Accent Wire, Tomball, Texas, describes itself as “the largest supplier of baling wire and wire tier systems in North America.”
The company’s President and CEO Bill Sims has worked in the industry for 16 years. He has a master’s degree in environmental engineering and a bachelor’s degree in mechanical engineering from Texas A&M University.
In the Q&A that follows, Sims responds to questions posed by Recycling Today’s Editorial Director Brian Taylor regarding managing baling wire expenses. He also offers his suggestions for reducing wire wastage and implementing best practices for wire usage at recycling facilities.
Recycling Today (RT): For paper recyclers and MRF operators, how high on the list can wire expenses rank as an ongoing operating cost?
Bill Sims: Wire expense is important to the profit of a recycling plant. Not including material and transportation, it is the second-highest operating cost behind labor in most facilities.
RT: How can recyclers determine whether their current wire costs are reasonable for the size of their operations or whether there is room to trim these costs?
Sims: Depending on a plant’s available storage space and working capital, there are price breaks available for larger wire shipments—your cost per pound of wire will be less for a truckload than for 10,000 pounds. Wire prices can fluctuate based on changes in the scrap and wire rod markets. It is smart for a recycling facility to independently follow these changes through one of the available indices that track these raw materials.
RT: Regarding what type or gauge of wire to use, what do recyclers of multiple materials (different fiber grades and different types of plastic) have to consider when making this decision?
Sims: This decision is largely predicated on the type of baler the plant is running. You have a little less flexibility with a single-ram baler when baling multiple materials. A potential way to manage wire costs is through the diameter (or gauge) of the wire. A MRF (material recovery facility) buys wire by the pound, but it is used by the foot on a baler. There are about 21 feet of wire per pound of 10-gauge wire and 26 feet per pound of 11-gauge wire—that is a substantial increase in yield. But this does not work in every baling application; it is a function of the material being baled, bale weight and wire quality.
Occasionally, a plant can drop a wire (the second wire from the top) and bale with four wires on light bales. On a two ram-baler with an automatic wire tier system, you can select how many wires to apply to the bale in addition to the diameter of the wire.
RT: Where can recyclers turn for guidance as to how much wire to use when baling a certain type of material?
Sims: Baler manufacturers and wire suppliers can provide some guidance, but this is largely a matter of operating experience.
RT: To what extent has research been done that measures wire usage best practices, or using enough wire to get the job done without using excess wire?
Sims: Broken bales from a wire failure are generally a result of three things: damage to the wire, selecting too light or too few wires for the baling application or bad wire.
Damage to the wire is caused by poorly maintained baling equipment and poor bale handling practices. We have already discussed some suggestions for the proper wire selection for the material being baled. As basic as it sounds, wire is not wire. Baling wire is specified to have the proper combination of strength and elongation (or the ability to stretch when under load). If you suspect a problem with your baling wire, keep the tags from the wire and take samples of the unused wire and broken wires for your wire supplier to inspect and test.
RT: How does safety fit into the equation in terms of ensuring enough wire is used to prevent bales from bursting suddenly?
Sims: While there are opportunities to reduce wire usage through some of these suggestions, safety should obviously be the first consideration. Many of today’s wire tiers feature bale containment guards to protect plant personnel if a bale fails during ejection.
RT: What are some of the automated devices or features that can help control wire usage or prevent recyclers from wasting wire?
Sims: First, it is important to take care of the wire the plant is storing. Wire should be stored in a well-ventilated, dry area. It is a good idea to cover the wire coils to keep them free of dust and debris.
Preventing wire wastage at the baler is largely a function of having equipment in proper operating condition. Wear grooves in feed tubes and worn pulleys and bearings can lead to short feeds on single-ram balers and, therefore, wasted wire.
Automatic tying heads on two-ram balers feed and tension wire at high speeds; there are a number of places or opportunities for wire not to feed home, resulting in wasted wire on a poorly maintained wire tier.
RT: What are some important tips for employees who operate balers to remember in terms of preventing the use of excess wire?
Sims: It is important to keep the wire tying equipment in top mechanical order through daily cleaning and regularly scheduled preventive maintenance.
Bill Sims is president and CEO of Tomball, Texas-based Accent Wire (www.accentwire.com), a provider of baling wire and wire tier solutions. He can be contacted at 800-383-8047.
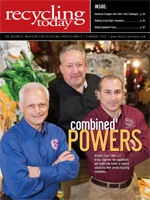
Explore the February 2012 Issue
Check out more from this issue and find your next story to read.
Latest from Recycling Today
- Cards renews municipal contract with Harrah, Oklahoma
- Secure Recycling scales up e-scrap shredding operations
- Farewell to Foam Act reintroduced to Congress
- European Commission publishes material stream requests for non-OECD country applications
- Shapiro receives NATM Innovation Award for Sustainability Excellence
- EAF mill underway in California
- Constellium recycled feedstock rate holds steady in 2024
- Lamor buys remaining shares in plastic scrap-to-oil facility