sites in the U.K. and principal SRS sites in continental Europe and North America. At the conclusion of the investigations, the committee determined that the overstatement of inventory was unique to circumstances at the U.K. locations in Newport and Long Marston. The committee found no evidence of control deficiencies or inventory miscalculation at any locations other than Newport and Long Marston.
The investigations revealed that the primary cause for breakdowns in SMM’s control environment can be attributed to the company’s failure to adequately supervise operations, safeguard assets and maintain adequate controls over financial reporting relating to inventory, SMM says.
LEGISLATION & REGULATIONS/PLASTICS
MBA Polymers Calls for UK VAT Exemptions
Plastics recycling company MBA Polymers, headquartered in Richmond, Calif., has called on the United Kingdom government to suspend the VAT (valued-added tax) on recycled plastics to help stimulate consumer demand and encourage investment in the plastics recycling industry.
Nigel Hunton, CEO of MBA Polymers, called for the action during The Future of Recycling – The Challenge of Plastics conference. The event’s audience included U.K. politicians, environmental groups and major plastics users.
In his presentation, Hunton said, “Plastics recycling is a big opportunity [in the U.K.]. We currently lie behind leading European countries in terms of the recycling rates of postconsumer plastic waste; in 2011 the U.K. performance was just over 20 percent. Sweden, Norway, Germany and France were all above us.”
Continuing his presentation, Hunton commented, “The U.K. can become a world leader in this sector, but we can only do that by changing some of our approach. Recycled plastics are a resource—not a waste product. There is the potential for major environmental and economic benefit, such as attracting new jobs and investment to the U.K., reducing our dependence on foreign oil and providing a competitive advantage for the U.K. through ‘green marketing’ and innovative technology. We also support the EU Environment Commissioner in welcoming reductions on incineration—switching from burning for energy generation to ‘full recovery’— maximizing recycling potential.”
In a news release issued by MBA after the event, Hunton adds, “Our view is that we only need to do a few things differently in the future. First, we need a level playing field. We need auditing of downstream overseas plastic waste processors, similar to domestic processors. We allow the export of plastics waste, but it needs better and more vigorous enforcement and checking.
“Second, we need something to incentivize the market with legislation designed to encourage postconsumer recycled plastics content in new products, such as exemption or a reduced rate of VAT,” Hunton says.
PLASTICS
Plastics Recycler to Open Plant in Missouri
Lyne Plastics has announced plans to invest $1.2 million to open a second plastics recycling operation in Missouri. The wholesale industrial recycling company, headquartered in La Monte, Mo., has decided to open a facility in Sedalia, Mo., that will measure approximately 48,000 square feet. The expansion will accommodate new production lines.
Lyne Plastics, which has been in operation for 19 years providing toll services, shreds, cleans, grinds and mixes plastics that are then shipped to industrial clients for use in a range of new products. Lesa Lyne, co-owner of the company, says the new location will be able to produce 1 million pounds of product, in addition to the product currently being produced at Lyne’s original site.
“We’re going to keep the line running constantly, day and night,” she says of the company’s production plans. “Hopefully within the next two to three years, we’re going to set up two more lines [similar to the existing ones],” Lyne says. “We’ve already got the material backed up, and there’s an endless supply of it.”
To assist the company with the expansion project, the Missouri Department of Economic Development has authorized an incentive package that includes $57,602 in Enhanced Enterprise Zone program tax credits over five years. The program has been designed for certain areas in the state that hold the potential to create sustainable jobs.
PLASTICS
Report Examines Plastics Recycling in Wisconsin
A study commissioned by the Wisconsin Department of Natural Resources (DNR) finds that the state could realize substantial economic rewards and jobs growth by increasing the amount of plastics it recycles. The study estimates that approximately $64 million in recyclable plastic materials are landfilled each year.
To get a better understanding of the opportunities afforded with increasing plastics recycling, the DNR commissioned a study to identify actions that can be taken to capture and recycle more used plastics. “In addition to the benefits to businesses and employment, increasing plastics recycling would provide environmental benefits by prolonging the life of landfills and reducing pollution,” says Cynthia Moore, DNR recycling program coordinator.
The study, authored jointly by Foth Infrastructure and Environment, Green Bay, Wis., and Moore Recycling Associates, Sonoma, Calif., lists steps Wisconsin can take to substantially increase plastics recovery rates.
The DNR’s Moore says the actions “could be implemented individually or as a coordinated approach and target the most valuable and commonly used plastic containers, such as consumer beverage bottles and containers for household cleaning products.”
The study also emphasizes the potential to increase the collection and recycling of plastic bags and other film plastics as well as recovered rigid plastics, such as clamshell containers, margarine tubs and drink cups.
Spurred by the study, the DNR has agreed to conduct a pilot project this spring to expand recycling of flexible film packaging among both consumers and businesses. The film recycling project will be carried out under a memorandum of understanding with the American Chemistry Council’s Flexible Film Recycling Group and the Sustainable Packaging Coalition’s GreenBlue Foundation.
Currently, Wisconsin’s plastic industry employs around 40,000 people with a direct payroll of $1.6 billion, which ranks eighth nationally. The executive summary is available at http://dnr.wi.gov/topic/recycling/documents/WIPlasticsStudyExecSummary.pdf.
LEGISLATION & REGULATIONS/PLASTICS
ACC Seeks Polystyrene Options in New York City
The American Chemistry Council (ACC), Washington, D.C., has released a statement saying it is willing to work with New York City to explore the possibilities of developing an effective polystyrene foam recycling program in the city.
The ACC announcement was made in advance of New York City Mayor Michael Bloomberg’s State of the City address, in which he called for restrictions on the use of polystyrene foam.
In his address, Bloomberg said, “One product that is virtually impossible to recycle and never biodegrades is Styrofoam. (Bloomberg referred to polystyrene by its Dow Chemical-trademarked name of Styrofoam.)” The mayor also said Styrofoam increases the recycling cost by as much as $20 per ton.
“Something that we know is environmentally destructive, that is costing taxpayers money and that is easily replaceable is something we can do without,” the mayor continued. “So, with Speaker Quinn and the city council, we will work to adopt a law banning Styrofoam food packaging from our stores and restaurants,” he said.
Steve Russell, ACC vice president of plastics, countered Bloomberg in a statement, saying, “The technology exists to recycle polystyrene foam food service right now. California is making this work—22 percent of households there can recycle polystyrene foam food service cups, plates, bowls, clamshells and other containers at curbside.”
Russell also notes that polystyrene foam food service products make up less than 1 percent of our nation’s solid waste and create significantly less waste by weight and comparable waste in terms of volume.
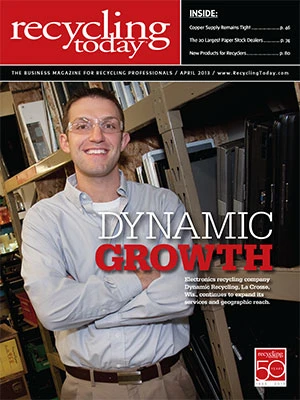
Explore the April 2013 Issue
Check out more from this issue and find your next story to read.
Latest from Recycling Today
- Lautenbach Recycling names business development manager
- Sebright Products partners with German waste management equipment company
- WasteExpo transitions to biennial format for enhanced experiences
- Study highlights progress, challenges in meeting PCR goals for packaging
- Washington legislature passes EPR bill
- PureCycle makes progress on use of PureFive resin in film trials
- New copper alloy achieves unprecedented high-temperature performance
- Gränges boosts profits and sales volume in Q1 2025