Every day, goods are unloaded from boxes and placed on the shelves at retail locations all over the country. Those countless empty boxes are finding their ways into balers located in the stock rooms of these stores. Not only does recycling keep this valuable secondary commodity from going to a landfill, it also can provide supplemental income to these businesses.
Conducting routine and preventive maintenance on a baler is an important step in making sure the equipment continues to churn out quality bales of old corrugated containers (OCC). Wastequip, a Charlotte, N.C.-based manufacture of balers, compactors and containers, supplies many retail locations with its vertical balers.
Kirk Warren, technical product manager at Wastequip, says most balers can run for many years with very little maintenance. That is good news for retailers, who may not be as equipment savvy as recyclers who are used to working with heavy machinery.
Warren spoke with Recycling Today Assistant Editor Kristin Smith and offers advice for maintaining balers used in retail settings.
Recycling Today (RT): Please describe the scope of Wastequip’s baling business. What types of balers are you selling and how do they fit into Wastequip’s overall product offering?
Kirk Warren (KW): Wastequip manufactures and sells vertical balers to commercial customers for their recycling and waste needs. With nine different models, Wastequip balers are designed for multiple applications. Vertical balers are part of our complete line of compaction equipment and complement our steel and plastic containers.
Keeping a Schedule Charlotte, N.C.-based Wastequip recommends the following weekly, monthly and yearly baler maintenance tasks: Weekly
Monthly
Yearly
|
RT: What are some of the common maintenance issues you encounter in balers located at retail locations?
KW: Generally, vertical balers are built to withstand years of use with relatively very little maintenance required. Common maintenance issues are changing the oil, breather cap and filter, and after many years in service we may receive a call for a ram UHMW-PE (ultra-high-molecular-weight polyethylene) wear strip.
RT: What kind of maintenance schedule do you recommend? Do most retailers opt for professional servicing from their suppliers or do they have their own service staff?
KW: We recommend and outline a weekly, monthly, initial 90-day and yearly maintenance schedule. (See sidebar, “Keeping a Schedule”.) The schedule is printed inside the “Operation and Maintenance” manual.
Retailers generally can handle the weekly and monthly maintenance items and call one of our service providers for the yearly maintenance. Yearly maintenance includes flushing and refilling the hydraulic oil, replacing the breather cap spin-on element, structural inspection and electrical connection inspection.
RT: What kinds of daily maintenance can retailers perform themselves to ensure the longevity of their balers?
KW: Check oil tank level and clarity; inspect hoses and fittings for leaks; remove any debris, dust, dirt, grease or moisture from the power unit or platen; and run the unit to verify proper operation.
RT: What can happen to a baler if a retailer is misusing it by putting the wrong type of materials into it? What other types of abuses do you see on the part of retailers?
KW: Placing items in a baler that are not designed for the model can lead to premature wear and possible failure, as the baler is not operating efficiently or effectively. We really don’t see too much abuse, as customers understand the use of the equipment and it is designed to work as intended.
RT: How important is regular maintenance? What issues can result if preventive maintenance is ignored?
KW: Preventative maintenance protects against premature wear and will extend the life of the baler.
We located the oil tank sight and temperature gauge at eye level to promote and make weekly inspections easy for the user. We have also designed the power unit to be eye level and easily accessible for inspection and maintenance.
While our vertical balers are designed to require little maintenance, ignoring maintenance can lead to premature wear and failure, resulting in equipment shutdown.
RT: What do you do to educate your customers on the proper operation/maintenance of a baler?
KW: In addition to providing an operation and installation manual with each baler we sell, we offer on-site training when the baler is installed, have a baler training video available on our website (www.wastequip.com) and offer customers refresher courses on operation and maintenance.
RT: What advice do you have for retailers that are interested in purchasing a baler but who don’t have experience working with baling equipment?
KW: We offer a free on-site waste and recycling audit to determine the application and recommend the proper equipment. We provide references so potential customers can speak to other retailers who use our balers and learn what to expect in the way of performance and maintenance. We also recommend potential customers view our training video and product brochure to familiarize themselves with the equipment.
RT: Can space constraints in the stock room limit the ability to access and make repairs to a baler?
KW: Yes, because space constraints may limit the ability to inspect/service the baler’s power unit in certain applications, Wastequip designed an eye-level, ground-accessible power unit. The oil sight and temperature gauge are positioned so that the operator can easily see the oil level and temperature while standing next to the baler. The power unit, which includes the oil tank, can be inspected and serviced without putting the service technician high up on a ladder.
RT: What do you recommend to ensure employee safety during servicing?
KW: Wastequip recommends following lockout/tagout procedures as outlined in the owner’s “Operation and Installation” manual. Lockout/tagout procedures establish performance habits that provide for the protection from injury of personnel during an unexpected startup or release of stored energy from the equipment while in, on or around the equipment during repair, scheduled or emergency maintenance and other associated activities.
Wastequip also recommends that any modifications to the equipment be in accordance with ANSI (American National Standards Institute) and OSHA (Occupational Safety and Health Administration) guidelines and be approved by the manufacturer prior to implementation.
Kirk Warren is manager, technical products, for Charlotte, N.C.-based Wastequip.
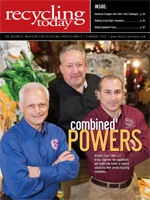
Explore the February 2012 Issue
Check out more from this issue and find your next story to read.
Latest from Recycling Today
- Aqua Metals secures $1.5M loan, reports operational strides
- AF&PA urges veto of NY bill
- Aluminum Association includes recycling among 2025 policy priorities
- AISI applauds waterways spending bill
- Lux Research questions hydrogen’s transportation role
- Sonoco selling thermoformed, flexible packaging business to Toppan for $1.8B
- ReMA offers Superfund informational reports
- Hyster-Yale commits to US production