Editor’s Note: This report is excerpted from a presentation given by Tim Alseth, technical service manager with Genesis Attachments, Superior, Wis., at the Institute of Scrap Recycling Industries (ISRI) Operations Forum, held Oct. 3-6, 2012, in Phoenix. These are general guidelines; for complete maintenance instructions, consult your manufacturer’s documentation. Additional details are posted at www.RecyclingToday.com/rt213-shear-maintenance.aspx.
As a rule of thumb, maintenance time on most brands of mobile shears should amount to about 10 percent of the operator’s work schedule. It’s not a lot of time—four hours for a 40-hour week—but it needs to be dedicated regularly to optimize the life of the shear and its components and also to prevent downtime and catastrophic system failures.
First, a few safety and preparation pointers before doing any maintenance on the shear. You’re dealing with high-pressure hydraulic systems, so you must bleed down all circuits to minimize the possibility of hydraulic oil injection injury. Operators must practice proper lockout/tagout procedures to release hydraulic pressure from all circuits. Opening up systems that are under pressure can lead to the spraying of high-pressure oil into skin, a serious condition that requires immediate medical attention and a trip to the hospital.
Prior to working on the tool, operators also need to make sure the shear is blocked up safely on the ground or on a suitable sawhorse so that it won’t fall. Once the hydraulics are disabled on the excavator, there’s no longer pressurized power that will hold it, so don’t ever trust the hydraulics.
Daily Inspections
Daily maintenance schedules should be implemented at four-hour and eight-hour intervals for many brands and models of shears on the market. Each interval should include specific inspections, greasing at identified areas and any action items that were found to be necessary.
A four-hour inspection should include checking for hydraulic leaks, blade damage and loose or missing bolts and cylinder pin keepers. At the eight-hour interval, operators need to inspect bolts, fittings and hoses, bracket pivot and pin retainers, cylinder pivot and pin retainers and the entire shear, looking for loose or damaged bolts, cracks and other damage to these areas.
When it comes to fittings and hoses, make sure you don’t have anything loose, chafed, cracked and/or ready to break. You also need to torque the bolts, using a torque wrench and torque multiplier, to the settings called for by the manufacturer. I have seen many more issues with bolts being over-torqued than with bolts being left loose. Over-torquing can cause the shank of the bolt to become stretched, or take on an hourglass shape at the point where it meets the threads, a condition that takes the elasticity out of the bolt, possibly leading to breakage of the bolt.
Check the bracket and cylinder pivots for wear and also inspect pin retainers. Pin retainers are a real source of problems if they become broken or if the pins are allowed to extrude from the retainer area, particularly with regard to the cylinder pivot connections. Pins that begin to extrude can rip the side of the shear, leading to catastrophic failures while the shear is in use. You also want to check the entire shear, the stick body bracket and the upper and lower jaw for any cracks.
Greasing Schedule
Locations that may need to be greased every four hours, according to many manufacturers, are the shear cylinder rod, shear cylinder butt, auto-guide fitting and upper jaw contact surface and the main shaft or pivot. Grease these connections with the jaw open and closed until grease extrudes from the area. Greasing should be done at the middle of the shift and the end of the day, when the shear is warm or hot, so that the grease goes to the connections where it needs to be. Don’t worry about over-greasing the shear, as there are no susceptible grease seals that can be damaged.
Greasing locations at the eight-hour interval include all those specified at four hours, plus the bracket pivot, bracket cylinder, rotation bearing and rotation head. After greasing the rotation bearing, rotate the shear through two full rotations.
Jaw and Blade Maintenance
Inspections of the jaws and blades also need to be conducted at the eight-hour interval. Here you want to check blade gaps as well as blade edge radiuses to see how much wear you have on the blade edge. Check for loose or damaged bolts in these areas and retorque loose bolts when the shear has cooled down. Check the auto-guide gap and shim or adjust if necessary or called for by the manufacturer. You also need to check that buildup and hard surfacing is where it should be and grind over any rolled-over or mushroomed blade edges.
