![]() |
Equipment maintenance: for some it’s one of the necessary evils of running equipment and a dirty job that can rob valuable production time. Even so, the tasks at hand are critical ones that can ultimately help equipment earn its maximum return on investment.
When it comes to the hydraulically powered mobile shear—one of the scrap recycling industry’s workhorse equipment categories—routine maintenance is all in a day’s work.
While some of the maintenance procedures are similar, the exact requirements can differ between brands.
Routine Upkeep
Mike Ramun, sales manager with Allied-Gator Inc., Youngstown, Ohio, points out that “shear maintenance relates directly to the design of the shear itself, and the better the design, the easier and less frequent the maintenance will be.” Because of the wide variety of shear designs on the market, maintenance can vary widely from brand to brand, he says, and also is highly dependent on the material being cut. “Shear maintenance is so dependent on the design of the tool, that it’s very hard to talk about shear maintenance in a generalized fashion,” says Ramun. “Allied-Gator shears, available in sizes from 800 to 52,000 pounds, are designed to maximize the life of the consumable parts with a focus on minimizing the time required for maintenance,” he adds.
![]() |
Colby Perkins, shear product specialist for Carroll, Ohio-based Company Wrench, which sells and services Stanley/Labounty mobile shears throughout the country, says multiple problems can stem from a lack of maintenance. “Without proper shear maintenance, we have seen busted blades, broken bolts, hydraulics issues, material jamming, premature wear on bearings, welds breaking—just a variety of structural failures.”
Tim Alseth, technical service manager with Genesis Attachments, based in Superior, Wis., says, “To the untrained eye, shears are a very simple machine.” However, he continues, “The tremendous forces produced by the shear and the extreme environment in which they work can make them self-destructive if not properly maintained and operated.” Alseth says the Genesis XP line, ranging from the 200 to 2500 series products, is the most popular with the scrap processing sector of Genesis customers.
Alseth says that since all parts of the shear are directly related to each other, excessive wear in one area can adversely affect other areas. “Seemingly small issues can therefore develop into large problems, if not addressed,” he says.
Blade Considerations
Manufacturers agree one of the most important mobile shear maintenance aspects is keeping the blades in proper operating condition. These consumable parts must be inspected regularly.
In some models, mobile shear blades have multiple usable edges and they are designed to be rotated when one of their edges has been worn out. However the life of each blade edge can vary.
Ramun says blade maintenance is largely about keeping the shear blades in proper operating condition so they will be sharp enough to perform the cutting tasks at hand. He notes that shear blades must be rotated as called for in the owners’/operators’ manual. Allied-Gator shears use four-way and eight-way indexable blades designed to be flipped when worn out, then replaced, along with the bolts when all usable blade edges have been used. “Our customers typically see 60 to 80 hours (per blade edge) in a general scrap cutting application,” Ramun says. For scrap recyclers, general cutting includes scrap materials such as I-beams and other structural steel, rebar, cable, steel plate, sheeting and industrial equipment, right down to items such as vehicles and appliances, he says.
But, Ramun adds, the most significant deciding factor concerning blade life is the material that’s being sheared. “Due to the fact that the MT is the only shear capable of working in extreme cutting applications, such as full-time steel cable or hardened wire processing, it is possible to wear out a blade edge in as little as 20 hours if you’re shearing in that specific type of extreme application,” he says. “However, with our design, if users are shearing a less demanding material, like copper cable or aluminum extrusions, for example, they can go as long as three months on a blade edge before they have to flip it.”
With the Genesis XP, Alseth says, operators need to inspect shear blades twice each day, at four- and eight-hour work intervals, to assess the condition of the blades. Along with that, Alseth says, operators may need to shim up the blades once a day or so to keep blade gaps at proper tolerances. Genesis XP blades also need to be torqued at proper intervals and to the proper specification—without being over-tightened.
Shear inspections also should reveal whether the blades need additional maintenance work, namely rotation or replacement. Or, shear operators may need to grind down and square up blade edges that have rolled, Alseth says.
Perkins suggests that users of Stanley/Labounty shears need to flip blades on those shears after every 40 hours of use. “Basic maintenance includes surface grinding all edges and shimming the blades to get them to the correct tolerance,” Perkins comments. Stanley/Labounty recommends replacing blades every 80 hours, he says, “but we’ve seen them last longer with proper use, and the opposite is also true.” He adds that early failures can often be attributed to cutting hardened, brittle material.
Perkins says the scrap recycling market uses the full product line of Stanley/Labounty shears, from the MSD7R to the MSD9500R. The dealer serves customers nationwide.
Along with attending to the blades, a number of other routine tasks may be needed daily, depending on the manufacturer. Greasing the moving parts is a requirement for all shears, and detailed instructions for this are provided in the operators’ manuals.
Alseth says Genesis shears need regular greasing at four- and eight-hour intervals, along with inspections of the auto-guide, blades, fasteners and hydraulic components. During these inspections, operators need to be on the lookout for cracked, missing or broken blades; loose, missing or broken fasteners; hydraulic leaks; or any cracks in the welds and attachment structure. And daily inspections of the Genesis XP also will indicate whether adjustments to the auto-guide or puck are needed.
![]() |
Technical Tasks
Along with these more routine maintenance tasks, other preventive tasks need to be handled on a longer-term basis. These requirements can vary by brand and are listed in the operators’ manual supplied by the manufacturer.
