As the recycling industry continues to grow and advance, so too has the equipment that operators use on a daily basis. Equipment manufacturers have introduced machines that can process additional types of materials; that feature a two-in-one tool; that are firsts for the industry; and companies have even created new lines, such as St. Louis-based American Pulverizer Co.’s launch of a preshredder line.
Recycling Today regularly brings you information on new and updated products in our monthly Product Spotlight. We have compiled a number of products that ran in this department over the last year. Their descriptions and features follow.
American Pulverizer preshredder line
American Pulverizer Co., based in St. Louis, has developed a line of dual-shaft hydraulically powered prerippers designed for pulling apart UBC (used beverage cans) bundles and aluminum siding and sheet at rates of up to 30 tons per hour, the company says.
The preshredders can be grapple or conveyor fed. The low-speed, high-torque machines consist of two opposing rolls with large ripping teeth, American Pulverizer says. A large clearance between the rows of teeth is designed to accommodate infeed material, and the differential speeds allow the teeth to rip and shred material.
According to American Pulverizer, the slow speed of the preshredders reduces fines generation. The preshredders are designed to produce material ideal for processing in secondary machines to achieve a product for melting purposes.
More information is available from AmericanPulverizer at www.ampulverizer.com or at 314-781-6100. Callers should ask for brochure No. BLB-14.
Artec modular plastic recycling system
New from Zimmer America, Cowpens, South Carolina, is a modular plastic recycling system made by Artec Machinery GmbH of Austria. The system produces granulate from film, fiber and polymer foam waste. Zimmer America says it also can process agricultural film as well as trimmings from postindustrial new film production or PET (polyethylene terephthalate) packaging. The modular machine concept makes it easier to design a recycling system that conforms to the input material quality and desired output quantities, the company says. The system features six modules, including material feeding, cutter-compacting, extruding, degassing, filtration and pelletizing functions.
The company says the material feeding module includes a metal detector; the cutter-compactor allows for the agglomeration and predrying of the input material; and the degassing module is for the elimination of gaseous contamination, such as low-molecular plastic fractions or moisture.
Additionally, a remote display is available, which allows the operator to walk around the machine to facilitate startup and production supervision, according to Artec.
Capable of producing at a range of capacities, the modular plastic recycling system can produce from 200 kilograms (440 pounds) to 2,500 kilograms (5,510 pounds) per hour, Zimmer says.
Visit www.zimmer-usa.com for more information.
Columbus McKinnon hybrid primary shredder
New from CM Tire Recycling, a Columbus McKinnon brand based in Sarasota, Florida, is the CM Hybrid primary shredder, developed for multiple applications, including the production of tire-derived fuel (TDF). CM says the shredder is considered a hybrid because it uses removable rotor technology.
The shredder offers the CM Secure Lock system, a new knife group locking technology and advanced bearing protection in which bearings are located outside of the shredding envelope, the company explains. The CM Hybrid primary shredder comes with standard CM knives or new CM shear blades.
The machine’s interchangeable cutting options create a multitude of cutting configurations by being able to swap out different size knives and shear blades for larger or smaller cuts. The company says its shredders are built using the patented Holman Knife Design, which CM says produces clean cut TDF chips.
The shredder is equipped with twin 75-horsepower motors.
Columbus McKinnon Corp. is a designer, manufacturer and marketer of material handling products headquartered in Amherst, New York.
Visit CM Tire Recycling’s website at www.cmtirerecyclingequipment.com for more information.
Doosan material handlers
The equipment company Doosan Infracore Construction Equipment America, West Fargo, North Dakota, has introduced three material handlers and four-tine grapples. The first model being launched is the DX225MH-3 material handler. Doosan says additional material handlers will include the DX300MH-5, a larger model with steel tracks, and the DX210WMH, a wheeled model.
Doosan says the new material handlers are being built specifically for material sorting and handling applications. Previously, dealers converted Doosan crawler excavators or wheel excavators into material handling machines, according to the company.
Doosan says its material handlers were developed in-house to meet the demands of material handling. Each model is based on a tested excavator model and is factory-fitted with cab risers for increased visibility, the company says. Other features include a straight boom and droop nose arm designed for improved reach, lift height and placement, as well as improved machine guarding, the company says. Dual-boom cylinders and under-mount arm cylinder placement are intended to provide improved lifting capabilities, Doosan says.
