The CP Group Reintroduces the McMRF
The CP Group, headquartered in San Diego, has announced the reintroduction of the McMRF™. The company says its McMRF is designed to handle, process and separate single-stream materials at about 10 tons per hour.
The CP Group has owned the McMRF trademark for years, inheriting the name when CP Manufacturing acquired Count Recycling in 2000. The McMRF was originally designed to process only containers.
The company says it has re-engineered the system to process single-stream recyclables to appeal to small communities that do not need a full-scale MRF (material recovery facility). The company says the system provides the benefits of a larger system, including high-quality machinery, high recovery rates and high material quality, and gives small communities the option to process material within their towns, thereby decreasing their hauling costs.
Sonoco Recycling President Ray Howard says the company’s new McMRF is one of Sonoco’s smaller sorting systems. “CP Group helped us design and build this system. No one else wanted to come into the small communities and put in a full-scale MRF like this,” Howard says. “What you see today is a system that can handle up to 3,000 tons a month—it is different, it is new and it is doing a great job. It’s cleaner, it is modernized and it is a state-of-the-art facility.”
The CP Group describes the McMRF as “an affordable compact solution that can fit into a 20,000-square-foot building.” According to the company, it is capable of achieving a 95 to 98 percent recovery rate and can be operated using a compact wheel loader and a forklift.
“The McMRF is modular in design with field proven equipment and our latest advances in machinery. It is easy to operate and delivers the best material separation,” says John Kemp, director of field services, CP Group.
The CP Group consists of CP Manufacturing, Krause Manufacturing, MSS, IPS Balers and Advanced MRF. The company designs, builds and installs material recovery facilities for various applications.
Film Producer Installs Plastics Recycling System
The Engineered Films division of Raven Industries, Sioux Falls, S.D., has installed a new reclaim production line designed to capture and recycle excess polymer material from its internal manufacturing processes. The reclaim line is capable of producing up to 15 million pounds of reprocessed resin pellets per year.
The Raven Engineered Films division makes “high-performance plastic films and sheeting [including] engineered geomembranes that provide critical protection of environmental resources through containment linings and coverings serving the energy, agriculture, construction, environmental and industrial markets,” according to the Raven Industries website.
According to the company, the design contains a specific line filtering system for the removal of foreign materials from the melt stream, which allows for the complete quality control of all materials produced.
Raven says it teamed up with consultants for the design and procurement of the reclamation system, electing to work with companies such as ADG Solutions, Fairfield, Conn., and Davis Standard LLC, Fulton, N.Y., because of their experience in reclaim automation systems.
“The installation of this advanced system achieves a closed-loop recycling stream for our manufacturing facility by reclaiming excess production material through a fully controlled process from start to finish,” says Anthony Schmidt, vice president and general manager for Raven Industries Engineered Films division. “Additionally, the reclaim line achieves a critical step in implementing actions directly aligned with Raven Industries’ sustainability initiatives, by reducing product waste and municipal landfill consumption.”
Excess polymer materials are generated during the normal production process through line startups and material edge trim processes, according to Raven Industries. The company’s past practices have included transporting this material to external reclaim facilities for reuse and discarding other nonreclaim materials. With the new system, however, the vast majority of excess material is captured and reclaimed within the Raven Industries facility, the company says.
Danish City Deploys Eldan Cable Recycling Plant
The city of Faaborg-Midtfyn, Denmark, has chosen Eldan Recycling A/S to provide it with a cable recycling plant. The first machine of its recycling system, a Micro Module, was installed in the beginning of 2012 and has subsequently been running at full production. Eldan is based in nearby Faaborg, Denmark.
In November 2012 the second machine, a Rasper R400-3, was delivered and installed to work in tandem with the Micro Module, according to a news release from Eldan.
“The modular approach is one of our trademarks,” says Flemming Hansen, Eldan’s product manager. “It gives our customers [the] possibility to gradually grow their business, as we see at the municipality of Faaborg-Midtfyn. The Rasper R400-3 will increase capacity and make it possible to process larger cables.”
Hansen adds, “We are very proud to have the municipality of Faaborg-Midtfyn as one of our new customers as they are situated in the same geographic area as Eldan Recycling.”
Jes Knudsen, CFO of Faaborg-Midtfyn, says, “Investing in this cable recycling plant is a way to benefit from our internal competence within waste management since we see a profitable business within the recycling industry.
“Eldan Recycling is well-experienced and also a local organization that we [have] know[n] for many years. We have high expectations on the reliability of the equipment and look forward to start processing cables at full capacity,” he adds.
The cable recycling plant processes dry cables collected from building and restoration projects in the city, with the output sold to scrap metal recyclers. The recycling plant’s processing capacity will be up to about 880 pounds per production hour, according to Eldan.
