REGULATIONS
EPA Finalizes Rules Affecting Boilers
The U.S. Environmental Protection Agency (EPA) has finalized changes to Clean Air Act standards for boilers and certain incinerators. The agency says the changes have been designed to achieve extensive public health protections by slashing toxic air pollution, including mercury and particle pollution, while also addressing feedback provided by industry and labor groups. As a result of the changes, 99 percent of the approximately 1.5 million boilers in the United States are not covered by or can meet the new standards by conducting periodic maintenance or regular tuneups, according to the EPA.
The final adjustments to the standards are based on what the EPA calls an extensive analysis of data and input from states, environmental groups, industry, lawmakers and the public.
“As a result of information gathered through this review, including significant dialogue and meetings with public health groups, industry and the public, the final rule dramatically cuts the cost of implementation by individual boilers that EPA proposed in 2010,” the EPA states in a Dec. 21, 2012, news release. “At the same time, these rules will continue to deliver significant public health benefits. EPA estimates that for every dollar spent to reduce these pollutants, the public will see $13 to $29 in health benefits, including fewer instances of asthma, heart attacks as well as premature deaths.”
The rules set numerical emission limits for less than 1 percent of boilers—those that emit the majority of pollution from this sector, according to the EPA. For these “high-emitting” boilers and incinerators, typically operating at refineries, chemical plants and other industrial facilities, EPA is establishing what it calls more targeted emissions limits to “protect public health and provide industry with practical, cost-effective options to meet the standards.”
EPA also has finalized revisions to the Non-Hazardous Secondary Materials (NHSM) Rule designed to provide clarity on what types of secondary materials are considered nonwaste fuels and provide greater flexibility in rule implementation. This final rule classifies a number of secondary materials as categorical nonwastes when used as a fuel and allows for operators to request that EPA identify specific materials through rulemaking as a categorical nonwaste fuel.
According to the EPA, implementing these standards will avoid up to 8,100 premature deaths, prevent 5,100 heart attacks and avert 52,000 asthma attacks per year in 2015.
More detailed information on the final standards for boilers and incinerators is available at www.epa.gov/airquality/combustion.
In a separate EPA action in late December 2012, to meet a court deadline, the agency issued final amendments to the 2010 clean air standards for the cement manufacturing industry. The final amendments maintain the significant emission reductions from the 2010 standards, “while providing industry additional time to implement the revised rules,” according to the EPA.
More information is available at www.epa.gov/airquality/cement.
PAPER
Catalyst Paper Sells Idle Arizona Newsprint Mill
Catalyst Paper, based in Richmond, British Columbia, has accepted a bid to sell its closed recycled-content newsprint mill in Snowflake, Ariz., as well as its shares of the nearby short line Apache Railway.
According to a news release issued by Catalyst, Los Angeles-based Hackman Capital and its affiliates have agreed to purchase the Arizona properties for $13.46 million “and other nonmonetary considerations.” The final acceptance of the bid is subject to U.S. court approval.
The buyer intends to continue to operate the Apache Railway as a going concern, according to the news release, but does not state an intention to restart the mill.
The transaction is supported by the town of Snowflake “and various local interests,” according to Catalyst Paper.
“We are pleased that this transaction has progressed efficiently and that the community’s interests have been considered through the process and in the successful bid,” says Catalyst Paper President and CEO Kevin Clarke. “While paper manufacturing is part of Snowflake’s past, this transaction puts the asset on a path to a new future that can continue to bring value to the region.”
The sale is expected to be completed in the first quarter of 2013 and is subject to various closing conditions.
PLASTICS
InterGroup International to Open Plant in Georgia
InterGroup International, a plastics recycling company based in Euclid, Ohio, has announced plans to invest $5 million to open a facility in Jackson, Ga.
“More and more of our customers have located in the Southeast, and Jackson is a convenient location for us to do business with them,” says Neil Gloger, InterGroup CEO. “Butts County has a pro-business attitude and has shown us they wanted us to be here. Other locations we looked at didn’t show us the same hospitality as Butts County,” he adds.
Prior to opening the new facility, InterGroup used tolling arrangements to process material.
InterGroup International says it processes approximately 13 million pounds of plastic scrap per month, primarily from industrial sources.
