Many of the characteristics that make plastics ideal for a variety of packaging and industrial applications also can make baling these materials a somewhat challenging task. Compression force is often the key to successfully baling a wide variety of plastics, according to two sources who are processing a combined total of more than 500,000 tons of the material monthly.
Be Forceful
“Get as much force as you can afford,” Kerry Getter advises material recovery facility (MRF) operators who are looking for a baler to process a range of recovered plastics.
Kerry is CEO of Balcones Resources Inc., headquartered in Austin, Texas. The company also operates MRFs in Dallas and in Little Rock, Ark.
Richie Getter, manager of plastics procurement and marketing at Balcones Resources, says the company is processing a range of postconsumer and post-industrial plastics, including polyethylene terephthalate (PET) bottles, high-density polyethylene (HDPE) bottles and crates, plastics Nos. 3 through 7, bulky rigid plastics and stretch film. Kerry adds that the company’s Dallas facility also handles ABS (acrylonitrile butadiene styrene) from the electronics demanufacturing sector.
Sandy Rosen, CEO of GLR Recycling Solutions, headquartered in Roseville, Mich., says, “In general, the more force you have, the better the bale will hold together (provided the wires are able to contain it). The bale will be more solid, likely stack better and less material would fall out.”
In addition to its Roseville location, GLR also operates facilities in Flint Township, Mich., and in North Tonawanda, N.Y., including a facility dedicated solely to processing industrial plastics, foam, shrink-wrap and many other types of plastic.
However, depending on the plastic’s degree of memory, or its tendency to return to its original shape, a too-tightly compressed bale may offer another set of challenges, with Rosen cautioning that “the tighter the plastic is packed, the more chance it will break the wires and blow up all over the place.”
Despite this possibility, for GLR and Balcones, compression force is at the top of the attribute list when shopping for baling equipment.
When asked what additional features he looks for in the balers GLR purchases to process plastics, Rosen says, “It’s also important that the baler allows for easy tying of the finished bale—this is something single-ram machines cannot do as well.”
Kerry says that in addition to compression force, Balcones Resources looks for robust construction, speed and a large infeed opening that will accept bulky materials.
Richie adds that a bale release door is also a key feature because it allows for material to be easily removed when the baler has been overcharged.
Balcones also looks for balers capable of producing bales of plastics weighing from 1,000 to 1,200 pounds. This is often best accomplished through the use of a two-ram baler, he adds. “The reason we have two-rams is to make weight on all shipping containers,” Richie adds.
Kerry adds that Balcones Resources sees a number of efficiencies as a result of producing compact bales of this size, including reduced wire usage, less floor space required for storage and fewer trips for the forklift drivers.
Twice as Nice
Two-ram balers offer more versatility when it comes to processing a range of plastics thanks to their large infeed openings and charge boxes and higher compression forces, which are achieved by one ram compressing material against a wall and into the path of the second ram.
Richie describes two-ram balers as versatile machines capable of processing a variety of materials, including paper, plastics and metals. “There’s not a lot of plastics we can’t bale now that we have large two-ram balers,” he says. However, he notes that rigid plastics and 50-gallon drums would be difficult to handle if an operation did not have a two-ram, high-compression baler.
Balcones’ Austin facility is home to the company’s largest two-ram baler, a REB-2 from Sierra International Machinery, Bakersfield, Calif. This site processes 98 percent of the plastics that Balcones handles, Kerry says. The company’s Dallas facility is home to a REB-1 model, and the Arkansas facility uses a two-cylinder vertical baler from Harmony Enterprises, Harmony, Minn., as the facility’s volume does not yet warrant a larger machine. However, Richie says this unit is capable of reliably baling some types of plastics and making weights for shipping containers on many grades.
Rosen says GLR also finds two-ram balers better suited to the task of baling plastics. “It handles everything we do better than a single-ram would,” he adds.
Knotty Issues
When baling mixed rigid plastics with its downstroke baler, Richie says Balcones often doubles or triples the amount of wire used to tie off a bale. He says this is a good practice that helps to maintain the integrity of the bales.
The type and quality of the wire used in a two-ram baler’s automatic wire tier also is a consideration. Rosen says GLR uses ultra-high-tensile galvanized steel baling wire in its two-ram baler, adding that 12 gauge or better works best when processing plastics. “The better the wire, the less you need to hold the wire together,” Rosen says.
When it comes to a two-ram baler’s wire tying system, Kerry says he looks for one “that we have confidence in and that gives us some options.”
He adds that in plastics baling applications, a baler’s wire tier may need special attention. Kerry stresses the need to keep the wire tier clean and its track clear of debris. “If you are baling soda bottles, there is only so much syrup and that kind of thing wire tiers can take without being cleaned,” he says.
Therefore, to ensure their smooth functioning, Balcones tunes up its wire tiers regularly and cleans them multiple times per day, Kerry says.
In terms of general maintenance, Rosen says plastic is among some of the easiest material on two-ram baling equipment. “I think it wears less than paper or metal and isn’t any more susceptible to jamming.”
However, this is not necessarily the case with single-ram baler models, where automatic wire tiers may be more vulnerable. Rosen adds. “In the case of the single rams, I know plastic can wreak havoc with the auto-tie inserter and often clogs up the inserter slots on the face of the ram.”
While Kerry points out that every recycler’s situation is somewhat different, this basic advice for selecting and maintaining a baler will help recyclers ensure the efficiency of their plastics baling operations.
The author is managing editor of Recycling Today and can be reached at dtoto@gie.net.
Get curated news on YOUR industry.
Enter your email to receive our newsletters.
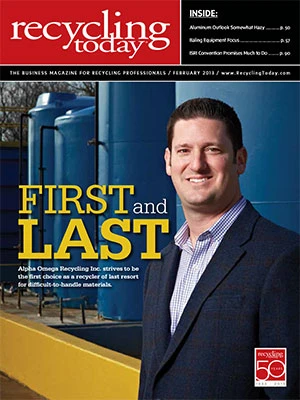
Explore the February 2013 Issue
Check out more from this issue and find your next story to read.
Latest from Recycling Today
- Japanese scrap can feed its EAF sector, study finds
- IRG cancels plans for Pennsylvania PRF
- WIH Resource Group celebrates 20th anniversary
- Ecobat touts commissioning 3 LIB recycling plants in a year
- NWRA: NIOSH cuts a step in the wrong direction
- Novelis announces plant closures
- ABTC reports production increase at LIB recycling facility
- ReMA contributes comments in Commerce Department investigation into copper