For years, communities have struggled to divert glass from landfills and to solve the glass recycling puzzle. Although glass is 100 percent recyclable and can be recycled repeatedly without affecting quality, challenges are associated with the material’s collection, contamination, transportation and marketability.
Technological advances, cost-sharing partnerships and increased demand for recycled glass may be the combination needed to create new opportunities for glass recycling in Tennessee.
According to Larry Christley, planning and financial assistance manager for the Tennessee Department of Environment and Conservation (TDEC), communities that divert glass from their landfills receive a dual advantage as it helps them reach the state’s required 25 percent waste reduction and recycling goal and, through cost avoidance, saves about $37 per ton in tipping fees. Therefore, to be more sustainable and ecologically sound, communities are rethinking strategies to keep glass out of landfills.
Sand and mulch
Tennessee’s Cumberland County chose an innovative approach to processing recycled glass. Their nonconventional strategy incorporates the use of the Andela Pulverizer, a glass crusher with advanced technology that crushes glass to 3/8 inch or less. The processed material can be screened to a fine, sandlike consistency or to a larger “mulch” size, with all paper labels and residue removed. The pulverized glass is angular in shape and has no sharp edges, which allows the glass sand and the glass mulch to be used safely for many different applications, including landscaping, road maintenance and as a raw material for making new products.
Facility operators hope to see their investment pay off by using the finely ground glass product as an additive to the mixture used in their road salting operation during icy conditions. Savings are realized by extending salt supplies, saving $75 dollars per ton of salt replaced.
A second product derived from the crushing process is larger sized glass mulch, which may be sold to the public for landscaping. Since crushing operations began, the rate of glass collection in Cumberland County has more than doubled. Initially the rate of glass collected was about 10 tons per week. The current rate averages more than 20 tons per week and continues to increase.
Tom Breeden, Cumberland County solid waste director, credits the acquisition of the Andela crusher as the main reason for this dramatic increase in the county’s glass collection and recycling rate. The county has been proactive in promoting the new system and glass recycling in general with the local newspaper, in radio ads and by adding glass recycling collection containers at its 14 convenience centers as well as at the main recycling center.
For every ton of glass recycled, Cumberland County saves its taxpayers $32.67 in tipping fees. At the county’s current glass collection and recycling rate, annual savings are about $32,000. Further, the crushed glass material is a marketable product that generates additional revenue for the county. The savings in landfill disposal costs, along with the revenue generated by the sale of the product, are projected to pay back the approximately $100,000 purchase cost of the Andela machine in about 18 months.
The county was recognized for its efforts when it was chosen as the recipient for the 2012 Governor’s Environmental Stewardship Award in the Materials Management category.
Counter culture
Virtuous Products Inc., a startup company near Knoxville, Tennessee, owned by Mark Wassenaar, has contracted with Cumberland County to purchase its recycled glass material for use in its green products.
Although Wassenaar is relatively new to the area, he has more than 45 years of manufacturing experience with commercial flooring, casual furniture and residential countertops.
The company uses crushed recycled glass in a proprietary process to manufacture items such as fire tables, vanity and countertops and decorative floor tiles. The crushed glass is purchased already separated into color groups including amber, white or clear, blue, aqua green and mixed. It is washed, cleaned and dried to prepare it for use in the process.
The mixture that is used to produce Virtuous Products’ “Sedonite” countertops contains approximately 53 percent cleaned, crushed postconsumer glass.
From on-site measurements to installation, the manufacturing process can be completed in about two weeks. The Sedonite countertops weigh approximately 14 pounds per square foot compared with 16 pounds per square foot for granite, which can be important when carrying them into homes.
Sedonite countertops are priced at about $60 per square foot, including installation, and are intended to compete with marble, granite and other high-end materials. A variety of colors and enhancements, such as mother of pearl, are available.
While the glass countertops are rated to withstand moderate temperatures as granite is, certain high-heat appliances are not recommended.
Silicone molds are available in a range of sizes with 8 feet diameters being standard. This offers flexibility to customers who need nontraditional products.
Sponsored Content
Labor that Works
With 25 years of experience, Leadpoint delivers cost-effective workforce solutions tailored to your needs. We handle the recruiting, hiring, training, and onboarding to deliver stable, productive, and safety-focused teams. Our commitment to safety and quality ensures peace of mind with a reliable workforce that helps you achieve your goals.
Funding solutions
In December 2012, TDEC provided awards of approximately $1.7 million in Recycling Equipment and Hub and Spoke grants for fiscal year 2013 projects to help reduce landfill waste in the state. The grants funded 18 projects through the state’s Solid Waste Management Fund to promote and increase recycling across Tennessee and to engage partnerships among counties and municipalities. Approximately $2.3 million in Recycling Equipment and Hub and Spoke grants were awarded for fiscal 2014.
The Recycling Equipment Grants cover key pieces of recycling equipment, including equipment to pulverize glass for market. The Hub and Spoke Grants can cover capital project costs that involve the purchase of property and property improvements that lead to the development and expansion of regional facilities to collect, transport and process recyclable material for multicounty areas or municipalities.
Innovative recycling technology, the efforts of savvy entrepreneurs such as Mark Wassenaar and determined citizens who choose to use recycled products provide the elements needed to save landfill space and to promote sustainability. Ultimately, they bring us closer to solving the glass recycling puzzle.
Harold W. Madison works in the Office of Sustainable Practices in the Tennessee Department of Environment and Conservation. He can be contacted via email at harold.w.madison@tn.gov.
Get curated news on YOUR industry.
Enter your email to receive our newsletters.
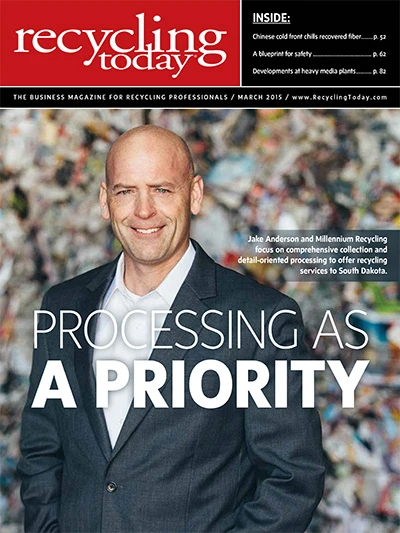
Explore the March 2015 Issue
Check out more from this issue and find your next story to read.
Latest from Recycling Today
- Two factors raise ferrous export questions in April
- Analyst: Scrap imbalance lost amid copper’s critical status
- AF&PA report shows decrease in packaging paper shipments
- GreenMantra names new CEO
- Agilyx says Styrenyx technology reduces carbon footprint in styrene production
- SABIC’s Trucircle PE used for greenhouse roofing
- Hydro to add wire rod casthouse in Norway
- Hindalco to invest in copper, aluminum business in India