“We have spent countless hours working to make Butts County the place for InterGroup International to locate,” says Bryan Bush, chairman of the Development Authority of Butts County. “They are creating quality green jobs that will have a great impact on our community. We are very excited they chose Butts County and look forward to a great working relationship with them in the future.”
Gloger says the site in Jackson, within 20 miles of Atlanta, is adjacent to rail access and a major highway. The 33-acre site has a number of existing structures, of which InterGroup will initially occupy a 220,000-square-foot building.
“Eventually we will use all of the available space,” Gloger says.
Product destruction equipment also will be installed at the new location.
The company took ownership of the facility in early October 2012 and says its goal is to reach full production capacity by the end of 2013.
“It’s a great honor to be a part of the team the Development Authority brought together,” says Roger McDaniel, chairman of the Development Authority board of commissioners. “They made sure the right people were at the table with the resources we needed to locate this company. I’m certain InterGroup International will be an outstanding corporate citizen for many years to come.”
In addition to its Euclid headquarters, InterGroup International has locations in Michigan, Pennsylvania and Texas. The company also exports plastic scrap from the Savannah, Ga., port.
METALS
Advantage Metals Recycling Acquires Nuelle’s 4X4 Salvage
Advantage Metals Recycling (AMR), headquartered in Kansas City, Mo., has purchased the assets and business of Nuelle’s 4X4 Salvage, Higginsville, Mo.
Nuelle 4X4, founded in 1986, operates a scrap metal processing facility and a full-service used auto parts store.
Cincinnati-based David J. Joseph Co. (DJJ), a division of Charlotte, N.C.-based Nucor Corp., owns AMR.
According to AMR, the new location is consistent with the company’s growth strategy and demonstrates DJJ’s commitment to expanding its existing regional recycling platforms.
AMR, with more than 350 employees, operates 15 recycling facilities in Kansas and Missouri. AMR’s Higginsville recycling center buys automobiles, scrap iron and steel as well as common household nonferrous scrap metal items. The company also sells used auto parts on site.
DJJ operates a total of 69 scrap recycling facilities and nine U-Pull-&-Pay self-service used auto parts stores in the U.S.
METALS
Upstate Shredding Signs Lease with Port of Albany
Upstate Shredding, Owego, N.Y., has signed a 15-year lease with The Port of Albany, N.Y., with options for two five-year extensions. The deal will allow the scrap metal company to build and operate a scrap metal transloading facility on 18 acres at the port.
A Dec. 14, 2012, article in The Business Review of Albany refers to the company’s project as “a $15 million shipping center” that will soon be linked to “a $35 million automobile shredding operation.”
According to Richard Hendrick, general manager of the Port of Albany, in addition to receiving approval to site the transloading facility, Upstate has applied for a permit to build and operate a 10,000-horsepower auto shredder at the site.
The 18-acre port location reportedly has access to rail sidings, which will be used as Upstate Shredding brings in processed scrap metal from its other yards to be loaded into ocean-going vessels.
Hendrick says Upstate Shredding will take over roughly 10 acres presently used by Cargill for a deicing operation, plus five acres that are vacant and three acres that are being used by a waste management firm.
Hendrick says Upstate already has contracted with a demolition firm to demolish one building. The company then expects to pour concrete and erect a scale house, an inside storage facility and a building designed for fluids removal. Demolition was expected to begin in early January, with construction of the new buildings to begin by the end of the first quarter of 2013, Upstate says.
While a local agency asked the company to erect an 8-foot fence around the facility, Upstate Shredding has sought a variance that would allow it to erect a 10-foot fence around the plant.
METALS
Metalico Expands into Cleveland
Metals recycler Metalico Inc., Cranford, N.J., has increased its presence in northeastern Ohio by expanding into Cleveland with the formation of a joint venture company. Metalico also has expanded in western New York through a recent acquisition.
Its Cleveland joint venture, Metalico JBI Cleveland, is in partnership with Joseph Immormino, who will operate the company, located on East 55th Street at the site of a former scrap yard.
The company says it expects the Cleveland facility to expand its retail business in northeast Ohio while supporting Metalico’s existing yards in Akron and Youngstown, Ohio. The company also has announced that its Rochester, N.Y., subsidiary has purchased the assets of Bergen Auto Recycling LLC, including its junk car inventory and property in Bergen, N.Y. Metalico says it plans to expand the location’s salvage car buying capabilities and continue its “pick-and-pull” auto parts business while locking in additional supply to feed its auto shredding facility in the Buffalo, N.Y., area.
