Over the past several decades, James (Jim) W. Lawrence has helped scrap metal company employers and employees learn more about how to properly identify metals and alloys. Lawrence has conducted training for co-workers over the years and often has been an instructor at metals identification workshops and training courses offered by the Institute of Scrap Recycling Industries Inc. (ISRI), Washington, D.C.
With the advent of hand-held metals identification analyzers in the late 1990s, scrap processors have had access to a fast and accurate way to identify inbound scrap at the scale without having to take samples to a lab in another part of their facilities.
As Lawrence, currently general manager of ISA Alloys, Louisville, Ky., notes in the following interview, the use of such analyzers does not mean scrap buyers can get by with knowing less about the metals they are inspecting and purchasing.
If anything, Lawrence says, new challenges are mounting. As metals producers introduce new alloys that are now being seen in scrap yards, they likewise expect their scrap suppliers to check and recheck their shipments to ensure the quality is better than ever.
Recycling Today (RT): What are some of the similar-looking but metallurgically different metals or alloys that have historically required know-how to identify properly at a scrap yard?
Jim Lawrence (JL): I think this is what makes the stainless and alloy field so difficult and goes right to the heart of metals identification. For example, we look at a stainless steel sink and we can all say, “It is stainless steel.” Then you go to Home Depot and see a price range from $228 to $800 and ask, “What the heck?”
A stainless sink can be 201, which is 4 percent nickel with manganese; there also is 201 with copper; there is 301, which is 7 percent nickel; and 304, which is 8 percent nickel. So a simple stainless sink can be four completely different materials, but they all look the same. There are valves that have markings on them. For example, CF8M is a common casting grade that is 316 stainless, which is a nickel-chromium-molybdenum grade. There is nothing easy or simple in the stainless steel and high-temperature alloy grades.
I had an old teacher who taught me to learn the applications and you will be able to understand and determine what the metals are. Applications include the chemical industry, where molybdenum-bearing grades are critical; the sea vessel applications that require corrosion resistance; the food industry; the automotive industry; the aircraft industry, etc. I think of all the metals, the stainless and alloy part of our business still remains a mystery to many.
RT: Prior to analyzers, what were the methods scrap recyclers could use to differentiate metals that look similar?
JL: This is a great question because this is the era I came from. We used acid testing, and those acids would not identify the metal per se. However if, for example, we were checking a stainless material and let’s say it was a piece of pipe and it came from a chemical plant, we would, through application, guess that it was 316, which contains molybdenum.
We had an acid test that would turn pink, which indicated the presence of molybdenum and the deeper the red, the higher the molybdenum content. We had acids that would test for chromium, nickel, manganese, etc. But to use the acids, you needed to have some idea of what you were checking.
We used spark testing, which was very effective. Even back in the early 1900s, many steel mills used this method and achieved accurate results. Spark testing has become a lost art, but I still use it, and it is very effective for identifying materials.
We also used a Fuess Spectroscope, which is an instrument that uses the spectra of elements by using a prism grating instrument. Using the spectrum of elements, you checked your unknown with a known alloy. This was a very difficult instrument to master but was very effective and still is in use today. We also used the file meter, which is also still in use today and is very inexpensive but also very effective.
Different metals will give off a different reading as the material is filed, and that reading is consistent with the alloy being checked. The early instrument that began the reading type analysis was the Kevex, which used a radioactive isotope that began the instrument-type technology.
And finally, the most important tool of all was, and still is, the most effective tool in the stainless and alloy industry: the magnet! The magnet will differentiate 300 from 400, identify 301, separate R & K Monel, help identify nickel-chromium grades of stainless, etc. Identifying is a process of elimination—application, color, density, markings and magnetic properties. Today’s identification needs to be a combination of the old methods and the new technology.
RT: With stainless alloys in particular, how can proper/improved separation make a financial difference at a scrap yard?
JL: This is huge. We receive loads of stainless every day with higher grades of stainless and alloys mixed in. Many can be seen by application and markings. The best example of this is finding 316 mixed in with 304, and so often it is valves that are clearly marked with the CF8M.
The difference can be as much as 30 cents per pound or more. So if you find 1,000 pounds of 316, that is $300 per load. When you get into alloys that are $4 per pound and up, the dollars can mount up quickly.
By the same token, using the magnet will quickly identify lower grades of stainless to prevent expensive downgrades and also leads to thousands of dollars both on the buy side and sale side. Knowing what you are buying and buying it right is just as important as selling it and eliminating downgrades and pulling out the materials that are of higher value.