The company reports that its cab riser is designed to provide better all-around visibility to the attachment and work area. Standard fixed risers for the DX225MH-3 are 4 feet, and 6 feet for the larger DX300MH-5. A 6-foot fixed riser is available as an option on the DX225MH-3. Doosan says the fixed risers can be lowered easily for transport with a self-contained, electronically powered hydraulic system.
Available as an option for the DX225MH-3 and DX300MH-5 is a 6.5-foot hydraulic cab riser, which is standard equipment for the DX210WMH.
To maximize the versatility and productivity of the material handlers, Doosan says the new equipment can be paired with a grapple for material handling applications. The 360-degree hydraulic rotating four-tine grapples feature a semiclosed tine design for a firm grasp on most materials, Doosan says. The tines are constructed with AR400 high-strength, abrasion-resistant steel for increased durability, and the tine tips are replaceable for easier maintenance.
A 5/8-cubic-yard grapple is approved for use with the DX210WMH and the DX225MH-3, while a 1-cubic-yard grapple is approved for use with the DX300MH-5.
Four power modes are available for the Doosan DX225MH-3 and DX300MH-5 material handlers to help operators manage the balance of fuel consumption and machine power to the working conditions, Doosan says.
In addition to the power modes, the Doosan DX225MH-3 and DX300MH-5 material handlers offer a lifting work mode providing increased pump torque, low engine RPM and an automatic power boost, Doosan says.
Visit www.doosanequipment.com for more information.
Eagle tire debeader
Eagle International, based in Dakota Dunes, South Dakota, has introduced the OTR Debeader for tire recyclers handling off-the-road (OTR) tires. The company says the OTR Debeader has been built, proven and engineered to complete the specific task of pulling bead bundles from OTR tires. Eagle says this machine is the only one of its type in the world capable of pulling bead bundles from all sizes of radial OTR tires.
To remove the bead bundles, Eagle explains that the tires are lifted onto the machine and are entirely contained for safety. The debeader is capable of running up to eight tires an hour through production, Eagle says.
The company points out that the OTR Debeader was designed based on customer requests. Eagle says recovered steel also can add to recyclers’ revenue streams.
Visit www.eagle-equipment.com for more information.
General Kinematics high- stroke vibratory screen
General Kinematics (GK), a vibratory equipment manufacturer based in Crystal Lake, Illinois, has introduced the SXS screen, which it says is the first of its kind in the industry. GK says the side-by-side screen is engineered to move less-dense, soft materials that typically do not convey or screen well.
The screen was developed for municipal solid waste (MSW), single-stream and commercial and industrial (C&I) materials, but GK adds many other kinds of materials also can be screened. The high stroke transmits more energy into the materials for faster travel speed and better separation, resulting in improved recovery, according to the company.
The SXS offers lower operating costs and uses up to two-thirds less horsepower than standard machines, according to GK. It also comes with the company’s service and support program.
The first unit was installed in September 2014, the company says.
More information can be obtained by contacting GK Resource Recovery Industry Manager Dick Reeves at 815-455-3222 or at mail@generalkinematics.com or by visiting www.gkrecycling.com.
Herbold plastic pipe shredders
Herbold Meckesheim USA, based in Slatersville, Rhode Island, has introduced its HOS heavy-duty pipe shredders. The company says the pipe shredders are designed to reduce large, thick-walled plastic pipes to chips about 2.4 to 3.9 inches square.
A high-torque hydraulic ram holds a horizontally oriented pipe against a moving cutting plate that is studded with blades, the company explains. As the vertical cutting plate travels back and forth across the end of the pipe, it slices off chips. The chips then fall onto a conveyor belt, which can transport them to a cutting mill for further size reduction, Herbold describes.
The grater-like design means the blades of an HOS shredder wear much more slowly than those of a typical heavy-duty pipe granulator and the unit uses less energy and requires less maintenance as a result, according to the company. HOS shredders are even suitable for various abrasive materials, such as fiberglass-reinforced piping. The pipe shredders produce little noise, and each model is equipped with a covered feed trough, the company adds.
Available in five sizes, the shredders can process up to 3,400 pounds per hour and can handle pipes as large as 9.8 feet in diameter.