Carlos Agüero, Metalico president and CEO, says, “These additions to our network should have an immediate benefit for us. Our full-service scrap yard platforms are already well-established in both of these geographic regions and have ample processing capacity to handle additional flow.
“Our expansion into these new locations is consistent with Metalico’s growth strategy of penetrating geographically contiguous markets and benefiting from intercompany and operating synergies that are available through consolidation,” he adds.
NONFERROUS
Exide to Idle Pennsylvania Battery Recycling Plant
Milton, Ga.-based Exide Technologies has announced it will idle its lead-acid battery recycling plant in Reading, Pa., by no later than March 31, 2013. The company says it will continue to recycle plastics at the Reading facility and will maintain the facility and necessary permits and approvals for future lead-acid battery recycling activities.
“This decision was based on several factors, including the dramatic swings in the lead market and the high capital investment needed, due to regulatory requirements, to remain operational in Reading,” says Paul Hirt, president of Exide Americas.
“By idling this facility, we can defer spending the capital while still having the majority of our internal lead demands met through our other three recycling centers in Vernon, Calif.; Canon Hollow, Mo.; and Muncie, Ind. The decision is in no way reflective of the Reading workforce. We sincerely appreciate our employees’ dedication and commitment over the years,” adds Hirt.
Exide Technologies has operations in more than 80 countries and refers to itself as one of the world’s largest producers and recyclers of lead-acid batteries.
CONSTRUCTION & DEMOLITION
Earth First Breaks Ground on Recycling Center
Earth First LLC, based in Fort Wayne, Ind., has broken ground on a recycling center and transfer station in that city. According to the company, when the construction is complete, Earth First will operate Northeast Indiana’s only complete construction and demolition recycling facility.
The new facility also has been designed to allow for expansion based on increased service in the manufacturing and commercial sectors.
Material to be handled by the new plant includes brick and block, concrete, drywall, wood, cardboard, plastics, metals, glass and paper. The 20,000-square-foot facility will contain a sorting line for separating materials, a two-ram baler for handling old corrugated containers (OCC) and plastics, loading docks and a trailer bay for shipping residuals.
The facility, scheduled to be open by March 2013, will cost $2 million when it is complete. Earth First also says the new facility will result in 15 new jobs.
Earth First operates a fleet of trucks that will transport material to the site. Additionally, third-party customers will be able to deliver material to the facility, which is Earth First’s first C&D recycling facility.
The company, which was founded in 2009, serves the recycling and solid waste needs of companies and residents in northeast Indiana. Gregg Walbridge and Jason Pickerman say they formed Earth First in an effort to bring back the locally owned, family atmosphere the Walbridge family created and maintained at National Serv-all for more than 30 years.
Kirk Salerno, a representative of Earth First, says the Fort Wayne area is an ideal location for the C&D recycling plant because no facility in the area currently can process this material stream.
When operational, “Earth First will operate the only facility of this type in northeast Indiana and will have close proximity to all buyers/processors of the construction and demolition materials being recycled,” Salerno adds.
The Indiana Department of Environmental Management (IDEM) Recycling Market Development Program awarded Earth First a $100,000 grant to assist in buying equipment for the facility.
MUNICIPAL
Rumpke Receives Financing Approval for Facility
Rumpke Consolidated Cos. Inc., headquartered in Cincinnati, has been authorized to receive $32 million in financing by the Ohio Air Quality Development Authority (OAQDA) for a new recycling plant in Cincinnati. The new plant will replace Rumpke’s facility that was damaged by fire in April 2012.
Under the financing package, OAQDA authorized the issuance and sale of up to $32 million in Exempt Facility Revenue Bonds. The authorization was OAQDA’s first federally tax-exempt financing for a recycling facility. The bonds will be issued in two series.
The 84,000-square-foot recycling plant will employ 110 workers and will process residential and commercial materials through a dual-infeed system. The system will be capable of processing 55 tons per hour of residential material and 20 tons per hour of commercial material. The processing and baling systems to be installed include six optical scanners for sorting fiber and containers, two eddy-current separators for aluminum, an electromagnet for ferrous scrap and an extensive mixed-glass removal system, according to the company.
Rumpke says the project is scheduled for completion in October 2013.
