Editors’ Note: The following article is an edited transcription of a presentation delivered by Bruce O'Neill, founder and president of Jupiter Transport Services, Jupiter, Fla., at the 2011 Paper Recycling Conference & Trade Show. The event, organized by the Recycling Today Media Group, was Oct. 23-25, 2011, in Chicago.
Jupiter Transport Services has been in business since 1980. We specialize in the transportation of recyclable products. We are based in Jupiter, Fla., but we are licensed and insured to do business in 48 states and in Canada. We are a member of the Institute of Scrap Recycling Industries Inc. (ISRI), the TIA (Transportation Intermediaries Association) and also the National Association of Small Trucking Companies.
The Truck Shortage
I’m sure everybody has noticed—there is a truck shortage.
Where are all the trucks?
A combination of rising truck equipment costs, a driver shortage and increased government regulations is forcing shippers to confront the new reality: Capacity is no longer infinite.
New ways to improve efficiencies must be found. Several industry experts have said that we have to do something to change the way we do business. The cost of capacity will continue to climb in 2012. Since 2008, a number of carriers have filed bankruptcy or gone out of business. In 2008 alone, 2,500 carriers shut their doors. The American Trucking Association’s (ATA’s) Truck Tonnage Index is at its highest point since the beginning of the recession. (This index starts in January 1973 and includes a not-seasonally adjusted [NSA] and a seasonally adjusted [SA] series. The index is set to 2000 equaling 100. ATA asks its membership the amount of tonnage each carrier hauled, including all types of freight, and calculates the index based on those responses.)
I’m sure you’ve all run into the situation where you’ve had a hot load sitting on your dock and you walk out and ask your yard foreman, “Where’s the truck?” Well, a couple of years ago, when you asked that question, two-dozen trucks might have been sped to that location to pick up that last-minute load, with each carrier offering a steep discount to get that load on the road. No longer today.
Shippers escaped what many expected would be a severe capacity crunch in the first half of 2011 as slower-than-expected economic growth brought freight demand and equipment supply into a rough balance. Don’t expect that to change soon. Even after several shocks to the economy, we are going into 2013 before we see this realigned again.
The Driver Shortage
The second problem that we are facing today in the trucking industry is a shortage of drivers.
Where have all the drivers gone?
There are several reasons for [the driver shortage]. Right now, there is low pay, the drivers are away from home too long and there is a shortage of younger drivers coming into the industry. If trucking continues to want to attract, hire and retain drivers beyond the short term, breaking the cycle of so-called shortages that stretch back to the industry’s origin, they need to come up with new strategies that deliver more certainty and stability for their businesses and, ultimately, their shipper customers.
Shippers need to be retrained in how they build their supply chain networks. If they want these long-haul routes, they are going to have to pay for them. Driver pay may be the biggest contributor to the perceived shortage, but it is an issue few shippers and carriers want to tackle head-on. Most agree driver pay needs to rise, but there are differences as to how much and when.
Government Regulations
The other thing that we are facing right now is government regulations. This is reducing productivity, and it is putting a burden on all the carriers, especially the small to medium-sized carriers that make up an estimated 95 percent of the trucking industry.
The federal government’s latest Hours of Service proposal will result in reduced wages for hundreds of thousands of truck drivers, significant costs for trucking companies and billions of dollars in lost productivity. These inefficiencies and costs would deal a serious and sustained blow to the huge tangible goods economy that trucking supports, affecting not only shippers of freight but ultimately consumers. The proposal also would impose new and unwarranted costs on local and state enforcement agencies responsible for enforcing these new rules.
The government wants to reduce the Hours of Service that truck drivers can actually drive. At the present, drivers are allowed to be on duty for 14 hours—11 hours driving and three hours loading, unloading, performing safety checks as so on. The government wants to reduce that. If you reduce that, that means you need more trucks to carry the same amount of freight. So it is going to cost everyone more money.
Also, old equipment is being retired because of new emissions standards, and financing is difficult because of tighter lending practices.
All of this is adding up to truck load carriers trying to keep capacity flat. Surveys find that nearly 75 percent of truckers plan no new capacity over the next year. Fewer truck load carriers are planning to add capacity [in 2012] than had planned to in the previous six months. The continued poor economic news is likely to dampen new truck orders over the next year, unless freight demand picks up. Truck load freight has been unusually strong for an economy plagued with unemployment, low consumer confidence and fear of a double-dip recession. But if carriers, seeing that demand and supply are in rough equilibrium, appear to be waiting for clear signals of economic growth before committing more resources.