Allied-Gator Shear Maintenance Routines Differ Mike Ramun, sales and marketing manager with Allied-Gator Inc., Youngstown, Ohio, says the proprietary-grade High-Alloy Steel CastTM construction of the patented Allied-Gator MT® Series Multi-Tool substantially reduces maintenance compared with shears constructed from steel plate. “When it comes to manufacturing a low-maintenance shear, the material used in the construction is a major contributing factor,” says Ramun. “The key advantages of the MT’s Steel Cast material include higher abrasion resistance, greater strength and the elimination of deflection/flex experienced while shearing.” He says the MT Steel Cast material requires less frequent welding than steel plate. Also, when weld buildup is required, the MT does not require hardfacing. According to Ramun, the material is impervious to directional force and withstands the high separating loads that can cause deflection and flex in shears constructed from steel plate. “Because the MT Steel Cast material resists deflection while it’s cutting, blade bolt failure is not an issue,” Ramun says. He adds that the use of Steel Cast in the Allied-Gator MT eliminates the need for certain antideflection features, leading to a lower-maintenance, more durable shear. |
Grinding out rolled blade edges is particularly important to do at the end of the day or when necessary, as the shear itself will never cut those edges off on its own. Rather, allowing mushroomed edges to persist will put undue pressure on the lower jaw and chin plate and can potentially lead to jamming, particularly when processing thin materials.
Blade shimming is required when blade gaps exceed those specified in your owner’s manual. It’s critical to note that blade gaps are highly variable and specific to each make and model.
These days, newer shears are calling for larger blade gaps than in years past. The reason for this is because shears are built to be heavier, faster and more powerful, and the materials being processed are thicker. With that comes more operating heat, which leads to thermal expansion of the upper and lower jaws. On the average shear, you can expect to lose about 20- to 25-thousandths-of-an-inch in gap between the piercing tip and guide blades once the shear reaches operating temperatures. If you don’t have the gap called for by the manufacturer, you will have interference between the blades and the piercing tip, which leads to further heat buildup and expansion and, ultimately, can lead to cracking of the blades. You also want to check the primary and secondary blade gaps.
The use of a blade shim is preferable to a feeler gauge when checking your blade gaps, as a shim offers a broader, more comprehensive check of the area where the blades extend into the lower jaw. Once these shears start to wear, it’s not uncommon to see blade seats actually start to tip out, and usually it’s toward the front of the chin plate where most of the piercing and work is being done. Running the shims all the way down along the blade through the bottom of the jaw helps ensure the upper blade to lower blade gap is consistent from the front to the back.
Rotating shear blades becomes necessary when the blade edge radius is worn more than one-eighth of an inch. That can occur typically anywhere from 20 to 80 hours or less if you’re cutting hardened or stainless material. It’s important not to run past this one-eighth-inch rule. Using dull blades tends to wedge or spread the lower jaw apart, as material is not cut off on the top edge of the blades, but is smeared apart between them. This also requires more power, wedges the upper jaw from side to side and leads to fatigue and reduced blade life. Continuing to operate a shear under these conditions also can set off a chain of unfortunate events within the shear structure and hydraulics system. Using worn blades and having excessive blade gaps can cause excessive wedging of the upper jaw from side to side and transfer loading to the shear’s hydraulic cylinder. This side loading greatly reduces cylinder life because excessive pressure is transferred to the rod and piston wear bands. Once they are worn to a point of metal-to-metal contact, catastrophic cylinder failures can occur. This type of failure can result in excavator pump failures, system failures and the need for expensive decontamination.
On the other hand, shears that are properly maintained require less maintenance and downtime in the long run and will typically last years beyond those that aren’t. Brief periods of frequent maintenance will always be better than long periods of downtime and major overhauls.
Tim Alseth can be reached at talseth@genesisattachments.com. Genesis Attachments offers Service and Maintenance Training for customers at select times throughout the year at its Superior, Wis., headquarters.
More Details Online...
Additional technical materials and schematics from this presentation can be found on our website at www.RecyclingToday.com/rt213-shear-maintenance.aspx.
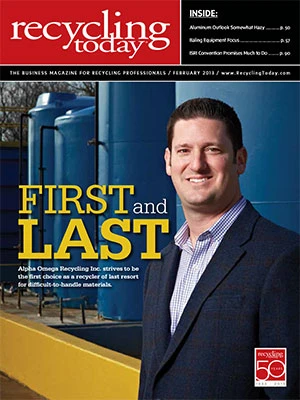
Explore the February 2013 Issue
Check out more from this issue and find your next story to read.
Latest from Recycling Today
- Aqua Metals secures $1.5M loan, reports operational strides
- AF&PA urges veto of NY bill
- Aluminum Association includes recycling among 2025 policy priorities
- AISI applauds waterways spending bill
- Lux Research questions hydrogen’s transportation role
- Sonoco selling thermoformed, flexible packaging business to Toppan for $1.8B
- ReMA offers Superfund informational reports
- Hyster-Yale commits to US production