“This creative financing package will allow Rumpke Recycling to install a state-of-the-art facility that will operate with maximum efficiency and retain our regional capacity at optimal levels,” Rumpke CFO Phil Wehrman says. “In addition, the federal income tax exemption on OAQDA’s bonds truly helped make this project come together.”
The OAQDA is a nonregulatory government agency created to help Ohio businesses comply with clean air regulations.
METALS
SEC Approves J.P. Morgan’s Copper ETF
Dow Jones has reported that the U.S. Securities and Exchange Commission (SEC) has approved J.P. Morgan’s application to introduce a copper exchange-traded fund (ETF) to the market. The fund will be backed by 61,800 metric tons of copper, according to the company.
Since J.P. Morgan first introduced the idea of offering the ETF as an investment vehicle more than two years ago, copper consumers have expressed concern that the fund would make copper scarcer by taking it off the market, ultimately driving up copper prices.
Where the JPM XF Physical Copper Trust differs from other copper ETFs is that it will be backed physically by copper, while other copper ETFs are backed by copper futures, according to the company.
The SEC approval was the final hurdle in J.P. Morgan’s 26-month quest to list the ETF. The investment bank had amended its request at least five times to answer the SEC’s questions and to address concerns from U.S. copper users.
In its Dec. 14, 2012, approval filing, the SEC says it doesn’t believe the copper ETF was “likely to disrupt the supply of copper available for immediate delivery.”
In a statement accompanying the approval, the SEC says the trust will not affect the copper market’s integrity but rather will serve as a transparent and accessible alternative by which participants in the copper market could access or off-load physical copper inventory and associated price risk.
Moreover, the SEC says its analysis of market data shows copper inventories have no statistical effect on copper prices, leading the regulator to conclude copper-backed funds would have no direct impact on market prices.
In related news, the financial firms IBlackRock Inc. and ETF Securities Ltd. have announced plans to introduce physically backed ETFs for industrial metals.
ELECTRONICS
AERC Changes Ownership
The electronics recycling company AERC Recycling Solutions, Flanders, N.J., has announced that Robert Landmesser, founder and CEO of the company, reached an agreement with Recycling Holdings LLC of Nashville, Tenn., to transfer his share of AERC stock to Recycling Holdings. The change in ownership will allow AERC to pursue new business opportunities to remain competitive in the marketplace and continuously improve the customer experience, the company says.
Prior to the transfer of his ownership stake to Recycling Holdings, made on Oct. 31, 2012, Landmesser was the single largest shareholder in the company.
Recycling Holdings and its affiliate have been involved with AERC throughout the past five years, the company says.
“This is a tremendous opportunity for AERC to continue its commitment in servicing its customers and providing excellent recycling options,” Landmesser says.
“AERC has demonstrated to be an exemplary company over the past 22 years, with a continuous-improvement business model, and has helped thousands of companies, government agencies, universities, hospitals and individuals properly recycle,” he continues.
“It has been a great honor to establish and lead this company throughout the years,” Landmesser says. “I have high expectations for what AERC will achieve in the future.”
AERC’s client base includes organizations in the financial services, real estate, property management, government, information technology, medical, pharmaceutical, education and retail industries. AERC specializes in providing full-service solutions for end-of-life electronics, secure data destruction, asset management and universal waste.
The company owns and operates Com-Cycle electronics recycling facilities in Allentown, Pa.; Ashland, Va. West Melbourne, Fla.; Houston; and Hayward, Calif. Each of the facilities has been certified to the Responsible Recycling Practices/Recycling Industry Operating Standard (R2/RIOS).
ELECTRONICS
CExchange Receives R2 Certification
The electronics recycling firm Consumer Electronic Exchange (CExchange), Carrollton, Texas, has achieved Responsible Recycling Practices (R2) certification following a third-party audit of its operations.
The R2 Standard sets forth requirements relating to environmental, health, safety and security aspects of electronics recycling. According to CExchange, R2 certification is granted to companies that comply with recycling standards based on a combination of state and national laws, international regulations and industry-accepted best practices. The certification also requires recyclers and their vendors to assure that toxic material streams are managed through to final disposition.
“There is no greater responsibility than protecting our clients’ trade-in and recycling by adhering to the most rigorous environmental criteria for recycling e-waste,” says Hunter Howard, CExchange president and COO. “To CExchange, matters of reuse and recycling are not treated simply as business practices—rather, it’s about a commitment we have to environmental stewardship and social accountability.”
