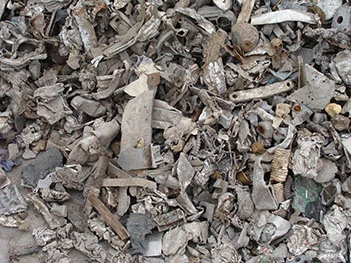
2015 by all accounts could be a tough year for the scrap metals market. With metals prices down virtually across the board, processors are increasingly looking to improve the recovery of their higher-priced products—the nonferrous metals—for profit potential.
While equipment purchases could be a tough sell in 2015, recyclers at all levels of the processing chain say this side of the business deserves at the very least more scrutiny if not outright investments in upgraded processes.
Upgrades for aluminum
Zorba, the aluminum-heavy scrap grade typically created through eddy current separation, is by volume the largest nonferrous product from auto shredding plants. But zorba still requires further separation before it can be used by a secondary smelter. This is often done domestically by the numerous companies with heavy media plants designed to recover the aluminum using sink/float tanks to separate aluminum from the heavier metals, such as copper, lead, stainless steel, brass and zinc.
An alternative strategy is to sell zorba on the export market to buyers most often located in China or other parts of Asia. But that market has suffered from lower prices and the lasting effects of China’s Operation Green Fence, a governmental crackdown on the quality of incoming scrap shipments, which officially called for “zorba 98,” or 98 percent metal content, some recyclers say.
David Wallace, senior vice president of Huron Valley Steel Corp., a zorba processor and heavy media plant operator based in Trenton, Michigan, says at the present, “China is still our most significant competitor for the purchase of zorba.” He points out that China’s import requirement calling for zorba 98 never really affected the domestic availability of zorba because the 98 percent requirement was rarely enforced, save for a limitation on the presence of circuit boards.
“There does seem to be more zorba available domestically in the last 12 months than previously,” Wallace says, “but that’s probably attributable to the general economic slowdown in China, rather than the Green Fence requirements.”
What about the plastics? Scott Newell, CEO of The Shredder Co., Canutillo, Texas, says that while there has been more interest in recovering the plastic portion of auto shredder residue (ASR), more of the progress in this area has occurred in Europe, where the European Union has mandated and subsidized the recycling or recovery of 95 percent of end-of-life vehicles, beginning in 2015. Recovering plastics from ASR using dense media separation or some other technology seems to be a task that current science would allow. The economic viability, however, remains unclear. Then there’s the federal restriction that also has muddied the waters, at least in years past. Here in the States, the recycling of plastics from ASR was forbidden by the U.S. Environmental Protection Agency up until last year. In light of that recent change, it’s a science that by many accounts remains in its infancy. “I don’t know of anyone in the U.S. who is currently doing that on an economic basis,” Newell says. Jeffry Gertler, co-founder of the Chicago-based recycling company Scrap Metal Services LLC, is currently upgrading his heavy media plant to provide cleaner products, but those changes are focused on metals, he says, and the company isn’t too interested in recovering ASR plastics presently. Still, he concedes the companies that operate megashredders might be interested in that. Meanwhile, Bobby Triesch of PlasMet LLP, based in Atlanta, draws a link between oil prices and plastics that are made from oil. Presently, he says, with oil prices near $55 per barrel, recovering plastics from ASR seems to make little business sense. “When it was $100, it was a little more interesting to recover plastics. With oil at $50, it’s not nearly as lucrative,” he says. |
Wallace says shredder operators and recyclers have always been trying to increase metal recovery, at least in terms of zorba. “Since 2000, many have added high-tech, downstream systems to upgrade their zorba products to a higher metallic content in order to take advantage of the export market.” But he says lately Chinese buyers aren’t paying what they were for zorba, perhaps in light of increased labor costs in the country. Meanwhile, the domestic availability of zorba also has declined because shredder output in North America has decreased. Regardless of availability, Wallace says Huron Valley continues to price its zorba based on expected metallic recovery.
Meanwhile, Bob Stein of St. Louis-based Alter Trading agrees that zorba prices are down at the moment, reflecting lower prices for the various base metals that are included in zorba. But the drop in prices doesn’t mean zorba markets are weak, he adds. Stein says the softness in prices for zorba should correct itself, particularly where aluminum is concerned.
“We anticipate there’s no sense of permanency to these lower values now,” he says. “The auto industry is doing well, the American economy is incredible, so zorba is not going to zero.”
Meanwhile, Scott Newell Jr., CEO of The Shredder Co., Canutillo, Texas, says presently the strength of the dollar is causing problems in terms of the demand for zorba from export markets.
When it comes to twitch, the resulting higher-content aluminum product commonly produced from dense-media-plant separation, Stein says recyclers are encouraged to add technology or processes to produce material to this specification depending entirely on the market and its value. “The market is going to determine when, where and how. It’s not an automatic.” He says, for example, a year ago the twitch grade earned a premium in the market, causing more recyclers to consider operational changes. These days, though, that premium has dissolved.
Newell says recyclers have the ability to make zorba 98, as well as twitch, but it’s a complicated issue. “The question is, how much material are you going to lose?” He says adjusting eddy current separators to sort for cleaner metal may lead to losses. Many recyclers in turn may choose to account for that by rerunning material. “That’s how they get to the 98,” he says.
