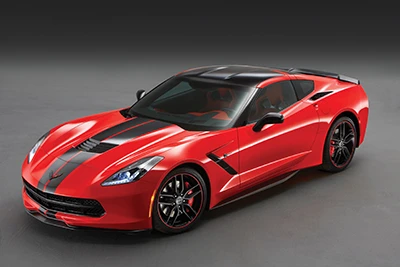
Auto recycling is a weighty business. Recyclers deal in pounds of copper, ounces of platinum, tons of ferrous scrap. Yet, while many things in America get bigger and heavier, vehicles are getting lighter.
Take, for example, the 2015 Ford F-150 pickup truck. It will be a full 700 pounds lighter than the current generation of F-150. The truck will not be shorter than the 2014 or 2013 models, nor will it be narrower. It will, however, include key components made of aluminum and not of steel.
“The frame of the new truck, like the old truck, is 100 percent steel, and in fact the new F-150 uses more high-strength steel than the existing truck,” Wes Sherwood of the Ford truck team says.
“The ratio of metal to plastic has not changed substantially overall, but we're moving toward lighter weight in general, using plastic, aluminum and high-strength steel,” explains Carrie Majeske, associate director of global sustainability integration for Ford Motor Co., Dearborn, Mich. “We’re also using recycled content or renewable content in plastics as reliable feedstreams become available.”
Other vehicles are moving away from traditional steel frames, as in the case of the Chevrolet Corvette Stingray, which was named 2014 Car of the Year at the North American Auto Show in Detroit in January. There is very little “traditional” material in this ‘Vette. It has a lightweight aluminum space frame that replaces the steel frame traditionally used on cars. Carbon-fiber and carbon nanocomposite structures reduce weight even further to achieve optimal handling and acceleration, according to General Motors Co., headquartered in Detroit.
Many microsize cars also are coming to market. Fiat is doing quite well with its 500 model. The Mini-Cooper, Chevy Spark, Ford Fiesta, Toyota Scion and the tiny Smart Coupe and other Smart Cars are all small, lightweight vehicles that will send many less pounds of material to scrap yards at the end of their useful lives. A Smart Car, for example, has a curb weight of 1,800 pounds. That is a fraction of what a standard car weighs. The Toyota Corolla, not a giant of a car by anyone’s standards, comes in a full half-ton heavier than the Smart Car, for instance.
That does not mean microsize cars necessarily will be easier to dismantle. The Smart Car, for example, has eight full-size air bags that need to be removed when a car is taken apart.
The new hybrid vehicles will present dismantling challenges of their, own as their battery power packs require special care when the car is disassembled.
Yet, traditional materials maintain their importance in 2015 vehicles. Lawrence Kavanagh, president of the Steel Market Development Institute (SMDI), Washington, D.C., maintains that most lightweighting is occurring with advanced high-strength steels (AHSS) and not with alternative materials. “We are now producing parts with AHSS equivalent in weight with aluminum,” he says.
Kavanagh, echoing Majeske, notes how much of the lightweighting of the F-150 results from the use of high-strength steel, not just from aluminum. “The frame is AHSS and accounted for a significant part of the lightweighting in the F150,” says Kavanagh.
“Many parts that were other materials are or will shift to steel,” he predicts.
Kavanagh says it will be difficult to measure the effect of one model on recycling operations.
“There are no recycling issues with AHSS,” he says, while adding that aluminum needs to be sorted and separated by grade before recycling.
Fuel driven
There is little question anywhere in the auto industry that lighter, cleaner cars are the future.
Majeske says, “Fuel economy, greenhouse gas and constituent emissions regulations are driving lightweighting and increases in hybrid and electric vehicle availability.”
Eric Mauk, corporate communications specialist for Honda North America, Marysville, Ohio, agrees. “The new standards will force all manufacturers to devise new ways to raise fuel economy,” he says. “Lightweighting throughout the entire vehicle will be a vital tool in getting better mileage.”
Smaller displacement engines and lighter but also stronger products will reduce vehicle weight while increasing safety, Mauk adds.
If any vehicle would appear immune to lightweighting because of worries about gas prices, it would be the Bentley Continental GT V-8. The GT is designed to zip from zero to 60 in 4.6 seconds and reaches a speed of just less than 200 mph. Still the manufacturer, Bentley Motors, based in Crewe, England, is trumpeting the vehicle’s new-found fuel efficiency. The company says its newest Continental GT model offers 40 percent better fuel efficiency than the previous model, despite weighing 6,063 pounds.
Futuristic materials are helping automakers shed weight. Munich-based BMW, for instance, managed to slim down its 2014 M3 by 176 pounds compared with last year’s model. Part of that weight reduction is thanks to a new carbon-fiber roof, which BMW included on its M3 sedan and M4 coupe.
