Baling ferrous materials requires some serious strength, and balers designed for baling paper, plastic, aluminum or other similar materials are not up to the task. Ferrous balers, first designed to handle automobiles, have the muscle necessary to bale heavy-duty materials.
“Balers designed for ferrous scrap require extensive structural strength as opposed to other balers,” says Curt Spry, scrap sales manager, Al-jon Manufacturing, Ottumwa, Iowa.
Typically, ferrous balers compress from three sides to achieve the density and compression required.
Jon Lanker, regional sales manager for Harris, Tyrone, Ga., says, “A ferrous bale is a high-density bale that does not require any ties and is used as a whole. If you have a 24-inch-by-24-inch-by-variable bale that goes to a steel mill, they will drop that whole bale into the furnace to remelt for steel.”
For a finished bale to not need ties, the amount of force applied to the scrap needs to be great. Robert Plichta, sales manager for Logemann Brothers, Milwaukee, Wis., explains, “The ferrous scrap balers with two or three rams exert a force of approximately 2,500 pounds per square inch minimum in final compression, whereas the paper balers with one or two rams exert approximately 200 pounds per square inch minimum in final compression. When those same [paper] balers are processing light metals and aluminum, the pressure increases to approximately 400 pounds per square inch.”
Strong Outlook
When shopping for a ferrous baler, several details should be kept in mind.
Lanker explains, “The old adage is ‘buy the biggest baler you can afford,’ and I guess it still holds true, but there is a cutoff to that as far as what you’re getting into.” He adds that sizing a baler for growth over a five-to-10-year period can be somewhat difficult to do.
“Most balers that we sell have the ability to process a certain amount, and very few companies are going to be right at the capability of that baler,” Lanker says. “If they are, then we would normally recommend they go to the next size machine to allow for what they’re processing now and still give them a growth factor.”
Plichta uses the following formula to determine the future growth of an operation: 5 percent per year multiplied by 10 years. This equals 50 percent growth during a 10-year period.
After considering future growth, bale size reigns supreme. This will depend on what the end user is looking for, but integrated steel mills tend to use bales measuring 24 inches by 24 inches by variable, and electric-arc furnace mills often require 16-inch-by-16-inch-by-variable bales.
Plichta says, “The most important thing once they move [beyond] the bale size is to give some thought to the physical size dimensions of the charging box. They actually want a box large enough to accept the material they happen to be processing at their particular yard.” He adds, “Beyond that, the actual structural strength of the equipment is very important at all scrap yards.”
Recyclers also should ask themselves about their expected throughput, or how much material they plan to move in and out of the facility each month. Additionally, portable balers can offer versatility, enabling operators to process material on site, Spry says. However, that versatility comes with a price in terms of overall capacity. Portable balers are easier to install and have a good resale value, he adds.
“A stationary baler, with proper care and maintenance, will last 30 years or so,” according to Lanker. “But there is no real end to the baler if it is properly maintained,” he continues. “It can be resold to a customer who can put a certain amount of money into it and it can last another 20 to 30 years.”
Shredded Interest
In the heyday of the auto industry, the auto giants produced giant cars—with weights approaching 6,000 pounds. Plichta says, “Those large automobiles were baled, but they don’t do that anymore.” He adds that the curb weight of a typical automobile has been reduced to approximately 3,500 pounds through the use of a variety of lightweight materials. “The only way to sort through these various materials is to shred.” He adds that while there has been growth in the number of auto shredders in operation, “that does not completely eliminate the need for baling.”
Pilchta adds, “The most popular bale appears to be the 16 inch by 16 inch by variable.”
According to Lanker, a shredder manufacturer once said that no more big balers would be bought because of the growth of the shredding industry. That has not been the case, he adds. “We have a steady volume of balers being purchased over the years and it is still very strong. I would say the future of the ferrous baler is still very strong.”
In an industry that values flexibility as a means to stay on top, even companies that have adding auto shredders to their operations still find themselves making use of their ferrous balers.
“The companies that operate shredders also have the flexibility of being able to bale,” Plichta says.
The growth of automobile shredding has led to increased interest in ferrous balers, Spry says. “As a matter of fact, we have seen increases [in ferrous baler sales],” he says. “These new shredder owners often purchase portable balers themselves to guarantee feedstock for their shredders,” he adds.
Another benefit balers still hold over shredders comes down to money. It will typically cost less to maintain a baler than it does to keep a shredder running.
“Baled material in some markets can have an advantage over shred, depending on what an end user is looking for; but, primarily a baler is much more cost effective to work with than a shredder,” Lanker says. “In the scrap yards today, the balers are probably the least expensive to run on a cost-per-ton basis based on the maintenance required to keep it running at its best as compared to a shredder, which costs more to operate because of the nature of the machine itself. It’s a lot more complicated than a baler is going to be.”
Material Handling
Although operators may be processing fewer automobiles with their balers these days, there is still plenty of material left to process. Spry says there is still some automobile scrap to be found, such as “hoods, doors and fenders,” which are all “optimal materials” for baling. Operators also are processing “miscellaneous alley scrap, like washers and dryers” with their balers, he says.
To determine what kind of ferrous material is best to process using a particular baler, it is a good idea to look at the size and type of bale the machine is designed to produce. The most desirable ferrous material to bale will be the type that does not require any pre-processing, according to sources.
“For instance,” Lanker says, “a small baler in an automotive plant is going to be baling scrap coming off the stamping line.”
Stamping plant scrap is an ideal material to bale.
“All of this material does not require size reduction because the box is large enough to handle the auto scrap,” Plichta says.
The author is assistant editor of Recycling Today and can be contacted at kstoklosa@gie.net.
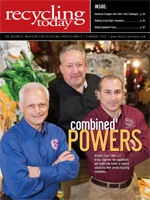
Explore the February 2012 Issue
Check out more from this issue and find your next story to read.
Latest from Recycling Today
- Aqua Metals secures $1.5M loan, reports operational strides
- AF&PA urges veto of NY bill
- Aluminum Association includes recycling among 2025 policy priorities
- AISI applauds waterways spending bill
- Lux Research questions hydrogen’s transportation role
- Sonoco selling thermoformed, flexible packaging business to Toppan for $1.8B
- ReMA offers Superfund informational reports
- Hyster-Yale commits to US production