On the other hand, Newell says domestic buyers of zorba are happy to receive material with 88 to 92 percent metal content to feed their density separation processes. Currently, he says, with export markets on the slower side, more recyclers are selling zorba to domestic processors with heavy media plants, who in turn produce twitch for sale domestically, as well as the heavier mixed metal products, such as zebra.
Newell comments that most of the twitch and stainless steel produced in this way, and a large portion of the copper, are purchased domestically.
Meanwhile, Jeffry Gertler, co-founder of Chicago-based Scrap Metal Services LLC (SMS), which operates a heavy media plant in Blue Island, Illinois, says the company in early 2015 is in the midst of completing a system upgrade designed to provide cleaner material as well as better separation of the various grades it produces.
According to Gertler, around 90 percent of the company’s end products are purchased domestically. Besides yielding a cleaner twitch product, Gertler says, the upgrade also delivers more efficient operations and lower operating costs. Though he won’t disclose how this higher-tech process works, Gertler says the new equipment doesn’t replace the company’s current process, and he acknowledges that copper is among the metals being targeted.
“Any business sorting metals today needs to have the best updated technology in order to get the best recovery possible to upgrade your product,” he remarks.
SMS operates four shredders, with three in the Midwest and one in Texas.
Copper and stainless
The mixed nonferrous metals remaining with the materials stream after eddy current separation may be further processed to cull the sensor-sorted zurik grade (primarily stainless steel). Others are continuing to mine the auto shredder residue (ASR) for any remaining metal.
One metals broker, who preferred to remain anonymous, questions if the shredded mixed metals product, whether produced by sensor-sorting or by heavy media process, still requires further sorting.
“For the most part, zurik is still a heterogenous material and there is a degree of randomness with the end product,” he says. All the nonmetallic debris might have been removed from it, he says, but the mix of metals may be something that “no metallurgist can relate to,” he says. What’s more, he adds, the next batch will be different depending on what has been shredded.
Bobby Triesch of PlasMet LLP, based in Atlanta, says the mixed zebra fraction, a media plant product, in his experience is usually exported. The company runs heavy media plants to produce twitch and zebra, which is the mixed stainless and red metals fraction, a heavy metals mix requiring further processing. He says much of that work is currently not done domestically.
“That’s a perfect product for Asia, so they buy almost all of that from everyone,” he says. “They are willing to pay more, sometimes, than the intrinsic value.”
He adds that buyers importing zebra are often able to bring in these mixed metals products without being subjected to the duties levied on imported virgin metals.
“They like to buy lower-value products and use their own internal labor to add value through separation,” he says.
Triesch says PlasMet considered purchasing separation equipment for this mixed metal product around a decade ago, but the high prices it commanded at the time convinced the company otherwise.
But, in recent months, Triesch says, as import business has slowed and scrap prices have fallen in sync with other commodities, such as primary steel and aluminum, the consensus could be changing once again.
Inspecting the fluff
If the newest installations are any indication, recyclers are now striving to capture the metals not recovered after eddy current separation.
For example Cincinnati-based Garden Street Iron and Metal installed a new shredder and downstream recovery system about a year ago. Owner Earl Weber says any metallics remaining in the fluff are less than a few percent.
Recyclers without newer systems may be losing a significant amount of metallics. On that point, Newell says quite a bit of nonferrous metal—including copper and stainless steel—isn’t being collected by the typical system. Instead, Newell says, much of it gets thrown away in ASR.
Newell says scrap metals recyclers are likely to continue investing in more sorting systems and technologies to recover more metals from fluff. “I think there’s enough value that’s being thrown away that the economic incentive will be to have more investment in that area,” he states.
The author is managing editor of Recycling Today Global Edition and can be reached at lmckenna@gie.net.
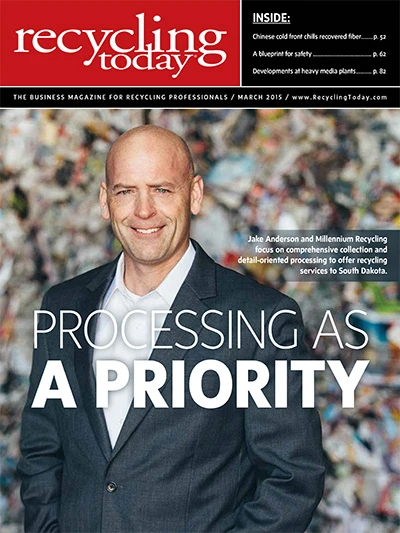
Explore the March 2015 Issue
Check out more from this issue and find your next story to read.
Latest from Recycling Today
- Recycled steel price crosses $500 per ton threshold
- Smithers report looks at PCR plastic’s near-term prospects
- Plastics association quantifies US-EU trade dispute impacts
- Nucor expects slimmer profits in early 2025
- CP Group announces new senior vice president
- APR publishes Design Guide in French
- AmSty recorded first sales of PolyRenew Styrene in 2024
- PRE says EU’s plastic recycling industry at a breaking point