METALS
Prime Materials Recovery Acquires Florida Recycler
Prime Materials Recovery (PMR), East Hartford, Conn., has completed the acquisition of Miami-based Allied Metal Corp.
PMR concentrates on wire and cable recycling and operates processing facilities in Canastota, N.Y.; Willimantic, Conn.; Shelby, N.C.; and Orangeburg, S.C. The company says it processes and brokers more than 360 million pounds of nonferrous metals each year.
Allied Metal Corp. has been involved in importing nonferrous metals throughout Latin America and the Caribbean for more than 50 years, according to PMR.
“We are excited about welcoming the Mosheim family (former owners of Allied) into ours and look forward to expanding our international sourcing capabilities with this acquisition,” says Bernard Schilberg, CEO of PMR. “It truly makes PMR a global leader in the industry.”
In addition to processing wire and cable and other nonferrous scrap, PMR has import and export capabilities. The company also says it “distributes a wide range of copper-based alloys, aluminum, tin, zinc, nickel and lead for resale to mills and foundries.”
Investment banking firm Carter Morse & Mathias (CMM), Southport, Conn., served as PMR’s financial advisor for the transaction. CMM will not disclose the terms of the transaction and financing.
“Having worked with PMR in the past, we are excited to assist in closing such a strategically compelling transaction,” says Ramsey Good-rich, managing director of CMM.
Nate Schilberg, PMR president and CFO, comments, “CMM’s expertise in analyzing, structuring and negotiating this transaction was invaluable. Their quality advice and experience with family-held middle-market businesses and creative problem solving were essential to successfully closing this transaction.”
PLASTICS
Petoskey Expands Plant Operations
Plastic film and bag producer and recycling company Petoskey Plastics, Petoskey, Mich., is expanding its operations in Petoskey; Hartford City, Ind.; and Morristown, Tenn. The company, which has invested $16 million in the projects, says it expects to have the expansions completed by April 2013. The investments include a new global enterprise resource planning software system.
The majority of the investments are being made at Petoskey’s 300,000-square-foot closed-loop recycling facility in Hartford City. The investment will include adding four blown film lines and one drawtape line at the plant.
Petoskey Plastics says it currently is processing more than 30 million pounds of postconsumer plastic film and bags into recycled-content pellets. When the expansion is complete, the company will be able to extrude the pellets into 30 million pounds of three-layer postconsumer recycled bags and film, all under a single roof.
When the investment is complete, the Indiana facility will be totally integrated and will provide the marketplace with “the lowest carbon footprint and cost-effective bags and film manufacturing in North America,” according to Petoskey Plastics.
ELECTRONICS
Sims Acquires Canadian Electronics Recycler
Sims Recycling Solutions (SRS), a division of New York-based Sims Metal Management Ltd., has acquired the assets of Genesis Recycling Ltd., Langley, British Columbia, expanding its North American electronics recycling business.
Genesis holds ISO 9001, ISO 14001, OHSAS 18001 and Responsible Recycling Practices (R2) certifications.
“We are excited to have the Genesis team join the SRS family,” says SRS Americas President Steve Skurnac. “With our strong presence in Ontario and eastern Canada, this acquisition was an attractive opportunity for Sims Metal Management to enter western Canada and further strengthen its North America SRS electronics recycling business.”
ELECTRONICS
DOJ Convicts Electronics Recycler Named in “60 Minutes” Segment
Executive Recycling Inc., a former Englewood, Colo.-based electronics recycling firm, former owner and CEO Brandon Richter and former vice president of operations Tor Olson have been convicted of multiple counts of mail and wire fraud, environmental crimes related to the illegal disposal of electronic scrap, smuggling and obstruction.
Executive Recycling, Richter and Olson were indicted by a federal grand jury in Denver Sept. 15, 2011. The jury trial began Dec. 3, 2012, and the jury reached its verdict Dec. 21, 2012. Sentencing is scheduled for April 2013.
The case involving Executive Recycling was featured in a November 2008 segment on the CBS TV program “60 Minutes,” which looked at the practice of unsafe electronics dismantling in Guiyu, China, and alleged misrepresentation by some electronics recyclers who shipped material there.
According to the DOJ, the defendants engaged in the practice of exporting electronic scrap, including cathode ray tubes (CRTs). The defendants negotiated the sale of electronic scrap to brokers who represented foreign buyers or who sold the electronic scrap overseas.