Selling aluminum trucks
Every automobile manufacturer is lightweighting vehicles wherever possible. AHSS, aluminum and plastics are major factors in the lightweighting process. That said, the 2015 F-150 is a bit of a watershed. No matter the manufacturer, marketing for pickup trucks is often built around toughness and durability. People can crush aluminum cans on their foreheads, which means Ford may face a bit of a marketing challenge, no matter how strong the aluminum its using in its trucks is. For that reason, Ford says its promotions will continue to mention steel. The F-150’s ladder frames use high-strength steel with through-welded crossmembers.
While she had no firm metrics to make public, Majeske says, “We expect increased use of aluminum and plastics as means to achieve weight savings and improve fuel economy. The rate of increase will depend on costs of those materials compared to the costs of other fuel-saving technologies.”
Ford says it will use “military grade aluminum alloy” and high-strength steel in the F-150. The auto manufacturer says it will use the aluminum alloy in the cab, the cargo area and the tailgate.
The phrase “military grade” describes the use of aluminum alloys in consumer products that are in the same aluminum alloy family as those in military applications, Sherwood says. Therefore, the new F-150 uses several grades that are either the same or similar to alloys used in military vehicles, he adds.
“From its fully boxed, high-strength-steel frame to the use of high-strength, military-grade aluminum alloys in its body and bed, this F-150 takes tough to a whole new level,” Ford says. “Weighing in as much as 700 pounds less than its predecessor helps make this truck a whole lot more capable and more effective too. Plus, it accelerates, brakes and resists corrosion like never before. In addition, we standardized the chemistry of the aluminum alloy used in construction of the 2015 F-150 body and bed to facilitate recycling,” the automaker continues.
“Our aluminum scrap can be reclaimed and sent back into the manufacturing process to minimize waste,” Ford says.
However, aluminum could have a further impact on recyclers, especially those whose yards are in the Northeast or Midwest. Aluminum corrodes at a much slower rate than iron does. (By definition, aluminum does not “rust” but it does corrode.) That means many vehicles may be on the road longer before reaching scrap yards and end of life.
As already noted, the 2015 Ford F-150 does not feature aluminum exclusively at the expense of steel. The company will build the trucks with a compacted graphite iron block. This adds credence to the steel industry’s argument that the material is not going away any time soon when it comes to vehicle manufacturing.
“Steel is presently 60 percent of vehicle curb weight and has been for many years,” Kavanagh says.
He says there may be some fluctuation over the next three to four years as carmakers experiment, but Kavanagh adds that he does not see steel’s percentage falling anytime soon. “We expect to remain in this position into the next decade.”
Steel components
“The frame of the new truck, like the old truck, is 100 percent steel, and in fact the new F-150 uses more high-strength steel than the existing truck,” Sherwood says.
While Ford is proud that the body of the 2015 F-150 is made of a high-strength, military-grade aluminum alloy, the company will not release specific information about materials by weight or percentage, Sherwood says.
It did not take long after Ford announced that its 2015 F-150 would feature a 700-pound weight reduction (in large part because of the vehicle’s use of aluminum) before the SMDI had a riposte fall into its lap. In mid-January, the 2014 North American International Auto Show announced the winner of its North American Car and Truck/Utility of the Year in the truck category: the Chevrolet Silverado.
The truck, SMDI was quick to point out, features a significant amount of advanced high-strength steel, which offers significant lightweighting benefits at a lower cost than aluminum.
Car fans could see this as the next round in the classic Ford vs. Chevy battle.
According to General Motors, the Silverado’s updated frame, such as the main rails and major cross members, are made from high-strength steel. Further, the cab structures incorporate high-strength steel in the A-pillars, B-pillars, roof rails and rocker panels. Ultra-high-strength steel also is used in the rocker panels and underbody in anticipation of new shallow-offset crash tests. In all, about two-thirds of the cab structure is made from high-strength steels, GM says.
“It’s an exciting time in the automotive industry as automakers evaluate vehicle components for lightweighting potential to meet industry needs while also balancing customer preferences and safety expectations,” says Ron Krupitzer, vice president, automotive applications for SMDI. “It’s no surprise that in the case of the Silverado, those solutions were advanced steel. We congratulate and applaud General Motors on their noteworthy win and adaptation of new steel grades and processing technologies that reduce mass while maintaining strength and enhancing safety in a cost-effective and ecofriendly manner.”
No matter the material used, end of life is a major consideration for OEMs.
“Honda recognizes Life Cycle Assessment as a critical tool for understanding the impact of its products and operations on the environment,” Mauk says, adding that the company is working to minimize that impact in virtually every aspect of its business.
Honda says it is expanding its remanufactured parts offerings, removing them from the waste stream and reducing the resources needed to make new parts.
