Kingsport, Tennessee-based Eastman is a global specialty chemical company that produces a broad range of products that can be found in a number of everyday items. Its five business segments are additives and functional products, adhesives and plasticizers, advanced materials, fibers and specialty fluids and intermediates. According to the company’s website, www.eastman.com, Eastman’s portfolio of specialty businesses “works with customers to deliver innovative products and solutions while maintaining a commitment to safety and sustainability.”
Helping to lead the company’s initiatives in the area of sustainability is Anne Kilgore, director of sustainability, a role she has held since April 2009. Kilgore’s responsibilities include leading the development and implementation of the company’s sustainability vision, principles, goals and execution. The team that Kilgore heads links sustainability to Eastman’s and its customers’ strategies, external commitments and performance tracking.
It is a considerable job, as Eastman has more than 40 manufacturing locations and several sales offices around the globe employing 14,000 people.
In the Q&A that follows, Kilgore shares the goals and successes of Eastman’s sustainability program as well as her advice for companies seeking to decrease waste generation and for recycling firms that are helping their clients achieve more sustainable operations.
Recycling Today (RT): How does sustainability factor into Eastman Chemical’s operations? What are the overarching goals of your sustainability program?
Anne Kilgore (AK): At Eastman, sustainability serves as a lens for how we do business and encompasses the triple bottom line: environment, social and economic. Our approach to sustainability is crucial to the future success and growth of Eastman.
We define corporate sustainability goals to support each pillar of sustainability. For example, we are focused on innovating new, sustainably advantaged products that make the world a better place while driving improved energy efficiencies. We are also committed to making societal impacts in the neighborhoods where we operate.
Our overarching objective is to embed sustainability across the company and along the value chain. The corporate goals we have outlined in our sustainability report will continue to evolve as we meet our milestones and understand the growing needs of our changing world.
RT: Can you describe how your integrated manufacturing process plays a part in achieving your sustainability goals?
AK: Eastman’s integrated manufacturing process plays an integral role in achieving our sustainability goals, primarily in our efforts to reduce waste and improve energy efficiency. Integrated manufacturing results in highly efficient operations, allowing waste heat from one chemical process to be used for heat within a different chemical process. The process also provides greater opportunity to use materials and reduction in transportation of materials, thus resulting in reduced emissions across the supply chain.
RT: What impact has integrated manufacturing had on Eastman Chemical’s operations?
AK: Integrated manufacturing is critical to our expansive North American operations where we leverage large scale and vertical integration to make products that are not only used internally by other segments of the company but also sold externally to customers. The coal gasification process in Kingsport, Tennessee, as well as the cracking facilities in Longview, Texas, are major parts of our intermediates manufacturing, producing acetyls and olefins, which are key ingredients in other Eastman finished products.
RT: Can you tell me about your zero waste initiative in Ghent, Belgium? What aspects of this program related to waste reduction, reuse and recycling have you introduced to other facilities?
AK: Eastman’s Ghent manufacturing facility started the effort to minimize waste going to the landfill in 2009. Through a process of continuous improvement, the goal is for the facility to become “zero waste to landfill” wherever possible. It achieved this accomplishment in 2011 and has continued to maintain this status.
The site has implemented a number of processes and solutions to achieve this goal. For example, nonreusable wooden crates, which accounted for the most significant amount of waste, have been replaced with returnable metal containers. As a result of the program, waste costs at the site have been reduced by one-third.
Additionally, the Ghent Chamber of Commerce now uses the Eastman facility’s program as a model for other organizations to implement waste management practices. Ghent staff members participate in the training and provide practical advice to other area manufacturing facilities.
Consistent with our strategy in sharing positive sustainability practices across the company, we work to replicate successes like this at other Eastman manufacturing facilities. For instance, our Heat Mirror™ Insulated Glass plant in Chicago is in its second year of a waste reduction focus and is making strong progress toward achieving a zero-waste-to-landfill designation.
RT: Please tell me about the Eastman Recy-Pack™ and the benefits it provides?
AK: Eastman’s Recy-Pack™ packaging system was designed especially for our acetate yarn products, Eastman Estron™ and Eastman Chromspun™. This is a solid example of efforts Eastman is making in sustainable packaging.