Herbold Meckesheim USA, a subsidiary of Herbold Meckesheim Germany, designs, manufactures and installs size reduction equipment and wash-line systems for the plastics industry. The company specializes in the recycling of industrial and postconsumer plastics.
Visit www.herboldusa.com or contact David Lefrancois, president, Herbold Meckesheim USA at 401-597-5500 or at info@herboldusa.com for more information.
Javelin Manufacturing ECS mobile recovery unit
Javelin Manufacturing, a Fort Wayne, Indiana-based producer of eddy current separators (ECS), has introduced the Javelin ECS mobile recovery unit, which it says solves problems that arise from equipment outages and location restrictions.
The company says the mobile recovery unit has the same features as the standard Javelin ECS with enhanced portability and can be used in nearly any capacity. The unit is capable of handling material sizes ranging from 0.5 inch to 5 inches. A Javelin ECS mobile recovery unit can be custom tailored to fit the needs of an operation, according to the company.
Systems options include a feed system with a drum or vibratory feeder, discharge conveyors and integrated Javelin ECS units. Customers can choose different gauss and pole setups in the ECS, as well as different feeding and collection methods.
Javelin ECS mobile recovery units can be used to remove ferrous and nonferrous materials in C&D (construction and demolition) applications or during equipment outages. They offer all weather operation and can aid in stockpile reduction. The units can be set up for long- and short-throw applications.
The company says the mobile recovery unit does not require a concrete slab for stability and can be used with ground power or a generator.
More information and videos are available at www.javelin-mfg.com.
Moley Magnetics Claw Magnet
Moley Magnetics, Buffalo, New York, has introduced the Moley Claw Magnet, described as a two-in-one tool for ferrous scrap recyclers.
According to Moley, the Claw Magnet is a fully enclosed hydraulic scrap magnet with two sets of claws. The company says the “robust and heavy-duty magnet [is] ideally suited for the demolition and scrap industry.”
The Claw Magnet comes in sizes ranging from 32 inches to 60 inches. The attachments consist of a “powerful and efficient magnet [and] extended scraping claws,” according to Moley. The claws can loosen up dirt, gravel and other debris, allowing access to clean metal pieces.
In addition to the Claw Magnet, Moley Magnetics Inc., a 20-year-old company, makes and supplies what it calls a complete inventory of electromagnets and accessories such as magnets, shears, grapples and track pads.
More information about the Claw Magnet can be found at www.moleymagneticsinc.com/moley-claw-magnet.
Olympus Delta Element handheld XRF analyzer
Olympus Corp., with U.S. offices in Waltham, Massachusetts, has released its new handheld X-ray fluorescence (XRF) analyzer that the company says is ideal for scrap metal sorting. The analyzer also is suitable for positive material identification, alloy quality assurance/control and precious metals analysis.
Olympus says the XRF analyzer incorporates the features and design of the Delta family with fast elemental ID for screening, sorting and metal analysis. The analyzer also features Grade Match Messaging for streamlined operations.
Visit www.olympus-IMS.com/element for more information on the analyzer.
Shred-Tech stationary single-rotor shredders
The new STS line of single-rotor shredders from Shred-Tech, Cambridge, Ontario, is now available in several sizes ranging from 24 inches to 120 inches in width with numerous drive options from 25 to 600 horsepower. Each STS shredder is designed to control shred size at high levels of throughput and is reinforced with all welded construction to maximize durability, according to Shred-Tech.
To improve reliability, Shred-Tech says all of the bearings and seals have been mounted outboard of the cutting chamber to avoid contamination. The units also feature a two-speed ram to maximize processing efficiency, the company says.
Numerous screen sizes are available and each machine can be designed into a complete system or used as a standalone shredder.
Shred-Tech is a leader in engineered reduction technology and solutions, designing and manufacturing shredding and recycling systems. The company builds solutions for many industries and applications, including tire and rubber, MSW, plastics, e-waste, wood, metals, C&D debris, medical and hazardous waste, military, off-spec products and secure document destruction.
More information is available from Shred-Tech at 800-465-3214, at www.shred-tech.com or at shred@shred-tech.com.