Addressing the Capacity Shortage
What I wanted to finish with is how we can address the capacity shortage. I think we want to be more broker, shipper and carrier friendly. What I am referring to is trucks come into your yards, and sometimes yards are not in good condition. I’ve been to yards where sometimes the water is up to the axles on the truck. Carriers don’t want to submit their equipment to these kinds of conditions. So we want to make our yards friendly for trucks to come into.
I spoke about the Hours of Service. Carriers nowadays also have become very sensitive to time; the drivers are only allowed to work so many hours a day. When a truck comes into your yard, you want to have the material ready for them to load the truck. Waiting time at the dock goes against the driver’s allowed driving time. Carriers remember difficult shippers and avoid them in the future or rate them higher.
I don’t know if anybody remembers the Seinfeld episode where Elaine went to the doctor and the doctor wrote on her form that she was difficult, and the doctor passed it on to all the other doctors. Well, it is the same thing in the trucking industry. When a carrier comes into your yard, if it is a difficult place to get into, if it is untidy, they are going to report that, and word will spread. That is something to keep in mind.
Make sure your material is loaded correctly. If in doubt, discuss the loading process with the driver: weight distribution, blocking and bracing. Avoid peak shipping times at the end of the month, end of the quarter as well as holidays. Costs rise in light of shortages of equipment during peak times.
Addressing Security
The last thing I want to talk about is security. I know there have been a lot of thefts lately in the recycling industry. The things I want to point out to you are:
- Know who you are dealing with. Are you dealing with a carrier directly, a broker, a freight forwarded or someone on the Internet? Check their references. Verify their insurance. Check past problems.
- Check that the carrier that was contracted on the load is the same one that arrives at your door. You wouldn’t believe that people actually load their product on trucks and they have no idea whether that is the correct load for the truck. We’ve sent in trucks to different yards, and the driver says he’s there to pick up a load. The load master says to back into the dock, and it’s the wrong load. And the shipping company doesn’t even know which truck they put the load on. So be careful, verify the carrier that you’re using.
- You want to check the driver ID and make copies of the driver’s license. At Jupiter Transport, we call ahead to the shipper and let them know the name on the truck, the driver’s name and the driver’s license ID number, that way when the truck arrives at your facility, you can compare the driver’s information with the information we gave you and know it is the correct driver for the correct load.
- You also want to check the tractor and trailer, including the name on the truck. You can make copies of the tractor ID and keep it on file for your records.
- Make sure scale tickets are up to date.
- Sealing the truck—There have been many times when the truck has been loaded, and the dock master gives the driver the seal and tells him to seal the trailer after he closes his doors. When the driver gets to the other end and there’s a shortage, who’s to blame? There was no seal put on the trailer when the trailer left the facility, so now we are asking who did what to whom. It is always a good idea for your man to seal the trailer before the truck leaves.
- You want to avoid shipping high-value loads over weekends or holidays. We certainly don’t want to see our loads hanging out at truck stops over the weekend. High-dollar loads we want to see shipped during the week, when they can get unloaded and reloaded in a day or two.
- If you are contracting transportation through a broker, build the relationship and communicate your security needs to them. They should have a definite program in place to minimize the chance of theft. Ask for details and make sure it suits your needs.
Besides providing security, how else does a broker protect you? The broker qualifies the carriers, verifies the authority, verifies the insurance and checks the Federal Motor Carrier Safety Administration (FMSCA) Compliance, Safety and Accountability Program (CSA) to protect you from legal liability in case of an accident.
Long Road Ahead
There is no quick fix to the capacity shortage. With the future of the economy unsure, the high cost of equipment and financing difficult to obtain, carriers are at a standstill about adding new equipment.
With new government regulation, such as the CSA and Hours of Service, finding capable drivers is also a problem. As the economy recovers, capacity shortage and higher freight rates cannot be avoided.
If you want your company to be on carrier and broker lists, make your yards carrier friendly, accounting friendly and driver friendly.
Bruce O’Neill is founder and president of Jupiter Transport Services, Jupiter, Fla. He can be reached at bruce@jupitertransport.com.
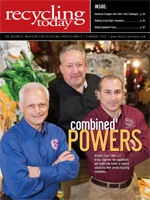
Explore the February 2012 Issue
Check out more from this issue and find your next story to read.
Latest from Recycling Today
- Aqua Metals secures $1.5M loan, reports operational strides
- AF&PA urges veto of NY bill
- Aluminum Association includes recycling among 2025 policy priorities
- AISI applauds waterways spending bill
- Lux Research questions hydrogen’s transportation role
- Sonoco selling thermoformed, flexible packaging business to Toppan for $1.8B
- ReMA offers Superfund informational reports
- Hyster-Yale commits to US production