Recy-Packs allow our customers to receive product in a protective package that is reusable and returnable, thus producing less waste. As reported in Eastman’s “2014 Sustainability Report,” it is estimated that Recy-Packs help to divert 12 kilograms (27 pounds) per case of cardboard packaging material from local landfills.
With the ability to reuse the packaging, the Recy-Pack trays have a potentially long life cycle, ensuring that Eastman acetate yarn customers can continue to protect the environment for years to come.
RT: What hurdles have you encountered in trying to reduce waste generation and how have you overcome them?
AK: It can be challenging to know where to start. As a Responsible Care® company (See the guiding principles for this program at http://bit.ly/16Gdp80.), Eastman has focused on waste reduction goals for years and uses six sigma projects, data monitoring and other mechanisms to identify the biggest improvement opportunities.
One example of a goal we are tracking is to reduce hazardous waste by 15 percent by 2020. Another goal relates to life cycle assessments (LCAs) and understanding the environmental impact of our products. We have a goal of completing life cycle assessments on all new product family launches this year—and to date we have completed cradle-to-gate LCAs on 74 percent of our top-selling product lines.
Having this type of information and knowledge about our products helps us further identify opportunities for waste reduction.
RT: What advice do you have for other companies that may be attempting to reduce waste generation in their manufacturing and shipping operations?
AK: For Eastman, having clear goals and engaging our employees has been a crucial component of success on waste management and reduction. Tapping teams of people with varying responsibilities and backgrounds can unearth some of the best and most effective ideas.
At Eastman, we have found that our employees often have new, innovative ideas that have helped us adjust and improve our operations to be more efficient and less wasteful. One example was featured in our “2014 Sustainability Report”—the Alternate Methods of Supply team—who work together to find better solutions to existing processes like 1) examining the life cycle of the transportation “legs” of suppliers across the globe to eliminate unnecessary shipments by truck, rail and ocean liners and 2) managing Eastman’s sale of byproducts and wide specification material to converters who recover and convert material into useful products that would otherwise become waste.
At Eastman, we appreciate the importance of collaborating with industry peers to discuss best practices and new approaches to waste management. For example, in 2012, Eastman organized the Full-Wrap Label Consortium, which is dedicated to improving the recycle stream. (Visit www.RecyclingToday.com/rt0714-shrink-labels-challenges.aspx for more information.) This industry group has grown over time, facilitating collaboration and improvement.
RT: What suggestions do you have for recyclers who are looking to help companies like yours meet their waste generation and recycling goals?
AK: It’s critical to understand our business—and what’s important to our customers and their businesses. At Eastman, we are focused on meeting the needs of our customers’ (and the end consumer). Our efforts—whether it is product innovation, streamlined production processes or reduced waste management—are all directed toward meeting our customers’ needs. It’s helpful for recyclers to understand our business, our customers’ needs and the importance they play in all that we do.
Anne Kilgore is director of global sustainability at Eastman, Kingsport, Tennessee. Visit www.eastman.com for more information.
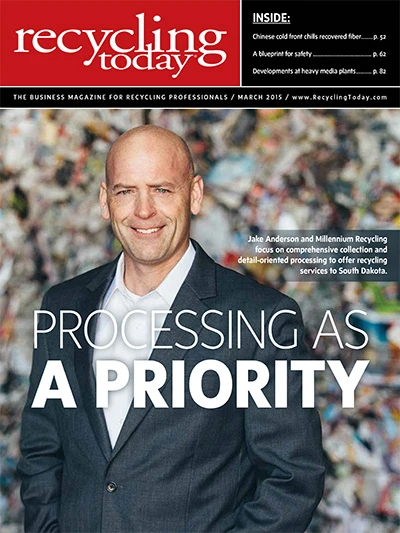
Explore the March 2015 Issue
Check out more from this issue and find your next story to read.
Latest from Recycling Today
- CP Group announces new senior vice president
- APR publishes Design Guide in French
- AmSty recorded first sales of PolyRenew Styrene in 2024
- PRE says EU’s plastic recycling industry at a breaking point
- Call2Recycle Canada, Staples Professional expand partnership
- Circular Services breaks ground on north Texas MRF
- Tariff uncertainty results in choppy nonferrous scrap flows
- CATL, Ellen MacArthur Foundation establish battery partnership