RT: What are some common complaints or claims from foundries and mills that might stem from improper identification?
JL: The biggest problem for stainless is copper. The specifications are 0.50, and with the price of nickel today there is a great deal of substituting copper for nickel. Identifying these copper-alloyed grades is very difficult, and we are finding grades such as 301 and 201 with copper, and it is making it very difficult. This often drives melts into penalty situations. The presence of tin is another problem that can lead to disaster in stainless melts.
RT: How have hand-held analyzers helped improve metals identification processes?
JL: The hand-held analyzers have been a big help in identifying things like copper, as mentioned before, as well as other elements, such as tin and lead, that can lead to serious quality problems at the melting facilities. The new units also can check for light elements such as phosphorous, which is another problem in the stainless field that leads to radiation problems as well as serious melt issues. The hand-held units also are a big help in identifying nickel and cobalt alloys that have very high values that can then be sorted and shipped as their own item. All of this relates to a very high return on investment.
RT: What are a few common shortcomings when using handheld analyzers of which processors should be aware?
JL: The shortcomings of the hand-held analyzers, or guns, involve not using them properly to get an accurate reading. These analyzers must be calibrated daily against a certified sample. The preparation of the surface of the piece being checked also is critical to obtain an accurate reading. Too often, users do not do this and get false readings that can be expensive mistakes.
A good example is when a customer of mine asked for a price on Ni200 (low-alloy 99 percent nickel) at a time when nickel was at $18 per pound. He bought the material and when I saw it, I knew it was not Ni200 because the application did not apply. I used a grinder to prepare the surface and the sparks indicated it was nickel-plated iron worth maybe 20 cents per pound. So, in this case, the old application and grinder told me what it was and using the gun cost him a lot of money.
Another problem we see is that the reading a shipper has and the reading a receiver has can be different, causing a differential in dollars. These guns do very well, but everyone has to understand the variances and needs to be careful using the analysis as the exact recovery.
Another problem, a big problem, is that too often those using the hand-held do not scroll the entire analysis to read all the elements. They allow the instrument to use the installed library to identify the piece being checked. It only means that the reading fits closest to that analysis. Good sorters will use all their knowledge to confirm the identification.
RT: As of 2013, what are some areas where there is room for improvement in how recyclers identify scrap metal?
JL: There is no question that identifying metals is a journey, especially as the price of intrinsic elements continues to rise. The mills and the foundries are constantly looking for ways to reduce their costs while increasing the value of the applications they are being used in.
There are now duplex alloys being used to replace 316 stainless, and this trend is only going to continue. The research and development units at steel mills around the world continue to experiment with residual elements that can be used to replace higher-cost elements. We have seen this with the use of using copper to replace nickel. The development many years ago of substituting manganese for nickel reduced costs while still making the application work. We are going to continue to see this kind of development and as this happens we are going to need to be able to identify those alloys and elements to meet the very stringent quality controls at the melting facilities.
We are in a very competitive environment in the recycling industry, and metals identification is a real competitive edge. Controlling costs and maintaining strict quality control measures must be a part of what every shipper has to concentrate on each day.
Jim Lawrence is general manager of ISA Alloys, Louisville, Ky. The company can be reached on the web at www.isa-inc.com/stainless-a-alloys/alloyscontactinfo.
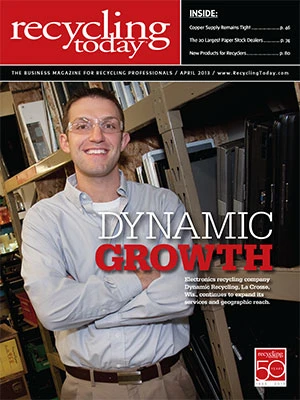
Explore the April 2013 Issue
Check out more from this issue and find your next story to read.
Latest from Recycling Today
- Fenix Parts acquires Assured Auto Parts
- PTR appoints new VP of independent hauler sales
- Updated: Grede to close Alabama foundry
- Leadpoint VP of recycling retires
- Study looks at potential impact of chemical recycling on global plastic pollution
- Foreign Pollution Fee Act addresses unfair trade practices of nonmarket economies
- GFL opens new MRF in Edmonton, Alberta
- MTM Critical Metals secures supply agreement with Dynamic Lifecycle Innovations