Recycling value proposition
Majeske says Ford continues to work to decrease its use of “substances of concern,” such as mercury, lead and cadmium, with a goal of clean feedstreams at a vehicle’s end of life.
“We design for serviceability and removal of major components, such as high-voltage batteries, engines, transmissions, etc.,” she says.
Sponsored Content
Labor that Works
With 25 years of experience, Leadpoint delivers cost-effective workforce solutions tailored to your needs. We handle the recruiting, hiring, training, and onboarding to deliver stable, productive, and safety-focused teams. Our commitment to safety and quality ensures peace of mind with a reliable workforce that helps you achieve your goals.
“Ford continues to increase its use of sustainable materials, such as plastics made with biobased content,” Majeske says. Also, large components, such as electric batteries, are designed to be easily removable so the battery can be recycled before the vehicle is sent to a dismantler.
If the makeup of new vehicles does not change much in the coming decade, as Kavanagh and others say they expect, recyclers and dismantlers can breathe a sigh of relief.
“Steel has a mature and efficient recycling infrastructure that pays for itself,” Kavanagh says. He says recyclers have no reason to anticipate the need to retool or reformat their internal processing lines to meet vehicle composition changes. At least, Kavanagh says, “Not as far as steel in concerned.”
What does the increased use of aluminum mean to a recycler? A ton of aluminum scrap currently fetches about five times what a ton of steel brings.
The base curb weight of the large, Ford Super Cab F-150 with a 5.0-liter V8 engine is about 5,700 pounds. Cutting 700 pounds out of the weight is a 12 percent reduction. If 60 percent of that 5,700 pounds in the 2014 version was metal (subtracting glass, plastic molding, seats, etc.), that is roughly 3,400 pounds. The 2015 aluminum version, slimmed down by 700 pounds, would have a metal weight of 2,700 pounds, or nearly 20 percent less metal (of any type) by weight than its predecessor.
Reducing waste starts with manufacturing. Majeske says that in addition to reducing waste created through end-of-life vehicles, Ford is committed to reducing waste in its manufacturing plants. “Ford’s recently enacted five-year global waste reduction strategy calls for a 40 percent per vehicle reduction in the amount of waste sent to landfill between 2011 and 2016—equal to just 13.4 pounds per vehicle worldwide,” she says.
Battery operated
One component that seems likely to remain heavy for the near future, despite recent successes in technology, is the battery pack in hybrid vehicles.
Honda recycles nickel-metal batteries from its hybrid vehicles in North America, Mauk says. “In 2013, Honda established the world’s first process to reuse rare earth metals extracted from nickel-metal hydride batteries for use in new batteries,” he adds.
Demand for hybrid and electric vehicles is increasing slowly and will continue to increase as the technology improves and becomes more affordable.
“Alternatives for recycling, refurbishing or reusing high-voltage batteries from hybrid and electric vehicles are being developed and will take shape as higher volumes of those vehicles reach end of life,” Majeske says, noting that an infrastructure already exists for high-voltage battery recycling. “We are working to connect that infrastructure with vehicle dismantlers,” she adds.
“We expect vehicle dismantlers will remove the batteries from vehicles and be connected with the emerging battery recyclers. Battery dismantlers will have specific expertise and processes to manage to batteries at the vehicle’s end of life,” Ford Motor Co.’s Majeske says.
So, it appears that no matter the actual makeup of the vehicle of tomorrow, its end of life will be in a recycling facility.
The Washington, D.C.-based Auto Alliance—a group of vehicle manufacturers comprising BMW Group, Chrysler Group LLC, Ford Motor Co., General Motors Co., Jaguar Land Rover, Mazda, Mercedes-Benz USA, Mitsubishi Motors, Porsche, Toyota, Volkswagen Group of America and Volvo Cars North America—estimates that approximately 86 percent of each vehicle by weight is recovered for reuse, remanufacturing or recycling.
Given that designers of vehicles are seeing end of life as just as important as other phases of the vehicle’s life cycle, that process should continue to be profitable for recyclers.
The author is a Cleveland-based contributing editor to Recycling Today. He can be contacted at curt@curtharler.com.
Get curated news on YOUR industry.
Enter your email to receive our newsletters.

Explore the March 2014 Issue
Check out more from this issue and find your next story to read.
Latest from Recycling Today
- Recycled steel price crosses $500 per ton threshold
- Smithers report looks at PCR plastic’s near-term prospects
- Plastics association quantifies US-EU trade dispute impacts
- Nucor expects slimmer profits in early 2025
- CP Group announces new senior vice president
- APR publishes Design Guide in French
- AmSty recorded first sales of PolyRenew Styrene in 2024
- PRE says EU’s plastic recycling industry at a breaking point