Executive Recycling appears as the exporter of record in more than 300 exports from the United States between 2005 and 2008, according to the DOJ. About 160 of the exported cargo containers contained a total of more than 100,000 CRTs.
Contrary to their representations to customers to dispose of electronic scrap “properly, right here in the U.S.,” the defendants sold the electronic scrap they received to brokers for export overseas to China and other countries, according to the DOJ.
The company faces a $500,000 fine per count or twice the gross gain or loss for seven counts of wire fraud; a conviction for one count of failure to file notification of intent to export hazardous waste, which carries a penalty of a $50,000 fine per day of violation or twice the gross gain or loss; and one count of exportation contrary to law, which carries a penalty of a $500,000 fine or twice the gross gain or loss.
Richter and Olson each face seven counts of wire fraud, each of which carries a penalty of not more than 20 years imprisonment and a fine of up to $250,000, and one count of exportation contrary to law, which carries a penalty of not more than 10 years imprisonment and a fine of up to $250,000, twice the gross gain or loss or both.
Richter faces one count of destruction, alteration or falsification of records in federal investigations and bankruptcy, which carries a penalty of not more than 20 years imprisonment and a fine of up to $250,000. An asset forfeiture allegation states that upon conviction the defendants shall forfeit to the United States any and all property or proceeds derived from their illegal activity.
CONSTRUCTION & DEMOLITION
Casella Makes Acquisition
Casella Waste Systems Inc., Rutland, Vt., has acquired the outstanding stock of Blow Brothers Inc., which does business as Bestway Disposal Services and BBI Waste Industries. The acquisition of the companies, based in Brentwood, N.H., closed Dec. 6, 2012.
BBI provides solid waste collection, transfer and liquid waste services in seven locations in New Hampshire and Maine. Bestway also operates a portable toilet service and supplies roll-off containers to contractors and individuals.
John Casella, chairman and CEO of Casella Waste Systems, says, “The BBI team has built an exceptional solid waste company that is well-regarded by its municipal, commercial and residential customers.”
He adds, “BBI’s operations overlay well with our footprint in New Hampshire and Maine, and we expect the acquisition to drive incremental value from our existing operations and provide a growth platform in several new market areas.”
BBI collects and transfers roughly 105,000 tons of solid waste and recyclables. Casella says the company should be able to internalize approximately 80 percent of this material at its facilities in addition to consolidating operations, routes and transportation.
ELECTRONICS
Goodwill of West New York Partners with Sunnking
Goodwill Industries of West New York (WNY) has named Sunnking Inc., headquartered in Buffalo, N.Y., as its partner to handle large-scale electronic donations in the Buffalo area.
“Sunnking’s reduce, reuse, recycle, dismantling, shredding and baling methods have a proven track record,” says Thomas Lynch, president and CEO of Goodwill Industries of WNY. “It is our responsibility to donors and to the community to recycle their products in an environmentally responsible way.”
Donors may drop off their electronics for recycling at any Goodwill donation site. From there, electronics are brought back to Goodwill’s headquarters, sorted and packaged by Goodwill employees for pickup by Sunnking.
Goodwill of WNY says it collects 42,000 pounds of electronics per month.
“We are honored that Goodwill has selected us for their electronic recycling,” Adam Shine, Sunnking sales manager, says. “We know that Goodwill has a tremendous reputation and has their pick of service providers, so we are thankful to be their service partner.”
Shine adds, “By adding Goodwill to our extensive collection network it allows residents considerably more free, easy and convenient ways to drop off old, obsolete and unwanted electronics.”
Sunnking Inc., a R2 (Responsible Recycling Practices) certified electronics recycling company, has locations in Buffalo and Brockport, N.Y.
PLASTICS
Geo-Tech Polymers Receives Loan
Money from a 2012 Community Development Block Grant (CDBG) Economic Development Program will be used to assist plastics recycling company Geo-Tech Polymers with an expansion project in Waverly, Ohio.
According to a news release from the Pike County (Ohio) Commissioners, Geo-Tech will receive a $460,000 loan from the county to help with the costs of purchasing and installing equipment at the Waverly plant.
The expansion will create 50 new full-time jobs, according to the Pike County Commissioners office.
