Charlotte, N.C.-based ReCommunity operates 36 facilities in 13 states, recovering and processing nearly 2 million tons of recyclables each year. Of the company’s 30 material recovery facilities (MRFs), 22 are processing single-stream material.
The company was established in 2011 by Pegasus Capital LLC, an affiliate of Pegasus Capital Advisors LP, Intersection LLC, MissionPoint Capital Partners LLC, HarbourVest Partners LLC and Ares Capital Corp. with the purchase of select recycling assets of FCR Inc., a wholly owned subsidiary of Casella Waste Systems Inc.
According to the company’s website, www.recommunity.com, “As we looked around, we saw the need to create an honest-to-goodness pure-play recycling company, with a single-minded commitment to community-first benefits. Pure play means we don’t have or operate landfills. Pure play means we don’t have or operate collection trucks.”
ReCommunity says its success comes from focusing on innovative and effective resource recovery solutions and building sustainable community partnerships.
Sean Duffy, ReCommunity president and CEO, says the company is equipment and vendor agnostic. “We look at all types of equipment from all types of vendors, which allows us the flexibility to embrace new technology quickly,” he wrote in the October 2012 article for Recycling Today, “Dynamic Duo,” available online at www.RecyclingToday.com/rt1012-single-stream-processing-investments.aspx. “More importantly, it allows us to use the best system for each specific application, which is not necessarily the cheapest equipment. Through this approach, we’ve seen better separation through improving disc technology and air flow innovations. And, we’re seeing better use and recovery with optical scanners.”
Under the Influence
The designs of ReCommunity’s MRFs have been influenced by a number of factors, chief among them has been the trend toward single-stream collection, Duffy says. “Due to the collection efficiencies, convenience at the household resulting in higher participation rates and increased products added to the acceptable list of recyclables, single stream is here to stay and will only expand,” he says.
While this move has helped to increase the volume of recyclables collected, it also has led to an increase in residue at the company’s MRFs, which ReCommunity tries to combat through community education when rolling out programs and on an ongoing basis, Duffy says.
Not only has the collection method changed but so has the composition of the recyclables stream, Duffy says, noting that containers, particularly PET (polyethylene terephthalate) bottles, have increased in prominence while newspapers have decreased. “Fiber used to account for 65 to 70 percent of the material stream,” he says. “Now, it is just about 50 percent.”
While newspaper is less prominent, OCC (old corrugated containers) have increased in light of the growth in online shopping, he adds. And many programs accept aseptic containers as well as plastics Nos. 3 through 7 for recycling in addition to the commonly accepted PET and HDPE (high-density polyethylene).
Flexibility Required
Processing equipment has had to change in response to the material stream. Screen designs have been modified and more screens have been added, as have optical sorters. “Sorting equipment has become more specialized and more efficient,” Duffy says. “As the inbound composition continues to change, so will the screens.”
In terms of screening technology, Duffy says ReCommunity’s systems vary by location and are influenced by a variety of factors, including the commodity mix, temperature and humidity of the area. Variability and flexibility are requirements for any screening technology, he adds.
In response, manufacturers have developed a variety of screens that feature discs of different sizes and shapes and shafts in varying numbers with different spacing to aid in separating two-dimensional material from three-dimensional material, he says.
Screens also feature hydraulics, which allow the angle of the screen to be adjusted in response to processing conditions. On humid days or when material is damp, the angle of the screens may need to be increased to aid in separation, Duffy adds.
Optical sorting equipment is becoming “more important every day,” he says, because it helps to increase plastics recovery and material quality and enables additional separation by resin type if required.
Today’s optical sorters can perform three sorts simultaneously, he says, but they require a lower burden depth to function optimally and, therefore, are often placed toward the end of the processing line. He adds that ReCommunity’s newest installation in Delaware employs five optical sorters in an effort to improve the quality of the recovered plastic products.
These equipment changes have enabled MRFs to employ fewer people on the sorting line, he adds. Those individuals who do work on the line function more as quality control than as sorters. These equipment advances have allowed MRFs to produce higher quality products at higher recovery rates, Duffy says. However, those benefits have come at a higher cost.
“In many cases you have to go bigger to offset the capital investment,” he says, adding that the hub-and-spoke approach helps MRF operators achieve the required scale. In this approach, material is consolidated at nearby transfer stations and then transported to a centrally located MRF for processing.
“If you have the volume, a bigger system will lower your operating costs.”
Duffy says ReCommunity does not receive a premium for recyclables recovered through its dual-stream facilities. In fact, he says, dual-stream programs can be more prone to contamination if the residents or haulers are not vigilant about sorting their recyclables. “Those systems don’t have the ability to do separations unless the material is manually pulled out,” Duffy says. “There may be a higher degree of contamination capability.”
He says broken glass also is more difficult to get out in dual-stream systems, as they seldom include the necessary screens.
Glass Act
Because much of the glass collected through single-stream programs is broken when compacted in the collection truck, MRF operators have few affordable options available for sorting the glass by color. Instead, Duffy says, ReCommunity focuses on removing the glass using screening technology and cleaning it up as much as possible by removing caps, labels and nonglass items, such as bits of paper.
When location permits, this material is sent to a glass beneficiation facility, where it is sorted using optical equipment and delivered to manufacturing plants. Duffy says approximately 75 percent of the glass ReCommunity recovers is delivered to beneficiation facilities.
When the company’s MRFS are not near a beneficiation facility, ReCommunity uses technology that allows it to crush and screen the glass to produce alternative daily cover (ADC) for landfills, he adds.
Beyond Residential
MRF operators and the municipalities they serve also are looking to process industrial, commercial and institutional (ICI) material to help improve their recovery rates.
This material is best processed on a second dedicated line, Duffy says, though it also could be processed through an existing residential line in a different shift, as the equipment may need to be modified slightly to best accommodate it and to realign the sorters.
He adds that ReCommunity does not blend this material with its residential material because the streams flow differently and the residual rate may increase, as commercial material can contain from 20 to 30 percent residuals.
Duffy says ReCommunity and other MRF operators are pursuing this strategy at plants where they have sufficient inbound and outbound storage and separation as well as ample space for system expansion.
Regardless of the material that ReCommunity is processing, Duffy says the company has three goals in mind—safety, quality and productivity—that are factored into all of its MRFs. “We have to have productivity in order to survive,” he says, “but we don’t want it to come at the expense of safety or quality.”
The author is managing editor of Recycling Today and can be contacted at dtoto@gie.net.
A Closer Look
To view photos of ReCommunity’s MRFs, visit www.recyclingtoday.com/rt0413-mrf-series-recommunity.aspx.
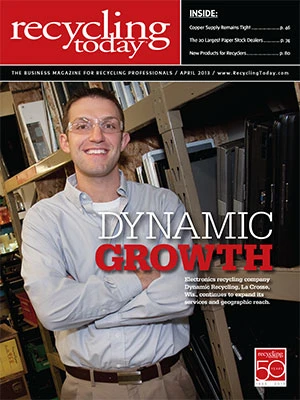
Explore the April 2013 Issue
Check out more from this issue and find your next story to read.
Latest from Recycling Today
- Fenix Parts acquires Assured Auto Parts
- PTR appoints new VP of independent hauler sales
- Updated: Grede to close Alabama foundry
- Leadpoint VP of recycling retires
- Study looks at potential impact of chemical recycling on global plastic pollution
- Foreign Pollution Fee Act addresses unfair trade practices of nonmarket economies
- GFL opens new MRF in Edmonton, Alberta
- MTM Critical Metals secures supply agreement with Dynamic Lifecycle Innovations