Steinert induction sorting system with Argos C technology
The equipment company Steinert, based in Cologne, Germany, with a U.S. office in Walton, Kentucky, has introduced its Fines ISS (induction sorting system) with Argos C technology to the recycling industry. The company notes that the system allows users to extract metals that are smaller than 3/8-inches in size.
Steinert adds that it developed the fines sorting system in cooperation with its customers and that interest in the system is strong because it offers users the ability to extract more copper from auto shredder residue (ASR). Recent system installations show that even a 1 percent increase in metal recovery with the Steinert Fines ISS will lead to a much quicker return on investment, according to the company
In research Steinert conducted, it found that the typical product extracted with the Steinert Fines ISS includes up to 80 percent of small bare and insulated copper wire not traditionally detectable with other systems found in the market.
The Steinert Fines ISS combines two new technologies—the Argos C inductive sensor and a bullet-type valve bar—to separate fine metals, according to the company:
Both the new Argos C sensor and the bullet-type valve bar are connected through a control panel, allowing for a large variety of signal-based information to be processed, Steinert says. The design, Steinert says, guarantees results in terms of recovery and purity with sensitivity and selectivity for customers.
While the initial success of the first Steinert Fines ISS sensor sorters started within the ASR industry, Steinert says the system has been incorporated in a range of other fields including waste to energy, metal processing from bottom ash and plastic scrap processing.
The Steinert Fines ISS is available in working widths of 40 inches and 80 inches.
For more information on the system, visit www.steinertglobal.com.
ZenRobotics sorting system
ZenRobotics Ltd., headquartered in Helsinki, Finland, has introduced a fully renewed robotic waste sorting system as an additional robotic recycling method. The Next Generation ZenRobotics Recycler (ZRR) doubles the capacity of the company’s first robotic heavy waste sorting system, which ZenRobotics launched in 2012.
ZenRobotics says the Next Generation ZRR incorporates the speed of its previous ZRR Fast Picker model and the strength of the company’s previous ZRR Heavy Picker—all in a multipurpose solution.
“During the past year, we have focused on dramatically improving both the speed and the capacity. We have developed new hardware that enables fully automated waste sorting. Now we are breaking speed records all the time,” says ZenRobotics CEO Timo Taalas.
Taalas says the Next Generation ZRR can sort on average 3,000 picks per hour, with a peak sorting speed of up to 4,000 picks per hour.
The updated system also includes a new gripper that can pick up bigger and heavier objects compared with its previous model, according to the company. With the new waste sorting system, ZenRobotics says fractions up to 50 centimeters (19.5 inches) wide and 20 kilograms (44 pounds) in weight can be sorted.
ZenRobotics says the Next Generation ZRR is ideally suited for a demanding heavy waste processing environment, including sorting heavy and large fractions in the C&D sector.
For more information, contact Taalas at ttaalas@zenrobotics.com.
The author is associate editor of Recycling Today and can be contacted at mworkman@gie.net.
Get curated news on YOUR industry.
Enter your email to receive our newsletters.
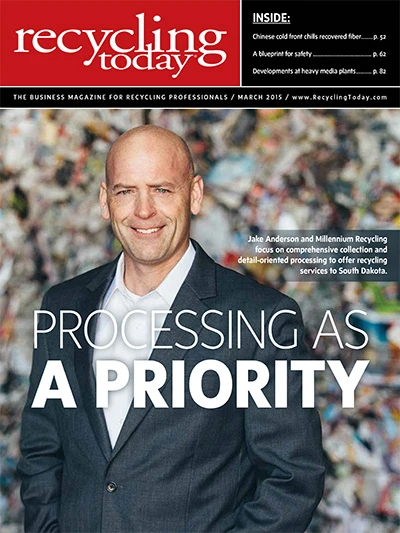
Explore the March 2015 Issue
Check out more from this issue and find your next story to read.
Latest from Recycling Today
- CP Group announces new senior vice president
- APR publishes Design Guide in French
- AmSty recorded first sales of PolyRenew Styrene in 2024
- PRE says EU’s plastic recycling industry at a breaking point
- Call2Recycle Canada, Staples Professional expand partnership
- Circular Services breaks ground on north Texas MRF
- Tariff uncertainty results in choppy nonferrous scrap flows
- CATL, Ellen MacArthur Foundation establish battery partnership