Geo-Tech, based in Westerville, Ohio, specializes in recycling coated plastics used in consumer and automotive applications. According to its website, the company has developed a process to “remove coatings (paints and metals) and reclaim valuable plastic substrate materials without using chemicals or solvents that can degrade properties and diminish surface appearance.”
Wastren Advantage Inc. (WAI), a Piketon, Ohio, environmental technology firm, acquired Geo-Tech in June 2012.
“The Pike County Commissioners have provided a tremendous amount of support to our project, and we appreciate their hard work in helping us secure this financing,” says Doug Collins, president of Geo-Tech.
“When WAI decided to acquire Geo-Tech and expand the operations to Waverly, our hope was to create opportunities and good jobs in our community,” Collins adds. “The Pike County Commissioners share our vision, and we are pleased to partner with them.”
Chris Ervin, Pike County economic development director, says, “We are excited to provide some of the financing for the Geo-Tech expansion to Waverly and look forward to the new jobs. WAI’s commitment to investing and creating jobs in southern Ohio makes it easy to support this project.”
In addition to the $460,000 loan, Geo-Tech has received a $50,000 grant from the Fluor-B&W Opportunity Fund, a $10,000 grant from the Southern Ohio Agricultural and Community Development Foundation, a $1.2 million loan through the Jobs Ohio program and a $50,902 Job Creation Tax Credit.
Ohio Valley Bank Corp., Gallipolis, Ohio, will finance the balance of Geo-Tech’s Waverly plant expansion project.
NONMETALLICS
Boeing, BMW Agree to Research Carbon Fiber Recycling
Aircraft maker Boeing, headquartered in Chicago, and German automaker BMW Group are collaborating on carbon fiber recycling research and sharing knowledge about carbon fiber materials and manufacturing. Boeing uses carbon fiber in its 787 Dreamliner, while BMW introduces two vehicles with passenger compartments made of carbon fiber in 2013.
“This collaboration agreement is a very important step forward in developing the use and end use of carbon fiber materials,” says Larry Schneider, Boeing Commercial Airplanes VP of product development.
“It is especially important that we plan for the end of life of products made from carbon fiber,” Schneider adds. “We want to look at ways to reclaim and reuse those materials to make new products. Our work with BMW will help us attain that goal.”
BMW board member Herbert Diess says, “Boeing has many years of extensive experience using carbon fiber in the field of aviation, while the BMW Group has earned a significant competitive advantage through its use of special manufacturing methods for production of carbon fiber parts.”
PLASTICS
Recycled-Content Plastics Pellet Facility Planned in Texas
HDi Plastics Inc., a subsidiary of Minneapolis-based Hypertension Diagnostics Inc., has signed a development agreement with the Eastland, Texas, Economic Development Inc. (EEDI) agency to build a plastics recycling facility in the Eastland Industrial Park.
The company, which collects and reprocesses plastic scrap into pellets for sale to manufacturers, plans to construct a 50,000-square-foot facility that can be expanded to 150,000 square feet. An estimated $4 million will initially be invested in the project, including an estimated $2.9 million in machinery.
Kenneth Brimmer, HDi CEO, says, “Developing and locating a project such as this is a costly and highly complicated process. We will continue to work with Jerry Conner, EEDI executive director and various state of Texas development agencies to acquire other sources of funding that will be required to make the project viable.
“We look forward to the construction process and startup hiring. We estimate first-phase construction could start as early as mid-2013,” Brimmer adds.
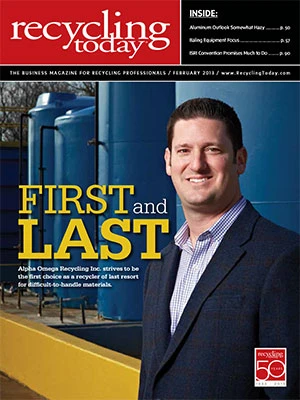
Explore the February 2013 Issue
Check out more from this issue and find your next story to read.
Latest from Recycling Today
- Aqua Metals secures $1.5M loan, reports operational strides
- AF&PA urges veto of NY bill
- Aluminum Association includes recycling among 2025 policy priorities
- AISI applauds waterways spending bill
- Lux Research questions hydrogen’s transportation role
- Sonoco selling thermoformed, flexible packaging business to Toppan for $1.8B
- ReMA offers Superfund informational reports
- Hyster-Yale commits to US production