Since 1956 Eldan Recycling has been involved in developing machinery and methods for recycling tires, cables and electronic scrap. Since its founding, the company has built and installed more than 830 plants and 7,100 single machines. More information is available at www.eldan-recycling.com.
Advanced Equipment Sales Updates Website
Sauderton, Pa.-based Advanced Equipment Sales (AES) has launched its new website, www.advancedequipmentsales.com.
According to AES, the revamped site features a contemporary design, new content and an improved customer interface.
The company’s full product line, from balers and shredders to turn-key recycling and sorting systems, can be viewed on the Equipment and Systems pages. The Used Equipment section is organized by equipment type. A click on the product image provides more detailed information, including downloadable and printable specification sheets in PDF format.
The website’s new Service and Parts section allows customers to request quotes or to order service, parts and baling wire. An interactive “Contact Us” form is accessible from every page.
Zimmer America and Stadler Partner to Form Stadler America LLC
Zimmer America of Spartanburg, S.C., and Stadler, based in Altshausen, Germany, have partnered to form Stadler America LLC, based at Zimmer America’s corporate headquarters.
Zimmer America is a supplier of machinery and sorting systems for the textile, recycling, industrial cleaning and solar power industries, while Stadler is a manufacturer of sorting systems for the waste and recycling industry.
“To partner with Zimmer America is the best thing we could have done to get a strong foothold in the American marketplace,” says Gerben Nijland, Stadler America vice president of sales for North America. “We can now offer complete and local engineering and sourcing for our customers who are interested in complete Stadler MRF (material recovery facility) or PRF (packaging recovery facility) solutions, commingled recycling lines and all other Stadler products for the waste recycling industry.”
Nijland and his family relocated to Spartanburg from Germany last November.
“We are proud to have formed this partnership with Stadler in Germany, a very strong and stable company in existence since 1791 and a world leader in waste recycling solutions,” says Roland Zimmer, CEO of Zimmer America and Stadler America. “This will allow us to expand our activities in this industry and become a major player in the North American marketplace.”
NexGen to Design, Install MRF in Oklahoma
The equipment company NexGen, Vernon, Ala., and United Engines, its dealer, have partnered to design and install $7 million in upgrades for American Waste Control’s (AWC’s) material recovery facility (MRF) in Tulsa, Okla.
NexGen says it was chosen by AWC for the project based on its experience in designing and building turn-key MRFs as well as its ability to offer a comprehensive equipment package from curbside collection to material processing, including balers, conveyors and compactors.
AWC’s existing facility will be upgraded to a fully automated single-stream recycling operation, which will allow for easier recycling of a wider variety of recyclables, such as cardboard, paper, aluminum, plastic and glass. The MRF currently processes 125 tons of recyclables per day. After the upgrade, NexGen says the MRF will be able to process 200 tons per day of recyclables once a 24-hour/six-day-per-week schedule is implemented.
AWC owns Tulsa Recycle and Transfer and American Environmental Landfill, which NexGen says is the only licensed hybrid MRF in Oklahoma. The 117,000-square-foot facility has a total investment of $10 million, including system, building and grounds.
The NexGen design replaces an almost entirely manual process with dozens of automatic sorting points, magnets, optical sorters and air classifiers.
US Shredder and Castings Group Joins the Bureau of International Recycling
The U.S. Shredder and Castings Group, Trussville, Ala., announced it has become a member of the Bureau of International Recycling (BIR), headquartered in Brussels.
The BIR is a global recycling industry association representing more than 850 companies and 40 affiliated federations from 70 different countries.
“We have been active supporters of ISRI (Institute of Scrap Recycling Industries Inc.) and many of its local chapters since we started the company,” says U.S. Shredder President Bill Tigner. “Our advance and progress into South America, Europe, India and the Middle East made it a logical progression for us to become a member of the BIR. We look forward to working with the organization to support the recycling industry worldwide.”
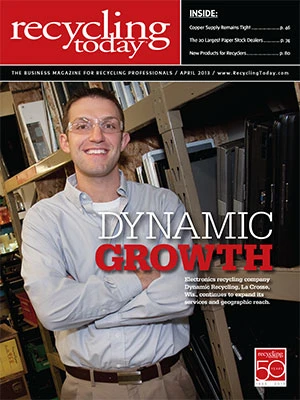
Explore the April 2013 Issue
Check out more from this issue and find your next story to read.
Latest from Recycling Today
- Unifi launches Repreve with Ciclo technology
- Fenix Parts acquires Assured Auto Parts
- PTR appoints new VP of independent hauler sales
- Updated: Grede to close Alabama foundry
- Leadpoint VP of recycling retires
- Study looks at potential impact of chemical recycling on global plastic pollution
- Foreign Pollution Fee Act addresses unfair trade practices of nonmarket economies
- GFL opens new MRF in Edmonton, Alberta