A fair amount of welding knowledge also may be required, again depending on the shear brand, to keep the shears maintained. For instance, one key task that Genesis XP operators or dealers may need to perform, Alseth says, is to build up and hard surface the jaws. This can return jaw surfaces that have been worn down back to their original profiles and harden the jaw surfaces. These specialized welding techniques are explained in the product manual, Alseth says.
However one recent Genesis product enhancement is designed to greatly reduce that requirement.
In March of 2011, the company introduced Jaw Armor, pre-formed hardened plates that are welded to the upper and lower jaws. The product is designed to help eliminate the need for weld buildup and hard surfacing. “They will eventually wear to the point where they have to be replaced,” says Alseth, “but you don’t have all the time involved for the welding buildup and hard surfacing that you would if you weren’t using them.” Jaw Armor can be ordered with the shears or purchased separately.
Meanwhile, Allied-Gator shears don’t require hard-face welding at all, says Ramun, and because of the MT’s dual-moving jaw cutting dynamic, typically have less maintenance associated with the area around the blades, he adds.
When Shearing Doesn't Cut It According to shear manufacturers, there are some types of material that should not be cut with a mobile shear, specifically things made of hardened steel. Common examples include railroad rail, truck axels, steel forgings and hydraulic cylinder rods. Mike Ramun, sales manager with Allied-Gator Inc., Youngstown, Ohio, says these types of materials are far too brittle to be sheared. He says, though, that they can be crushed. And with its modular design, the MT line from Allied-Gator has a jaw to do that. Ramun says the shear jaw on Allied-Gator MT models can be switched out with the company’s cracker/crusher jaw, which is designed to break hardened steel materials that are not advisable to cut with a shear jaw. The MT has been on the market since 2001, says Ramun, who adds that its versatility has made it a popular option with recyclers. “It’s become a very hot item,” he says. “The fact that recyclers are able to [process] this type of material now is a great thing for them.” |
However, users do need to maintain tolerances between the cutting blades and between the shear tip and lower jaw. Ramun says Allied-Gator is the only manufacturer to offer a shear design to work with two different tips: an MT Solid Tip as well as a patent-pending MT Disposable Tip, featuring blade segments that are replaceable in under 10 minutes.
The Solid Tip requires a 30-to-45-minute weld maintenance task once per week, according to Ramun, when the user is required to weld-build the corners of the tip.
With the Disposable Tip, users replace the blade segments when they are worn and no longer within tolerance, he adds. “Allied-Gator’s Disposable Tip has been designed to eliminate welding to these areas,” Ramun states.
Service Assistance
Alseth says that while most Genesis users can perform their own routine maintenance, some also rely on local equipment dealers or outside contractors to perform maintenance tasks. “Our dealer network is quite extensive, and most dealers have personnel trained for this,” he says.
Alseth says some shear operators opt for dealers that can service both the attachment and the carrier itself. “A lot of times you can have hydraulic issues with one or the other and you don’t know where the problem is,” Alseth says.
Perkins says in his experience, it’s about a 50-50 split between scrap recyclers who take care of their own maintenance and those who call in technicians. “Recyclers who need this support can purchase complete shear service plans available from Company Wrench,” Perkins notes.
Ramun says the Allied-Gator design, by contrast, allows end users to perform their own routine maintenance.
Common Problem Areas
Alseth says some of the common maintenance issues he sees in the field are not greasing the attachment at the specified intervals, using blades long past their service lives and not maintaining the blade gaps specified by the company.
A common mistake on the operations side is using the shears to cut un-shearable items—hardened-steel objects, such as railroad rails, axel shafts and truck springs. “These seem to cause recyclers the most problems with their shears,” Perkins says. “We recommend using torches to cut these types of hardened, brittle materials and saving your shears for what they are designed to cut.”
Another common mistake, according to Alseth, is using the weight of the excavator to pound the shear’s upper jaw into the ground to clear a jam or to get the shear to cut more than it is hydraulically capable of. These actions cause excessive wear to the parent material of the jaws and blades, he says, and will lead to more frequent need for build up and hard surfacing.
“What we tell people to do is cut out of a smaller pile,” Alseth comments. “Don’t scratch around on the ground with the shear.” Operators also need to keep heavy loads centered in the jaws, he says.
Another common problem he’s seen is over-tightening of the blade. “It stretches the bolts beyond yield and they lose their strength,” Alseth remarks.
And one surprising problem area, according to Alseth: not attending to routine maintenance at all. “I’ve seen guys who don’t do any maintenance, period,” he says. “And the shears were junk in five, six months.” Conversely, Alseth says, following the proper specified maintenance schedules will help ensure that the shear lasts for many years.
The author is a managing editor with the Recycling Today Media Group. She can be contacted at lmckenna@gie.net.
Not Cutting It
For information on how recyclers can process hardened steel, see the sidebar “When Shearing Doesn’t Cut It.”
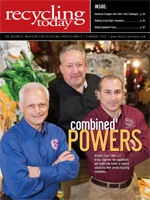
Explore the February 2012 Issue
Check out more from this issue and find your next story to read.
Latest from Recycling Today
- Aqua Metals secures $1.5M loan, reports operational strides
- AF&PA urges veto of NY bill
- Aluminum Association includes recycling among 2025 policy priorities
- AISI applauds waterways spending bill
- Lux Research questions hydrogen’s transportation role
- Sonoco selling thermoformed, flexible packaging business to Toppan for $1.8B
- ReMA offers Superfund informational reports
- Hyster-Yale commits to US production